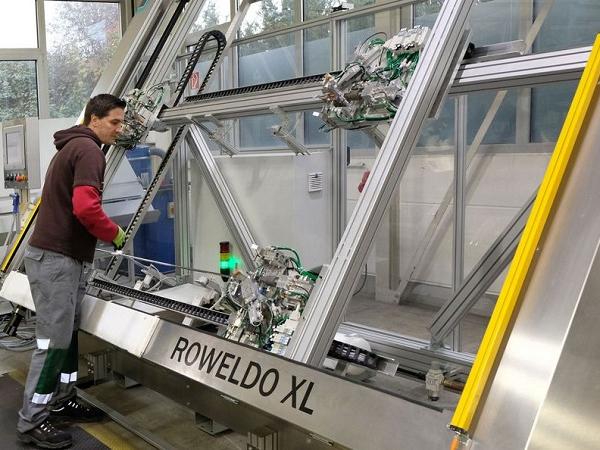
Date: 25 May 2018
This resolved the contradiction “glass yield versus optimal production sequence” intelligently.
Automatic line production makes manufacturing as efficient as possible at Glas Herzog. An innovation network including the software partner A+W and the machine partner HEGLA created a solution that has become the industry standard for insulated glass producers.
However, new solutions require the courage to innovate, and clearly this is in the DNA of this owner-operated company. The start-up of insulated glass production in 1962 by what at the time was a glass and mirror-grinding shop is also part of the company culture. Since 1978, Glas Herzog has relied on A+W Software in production and administration.

Today, Glas Herzog uses only state-of-the-art system technology and comprehensive software control – from the creation of quotations to production management to shipping. With this ensemble, the family-owned company produces the complete Climaplus series of complex, functional insulated glass, including special products such as heatable glass, sun protection glass, high-quality door inserts, and insulated glass units with interior blinds (isolette).
Glas Herzog’s products are sold throughout Southern Germany and nearby countries to window and door manufacturers and metal workers.
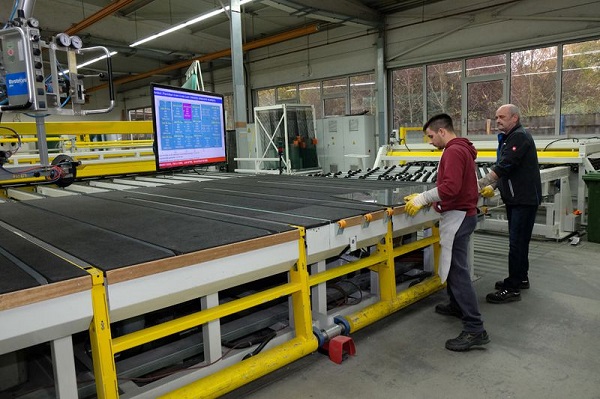
Qualified employees
Today, Glas Herzog employs approx. 80 people. “Our high degree of automation not only ensures cost-effective, higher-quality production, it also frees employees from activities that are hazardous to their health,” says Managing Director Andreas Herzog Sr.
“Instead of carrying heavy glass around, our employees are operating complex machine technology. As a company, we have fewer unskilled workers and more highly qualified employees who are justifiably proud of the work they do.”
To ensure a steady supply of talent, the company invests its resources training young people to become flat glass mechanics and glass construction technicians in production or industrial salespeople in the commercial sector. Most remain at the company after their training.
Insulated glass for all applications
Glas Herzog runs three insulated glass lines using the Swiss Spacer system, Super Spacer for warm edges, and a special multi-layer insulated glass line for high-quality door inserts.
Viprotron quality scanners on all lines guarantee flawless insulating glass units. Defective sheets are detected, discharged, and reproduced. Glas Herzog was among the pioneers with this technology too: quality scanners have been used on the insulated lines of the company since 2000.
