Article Information
- Digital Object Identifier (DOI): 10.47982/cgc.9.614
- Published by Challenging Glass, on behalf of the author(s), at Stichting OpenAccess.
- Published as part of the peer-reviewed Challenging Glass Conference Proceedings, Volume 9, June 2024, 10.47982/cgc.9
- Editors: Christian Louter, Freek Bos & Jan Belis
- This work is licensed under a Creative Commons Attribution 4.0 International (CC BY 4.0) license.
- Copyright © 2024 with the author(s)
Authors:
- Chiara Bedon - University of Trieste
- Alessandro Massi Pavan - University of Trieste
- Nicola Cella - University of Trieste
- Nicola Blasuttigh - University of Trieste
1. Introduction
Photovoltaic (PV) modules are designed to ensure more than 25 years of functionality under variable and even unfavourable operational conditions, including the effect of temperature / humidity changes, wind, rain, hail and snow, etc. While their electrical functionality is of primary importance, the mechanical performance also represents a critical aspect, which is implicitly correlated to the durability and efficiency of PV modules. According to literature, in this regard, there are several monitoring and diagnostic strategies to monitor possible faults and defects, such as shading, dust or sand accumulation on the PV surfaces, short circuits, bypass diodes failures, disconnections of PV modules, shunting of PV modules, and others (Mellit et al. 2018, Li et al 2019, Mellit et al. 2023). Hot spot faults represent one of typical localized damage configurations that should be promptly detected (Tsanakas and Botsaris 2013, Zhang et al. 2017, Jiang et al. 2020, Li et al 2022).
Structurally speaking, a special care should be required for the prompt detection of many different progressive degradation / failure mechanisms that are associated to possible power-losses and major effects on the functionality and efficiency of PV modules, such as possible micro and macro cracks in cells (Sander et al. 2013), breakage of interconnects (Dietrich et al. 2013), detachment of the frame members at the edges, and especially delamination of sandwich components in the PV system (Dadaniya and Varma Datla 2020, Dobra et al. 2022, Sangpongsanont et al. 2023, Meena et al. 2024, Bedon et al. 2024).
2. Reference PV module and methodology
2.1. Geometry
As in Fig. 1, the majority of commercial PV modules are usually characterized by a relatively thin cross-section and a typically high slenderness and bending flexibility to out-of-plane mechanical loads, due to their size-to-thickness ratio and also to the typical arrangement of restraints and fixings. As a sandwich cross-section, the mechanical capacity is usually assigned to thin glass covers with a typical thickness in the range of h1≈ 3-5 mm and (for single-glass compositions) back Tedlar® / plastic layers with h2≈1-2 mm, which are mechanically bonded by Ethylene-Vinyl Acetate (EVA) interlayers with hint≈ 1 mm in total.
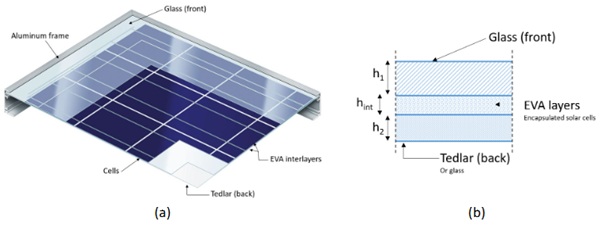
2.2. Strategy
Following the existing literature evidences, a Finite Element (FE) numerical study is thus presented in this paper to assess the convenience of non-destructive dynamic techniques for the mechanical characterization and for the early damage / deterioration detection of EVA bonding interlayers for PV modules (Fig. 2). The methodology takes advantage of classical structural health monitoring (SHM) procedures for civil structures and machineries (Pander et al. 2011, Limongelli et al. 2021, Bedon et al. 2023, Dimarogonas 1996), where the on-site experimental analysis in the frequency domain is usually carried out to detect and characterize the vibration modes of the system object of study, and thus to assess the effect of single components and possible influencing parameters. The approach follows earlier applications to laminated glass systems and composite elements, where in-field and/or historic structures have been efficiently characterized under various loading and boundary conditions, including walkways in unfavourable environment and operational configurations (Bedon 2019a), facades (Bedon et al. 2022), fractured pedestrian systems (Bedon et al. 2021) and beams with delamination (Bedon 2019b).
