Challenging Glass 6
Conference on Architectural and Structural Applications of Glass
Louter, Bos, Belis, Veer, Nijsse (Eds.), Delft University of Technology, May 2018.
Copyright © with the authors. All rights reserved.
ISBN 978-94-6366-044-0, https://doi.org/10.7480/cgc.6.2150
Authors:
- Marcin Kozłowski - Faculty of Civil Engineering, Silesian University of Technology, Gliwice
- Peter Lenk - ARUP, London
- Michael Dorn - Department of Building Technology, Linnaeus University, Växjö
- Dániel Honfi - RISE Research Institutes of Sweden, Borås
- Johan Sjöström - RISE Research Institutes of Sweden, Borås
This paper focuses on a recently developed concept, in which glass is combined with timber to provide post-breakage strength and ductility. This combination allows for good post-breakage performance and overall robustness of timber-glass composite beams and wall elements, which has been reported in several publications. The application of timber-glass elements in practice, however, raises important issues related to structural fire performance.
The paper elaborates on this issue and provides general information about the behavior of glass, timber and adhesives at elevated temperatures and under fire conditions. Furthermore, it presents ideas and strategies developed for potential application of timber-glass composites in practical situations. The paper presents also initial results from an on-going research project on fire performance of timber-glass composites.
1.Introduction
Its inherent brittleness, much lower tensile than compressive strength, risk of fracture due to practically unavoidable defects and decrease of strength with time make glass challenging for structural applications. To overcome these undesired failure characteristics in glass structures, several promising solutions have been tested and developed in recent years including applications where glass is combined with other materials to provide post-breakage strength and ductility thus enhancing post-breakage performance and the overall robustness of the design (Kozłowski 2012; Martens et al. 2015).
Recent trends in design are also considering design aspects of sustainability and circular economy, where timber-glass composites could provide some positive advantage against more traditional solutions. Such a recently developed concept uses timber flanges glued to glass webs creating timber-glass composite beams with an effective load carrying behavior (Hamm 1999; Hamm 2001; Cruz and Pequeno 2008; Blyberg and Serrano 2011; Blyberg et al. 2014; Kozłowski et al. 2014, Premrov 2014; Kozłowski et al. 2016; Rodacki 2016). The same idea can be applied for walls, in which a glass pane is bonded to a timber frame (Ber et al. 2014; Dorn et al. 2014; Ber et al. 2015; Kozłowski et al.2015; Strukelj et al. 2015).
The concept of timber-glass composite beams involves a glass web made of glass (primarily annealed float glass) and timber flanges bonded together with an adhesive(Kozłowski et al. 2015). Under loading the stress in the glass web increases until it reaches the tensile strength of glass resulting in a brittle failure, however, in does not lead to the total failure of the composite beam. Even if the glass web fails, the glass shards are held in place by the timber flanges and the beam can still withstand loading. The timber flange with the bond line adhesive connection acts as a bridge: the forces that before failure were carried by the tensile zone of the web are now transferred by the timber flange, see Fig. 1. Therefore, the concept prevents brittle failure of the beam, provides ductility and offers a post-breakage strength after initial glass failure (e.g. caused by overloading or vandalism), see Fig. 2.
The integrity of the beam and continued load-bearing capabilities are only guaranteed when using annealed float glass. The use of strengthened glass on the other hand leads to immediate failure of the beam since the web fails in its entire length. Additionally, very small pieces form which do not stay in place (in contract to large shards in annealed float glass). On the other hand, much higher loads can be achieved when using strengthened glass webs.
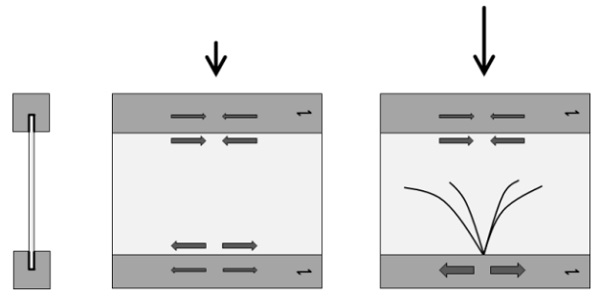
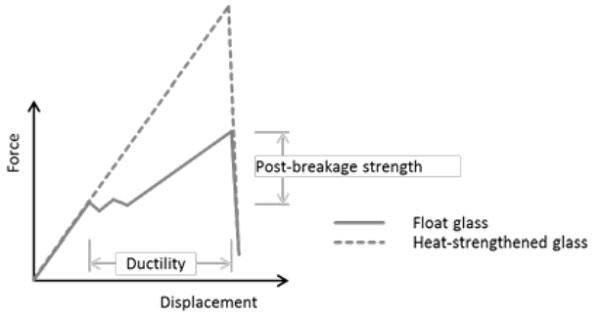
Limited practical applications of timber-glass composites can be found in literature and most designs are still in the concept stage. The idea developed by Kreher was applied in the roof structure of the Palafitte Hotel in Monruz, Switzerland (Natterer 2002; Kreher 2004), see Fig. 3. The beams support a light roof and transfer snow and wind load to steel posts hidden inside external walls. Each one of the 6000 mm long and 580 mm deep I-shaped composite beams composed of a single glass pane and timber flanges bonded on both sides of the glass web. The upper flange consisted of two solid timber blocks 100×160 mm2 whereas the lower flange involved two timber blocks 65×65 mm2.
For the web a 12 mm thick glass pane made of fully tempered glass was used. Due to the lack of post-breakage strength of toughened glass, which breaks into small shards, the upper flanges were designed to resist external loads even in case of total failure of the glass web. This over-dimensioning ensures the structural safety of the structure. The beams were examined in four-point bending before, showing the maximal load obtained during the testing was approximately three times bigger than the design load on the roof structure.
Taking the example of a pedestrian bridge, Vallee et al. (2016) present the whole design process, from the early concept stage, through numerical simulations and manufacturing to the final design. To the knowledge of the authors,the only economically successful implementation of timber-glass composite is a façade system reported by Fadai and Winter (2014) and Jiang et al. (2014). It involves glass panes bonded onto timber connecting strips with a silicone adhesive mechanically fixed to the main structure made of timber. Large glass panes are used in a recently developed concept called timber-glass buildings, in which large windows together with the main structure made of timber allow to achieve high energy efficiency, see Fig. 4.
