First presented at GPD 2017
Modern architecture is focusing on new solutions to energy-efficient buildings. Nowadays, heat exchange systems by use of smart windows are under development to actively control the climate conditions in the buildings. Furthermore, it is possible to harvest solar energy by building integrated photovoltaics. Such technologies require high demands on the glass structures which can be achieved by new material combinations.
New approaches from recent developments of Folienwerk Wolfen GmbH and it´s scientific partners offer the possibility to match these requirements. The presentation will focus on the effect of the crosslinking of polymeric interlayer or laminating films on the performance of laminated glass structures. Mechanical and safety properties under hard climate conditions, compatibility of the interlayer films to chemicals as well as life-time stability of the glass structures and the final products will be discussed. Furthermore, some new glass structures for the achievement of the requirements will be introduced.
Introduction
Today, urban life is requiring huge resources. Buildings, part of our culture, are still demanding a lot of energy. In modern architecture, the skins of the buildings are used mostly for representative purposes. The more urban life is moving into cities, more and more buildings with large façades and roofs are being built. Why not use these large areas of the skin for more than aesthetic purposes? New architectural concepts are including energy relevant topics into the development of new buildings.
Such new projects and concepts for energyefficient buildings have reached popular science, too. For example, articles about future trends in urban life discuss energy harvesting façades or windows which store heat and energy. [1]
There is a huge market for energy efficient buildings and façades along the so called “sunbelt” of our planet. Prosperous megacities, growing and ambitious economies, as well as progressive nations are located in these areas. Due to the high solar radiation, the geographic regions in the “sunbelt” are offering tremendous possibilities for energy harvesting technologies like photovoltaics or intelligent façades.
However, besides the high solar radiation, the other climate conditions are challenging: high differences in temperature between day and night, condensing fog in the morning hours, arid climate conditions as well as strong wind or sand storms have to be considered during development of materials for energyefficient buildings and façades. The use of laminated structures is a powerful tool for the development of tailor-made materials for such environmental challenges.
Laminated glasses consist of glass panes which are bonded together by an adhesive material. Such adhesive material can be a glue or a polymeric interlayer film. The requirements of the film are manifold: good adhesion to the glass, long lifetime without loss of functionality, outstanding resistance to outdoor effects, or high transparency have to be achieved in combination with easy processing and justifiable costs. These days, the manufacture of laminated glasses by polymeric interlayers is a state-of-the-art process all over the world.
Polymeric interlayer films
For the manufacture of laminated glasses, different polymeric films can be used: The standard interlayer film in the glass industry is consisting of polyvinyl butyral (PVB). However, other polymeric interlayer films have entered the market successfully, especially for niche applications: interlayer films consisting of ionomers (i.e. Sentry glass) are used for safety applications with high static requirements, while polyolefin, silicone or ethylene-vinyl acetate (EVA) based interlayer films offer significant advantages, especially for applications under humid climate. The market of photovoltaic applications has been dominated by EVA based interlayer films for a long time.
Depending on the applications, different EVA interlayer films can be chosen: For the fabrication of photovoltaic modules, EVA films were developed for fast processing speed and special performance in the vacuum lamination process. Contrary to this, EVA interlayer films for the manufacture of laminated safety glasses for façade or architectural applications have to fulfill the requirements of the glass industry, including verifiable certification of the building industry.
EVA interlayer film:
Compared to the other polymeric films, EVA interlayer film behaves differently. Under the effect of temperature and time, the polymer chains of the EVA will create a three-dimensional network structure due to a crosslinking step. This crosslinking step is initiated by peroxides. The peroxide is part of the formulation of EVA interlayer films like evguard®, the interlayer film developed and produced by Folienwerk Wolfen GmbH.
The process of the crosslinking can be described as followed: The peroxide will decompose, creating radicals. In the next step, these radicals will activate carbon-hydrogen bonds at the polymer chains by abstraction of hydrogen atoms. By recombination of such activated polymer chains or fragments thereof, a three-dimensional polymeric network will be achieved. The formation of the crosslinked polymeric network, as well as the properties of the resulting material, can be controlled by varying the formulation of the EVA film, and the process parameters.
The crosslinking speed of an EVA interlayer film during the lamination process is shown in figure 1. Due to the crosslinking, the viscosity, as well as the viscous and storage modulus of the polymer melt will change. The conversion of the crosslinking at different temperatures was measured by means of a rheometer (Malvern Kinexus Ultra). Measurement was carried out by plate-plate equipment, under isothermal conditions. The change of the viscous and storage modulus was used for determination of the crosslinking conversion.
