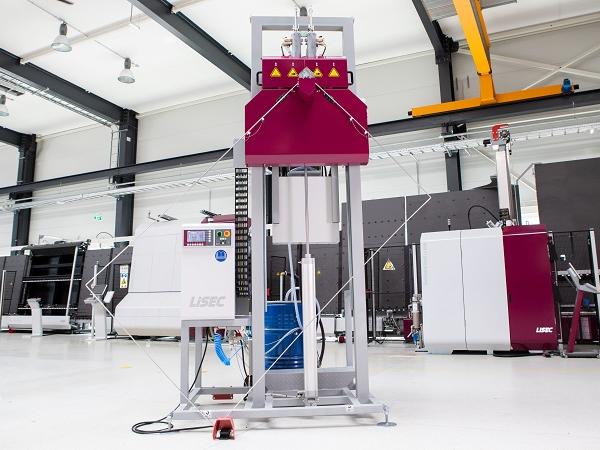
Date: 15 September 2021
The ARL-45F is another step in this direction. In the extensive LiSEC product range, automatic desiccant filling machines have been part of the standard range for many years. The ARL-45F raises the standard to a new level with the automatic filling amount check. In this interview, LiSEC product manager Ewald Schadauer will talk more about the configuration, functions and special features of this frame processing machine.
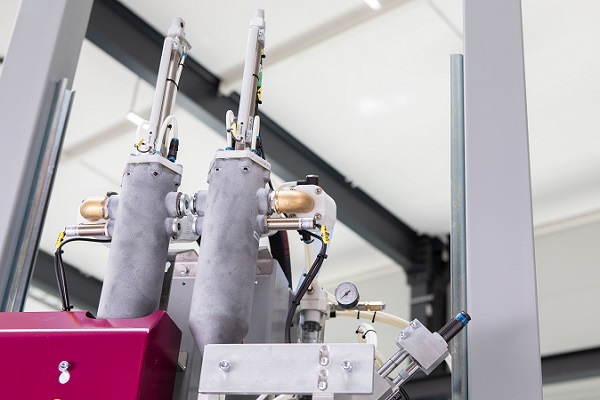
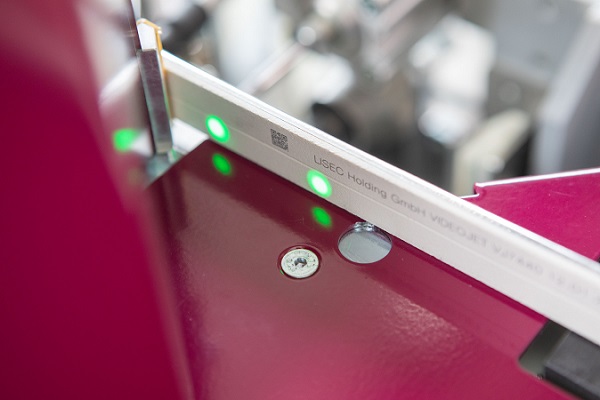
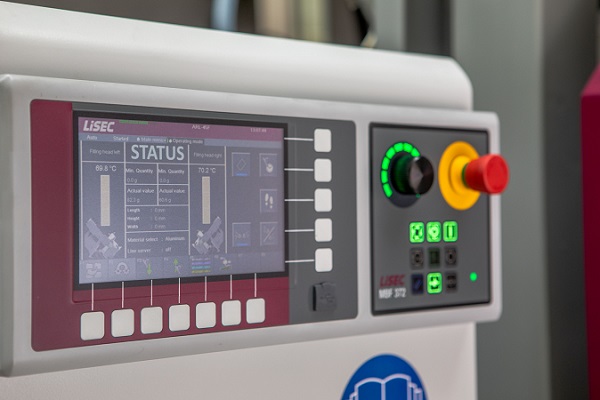
QUESTION: MR SCHADAUER, HOW IS THE ARL-45F CONFIGURED?
Ewald Schadauer: The ARL-45F is supplied with desiccant via a 200l drum. The height-adjustable frame clamp and two movable units are essential components. These moveable units contain a desiccant supply tank, a drilling unit, the desiccant transport with filling opening and a closing unit.
QUESTION: HOW DOES PROCESSING OF THE FRAME WORK?