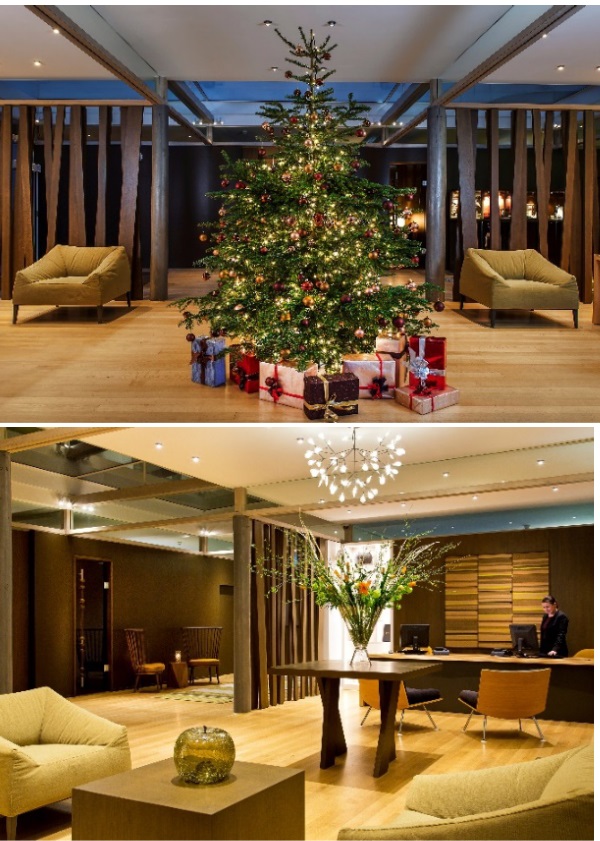
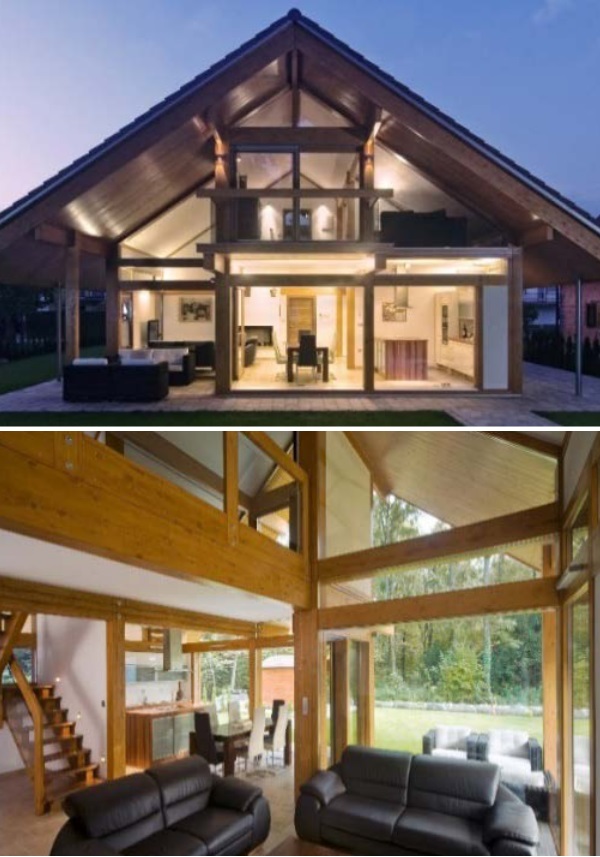
The application of timber-glass elements in practice, however, raises an important issue related to structural fire performance. The behavior of timber in fire and adhesives at elevated temperature is well known phenomena. However, up to now little is known about the effects of temperature changes on the performance of structural glazing (Bedon 2017; Bedon et. al 2018). This is particularly true at high temperatures to be expected in real fire conditions.
Furthermore, even in “normal” conditions, glass elements absorb and transmit a significant amount of solar radiation. The absorbed radiation significantly increases the temperature of glass, which may reach temperature of 50-80°C in summer conditions (depending on if and what type of coating is applied). These temperatures highly influence the mechanical properties of interlayers and the adhesive creating the bond line connection between the glass web and the timber flanges.
The current contribution discusses some interesting issues relevant for the application of timber-glass composite structures in practical situations, where fire safety is a primary concern. Firstly, the behavior of glass, timber and adhesive at elevated temperatures and fire conditions is presented. Secondly, examples of strategies for timber-glass composites are presented and discussed. Further, initial results of experiments are shown and directions of further studies provided. Finally, general conclusions and practical recommendations are given.
2.Materials
Timber-glass composites as presented before consist of the glass elements and timber parts at the edges of the glass (either on top and bottom in the case of beams or around the perimeter in the case of wall elements), glued together by an adequate adhesive. It is not only the individual materials’ behavior but also the combination that is to be checked for the case of fire. This section provides general information about the behavior of glass, timber and adhesives at elevated temperatures and fire scenarios.
2.1.Glass
Glass itself is non-combustible and does not lead to drop-formation which is of course beneficial. Still there are severe disadvantages with the material. In a fire scenario, the glass will be heated up rather quickly, leading to large temperature gradients in particularly the thickness direction. The temperature gradient will most likely lead to the fracture of the glass pane which is exposed to the fire within a matter of minutes. Needless to say, a single-pane construction will not be stable longer than that and will hence not be of any use.
The use of laminated glass elements is anyway inevitable for a number of other reasons than the fire case. Laminated glass with multiple panes is to be studied with respect to the loss of composite action due to loss of stiffness in the interlayer material. Again, the heat will warm up all the panes and the interlayers. With the interlayers made from polymeric materials they will soften quickly. This softening may not lead to delamination in the first place, dependingon the application the structural load-bearing capacity will still decrease. In the case of shear walls the resistance against buckling will decrease due to a reduced bending stiffness of the glass pane; in the case of beams the load distribution between the panes will not be working in the same way as for the ambient temperature.