The gel-rate, representing the amount of the crosslinked EVA polymer chains, was analysed by extraction in xylene. The conversion of the crosslinking is shown for three different temperatures. For achieving safety properties of laminated glasses, a crosslinking degree of at least 80% is required. As can be seen (figure 1, right diagram), an increase of the temperature from 130°C to 150°C reduces the conversion time to achieve a crosslinking level of at least 80% from approx. 40 min. to 5 min.
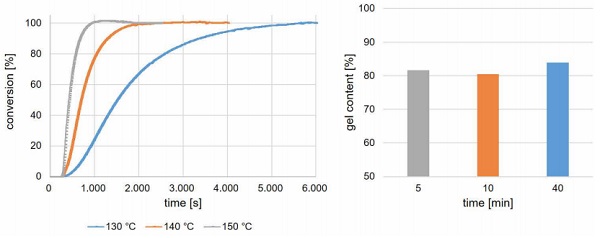
The crosslinking step changes the behaviour of the EVA interlayer film. This is important for the properties of the film, and the laminated glass, too. The effect of the crosslinking on the mechanical properties of the EVA interlayer film can be shown easily by the tensile test. In figure 2, the mechanical properties of uncured (left) and crosslinked (right) evguard® EVA interlayer film are shown. Neat, uncured EVA interlayer film is characterized by a stress of up to 12 N/mm² and an elongation of more than 700%.
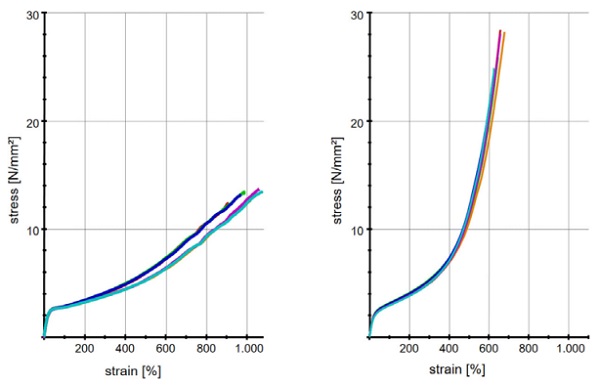
Slightly different curves can be seen depending on the orientation of the film. The stress-strain curves of machine oriented EVA film typically show less elongation than the curves measured for transversal specimen. Such behaviour is well known for films made of thermoplastic materials. In contrast to uncured EVA, the crosslinking yields in a significantly stronger, stiffer film. This is shown in figure 2 (right). Stress values more than 20 N/mm² and elongation values of about 600 % are detected for the crosslinked EVA interlayer film. No effect of the film orientation can be seen now,
Due to the change of the EVA film properties by crosslinking, the properties of the laminated glasses can be modified considerably by this kind of interlayer. As an example of the effect of the crosslinking rate, results of the pendulum impact test are shown in figure 3. The pendulum test was carried out according to DIN EN 12600, drop height 1200 mm. Laminated glasses of the structure 44.2 were tested.
The EVA interlayer film was crosslinked to different extent. When the EVA interlayer film was crosslinked to low level only, the pendulum test failed. A long crack can be seen as a typical result. Compared to this, a laminated glass with high crosslinked EVA interlayer film passed the pendulum test. As can be seen in figure 3 (right), no crack of the glass occurs. The shown pictures in figure 3 are exemplarily for these observations.
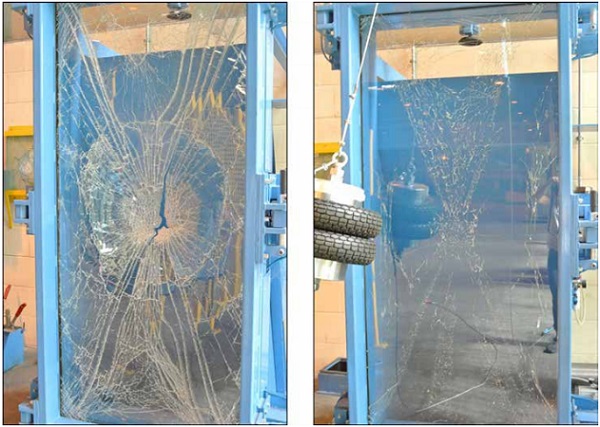
Use of EVA interlayer films for composite capillary glasses
Within the EU Horizon 2020 funded project Lawin (large area fluidic window), ultrathin composite capillary glasses are under development. [2] The capillaries of the glass will be created by a rolling process during float glass processing. The structured float glass will be connected with a thin, strengthened cover glass, to achieve a composite structure.
The result is a flat-panel laminate with thickness adapted to a single glass sheet in conventional windows. A fluid is flowing through the capillaries, allowing absorption or release of heat. By combination with a heat exchanger, these composite capillary glasses will be used in isolating glass units or façades for absorption, storage or transfer of heat. Key market of the product is the use for climate controlled windows and façades. [3] The structure of such composite capillary glass for use as large area fluidic window is shown in figure 4.
