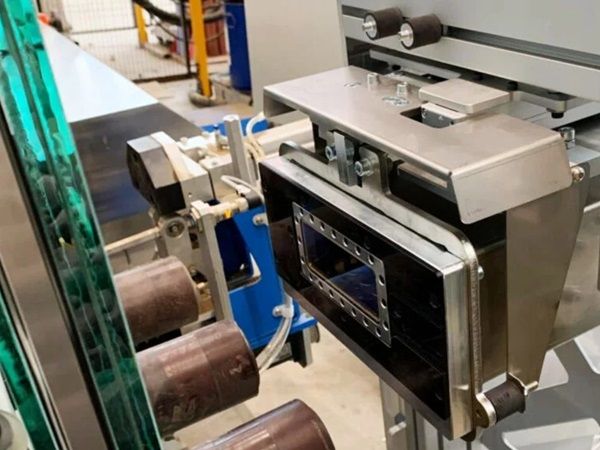
Date: 17 September 2024
Sparklike Laser Integrated offers non-destructive, precise measurement of gas concentration within IGUs, ensuring optimal thermal performance and durability of IGUs. By incorporating this technology into a production line, manufacturers can continuously monitor and verify the gas filling processes, reduce gas leakage, and maintain airtight seals. The integration of the Sparklike Laser Integrated supports the production of high-quality IGUs, meeting industry standards and improving overall product reliability.
Insulating Glass Manufacturing Line
Here are the basic steps to make insulating glass.
- Glass Cutting: Large glass sheets are cut to the desired size.
- Spacer Preparation: Spacers, typically made of aluminum, are cut and filled with desiccant material to absorb moisture.
- Assembly: The spacer is placed between two glass panes to create a sealed unit.
- Primary Sealing: Butyl is applied as the primary sealant to bond the glass and spacer.
- Gas Filling: The unit is filled with insulating gas, like argon, to improve thermal performance.
- Secondary Sealing: A secondary sealant, typically polysulfide or silicone, is applied around the edges.
- Quality Control: The final unit is inspected for defect.
Where is Sparklike Laser Integrated Installed in the insulating glass production line?
Sparklike Laser Integrated is typically installed after the gas press. Sparklike customer Isophon GmbH has combined their gas monitoring with Sparklike Laser Portable to double-check that measuring results do not change between measurements. Below is an animation of Sparklike device in the insulating glass production line.
Information and Actions Required for Installing the Insulated Glass System
- During the purchasing process, the glass type and other specifics are mapped to ensure the device fits the IG line. In other words, both parties will have a clear understanding of what their machines and systems are capable of. The device’s limitations and features are known by the customer before installation.
- A designated contact person from both the customer and the insulating glass manufacturing line producer will provide necessary information and prepare the settings to ensure a smooth installation of the Sparklike Laser Integrated system. This contact person must also be available during the installation in case assistance is needed.
Items to be Arranged:
- 240V Power Supply – A 240V power source must be provided for the Sparklike Laser Integrated system, as we cannot guarantee functionality under lower voltage conditions.
- High Voltage Coupling – For safety reasons, the customer’s electrician must handle any high voltage Coupling required during the installation.
- Anchoring of the Measuring Station – The customer is responsible for anchoring the measuring station to the production site. While we can supply the concrete anchor, the installation into the floor is performed by the customer.
- Access Equipment – A ladder or aerial access platform must be provided to work on the upper parts of the Laser Integrated system.
- Connection Setup – Sparklike must have internet access and a connection to the IG production line so the integration can begin immediately. The customer must also ensure that all data security protocols have been considered to allow Sparklike to perform the necessary software installations.
- Approval Protocol – All parties must be aware of the approval protocol before the installation begins.
- Installation Schedule – The installation schedule must be agreed upon and approved by all parties involved.
- Production Interruptions – The customer must be prepared for minor production interruptions during the integration process.
Customer Case: Isophon Glass Gmbh
Isophon successfully implemented Sparklike Laser Integrated into their IG line to enhance quality control and automate gas measurement in insulating glass units (IGUs). The system was installed directly into their production line, allowing non-destructive measurement of insulating gases like argon and krypton. This integration resulted in increased efficiency, ensuring consistent product quality and traceability. The collaboration underscores Isophon’s commitment to innovation and high standards in IGU production.
Read Isophon blog posts:
Sparklike Laser Integrated™ Installation at Isophon
How Isophon Successfully Implemented an Automated Insulating Gas Measurement System to Their Ig-Line
Contact Sparklike for more information and support on measuring argon concentration in IGUs.
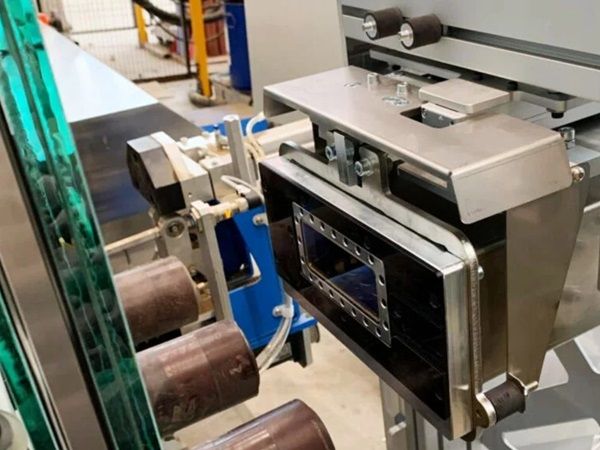

Add new comment