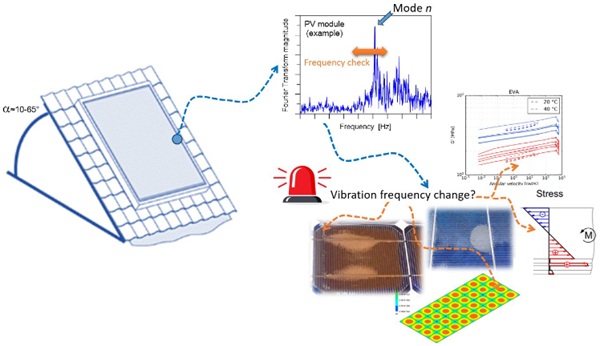
The present study, differing from earlier investigations, consists in the analysis of composite systems characterized by higher flexibility (due to typical geometrical and mechanical features), severe exposure to environment, and thus higher sensitivity to possible material degradation. A carefulcalibration of a FE numerical model representative of the reference PV module is performed, in which the basic constituent members are efficiently described in geometrical and mechanical terms, and the EVA material is described as equivalent linear elastic. Parametric numerical analyses are hence carried out in Section 5 to address the sensitivity of dynamic features to basic material modifications for the bonding encapsulant, which could take place due to progressive ageing in the long-term period, exposure to unfavourable ambient conditions, repeated thermal gradients, and even possible localized / non-uniform delamination or damage due to extreme mechanical loads.
3. Frequency analysis
The current approach assumes that the frequency analysis of PV modules – experimentally derived based on the Fourier Transform function analysis of measured acceleration records, as in Fig. 2 – can offer important feedback and can be used to calibrate and validate a refined FE model representative (in average) of the tested PV samples, in which the geometry and the mechanical composition of a selection of commercial full-scale modules is properly taken into account. The numerical analysis of the reference FE model is then further extended to a parametric and sensitivity study, to assess the effect of further influencing parameters of technical interest for long-term and severe ambient conditions.
Under unfavourable environments, the vibration frequency of the PV system in Fig. 3 (a) is in fact affected by many factors, that are namely associated to the sandwich section features, to the contribution and edge restrain of the metal frame (Fig. 3 (c)), to the effect of brackets (Fig. 3 (d)), etc. At the level of sandwich in Fig. 3 (b), the protective glass cover is expected to behave elastically without significant modifications in the elastic modulus of the basic constituent material (Udi et al. 2023), and the same concept applies to the aluminium components of frame members and restraints. Besides, the interposed EVA films are sensitive to temperature and humidity, which could both affect the PV modules in the long-term period (Dietrich et al. 2010, Hána et al. 2019). As far as the bonding interface of EVA films and glass/plastic covers is possibly affected by external agents, and/or the interlayer suffers for stiffness modification due to operational conditions, the PV module acts as a composite panel with weak / flexible shear connection, and this could result in compromised load-bearing mechanisms under design mechanical loads (Naumenko and Eremeyev 2014, Gong et al. 2021). On the other side, it is experimentally proved that high vibration frequencies for EVA films – like for viscoelastic interlayers in general – typically have a stiffening effect, and this can be positively quantified in a possible moderate increase in shear bond efficiency (Knight et al. 2022, Hána et al. 2019). However, it is also experimentally observed that repeated mechanical loads (even at high strain rate) induce a marked reduction in the material stiffness, with deterioration of shear bond rigidity (Schmidt et al. 2017). In such a variable and uncertain scenario, both the metal frame at the edges (Fig. 3 (c)) and the fixing brackets (Fig. 3 (d)) – that can be efficiently characterized by numerical analysis –further contribute to modify the vibration response of the PV system, compared to ideal simplified restraints.
