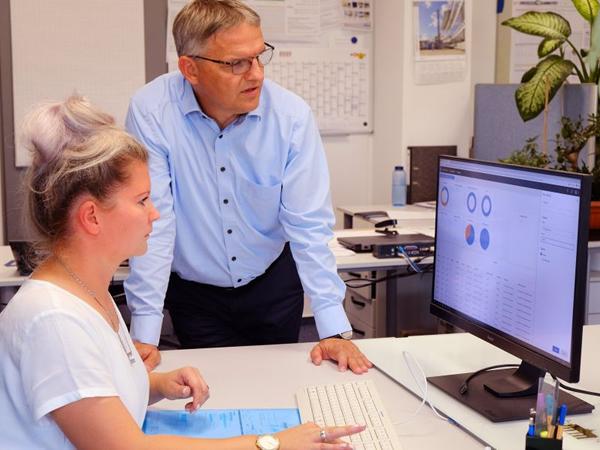
Date: 5 November 2020
Modern, digitalized production systems offer ever more sensors and interfaces from which valuable data can be tapped. What has been missing thus far, however, was a uniform, higher-level platform on which the data from an entire machine park can be combined automatically for integrated use and evaluation. Where all machines "talk" to the user and the connected software systems in the same language.
The challenge here, in a mixed production environment with different machines, is to read out data from state-of-the-art digitalized systems as well as older machines with a lower degree of digitalization.
This is precisely why we developed A+W IoT Smart Trace. This system is the intelligent platform to which any machine park can be docked, read out, enriched with metadata (generated and sent when, where, by whom, under what conditions), and evaluated. Thanks to A+W IoT Smart Trace, glass processors can save, document, and evaluate the production of a single sheet, an order or a whole batch seamlessly. The system provides users with all required information with just a mouse-click.
Schollglas Sachsen: automating data collection and evaluation
Schollglas Sachsen could be called the "project business location" among the 13 Schollglas branch offices. The Schollglas Group is a high-performance full-range provider of top-quality products across Europe; it is also involved in projects around the world. The company has all the technical prerequisites and knowledge to handle even the most complex projects. In a 30,000 sq m production facility, 400 employees produce all kinds of architectural and highly-specialized vehicle glass from 120 different types of glass; in particular the whole spectrum of technical and safety glass and performance IG, on through to jumbos.
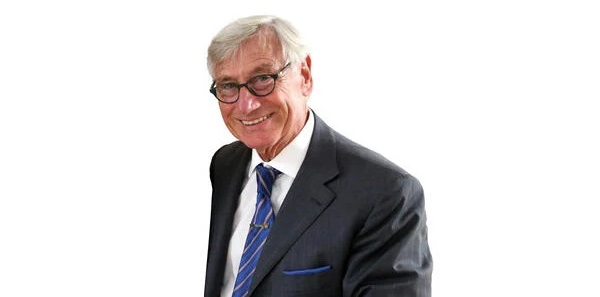
This is where Schollglas demonstrates its power of innovation: production is done with a special GEWE®-com connect laser system, a modern glazing solution for buildings and trains, which enables mobile radio signals to pass directly through train and building windows – this is something that not every glass processor can offer.
State-of-the-art grinding and printing techniques enable creative solutions, unite the best performance and elegant design, and open up paths to fascinating architecture and breathtaking facade design. Exemplary projects are handled jointly with partners, frequently metalworking companies, which are among the best in the world and push things right to the boundaries of what is technically feasible. Schollglas IT Manager Torsten Brose: "There is practically no flat glass that we can't produce here."
Companies that move in such spheres and regularly deliver large quantities of sheets around the world need continuous, secure production documentation for individual sheets and complete batches. Reliable quality assurance is essential. Of course Schollglas Sachsen already takes care of this, but with complicated, manual processes where a typo or reversed digit can cause incorrect assignments and thus make tracing more difficult. For homebuilders there is surely a solution, but what happens with mammoth projects involving hundreds of sheets? In case of a complaint, searching for the information in various sources can take hours or even days. With A+W IoT Smart Trace, this data is available at any time with just a mouse-click.
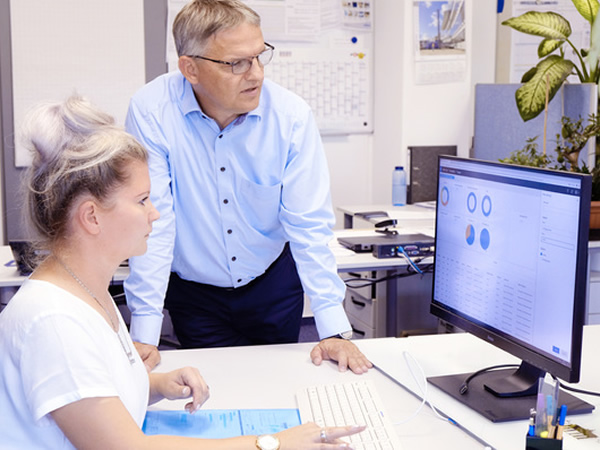
The pioneering project: managing production data digitally
Such complex digitalization projects as A+W IoT Smart Trace should not be implemented right away with all technologies – especially if the users are still inexperienced. Processes have to be redefined, employees incorporated and trained. No catastrophes such as machine shutdowns, lost orders, etc. are looming, but complex project such as an IoT data collection and management system are better built carefully and step by step. For in the end, the result should be an intelligent data container, which is not just complete but also easy to access – with an ergonomic interface and clever dashboards. It has to be possible to search for, find, and further utilize documents quickly and easily with just a few mouse-clicks.