Ewald Schadauer: The desiccant is conveyed from the 200l drum into the supply tanks. The operator inserts a corner of the frame into the clamp and starts the automatic process by pressing a foot pedal. The two drills are brought into position and drill a filling hole on the back of the profile. The two legs of the spacer frame are filled with desiccant and the two drilled holes are sealed with butyl. Then the clamp releases the frame again and the operator removes it from the filling machine.
The ARL-45F drills the filling openings on the back of the profile and thus offers the possibility of filling rectangles and shapes of all conventional spacer materials. Filling at the back of the frame guarantees a stable process, even with delicate plastic materials. The modern control system and smooth operation make working with this machine incredibly easy.
QUESTION: WHAT ARE THE SPECIAL FEATURES OF THE LISEC ARL-45F?
Ewald Schadauer: The ARL-45F particularly impresses with the optional automatic measurement of the amount of desiccant. With conventional desiccant filling systems, spacer frames are filled until no more material flow is registered and it is therefore assumed that at least two legs are completely filled. Even simpler systems only fill for a preset time without ensuring that a material flow is occurring at all. All these simple systems have one crucial problem in common: if the material flow comes to a halt due to a blockage, the spacer frame will not be sufficiently filled with adsorption material. The problem here is that the residual moisture contained in the air gap cannot be reliably absorbed by the insufficient amount of desiccant and the insulating glass units runs the risk of misting or becoming cloudy from the inside.
In comparison, the ARL-45F ensures that there is sufficient desiccant in the frame. This volumetric measurement system is based on a precise filling level detection in the desiccant supply tanks and guarantees a precise recording of the adsorption material filled. Consumption costs can be further minimised by the optimisation of consumption in spacer production or by precise metering of the desiccant amount that is adapted to the size of the frame.
QUESTION: HOW EXACTLY DOES THIS AUTOMATIC FILLING WORK?
Ewald Schadauer: So that the measured values obtained can be compared with the calculated amount for the currently filled frame, a data matrix code is printed on the inside of the frame profile during the spacer production. A scanner integrated into the ARL-45F evaluates the data matrix code and the correct desiccant filling quantity can be calculated using the available frame data such as dimensions, spacer width and profile material. If the amount filled is below the calculated value, the machine immediately reports a filling error and prompts the operator to turn and refill the current frame. This guarantees that no unit with insufficient desiccant finds its way into a window. In order to be able to prove this, all measured filling quantities are documented in the “Quality Pass” and stored in a file for evaluation by other systems.
FACT BOX:
Standard functions
- Automatic drilling of the spacer frame on the rear side of the short and long frame leg
- Adjustment of the optimum working height by means of a pneumatic lifting device
- Automatic pumping of the granulate from a 200 l drum to the filling devices
- Simultaneous filling of two sides of the spacer frame with granulate
- Sealing the drilled hole with butyl
Optional functions
- Measurement and documentation of the desiccant filling quantity
- Equipment for processing heat-flexible spacers (Swisspacer, Multitech, Thermobar, TGI Precision)
- Processing of frames with a max. size of 3,500 x 1,200 mm
Highlights
- Automatic drilling of the spacer frame on the rear side of the profile
- Measurement of the desiccant filling quantity: A device is installed in the two desiccant tanks, which measures the exact amount of desiccant filled per frame leg.
- Intelligent networking with the production software: The required quantity of desiccant is calculated in advance and compared with the measured quantity through a connection to the IG LineManagement. This results in direct error detection during the filling process, meaning that timely intervention is possible. Documenting the process values facilitates the verification of faultless frame production to the end customer.
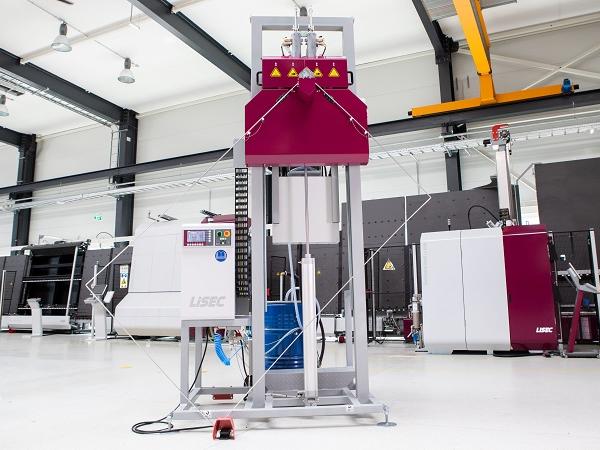

Add new comment