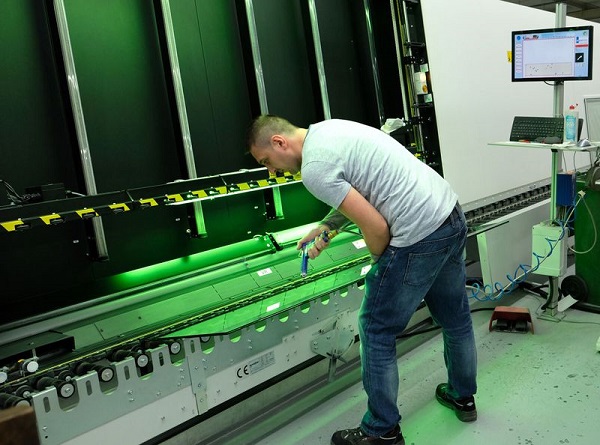
In 2017, Glas Herzog responded to an increasing demand for Laminated Safety Glass by installing a high-performance LSG cutting system. With integrated residual management, the new system ensures a more consistent supply of laminated glass to the production lines.
Thanks to state-of-the-art machine technology, even shapes can be cut with CNC precision—an important benefit for Glas Herzog since there are many shapes in their typical order mix. The A+W Realtime Optimizer software ensures the greatest flexibility and best optimization results.
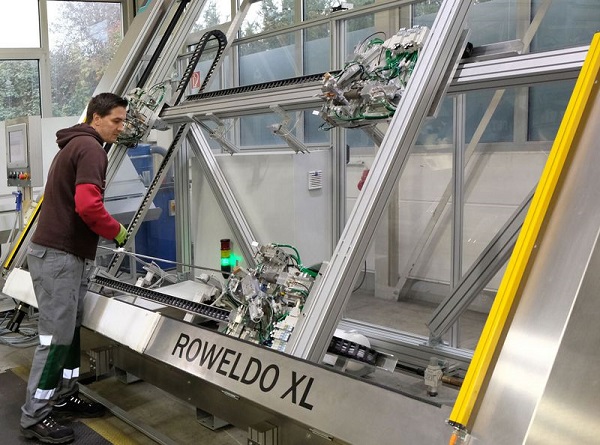
The company’s ReMaster residual storage solution is incorporated into the A+W optimization. If the glass type and size of a residual sheet fit the bill, then the A+W Realtime Optimizer automatically uses the sheet for the current or the next possible optimization batch.
Valuable first cuts are easily accessible within the cutting line, and are processed optimally. This saves a lot of glass and ensures fluid procedures in cutting: nobody has to remove residual sheets manually and store them “somewhere”.
Comprehensive company software
The comprehensive A+W software controls all processes from quotation creation and order entry to production planning and control with A+W Production 6 – right on through to delivery of the finished products.
With the A+W Business 6 ERP system, the Glas Herzog team can not only enter, copy, and manage quotations, orders, credits, purchase orders, and inquiries, it can also control other company areas (e.g. storage, purchasing, shipping, route planning, etc.). The management appreciates the many possibilities for business analyses, statistics, and evaluations using the integrated analysis tool Crystal Reports.
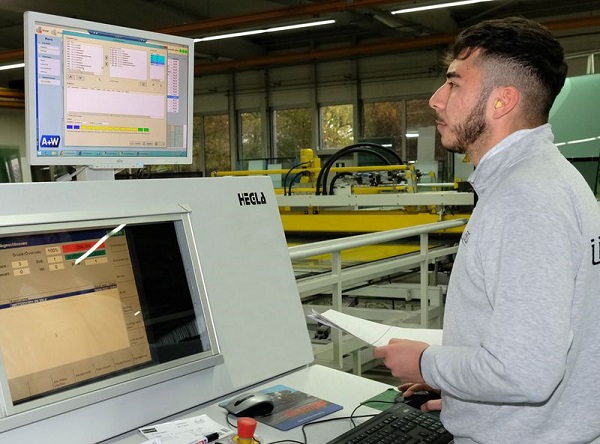
Many orders at Glas Herzog are received electronically via EDI and moved directly into A+W Business. All commercial and technical data is available everywhere at the company. A+W Business “knows” the status of each order in production and makes appropriate information available to answer customer inquiries.
“A+W Business 6 is the best version of the commercial A+W software,” says Andreas Herzog Jr. “The system works reliably, and thanks to the BOM concept, all products can be mapped. And if something gets hung up, A+W offers reliable service – our contact people, with whom we have been working for years, are experts, they help us quickly and easily.”