Little is known about the effects of temperature changes on the performance of structural glazing (Vandebroek 2014).Besides known influence of temperature on mechanical and thermal properties, glass related phenomena, such as thermal shock, frame constrain and shading effects are critical for glass when exposed to high temperature and fire scenarios.
Density of glass as a function of temperature has been studied by de Sa (1986) and Fluegel et al. (2008). In general, the density of glass decreases with increase in temperature, see Table 1. Below glass transition temperature (Tg), which is approximately in the range of 400-550°C (Le Bourhis and Rouxel 2003; Rouxel 2007), the decrease in density is primary due to the thermal expansion of the volume of glass (Zarzycki 1982). Above Tg, the decrease is faster due to higher expansion coefficient in the super-cooled liquid state. Also, there is time dependence involved near Tg due to structural relaxation effects which are dependent on the thermal history of the glass. The density at 900°C is reduced by about 5% compared to ambient temperatures.
Table 1: Variation of density of soda-lime glass with temperature (de Sa 1986).
Elastic modulus, tensile strength and linear thermal expansion coefficient of glass may significantly affect the behavior under fire loads and subsequent cracking and fallout of glass shards. Rising temperature corresponds to the decrease in the modulus of elasticity (Badger 1935; Shen et al. 2003), see Table 2, caused by accelerated corrosion (Scholze 1991). Thermal expansion is an important property when predicting thermal stresses that develop in a structural member under fire conditions. In general, the linear thermal expansion coefficient increases with rising temperature, however, the relationship is not linear. The temperature dependence of expansion is closely tied with the temperature dependence of density (Scholze 1991), see Table 2.
Linear thermal expansion coefficients, presented in Table 2, were generated (using a polynomial curve fit into the results reported by Scholze (1991)) for the same range of temperatures as for the modulus of elasticity. Despite the fact, that tensile strength is a critical parameter for glass, it is the least well known among other parameters (Wang 2014). Strength parameters of glass at elevated temperature are very difficult to test and definitely require further studies (Rouxel and Sanglebuf 2000; Xie et al. 2011; Li et al. 2015).
The results presented show significant discrepancies and cannot be directly compared. In general, strength of glass decreases with temperature, at Tg and higher, it drops drastically. Results are reported that by treatment of the glass at high temperatures (at approximately 100°C) the tensile strength increases slightly and then decreases (Wang 2014). This is probably caused by evaporation of H20, present before (Scholze 1991).
Table 2: Variation of modulus of elasticity and linear thermal expansion coefficient of soda-lime glass with temperature (Shen et al. 2003; Scholze 1991).
The literature review above concludes that advanced viscoelastic material models to capture the material behavior of glass are required, especially if the temperature is above Tg. Material models were recently summarized by Aronen (2012) and Nielsen (2009), based predominantly on the work of Narayanaswamy (1978), Carré and Daudeville (1999) and Daudeville et al. (2002).
2.2.Timber
Wood is understood as a material that is burning easily, which in the case of structural behavior may be a misinterpretation. With structural timber, the “size effect” is beneficiary since the area exposed to fire is determining how it burns. Wood is burning/charring from the outside in thickness direction at a rather well-known rate with the core material intact structurally with respect to stiffness and strength. The burned wood becomes a layer of char which loses all strength but retains a role as an insulating layer preventing excessive temperature rise in the core (Buchanan 2001).
This is in general advantageous in timber structures compared to other building materials (steel loses stiffness when heated up; concrete is prone to spalling from the outside, exposing the reinforcement to fire). The usual approach is hence to oversize the timber cross-section allowing for a sufficient core or to protect some of the outer surface from fire exposure by suitable fire-resistant protection (e.g. gypsum board).
2.3.Adhesive and interlayer
The adhesive as the third material is possibly the one being most sensitive to heat and fire exposure. Adhesives are commonly used to transfer shear forces between timber and glass, whereas interlayers are applied to transfer loads between glass plies thereby increasing the redundancy of glass structural elements should one or several plies break. Unfortunately, the stiffness of these materials decreases significantly as temperature rises (they even melt), therefore they no longer fulfil their original purpose provided at ambient temperature. Adhesives become soft already at modest temperatures, may start drop-formation or simply burn up.
The challenge is therefore to avoid these phenomena by suitable constructive measurements. In timber-glass composites, firstly, the bond-line between the glass and the timber may not become exposed to fire/heat, e.g. by using a sealant withstanding the imposed temperatures. Secondly, indirect heating-up by heat conduction from the glass-side may prove fatal for the adhesive; not from the wood-side though since heat conduction is low in wood. When using laminated glass, the interlayer material may also melt and become soft. The use of timber around the edges though keeps the interlayer material in place and hence drop formation or evaporation of the adhesive, both a potential risk to people, is minimized.
3.Strategies for timber-glass composites in fire
The unity of a timber-glass composite may also be studied from the aspects of the use-scenario of the elements since the requirements are different if the elements are used in a load-bearing case (REI classification acc. to (EN 13501-2 2016)) or “simply” as partitioning walls (EI classification acc. to (EN 13501-2 2016)). There are different solutions, depending on the level and duration of fire protection by having a heat-reflective surface coating minimizing heat radiation or interlayers of waterglass which swell up and form a foam barrier which stops the spread of fire. Solutions on the market are e.g. Pyrostop and Pyrodur by Vetrotech; and Vetroflam and Contraflam by Pilkington, where not only the glass part itself is certified but also the respective framing details are specified.
Timber-glass composites, such as beams and walls can be considered from two angles. The first idea involves the load-bearing glass pane being protected by a fire protection layer, also made of glass. The second approach relates to the loss of adhesive bond between glass and timber caused by the lack of resistance of the adhesive under elevated temperatures. It includes mechanical coupling systems which activate after failure of the adhesive bond.
