This paper was first presented at GPD 2023.
Link to the full GPD 2023 conference book: https://www.gpd.fi/GPD2023_proceedings_book/
Authors: Diana Lohrer and Juan Pablo Martínez
Diana Lohrer is the Director of QC and Internal Processes of Tecnoglass, a leading manufacturer of architectural glass and associated aluminum products for the global commercial and residential construction industries. Diana earned a Bachelor of Industrial Engineering from the College of Engineering at Universidad del Norte. For over 25 years Diana has been involved in the decision making for new machinery and quality control protocols for the production of architectural glass for Tecnoglass.
Abstract
Implementing quality controls and checkpoints during production and inspecting 100% of the tempering process, guarantees less rejections in the field converting into more profit. By expertly comprehending the machinery and tempering process, how it’s done and how the equipment works, a new standard of flatness can be achieved, preventing the glass from being overheated thus reducing the chances of affecting its flatness.
Making industry-wide standards that require flatness measurements will benefit the aesthetics and end users of tempered products.
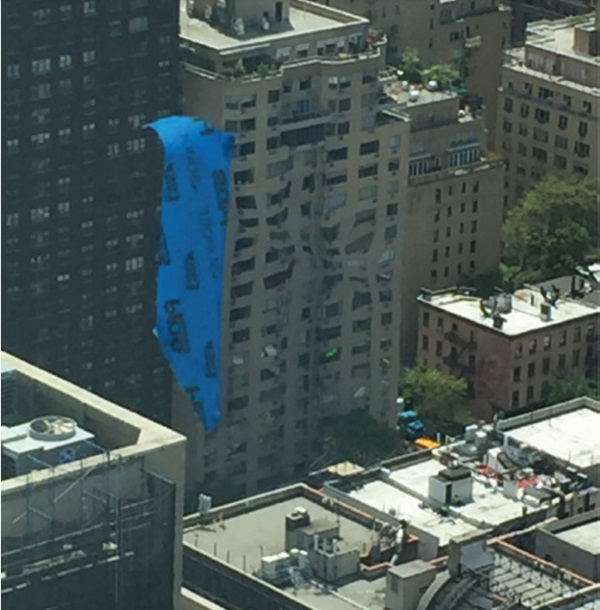
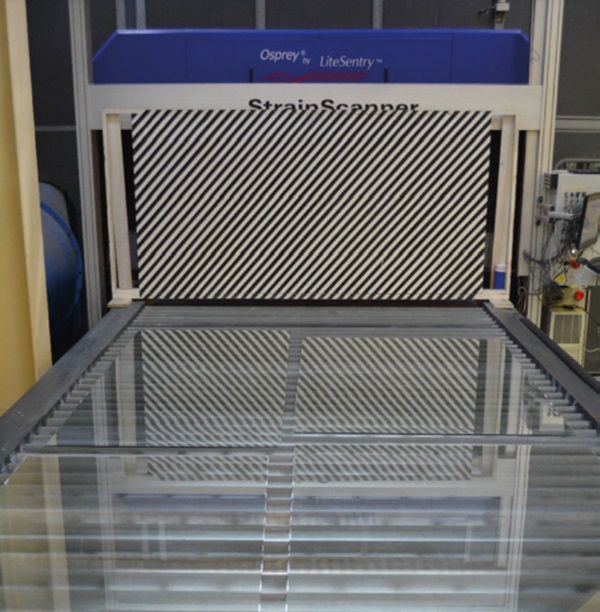
Introduction
Market demand
Today’s architecture requires increasingly larger lites of glass. With larger glass, there is a need to heat-treat it so the glass can withstand the higher wind loads imposed onto bigger surface areas of the glass.
Low-E coatings that reduce the cooling load on buildings by blocking solar radiation, are available with a wide range of exterior reflectance. The exterior reflectivity of the glass can accentuate visible distortion from the heat-treating process.
Finally, construction along coastal areas with hurricane impact and higher windspeeds also means that glass must not only be heatstrengthened or tempered, it also may require multiple layers with laminates consisting of polyvinyl butyral (PVB) or ionoplast interlayers. These requirements all add complexity to making glass as flat as possible.