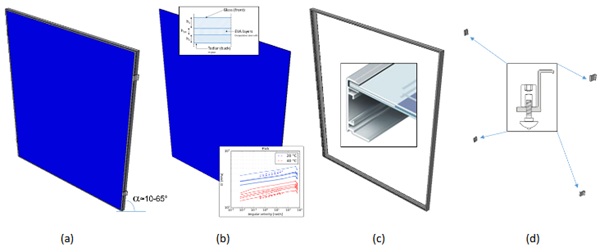
To assess the severity of all these possible effects, the present study assumes that – for the sandwich section – the stiffness of EVA films and its viscoelastic modification are for the major part responsible of the vibration frequency and rigidity of a given PV module in out-of-plane bending deformations. The “effective” composite flexural stiffness of the sandwich is in fact (Li et al. 2020, Gong et al. 2021, CNR-DT 210/2013):
Rationally, it is expected that:
where Dabs and Dfull denote the bending stiffness values of the sandwich section under weak / null shear bonding offered by EVA foils (“abs”, layered limit) or with ideally rigid connection in shear (“full”, monolithic limit) respectively. From an analytical point of view, as also in accordance with Li et al. (2020) and other studies, the basic assumption for the analytical mechanical analysis of a sandwich section like in Fig. 3 (b) is that:
- the front glass cover (h₁ thickness) is described as linear elastic layer (with E₁, ν₁, ρ₁ the material properties in terms of modulus of elasticity, Poisson’ ratio, density);
- the backboard Tedlar layer (h₂ thickness) can be also described as linear elastic (E₂, ν₂, ρ₂);
- the EVA interlayer, with total thickness hint, is described as an equivalent linear elastic material with secant stiffness Eint which is in general very soft compared to E₁ and E₂. For more realistic estimates, however, this value should be calibrated to represent – based on the typical viscoelastic material behaviour – a specific loading and boundary condition of practical interest (i.e., time loading, temperature, ageing (CNR-DT 210/2013));
- the encapsulated solar cells are disregarded in mechanical terms, and assumed to offer null contribution to the composite PV section in bending.
Under such a kind of assumption, it is conservatively expected that the bending stiffness of the sandwich section is mostly governed by the front and back covers only, where (i= 1, 2):
is the stiffness of external layers and the limit values are:
with:
The corresponding deflection under uniform pressure and simple boundary conditions can be thus estimated analytically, see for example Naumenko and Eremeyev (2014).
4. Numerical modelling
The reference FE model was assembled in ABAQUS (Simulia). To optimize the computational cost of simulations, the FE model consisted of a combination of full 3D solid brick elements (for the metal frame and brackets) and 2D shell elements for the PV components schematized in Fig. 1 (i.e., glass cover, EVA, Tedlar layer, solar cells). To account for possible complex vibration modes, the full geometry of PV modules was numerically described. The adopted mesh pattern was chosen to ensure accuracy in frequency estimates, and thus resulted in ≈28,000 elements and ≈42,000 DOFs, see Fig.4.
Materials were described in the form of linear elastic constitutive laws, for the purpose of linear modal analyses and frequency predictions. For glass and aluminium, the nominal mechanical properties in Table 1 were taken into account (EN 572-2, EN 485-2). The Tedlar plastic layer was mechanically characterized based on product datasheets, see Table 1 and Tedlar Technical Bulletin (2020). Finally, for the EVA interlayer, the tentative mechanical characterization was preliminary based on experimental and numerical studies reported in Li et al. (2020) and Knight et al. (2022). To note that in the present analysis, the solar cells were described as an equivalent linear elastic material (Li et al. 2020).
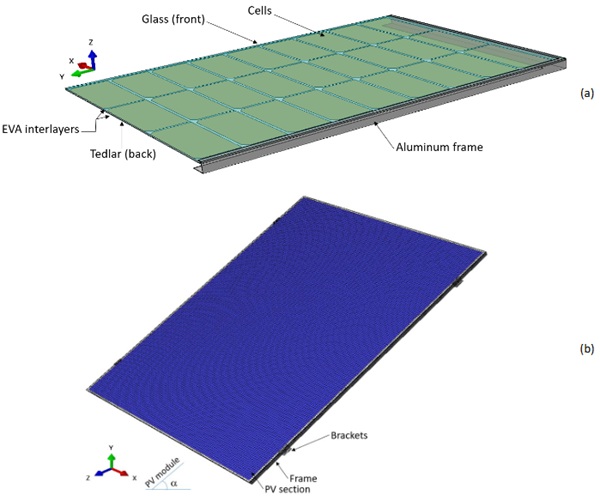
Table 1. Input mechanical properties for the frequency analysis (ABAQUS).
5. Preliminary results
The parametric analysis was carried out to assess the effect of a progressive modification of the interlayer stiffness. For the purpose of present study, the elastic modulus Eint in Table 1 was progressively modified in the range from 0.1 MPa up to 70 GPa, which correspond respectively to the “abs” lower limit and to the ideal “full” configuration in which the interlayer has the same rigidity of the glass front cover.
In terms of vibration modes and shapes of the PV module, no marked modifications were noted. Besides, a major effect of interlayer stiffness was numerically quantified in the modification of vibration frequencies for the examined PV module. In this regard, the typical results can be seen in Figs. 5 (a) to (d) in terms of frequency trend as a function of Eint, for the four lower vibration modes, which are characterized by one-to-three half sinewaves for the PV module. As far as Eint ideally increases, the corresponding vibration frequency progressively increases for all the detected vibration modes.