3.1.Fire-Protection layer
In order to achieve an R-classification (or a combination with particularly E and or I acc. to (EN 13501-2 2016)), additional measures have to be taken. A previous work by (Karlsson et al. 2017) studied the fire case in timber-glass composites on the example of load-bearing wall elements. The case of composite wall elements was studied whereby the main field of interest was the use in outer walls, assuming only one side exposed to fire, namely the interior, and the fire case from the outside excluded. The study proposes that the fire-protecting and the load-bearing functions should be separated in order to secure both aspects. A double-layered design decouples the function, thereby having an EI-layer on the fire side and an R-layer on the outside (see Fig. 5a).
An important aspect is to guarantee the integrity of both layers, hence not to endanger its respective function, i.e. making sure that the load-bearing layer is not getting (too) hot, neither may the fire-protection layer be loaded un-proportionally. Assuming this is solved for the fire-protecting layer (by e.g. the commercial variants), the mechanic decoupling may be done by using a solution with the respective bonding of the glass layers to the frame. Hereby the fire-protection layer is bonded by a soft adhesive and a thick bond-line whilst the load-bearing layer is bonded to the frame by a stiff adhesive and a thin bond line.
This combination of material (adhesive) and geometric (bond line thickness) stiffness is attracting the forces towards the load-bearing layer while there is more slip in the bond of the fire-protecting layer. The detailing of this solution has so far not been studied with respect to geometry, choice of adhesives and the glass package. Furthermore, it may depend significantly on the load-level to be imposed as well as the fire-safety duration.
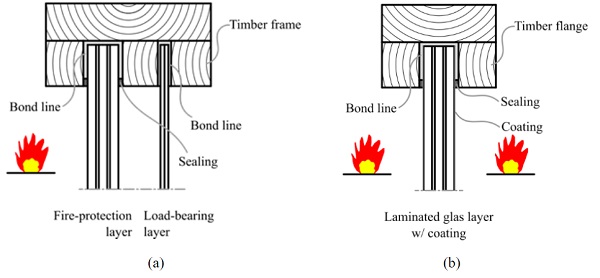
Looking at beams, there are some different conditions. The application for beams is seen in interior uses, in girders in open room solutions or similar. Therefore, there is no dedicated side facing the fire with the other side without need for protection which needs a different design as presented above. Additionally, the beams supposed to be mounted on ceiling level, hence in the warmest region of the room (wall elements may be regarded cooler for a longer time at least close to the bottom). This may lead to a quicker warm-up.
Implementing the solution described for wall elements would lead to a triple-layer design with a fire-protection layer on either side of the load-bearing layer. This solution is feasible but it may not be practical as the set-up is becoming too thick since the layers should not be too close together in order to have sufficient bonding and bearing capacity in the load-bearing layer. Another solution could be to have only one layer of glass with the load-bearing and the fire-protecting layers combined, see Fig. 5b. Again, the inner glass panes are for load-bearing purposes whilst the outer panes are for fire protection.
The outer panes are again doomed to be destroyed by the fire with foam protecting the panes behind. Depending on the safety level, possibly multiple sacrificial layers need to be laminated together. The biggest problem might be how to guarantee the functionality of the fire-protecting and the load-bearing function. Since there is only a single glass package, a mechanic decoupling cannot be ensured as easily, since all layers function together. In the warm-case, only the inner panes are taken into account for load-bearing purpose whilst for the cold-case all layers are taken into account. The warm case is also special as the outer layers are broken whilst composite action of glass and the timber flanges needs still to be intact.
As a variant, a stepped solution can be thought of whereby the inner panes are wider, hence protruding longer into the flanges and can so be bonded on the sides towards the flanges. A further variation is to rely only on the coating to minimize temperature in the glass pane, hence assuming the whole glass package being intact in the warm case. This may be linked to a shorter time of resistance than a decoupled option or a solution with a foam layer. The timber flanges itself are again regarded as to be of a minor problem. An over-dimensioning of the cross-section with respect to the charring from the outside may be sufficient. Alternatively, there are also coatings available for timber which form a foam layer and thereby reducing the fire reactions. Out of aesthetic reason this may not be an optimal solution (for the cold case).
3.2.Alternative mechanical coupling systems
The previously discussed timber-glass composite beams rely on a chemical bond adhesion to transfer coupling forces between the timber flange and glass shear wall. At elevated temperatures this may still be feasible but high temperatures may require resistive adhesives. This chapter will outline two basic structural concepts of timber-glass composite beams where mechanical couplings between the glass and the timber were investigated and possible solutions are presented in detail. Two distinct structural systems are selected from an initial pool of ideas produced by this research group. The structural schematic for each option is presented in Fig. 6.
The first option considers a continuous glass panel over the entire beam length. The glass shear wall is notched with shear keys. The shear forces are transferred via direct contact with hardwood timber flanges and secured with elastomeric bearing blocks. The primary function of the bearing blocks is to provide appropriate stiffness to accommodate temperature and moisture movement between glass and timber. The top and bottom hardwood flanges are milled with grooves where the glass shear wall interlocks. Timber flanges are then mechanically together via edge beams.
The second option involves dividing the glass shear wall into smaller sections of reasonable length, thus the total cost of this composite beam could be reduced. With this option, the glass panels transfer load in compression only with small diameter tension rods hidden at the panel joints pre-tensioning the system to account for thermal movements, shrinkage, asymmetric loading etc. However, it should be noted that this system is more time consuming in terms of engineering design and installation.
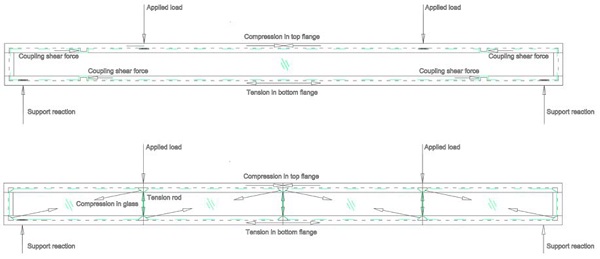
A non-linear, finite element analysis investigated the feasibility and structural behaviour of both systems under static point loads applied to the top of the composite beam. The top flange is restrained out-of-plane to prevent buckling instability. Analysis results for both options are presented in Fig. 7. As expected, the shear key option has approximately twice the stiffness of the glass truss option, driven by the continuity of the glass panel spanning the length of the beam. Here, the glass is working predominantly in bending with relatively modest coupling shear forces of 1.3 kN per connection. Conversely, in option 2 the glass panel is divided into separate elements with ‘soft’ interfaces reducing stiffness.