In work preparation, A+W Production pulls the orders apart so that individual items are produced independently and combined again in shipping. Packing lists, which can be transmitted electronically on request, assist Glas Herzog’s customers with their internal logistics.
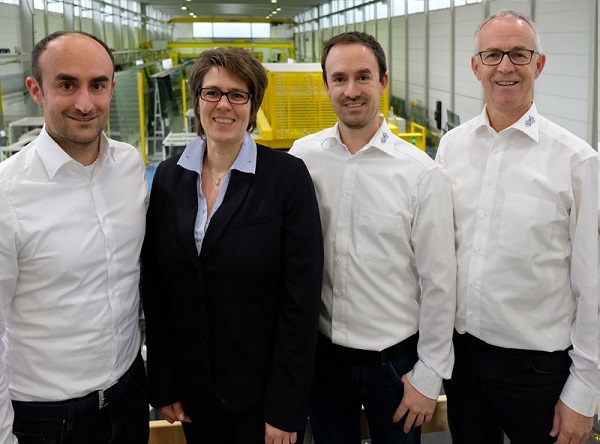
Maximum Customer Orientation
Glas Herzog is known in the industry as a reliable, innovative insulated glass partner that always delivers in top quality. It is the broad spectrum of services, from expert advising to production on state-of-the-art systems to timely delivery that Glas Herzog’s customers appreciate.
Glas Herzog people connect with customers as partners, and are solution-oriented. This level of support has enabled the company to enjoy a stable customer base: Some companies have been buying from Glas Herzog for thirty years.
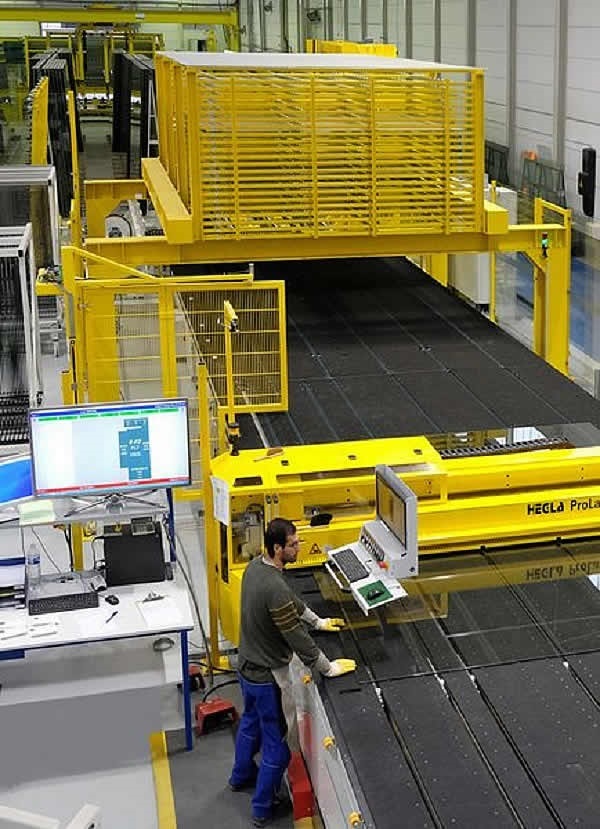
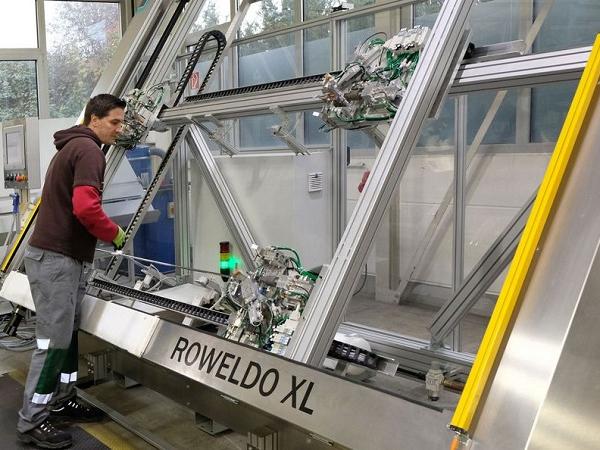