Most importantly, Fig. 6 further emphasizes the interlayer effect on the vibration frequency, as a function of the “abs” or “reference” (Table 1) shear bonding level offered by the interlayer.
Compared to a weak bond in Fig. 6 (a), it can be seen that the minimum contribution offered by the interlayer can manifest in a major stiffening contribution for the sandwich section. The calculated percentage scatter of frequency increases tends to increase with the increase of mode order, that is the number of sinewaves and the bending deformation of the system.
Besides, especially for health monitoring purposes, the percentage frequency variation can be further interestingly measured as a function of the “initial” configuration of the PV module, that is the system with efficient bonding connection at the time of its installation. For the present study, the numerical results in Fig. 6 (b) are calculated in percentage scatter compared to the Eint properties reported in Table 1. It can be thus noted that even a major increase in the stiffness of interlayer (i.e., as a function, for example, of high dynamic or impulsive loads), there is no marked modification in the corresponding vibration frequency. Only for very rigid (but not realistic) bonds, it can be expected a frequency increase up to 13-15% for the three lower vibration modes of the system. It is worth to note in Fig. 6 (b) that event relatively stiff bonds (i.e., up to ≈1000 MPa in modulus) would result in a minimum increase of stiffness and frequency (less than 3%). This suggests that the sandwich system under high strain rate effects (i.e., for the PV module under impact loading) cannot take advantage of possible stiffening effects in the interlayer.
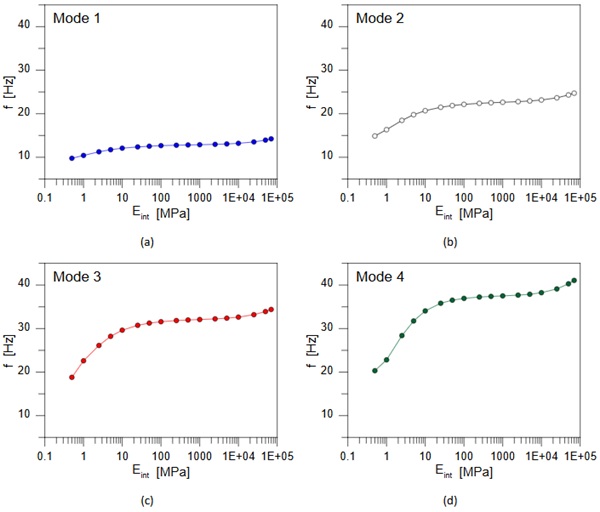
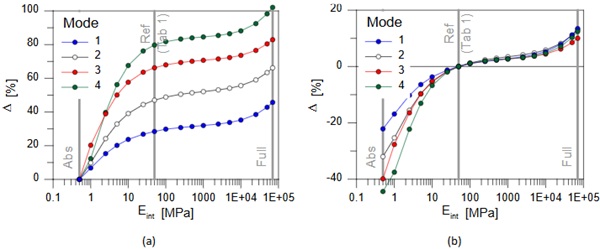
It is indeed of major interes the effect of bond rigidity when degrading phenomena, as well as the progressive ageing of interlayer stiffness or even possible delamination of interfaces, can take place in the long-term period. Fig. 6 (b) highlights in fact a frequency decrease down to -45% when the shear bonding efficiency of the connection vanishes. Also, the higher is the mode order for the examined system, and the higher is the percentage variation of vibration frequency.
In other words, the present analysis confirms that the interlayers have – as in typical glass and composite laminates applications – a key role for the determination of the load-bearing capacity and mechanical performance of typical thin sandwich sections in use for commercial PV modules. In the long-term period, or even in unfavourable environments that could affect the interlayer efficiency, it can be useful to track and detect possible modifications in the mechanical properties of basic components, and thus prevent possible weaknesses or loss or functionalities for PV modules.
6. Conclusions
Photovoltaic (PV) modules, that are designed to ensure about 20-25 years of functionality, are typically exposed to variable environment scenarios and even unfavourable operational conditions, including the effect of temperature changes, wind, rain, hail and snow, etc. Their mechanical efficiency and performance, in this regard, represents a critical aspect to support an optimal durability and electrical efficiency of PV modules. Besides, typical sandwich sections are composed of relatively thin top/bottom covers and an interposed film to encapsulate the solar cells. From a mechanical point of view, the interlayers have a key role in ensuring the shear bond between the constituent components, and thus maximize the load-bearing performance capacity of the system. Among others, the bonding interlayers can suffer for stiffness modification which has direct effects on the composite action and response of the sandwich section.