The glass acts in compression with a relatively larger force of 8.7 kN. Analysis suggests that this option behaves like a glass beam with relatively small contribution from the timber flanges, acting in a true composite nature. It should be noted that a timber cross section as presented in Fig. 5 was analysed. It will be interesting to examine the influence of a stiffer flange beam. However, the most significant investigation will be to understand the behaviour of both distinctive systems under fire load and review their post failure capacity.
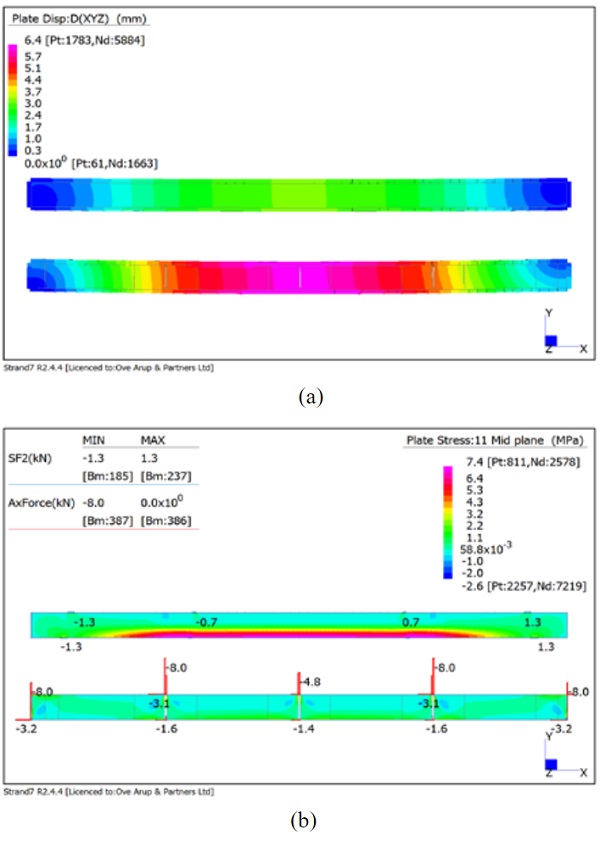
The timber edge beam profile is shown in Fig. 8. Charring rates are calculated according to the timber used and thickness is increased accordingly. The minimum cross section inertia of the edge beam to resist accidental load combination as prescribed in the codes shall be carefully calculated and experimentally tested so that the required fire performance is achieved.
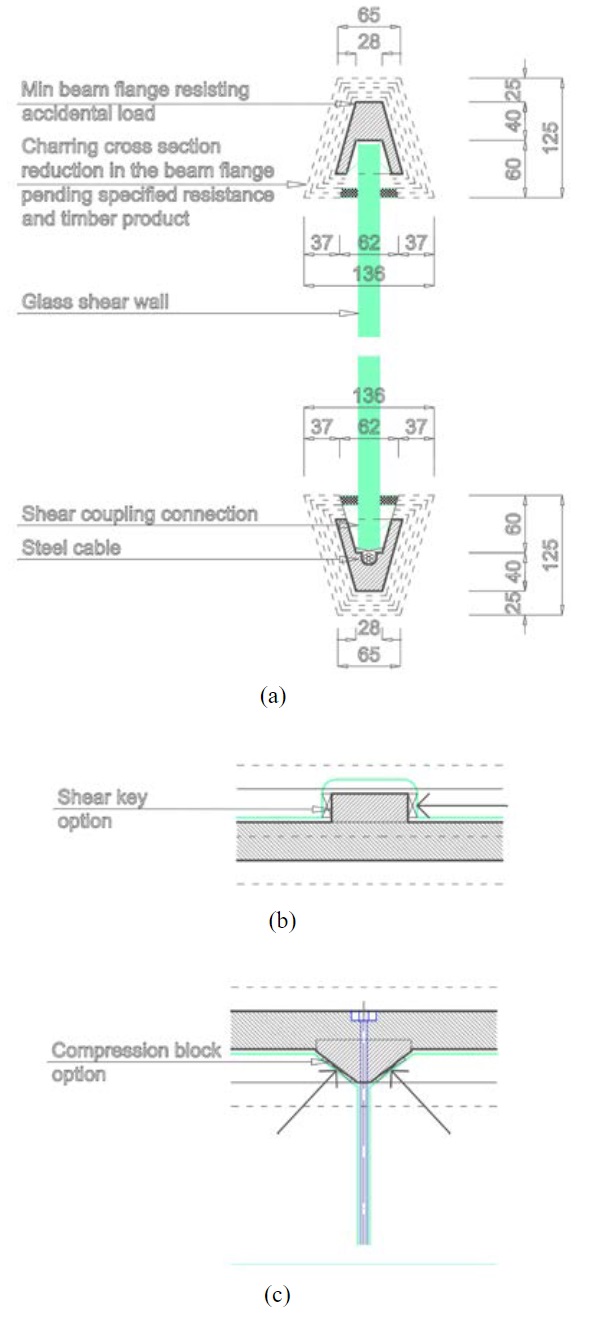
Finally, two practical applications of the discussed options are tested by a design team within Arup. Two competition entries for a short pedestrian bridge with 20 m span are presented in Fig. 9.