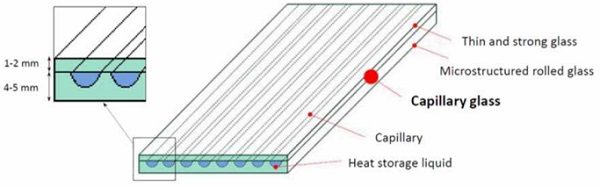
During the project, different approaches for the connection of the structured float glass and the thin, strengthened cover glass were investigated. Both gluing and lamination technologies were tested for the manufacture of the required composite capillary glass. Visual appearance, durability and thermal performance under various climate conditions are the key requirements for the product, as listed in Tab. 1.
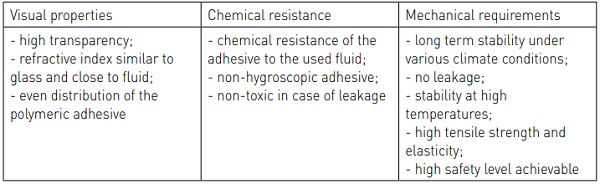
Laminated glass samples of different size and structure were subjected to a defined test program, including chemical, mechanical and optical measurements. The test specimens were exposed to cyclic and climatic conditions to access the long-term behaviour of the bonded areas. [4]
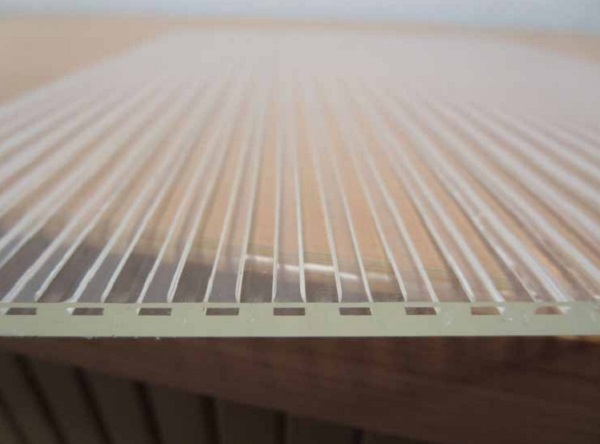
The use of glues as well as interlayer films as adhesive for the manufacture of the composite capillary glass was investigated. From the first results of the tests, the EVA interlayer film was found to be a material with well-balanced performance profile. The EVA interlayer film offers the following advantages:
- Good adhesion: Composite capillary glasses were laminated using strips of the EVA interlayer. A side view parallel to the capillaries is shown in figure 5. As can be seen, the EVA interlayer film strips bond the capillary glass and the ultra-thin cover glass only at the connecting zones. This allows a maximum cross section of the capillaries which is needed for constant flow of the fluid.
- Resistance to the fluid: In case of glues or thermoplastic interlayer films like PVB, the contact of the fluid with the adhesive will possibly lead to brittleness, negatively affecting the safety properties. In case of glues, the formation of cracks was found, possibly enforcing the brittleness. For PVB interlayer films the contact to the fluid may cause a leaching of softeners from the polymer. Compared to this, the crosslinked EVA remains stable for a longer time. It is also free of softeners, showing significantly improved resistance in contact to the fluid of the capillary glass.
- Exposure to high temperatures: Used at the façade of a building, the composite capillary safety glass will be exposed to high temperatures. Due to the crosslinked nature of the EVA film, such material has sufficient performance also at temperatures above 50°C.
- Edges: At the edges of the capillary glass, the bonding material is in contact both to the fluid in the inside the capillaries and the external sealant. Good compatibility to the different materials is required at this sensitive area. The EVA based interlayer film also reduces the risk of delamination at this critical part of the composite capillary glass.
- Safety properties: The selected EVA interlayer film is certified by various German, European and American certifying bodies for use as laminated safety glass.
Environmental conditions
All components of energy efficient buildings and façades or building integrated photovoltaic modules for the sunbelt areas have to resist the challenging climate conditions. Compared to central European climate, the temperatures, differences in day-night temperatures, and solar radiation are significantly higher. Only selective materials can resist the harsh climate conditions, especially the high UV radiation, in combination with wind and sand load.
