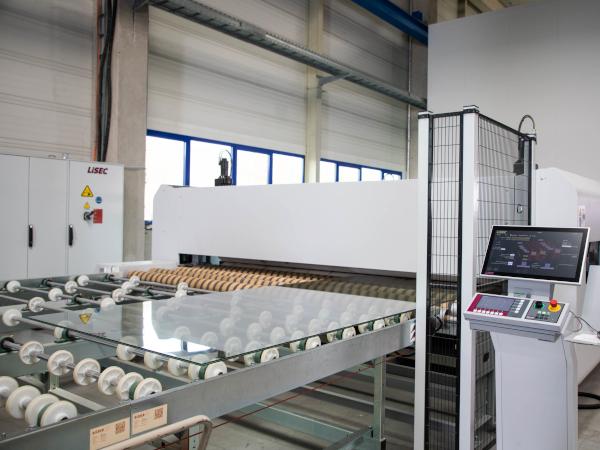
Date: 19 June 2024
Based in Feuchtwangen, Germany, arcon Flach- und Sicherheitsglas GmbH & Co. KG is an expert in flat glass processing and is an important source of supply within the Arnold Glas Group. In order to meet rising levels of customer demand for jumbo laminated glass units, which could not previously be produced on site, and to cater for the trend towards increased automation in production, arcon recently invested in a state-of-the-art LiSEC laminated glass line.
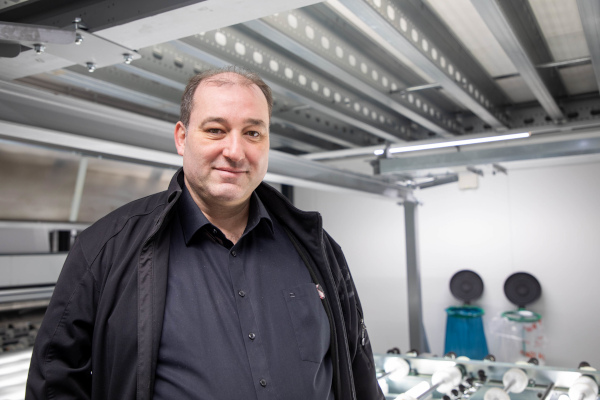
ABOUT ARCON
arcon is a member of the Arnold Glas Group, which has a total of five sites in Germany and Austria. The group's success story began back in 1959, with the establishment of Glaswerke Arnold. The production facility in Feuchtwangen, which employs around 115 dedicated employees, encompasses an area of 15,000 square metres. A wide range of products are manufactured here, supplying sites belonging to the Arnold Glas Group, as well as customers in the façade and window construction, automotive, sanitary, kitchen and interior sectors. arcon offers a broad product range that includes radio-transparent glass, decorative glass, safety glass, bird protection glass, solar control glass, and thermal insulation glass. Roughly 35% of the products manufactured by the group are exported.
LISEC & ARCON: A LONG-STANDING PARTNERSHIP BASED ON QUALITY & SERVICE
The collaboration between arcon and LiSEC began around 30 years ago with a LiSEC glass cutting system. Cooperation has become increasingly close over the years, with arcon always paying a visit to the LiSEC stand when attending trade fairs. LiSEC impresses at the Feuchtwangen site with the quality of its machines and end products, the high availability of spare parts and outstanding service. "The goal that we want to achieve with LiSEC products is very clear – to increase productivity and open up new opportunities for our company on the market. They say a machine is only as good as its service. Well if you need help quickly, advice is always available from LiSEC and the problem is resolved fast," Markus Biswanger, Plant Manager at arcon, enthuses about the collaboration with LiSEC. For arcon, LiSEC is a competent and dependable partner that impresses above all thanks to constant innovations.
NEW LISEC LAMINATED GLASS SYSTEM ENABLES JUMBO FORMATS
A highly automated two-storey LiSEC laminated glass line has recently been installed at arcon. "The reason we decided in favour of LiSEC when it came to the laminated glass line was the ability it gave us to process large units, as well as the top-class service provided for our systems in the past," explains Markus Biswanger.
At the beginning of the laminated glass process, we first scan a barcode on all glass lites sheets. A highlight of the line is the large foil store on the upper level, with automatic foil selection and video surveillance. The selected foil slides through the foil chute into the bottom level via inclined slide plates, where it is gripped by the LiSEC FLA automatic foil laying machine and transported over the glass fully automatically. The FCC foil cross cutter cuts the foil to the required length.
The second sheet is then placed on the unit using a suction cup before moving on to the LiSEC FTC, a system for automatically trimming the excess foil on all four sides of rectangular glass-foil-glass packages. "A major bonus with the new line is the FTC, which enables unmanned cutting of the foil and means that this process no longer needs to be performed manually. This is hugely advantageous for us," says Markus Biswanger.
The glass is transported to the pre-lamination press. At the same time, the pre-lamination press (PNM) receives the required furnace settings, which are pre-installed as a formula or can also be customised and expanded by us. Immediately before entering the pre-heating zone, the geometry of the glass (the glass thickness, glass width and glass shape) is measured. Algorithms automatically determine the required pressing pressure for the downstream servo-driven pressing rollers, which always press in a plane-parallel manner. This is particularly helpful and prevents damage to shapes, because the pressing force is metered according to the shape. If the sheet is narrower than ½ the maximum furnace width, the IR emitters only switch "on" on the relevant side and therefore help us to save energy. LiSEC refers to this as the Eco-Heater function.
The pre-nip machine is the centrepiece of every laminated glass system and has a significant influence on the success of the process as a whole. Sensors in the infeed area detect the glass thickness before the unit enters the pre-heating zone and subsequent main heating zone. LiSEC relies on convection and radiation for an energy-efficient and high-quality laminated glass process. After the glass-foil-glass package has passed through the pre-lamination furnace (PNM), the surface temperature of the glass is measured on the top and underside; if it is too high then the speed of the subsequent glass unit is increased, and if it is too low then the furnace speed is reduced. This also serves to save energy.
LOOKING TO THE FUTURE
In order to satisfy market requirements and conditions, arcon will be increasingly focussing on automation in the future and offering on-trend products such as bird protection glass and stock sheets. arcon also recognised its responsibility for sustainability at an early stage. The company has already taken several steps towards a greener future and plans to further intensify these efforts in the coming years. One example of this is the installation of a photovoltaic system on the roof of the company, which supplies ongoing operations with sustainably generated electricity, while arcon has also taken measures to minimise waste and use resources efficiently. All glass waste from production is fed back into the melting process.


Add new comment