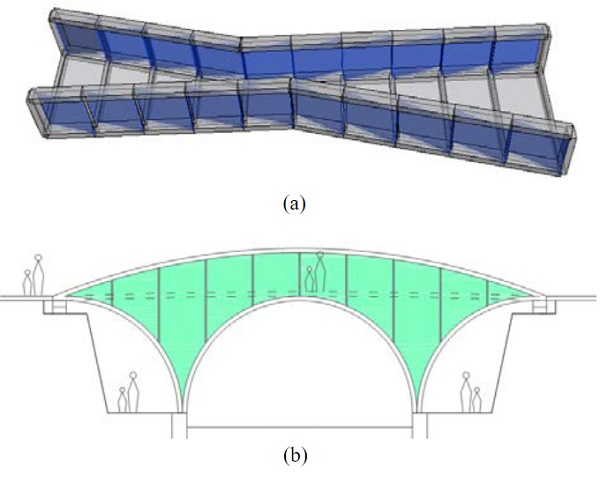
The first concept benefits from the timber-glass compression truss optionwithglass panels envisaged as inclined overlaying shingles. The second concept employs a traditional timber arch bridge reinforced with a glass shear wall. These concepts showcase the scale of projects where the ideas presented in the paper could be potentially further deployed, i.e. that traditional bracing diagonals are replaced with structural glass where the load is introduced through contact bearing. The fire resistance of the glass can be improved by fire protective shielding as discussed earlier. It should be noted that the alternative mechanical coupling concepts are initial ideas, not fully developed nor tested. However, the authors believe that they are feasible and plan further investigations into this direction in the next stage of the project.
4.Experimental work
An ongoing research project in Sweden aims to increase the knowledge about the performance of timber-glass composite structures. A major part of the project is to carry out laboratory experiments on such structures at elevated temperatures. The objectives of the experimental work include a better understanding of heat transfer in monolithic and laminated glass and determination of thermal properties of structural adhesives (used for gluing together timber and glass). The information obtained by the laboratory testing is used to develop a coupled heat transfer and mechanical FE-model to simulate structural behavior under varying temperature. With the verified numerical model virtual experiments can be carried out to explore viable design solutions to improve the fire performance of timber-glass composites.
The first series of tests were focusing on the thermal characteristics of adhesives and interlayers. For this paper two adhesives were studied using simultaneous Differential Scanning Calorimetry (DSC) and Thermogravimetric analysis (TGA). The materials, both two components, were DP490 epoxy adhesive by 3M and SikaFast acrylic adhesive by SIKA. They were heated at a rate of 2°C/min up to 300°C and at 5°C/min (only TGA) up to 800°C in a nitrogen atmosphere using a thermal analyzer STA F3 Jupiter by Netzsch. Considerable mass loss of the adhesives has clearly started at 324°C and 348°C for the SikaFast and DP490 adhesive, respectively, see Fig. 10.
For the SikaFast, a residual mass of 25 % is left until 700 °C whereas 15-20 % mass residual is found for DP490 until the end of the measurement. Very small (1-2 %) mass losses can also be observed when the materials soften significantly around 200°C. For low temperatures, endothermic processes, most probably related to melting of some crystalline fractions and bond breaking are noticed for the DP490 adhesive. The latent heat of the process is however very small, 11.5 J/g, compared to melting of more crystalline polymers such as polyethylene (100 – 200 J/g).
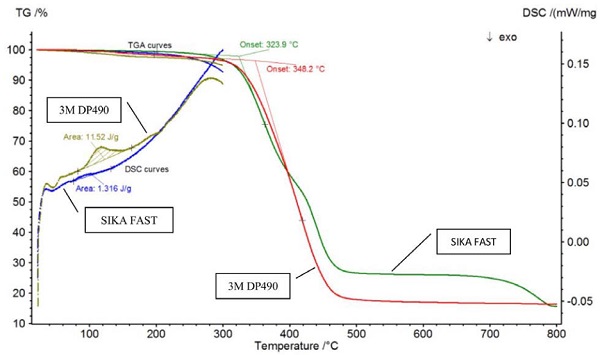
In addition, five interlayer materials were tested by the same technique. They were QS41 (acoustic PVB), RB71 (clear PVB), DG41 (stiff PVB), Vanceva (coloured PVB) and SG (SentryGlas). All of the interlayers show an onset of mass loss around 300°C except for SentryGlas for which it is around 450°C. Almost no residual materials exist above 500°C.
At lower temperatures, the other interlayers have no or marginal endothermic processes whereas SentryGlas exhibits two more distinct processes between 40 and 100°C with a combined latent heat of about 43 J/g, see Fig. 11.
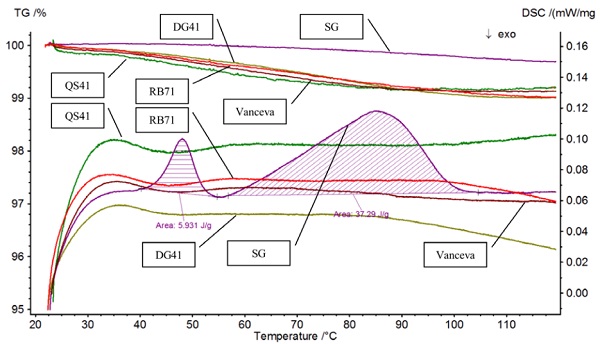
Another series of test, currently ongoing, aims to explore how temperature changes within glass when exposed to heat and how temperature differences lead to breakage. Previous tests at the same laboratory have been carried out by Debuyser et al. (2017) using a radiant panel to subject sheets of glass to a constant heat flux. In the new series of tests, the restraining and shading effects at the boundaries are eliminated as much as possible to obtain breakage caused by the temperature gradient rather than local stresses due to restraints by the supports (see Fig. 12a).
One lesson from these tests is that when the interlayer starts to decompose at the temperatures where mass loss is evident from the TGA tests, bubbles are formed in the layers combine with discoloration. However, despite this decomposition, the panes, which so far have been without external loading, stick together. Furthermore, besides annealed glass specimens, heat strengthened and toughened glass specimens are studied.