The present investigation was focused on the frequency assessment to monitor and alert possible major modifications in the encapsulant layers, to prevent major stress peaks and possible severe damage conditions in the sandwich section. The numerical study proved that the vibration frequency can be largely sensitive to possible stiffness modifications in the interlayers, with frequency variations down to -40%, and thus should be usefully checked to reveal the progressive mechanical deterioration or even possible defects in the sandwich components. To this aim, the present numerical analysis will be further exploited by including in the investigation a number of different PV module configurations, as well as experimental observations from in-field measurements on aged PV samples.
References
Bedon, C.: Diagnostic analysis and dynamic identification of a glass suspension footbridge via on-site vibration experiments and FE numerical modelling. Composite Structures, 216: 366-378 (2019a)
Bedon, C.: Issues on the vibration analysis of in-service laminated glass structures: analytical, experimental and numerical investigations on delaminated beams. Applied Sciences, 9(18): 3928 (2019b)
Bedon, C., Noè, S.: Post-Breakage Vibration Frequency Analysis of In-Service Pedestrian Laminated Glass Modular Units. Vibration, 4: 836-852 (2021)
Bedon, C., Noè, S., Fasan, M., Amadio, C.: Role of In-Field Experimental Diagnostic Analysis for the Derivation of Residual Capacity Indexes in Existing Pedestrian Glass Systems. Buildings, 13: 754 (2023)
Bedon, C., Santi, M.V., Fasan, M.: Considerations on efficient procedural steps for seismic capacity assessment and diagnostics of historic structural glass systems. Soil Dynamics and Earthquake Engineering, 163: 107562 (2022)
Bedon, C., Santos, F., Fasan, M.: Mechanical Analysis of the Quasi-Static and Dynamic Composite Action in PV Modules with Viscoelastic Encapsulant. Materials 2024, 17(6), 1317 (2024)
CNR-DT 210/2013; Istruzioni Per la Progettazione, L’esecuzione ed il Controllo di Costruzioni con Elementi Strutturali di Vetro. National Research Council of Italy (CNR): Rome, Italy, 2013. (In Italian)
Dadaniya, A., Varma Datla, N.: Degradation prediction of encapsulant-glass adhesion in the photovoltaic module under outdoor and accelerated exposures. Solar Energy, 208: 419-429 (2020)
Dietrich, S., Pander, M., Sander, M., Ebert, M.: Mechanical investigations on metallization layouts of solar cells with respect to module reliability. Energy Procedia, 38: 488-497 (2013)
Dietrich, S., Pander, M., Sander, M., Schulze, S.-H., Ebert, M.: Mechanical and Thermo-Mechanical Assessment of Encapsulated Solar Cells by Finite-Element-Simulation. Proceedings of SPIE – The International Society for Optical Engineering – Reliability of Photovoltaic Cells, Modules, Components, and Systems III, San Diego, California, USA; volume 7773, id: 77730F, (2010). https://doi.org/10.1117/12.860661
Dimarogonas, A.D.: Vibration of cracked structures: A state of the art review. Engineering Fracture Mechanics, 55: 831-857 (1996)
Dobra, T., Vollprecht, D., Pomberger, R.: Thermal delamination of end-of -life crystalline silicon photovoltaic modules. Waste Management & Research, 40(1): 96-103, (2022). https://doi.org/10.1177/0734242X211038184
EN 485-2, Aluminium and Aluminium Alloys – Sheet, Strip and Plate – Part 2: Mechanical Properties. European Committee for Standardization (CEN), Brussels, Belgium
EN 572–2:2004. Glass in buildings – Basic soda lime silicate glass products. European Committee for Standardization (CEN), Brussels, Belgium
Gong, J., Xie, L., Li, Y., Ni, Z., Wei, Q., Wu, Y., Cheng, H.: Analysis of the Impact Resistance of Photovoltaic Panels Based on the Effective Thickness Method. Journal of Renewable Materials, 10(1): 33-51 (2021)
