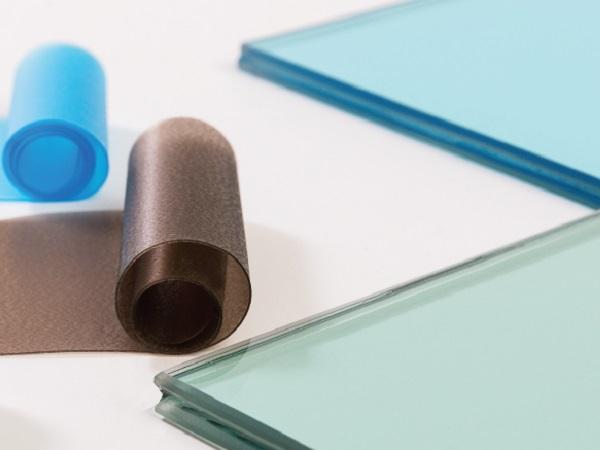
Date: 7 February 2018
As these only could get worse in the autoclave, it is important to have the right configuration of the nip roller line.
A key parameter is temperature – on the line and in the environment – as it affects the mechanical properties of PVB during the glass lamination process. The right temperature will uniformly soften the PVB surface and allow the air out under nip roller pressure.
If the temperature is too hot at the edges, the air will be trapped in and bubbles will form. We see it too often, when line control elements are triggered by underperforming parameters, corrective action comes too late and part of the production is doomed.
Ultimately, the robustness of laminates is directly dependent on temperature. Controlling it effectively is paramount to the production of quality products. Convection and infra-red radiation systems require a good understanding from the operator of the interaction between them to allow lamination at the right temperature.
Many of the issues that laminated glass producers face come from inadequate control of the production line. At EVERLAM, we have in-depth technical knowledge and expertise acquired over years of working with our customers to work out improvements, fix issues and find creative solutions.
We work with laminating line producers and laminators to provide technical assistance, tools and programs to enhance the productivity of your manufacturing operations. We also assist with training of the production and maintenance team.
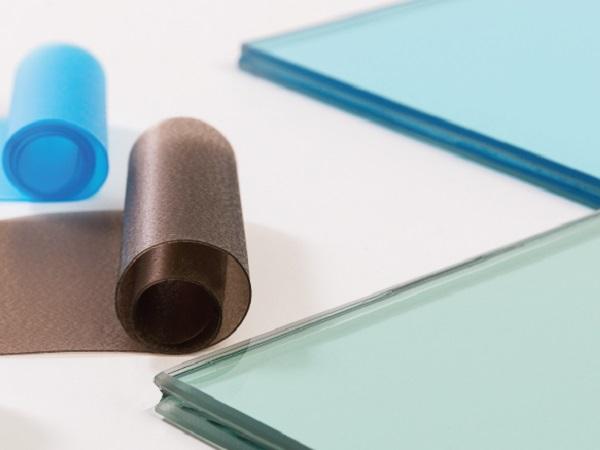

Add new comment