That's why Schollglas Sachsen started with the technologies cutting, insulated glass, TG, and heat soak.
"Today, IoT offers an endless number of possibilities that are not always easy to evaluate. With a consciously limited project that already offers great benefits, we have opened up entirely new paths."
To every sheet its batch!
The batch number of each sheet is recorded in cutting. That which earlier was done with pencil and paper is now done using the A+W Realtime Optimizer, the A+W cutting computer.
In insulated glass production, employees only record the batches of sealant when they change them. Instead of entering the number of each sealant package manually in lists, today scanning a barcode on the pail is an easy, practical solution with which the batch number assigned in incoming goods is transferred automatically to the A+W IoT Smart Trade data platform. The assignment of the batches to the individual insulated glass sheets is then done completely automatically since the system can determine the sealant actually used via the sheet's BOM. Therefore, there is no extra work for the employees if the sealants change frequently (at any given time, the machine generally has access to different sealants).
In just a few simple steps, the components of an insulated glass sheet can be linked securely to batches (even after a few years have passed) and displayed quickly with a mouse-click.
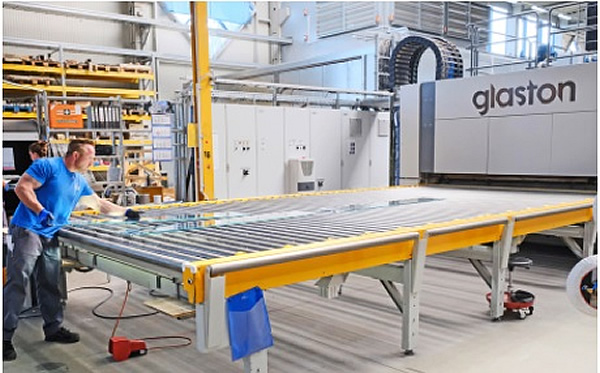
Added value for customers: proof of quality for each TG sheet
State-of-the-art TG furnaces generate a lot of data that is very important for continuous quality control; you just have to coax the data out of the furnace so that it is prepared clearly and can be archived. A+W IoT Smart Trace creates a clear PDF list for each tempered sheet with all relevant data that was generated by the furnace's various sensors and scanner systems – including a depiction of the furnace bed assignment. This data is not just stored in the archive, it is also made available to the customer with each order.
From recording to visualization
The whole process in production is not spectacular to look at. Barcodes are entered or scanned on production computers. Employees love this solution because their work is easier – they gain a bit of security with the entry, the batch assignment process is more orderly and systematic.
Evaluation of the data and linking to the ERP system is done in the commercial area with intelligent tools such as ergonomic dashboards, where all IoT data can be visualized in clear charts according to the user's requirements. The data from A+W IoT Smart Trace can be loaded directly, combined, and displayed intelligently.
In order processing, there is another strong visualization tool: a sidebar in which all data associated with the order is displayed interactively. The ERP employee sees all details that were recorded and sent via A+W IoT Smart Trace to data storage, including the batch numbers, the PDF generated by the furnace with all tempering data, the batch numbers of the TPS material from the IG line, and the heat soak report.
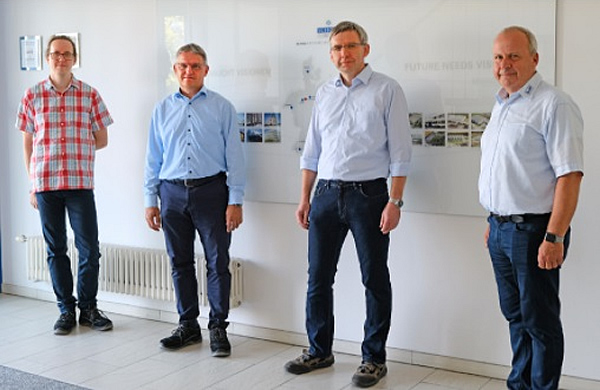
Digitalization as customer service
With the four pioneering technologies, the project is still in an early phase, but Torsten Brose, IT Manager of the Schollglas Group, is enthusiastic and can already see the benefits:
"We have piloted a number of software solutions with A+W and we are clearly on the right path with A+W IoT Smart Trace." With the automatic coupling of machines and generated data, we achieve the greatest benefit with much less work – which saves time and money. Our customers are the ones who really profit from this. We can now provide proof of quality with every order as an additional service, regardless of whether anyone inquires about this. With the incorporation of all machines in A+W IoT Smart Trace, we achieve an enormous degree of digitalization across all systems and we can realize a further piece of Industry 4.0."
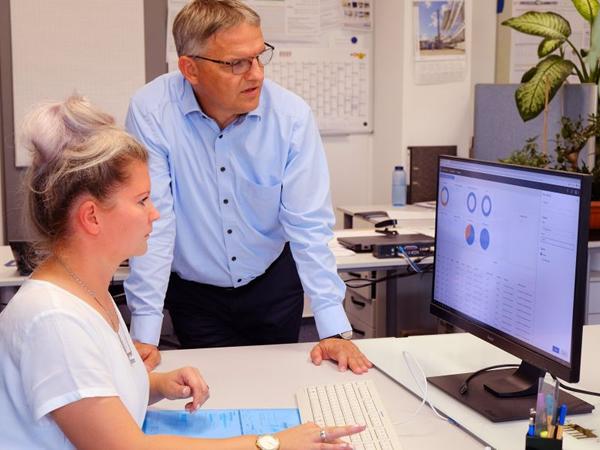

Add new comment