In another cooperation project, test scenarios for the investigation of glass laminates or solar modules under challenging climate conditions in combination with geographical aspects were developed. [5]
Based on the international standard IEC 61215:2016, test programs were extended or newly generated. [6] Temperature changes over the season can be used to prepare thermal cycling tests, while day-night temperature changes are needed to prepare test programs especially for thermally sensitive materials like wires or inlays. The differences in solar radiation between the various climate zones have to be considered in relation to humidity and other effects. To estimate the mechanical stress of glass laminates or façades for building integrated photovoltaics, the wind load has to be considered. Following these considerations, three different models were defined as basis for the test programs: tropical climate (temperature always above +18°C), desert climate (extremely dry conditions), as well as moderate climate as reference (central European climate). In moderate climate zone, the temperature of the cold season is in the range of -3°C to +18°C, deposits are at a level higher than in dry environment. For each climate model zone, typical geographical areas can be identified.
Different polymeric materials, usable as interlayers for laminated glasses or photovoltaic modules, are currently under investigation using the developed test methods. First results indicate, that special polyolefin materials are offering very good ageing properties. [7]
However, EVA based interlayer films are also showing durable performance under the test conditions. EVA interlayers are also an advantage, if effects of wind have to be considered. Due to the crosslinked polymeric network, EVA films can withstand wind loads, especially at high temperatures better than most of the thermoplastic materials.
This performance strongly depends on the formulation of the EVA interlayer film. The selection of the EVA needs to be focused on the content of vinyl acetate, and the melt flow index. [8] These factors influence the melting behaviour of the film during extrusion and lamination, as well as the optical properties of the final laminated glass or photovoltaic module. The selection of the optimum additive formulation is the second important key to a successful interlayer film. Some basics are well-known, but mainly focusing on solar applications. [9-11] For application in energy efficient buildings, further developmental work is required. This is the focus of current work of the Folienwerk Wolfen GmbH and its research partners.
Conclusions
Modern architecture requires new concepts for energy-efficient buildings. Due to the large surfaces, façades, roofs and windows are offering the possibility to generate and store heat or energy. To bring in such functionalities, laminated structures can be used. Glass laminates are an advantage both of regarding aesthetics and functionality.
As an example for façade and window application, results of a research project for the development of composite capillary glasses were discussed. The key targets for such laminated capillary glass include visual appearance, chemical resistance, as well as mechanical and safety requirements. For fulfilling the needs, an adhesive with well-balanced properties is required for the laminated glass. Different adhesion systems were examined. From the results, the evguard® EVA interlayer film has shown good performance for the requirements.
Potential markets for energy-efficient buildings are along the sun-belt of our planet. However, the solar energy gain in these areas is combined with harsh environmental conditions. The temperatures, differences in day-night temperatures, load of wind and sand, as well as UV radiation are significantly higher, demanding materials which can withstand the challenges of the climate conditions. The development of materials for such regions requires ambitious test methods. Some initial results of such test methods for laminated glasses for architectural and photovoltaic applications are shown.
References
[1] Nat. Geographic magazine, German Ed., Nov. 2015, p. 100
[2] www.lawin.uni-jena.de
[3] B.P.V. Heiz, Z. Pan, G. Lautenschläger, C. Sirtl, M. Kraus, L. Wondraczek, Adv. Sci. 2017, 4, 1600362
[4] C. Sirtl, M. Kraus, C. Hadlich, A. Osburg, L. Wondraczek, in: B. Weller, S. Tasche (Eds.): Glasbau 2017, Ernst & Son, 2017, p. 305
[5] E. Heyer, Witterung und Klima – Eine allgemeine Klimatologie, B.G. Teubner Verlagsgesellschaft, 1988, p. 169 ff.
[6] S. Dietrich, M. Pander, M. Sander, S.H. Schulze, M. Ebert, in: N.G. Dhere, Bellingham, WA: SPIE, 2010 (Proceedings of SPIE 7773) Paper 77730F
[7] S.H. Schulze, M. Wendt, C. Ehrich, S. Henning, R. Meitzner, Proc. EU PVSEC 2014, p. 3138 – 3141
[8] D.C. Anderson, „EVA overview: Global demand, regional market capacities and trends”, 2nd Symposium Polymer Apps in Photovoltaic, Leipzig, 12. /13.03.2012
[9] F.J. Pern, Angew. Makromol. Chemie, 252 (1997), 195
[10] S.M. Tamboli, S.T. Mhaske, D.D. Kale, Indian Journal of Chemical Technology 11 (2004) S. 853
[11] S.H. Schulze, A. Apel, R. Meitzner, M. Schak, C. Ehrich, J. Schneider, Proc. EU PVSEC, 2013, p. 503 - 507
Acknowledgements
The authors kindly acknowledge financial support from the European Commission through its Horizon-2020 framework program (Grant Agreement GA 637108). The financial support of the Federal Government of SaxonyAnhalt (project number 1604/00008) is also gratefully acknowledged. Many thanks to all members of the projects for fruitful discussion and collaboration.