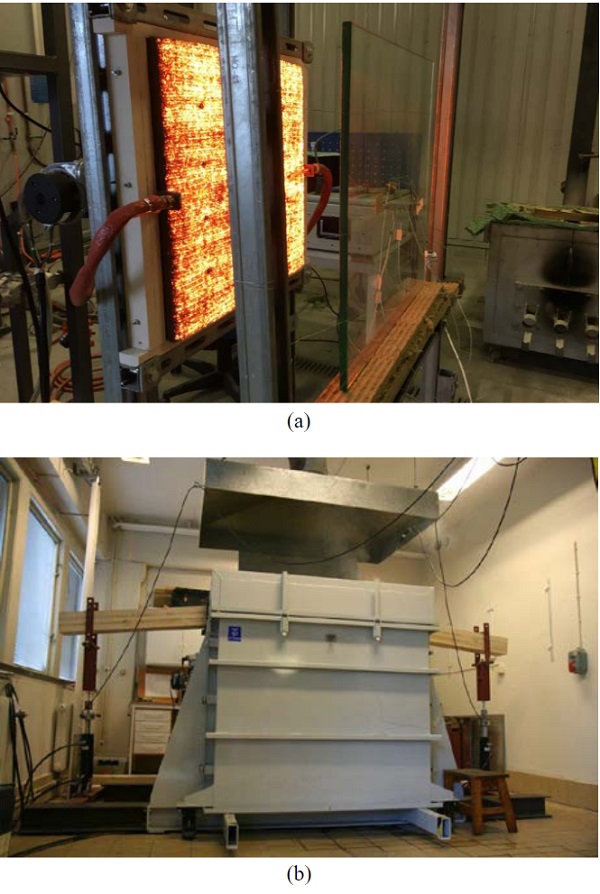
The final test series is focusing on beams under mechanical loading. Timber-glass composite beams will be scaled down to fit a furnace of a size about 1×1 m2, see Fig. 12b. Four-point bending will be applied, in a setup similar to Louter and Nussbaumer (2016). It is expected, however, that the timber flanges will prevent excessive deflections possibly leading to cracking. Temperatures and the deformations will be measured during the test and in-situ video recording of the tests is planned.
5.Conclusions and further study
The paper presents the concept of timber-glass composite for beams and wall elements. The concept has been investigated in several research projects, however, the elements were tested under short-term loading at ambient temperature of approximately 20°C. The practical application of timber-glass elements in practice, however, raises an important issue related to structural fire performance. The behavior of timber in fire and adhesives at elevated temperature is well known. However, up to now little is known about the effects of temperature changes on the performance of structural glazing, both thermal and mechanical.
This is particularly true at the high temperatures which may be expected to be achieved in real conditions and in fire scenarios. This reflects a significant knowledge gap in the performance of structural load bearing glass elements at elevated temperature and fire conditions, and one which must be addressed in order to enable the safe continued growth in the use of structural glass in buildings.
Furthermore, breakage of glass components in buildings where glass is used structurally may have a significant effect on the robustness of the entire structure or the building envelope in case of glass facades. More general, a good understanding of the behavior of glass and glass-based composites exposed to extraordinary loading conditions is essential for avoiding disproportional consequences of glass breakage.
To fully understand the phenomena related to the behavior of timber-glass composites in fire and further assessment for potential practical applications, extensive research must be carried out. This should include basic material research on glass, in particular the variation of mechanical and thermal properties with temperature. Special focus should be put on the strength properties of glass that govern the load-bearing capacity of timber-glass elements and are critical to fulfill the principle and requirements for safety, serviceability, robustness and fire defined by European standards.
Along with the research on material level, experimental testing of timber-glass composite components and developed concepts presented in this paper at elevated temperature and fire conditions should be carried out. This should lead not only to the experimental verification of the ideas in real (fire) conditions but also to a validation of coupled, thermo-mechanical numerical models. The verified models should be then used for further parametric simulations to optimize the concept.
Acknowledgements
This work was supported by the on-going research project “Structural performance of load-bearing timber glass composites - testing and modelling of glass under temperature loading” financed by The ÅForsk Foundation (www.aforsk.com). The project has been carried out at RISE (www.ri.se), Faculty of Engineering LTH at Lund University (www.lth.se) and ARUP (www.arup.com).
References
Aronen, A.: Modelling of Deformations and Stresses in Glass Tempering, PhD thesis, Tempere University of Technology (2012)
Badger, A. E., Silverman, W. B.: Modulus of elasticity of glass in relation to temperature, Journal of the American Ceramic Society 18 (9), 276–280 (1935)
Bedon, C.: Structural Glass Systems under Fire: Overview of Design Issues, Experimental Research, and Developments, Advances in Civil Engineering 2017, Article ID 2120570 (2017)
Bedon, C., Zhang, X., Santos, F., Honfi, F. Kozłowski, M. Arrigoni, M. Figuli, L., Lange, D.: Performance of structural glass facades under extreme loads – Design methods, existing research, current issues and trends, Construction and Building Materials 163, 921–937 (2018)
Ber, B., Sustersic, I., Premrov, M., Strukelj, A., Dujic, B.: Testing of timber–glass composite walls, Structures and Buildings 168, 500-513 (2015)
Ber, B., Premrov, M., Strukelj, A., Kuhta, M.: Experimental investigations of timber–glass composite wall panels, Construction and Building Materials 66, 235-246 (2014)
Blyberg, L., Serrano, E.: Timber/Glass Adhesively Bonded I-beams, Glass Performance Days, Conference Proceedings, Tampere (2011)
Blyberg, L., Lang, M., Lundstedt, K., Schander, M., Serrano, E., Silfverhielm, M., Stalhandske, C.: Glass, timber and adhesive joints - innovative load bearing building components, in: Constr. Build. Mater. 55, 470–478 (2014)
Buchanan, A.H.: Structural Design for Fire Safety, John Wiley & Sons, Chichester (2001)
Le Bourhis, E., Rouxel, T.: Indentation response of glass with temperature, Journal of Non-Crystalline Solids, vol. 316, no. 1, 153–159 (2003)
Carré, H., Daudeville, L.: Load-Bearing Capacity of Tempered Structural Glass, Journal of Engineering Mechanics 125 (8), 914-921 (1999)
Cruz, P., Pequeno, J.: Timber-Glass Composite Beams: Mechanical Behaviour & Architectural Solutions, Challenging Glass Conference 1, Conference Proceedings, Delft University of Technology, Delft (2008)
Daudeville, L., Bernard, F., and Gy, R.: Residual stresses near holes in tempered glass plates, Materials Science Forum, 43-48 (2002)
Debuyser, M., Sjöström, J, Lange, D., Honfi, D., Sonck, D., Belis, J.: Behaviour of monolithic and laminated glass exposed to radiant heating, Construction and Building Materials, Vol. 130, 212–229 (2017)
EN 13501-2. 2016. Fire classification of construction products and building elements – Part 2: Classification using data from fire resistance tests, excluding ventilation services. DIN Deutsches Institut für Normung e.V.