Hána, T., Janda, T., Schmidt, J., Zemanová, A., Šejnoha, M., Eliášová, Vokáč, M.: Experimental and Numerical Study of Viscoelastic Properties of Polymeric Interlayers Used for Laminated Glass: Determination of Material Parameters. Materials, 12: 2241, (2019). https://doi.org/10.3390/ma12142241
Jiang, L., Su, J., Shi, Y., Lai, J., Wang, H.: Hot spots detection of operating PV arrays through IR thermal image. Acta Energiae Sol. Sin., 8: 180-184 (2020)
Knight, J.T., El-Sisi, A.A., Elbelbisi, A.H., Newberry, M., Salim, H.A.: Mechanical Behavior of Laminated Glass Polymer Interlayer Subjected to Environmental Effects. Polymers, 14: 5113, (2022). https://doi.org/10.3390/polym14235113
Li, G., Wang, F., Feng, F., Wei, B.: Hot Spot Detection of Photovoltaic Module Based on Distributed Fiber Bragg Grating Sensor. Sensors: 22: 4951, (2022). https://doi.org/10.3390/s22134951
Li, Y., Ding, K., Zhang, J., Chen, F., Chen, X., Wu, J.: A fault diagnosis method for photovoltaic arrays based on fault parameters identification. Renewable Energy, 143: 52-63 (2019)
Li, Y., Xie, L., Zhang, T., Wu, Y., Sun, Y., Ni, Z., Zhang, J., He, B., Zhao, P.: Mechanical analysis of photovoltaic panels with various boundary condition. Renewable Energy, 145: 242-260 (2020)
Limongelli, M.P., Manoach, E., Quqa, S., Giordano, P.F., Bhowmik, B., Pakrashi, V., Cigada, A.: Vibration Response-Based Damage Detection. In Structural Health Monitoring Damage Detection Systems for Aerospace; Springer Aerospace Technology: Cham, Switzerland (2021)
Meena, R., Pareek, A., Gupta, R.: A comprehensive review on interfacial delamination in photovoltaic modules. Renewable and Sustainable Energy Reviews, 189, Part A, 113944, (2024). https://doi.org/10.1016/j.rser.2023.113944
Mellit, A., Benghanem, M., Kalogirou, S.A., Massi Pavan, A.: An embedded system for remote monitoring and fault diagnosis of photovoltaic arrays using machine learning and the internet of things. Renewable Energy, 208: 399-408 (2023)
Mellit, A., Tina, G.M, Kalogirou, S.A.: Fault detection and diagnosis methods for photovoltaic systems: A review. Renewable and Sustainable Energy Reviews, 91: 1-17 (2018)
Naumenko, K., Eremeyev, V.A.: A layer-wise theory for laminated glass and photovoltaic panels. Composite Structures, 112: 283-291 (2014)
Pander, M., Dietrich, S., Schulze, S.-H., Eitner, U., Ebert M.: Thermo-mechanical assessment of solar cell displacement with respect to the viscoelastic behaviour of the encapsulant. Proceedings of the 12th International Conference on Thermal, Mechanical & Multi-Physics Simulation and Experiments in Microelectronics and Microsystems, Linz, Austria, (2011). doi: 10.1109/ESIME.2011.5765831
Sander, M., Dietrich, S., Pander, M., Ebert, M., Bagdahn, J.: Systematic investigation of cracks in encapsulated solar cells after mechanical loading. Solar Energy Materials & Solar Cells, 111: 82-89 (2013)
Sangpongsanont, Y., Chuangchote, S., Chenvidhya, D., Kirtikara, K.: Annual expansion in delamination of front encapsulant in tropical climate Field-Operated PV modules. Solar Energy, 262: 111850 (2023)
Schmidt, J., Janda, T., Sejnoha, M., Valentin, J.: Experimental determination of visco-elastic properties of laminated glass interlayer. Proceedings of 23rd International Conference Engineering Mechanics 2017, Svratka, Czech Republic (2017)
Simulia, Dassault Systémes. ABAQUS Computer Software; Providence, RI, USA
Tedlar Technical Bulletin (2020). Mechanical properties of Tedlar Films, 6 pages
Tsanakas, J.A., Botsaris, P.: On the detection of hot spots in operating photovoltaic arrays through thermal image analysis and a simulation model. Mater. Eval., 4: 457-465 (2013)
Udi, U.J., Yussof, M.M., Ayagi, K.M., Bedon, C., Kamarudin, M.K.: Environmental degradation of structural glass systems: A review of experimental research and main influencing parameters. Ain Shams Engineering Journal, 14(5): 101970 (2023)
Zhang, Z., Shan, L., Wang, L., Wu, J., Quan, P., Jiang, M.: Study on case analysis and effect factors of hot spot fault for photovoltaic module. Acta Energiae Sol. Sin., 1: 271-278 (2017)