Dorn, M., Kozłowski, M., Serrano, E, Enquist, B.: Development of large-scale load-bearing timber-glass structural elements, WCTE 2014 - World Conference on Timber Engineering, Proceedings (2014)
Fadai, A., Winter, W.: Application of timber‐glass composite (TGC) structures for building construction, Proceedings Challenging Glass 4 & COST Action TU0905 Final Conference. CRC Press (2014)
Fluegel, A., Earl, D.A., Varshneya, A.K., Seward, T.P.: Density and thermal expansion calculation of silicate glass melts from 1000c to 1400c, Physics and Chemistry of Glasses - European Journal of Glass Science and Technology Part B 49 (5), 245–257 (2008)
Hamm, J.: Tragverhalten von Holz und Holzwerkstoffen im statischen Verbund mit Glas, PhD thesis, École Polytechnique Fédérale de Lausanne, 1999
Hamm, J.: Development of Timber-Glass Prefabricated Structural Elements, Innovative Wooden Structures and Bridges IABSE, Conference Report 85, 41-46 (2001)
Jiang, Y., Schaffrath, J., Knorz, M., Winter, S.: Bonding of Various Wood Species – Studies about Their Applicability in Glued Laminated Timber, Proceedings RILEM Conference Materials and Joints in Timber Structures—Recent Advancement of Technology, Stuttgart, Germany, 365-374 (2014)
Karlsson, V., M. Wärnelöv, M. Dorn, and B. Östman: Brandpåverkan på lastbärande trä-glasväggar. Bygg & teknik 109, 44–47 (2017)
Kozłowski, M.: Hybrid glass beams. Review of research projects and applications, Architecture, Civil Engineering, Environment 3, 53–62 (2012)
Kozłowski, M., Serrano, E, Enquist, B.: Experimental investigation on timber-glass composite I-beams, Challenging Glass 4 and COST Action TU0905 Final Conference - Proceedings of the Challenging Glass 4 and Cost Action TU0905 Final Conference, 261-268 (2014)
Kozłowski, M., Dorn, M., Serrano, E.: Experimental testing of load-bearing timber–glass composite shear walls and beams, Wood Material Science and Engineering 10(3), 276–286 (2015)
Kozłowski, M., Kadela, M., Hulimka, J.: Numerical Investigation of Structural Behaviour of Timber-Glass Composite Beams, Procedia Engineering 161, 990-1000 (2016)
Kreher K., Tragverhalten und Bemessung von Holz-Glas-Verbundträgern unter Berücksichtigung der Eigenspannungen im Glas, PhD thesis, École Polytechnique Fédérale de Lausanne, Lausanne (2004)
Li, D., Li, W., Wang, R., Shen, X.: Temperature dependence of the three-point bending fracture behavior of sodalimesilica glass with surface scratch, Journal of NonCrystalline Solids 409 (Supplement C), 126 – 130 (2015)
Louter, C., Nussbaumer, A.: Fire Testing of Structural Glass Beams; Initial Experimental Results. Proceedings of the GlassCon Global Conference - Boston - (2016)
Martens, K., Caspeele, R., Belis J.: Development of composite glass beams – A review, Engineering Structures 101, 1–15 (2015)
Narayanaswamy, O.S.: Stress and structural relaxation in tempering glass, Journal of the American Ceramic Society, 146-152 (1978)
Natterer et al.: New joining techniques for modern architecture, in: Rosenheimer Fenstertage (2002)
Nielsen, J.H..: Tempered Glass - bolted connections and related problems, PhD thesis, Technical University of Denmark (2009)
Premrov, M., Zlatinek, M., Strukelj, A.: Experimental analysis of load-bearing timber-glass I-beam, Constr. Unique Build. Struct. 4 (19), 11-20 (2014)
Rodacki, K.: Composite timber-glass i-beams - case study, Technical Issues 3, 106-112 (2016)de Sa, J. C.: Numerical modelling of glass forming processes, Engineering Computations 3 (4), 266–275 (1986)
Rouxel, T.: Elastic properties and short-to medium-range order in glasses, Journal of the American Ceramic Society, vol. 90, no. 10, 3019–3039 (2007)
Rouxel, T., Sanglebuf, J.-C.: The brittle to ductile transition in a sodalimesilica glass, Journal of Non-Crystalline Solids 271 (3), 224 – 235 (2000)
Scholze, H.: Glass. Nature, Structure, and Properties, Springer-Verlag (1991)
Shen, J., Green, D. J., Tressler, R. E., Shelleman, D. L.: Stress relaxation of a soda lime silicate glass below the glass transition temperature, Journal of Non-Crystalline Solids 324 (3), 277 – 288 (2003)
Strukelj, A., Ber, B., Premrov, M.: Racking resistance of timber-glass wall elements using different types of adhesives, Construction and Building Materials 93, 130-143 (2015)
Vallee, T., Cordula, G., Milchert, L., Fecht, S.: Design and dimensioning of a complex timber-glass hybrid structure: the IFAM pedestrian bridge, Glass Structures & Engineering 1, 3–18 (2016)
Vandebroek, M.: Thermal fracture of glass, Ph.D. thesis, Ghent University (2014)
Wang, Y., Wang, Q., Shao, G., Chen, H., Sun, J., He, L., Liew, K.: Experimental study on critical breaking stress of float glass under elevated temperature, Materials & Design 60, 41–49 (2014)
Wang, Y., Wang, Q., Shao, G., Chen, H., Sun, J., He, L., Liew, K.: Experimental study on critical breaking stress of float glass under elevated temperature, Materials & Design 60, 41 – 49 (2014)
Zarzycki, J.: Glasses and the vitreous state, Cambridge University Press (1982)
Xie, Q., Zhang, H., Si, D.: Experimental study on critical breakage stress of float glass with different thicknesses under conditions with temperatures of 25 and 200c, Fire and materials 35 275–283 (2011)