The increased demand for heat-treated glass has placed focus on the level of flatness and clarity that architects and building owners’ demand. But first, let us get into a quick overview of what heat-treated glass is.
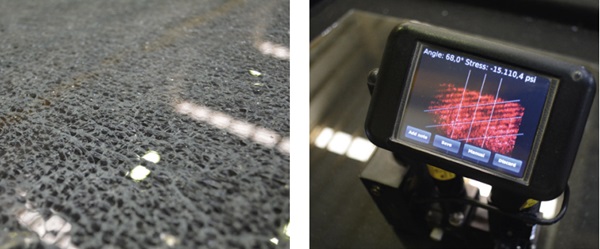
Heat-treated glass codes and standards
Heat-treated glass includes both heatstrengthened and tempered. The glass goes through a tempering oven to heat to a colloidal state and then is rapidly cooled with an air quenching process to induce stress into the glass to strengthen it over annealed glass. Heat-strengthened glass is roughly 2X stronger than annealed glass and tempered is 4X stronger. Tempered glass is also considered safety glass.
The tempering process for heat-strengthened glass creates a surface compressive stress level of 3,500psi to 7,500psi for glass thicknesses of 1/4” [6mm] or less. Tempered glass possesses a surface compressive stress level of a minimum of 10,000 psi for glass thicknesses of 1/4” [6mm] or less. The high level of surface compression for tempered glass causes it to break in small harmless pieces when the surface or edge is penetrated with a sharp object. That is why it is a considered safety glass for use in certain areas dictated by codes.
Heat-treated glass, especially tempered, can exhibit visible distortion versus annealed glass. The distortion can include several measurable items. These include bow, warp, and peak-tovalley roller wave, to name a few.
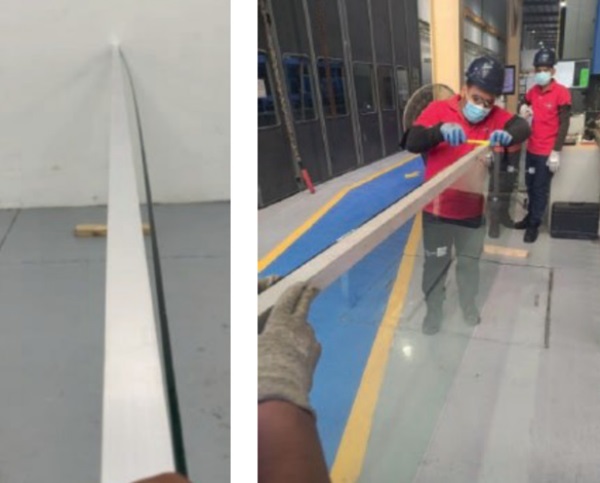
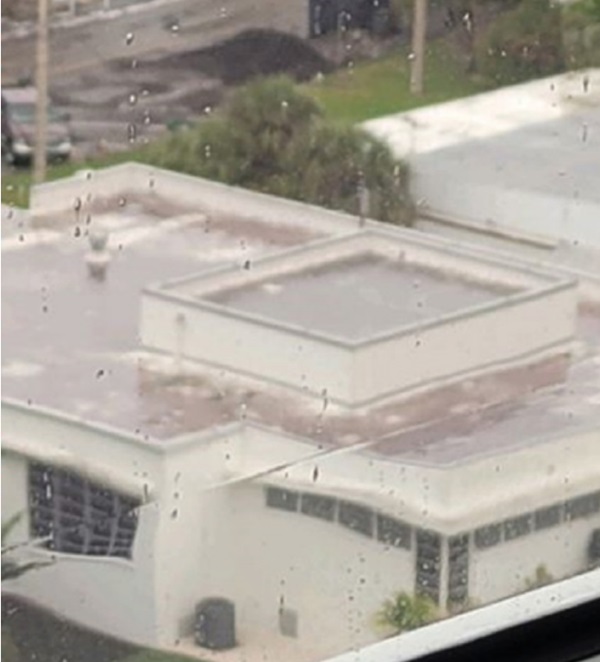
Tempered glass quality standards have been created and have evolved over the years to set guidelines for flatter glass. Some of these are the ASTM C1048-18 “Standard Specification for Heat-Strengthened and Full-Tempered Flat Glass”, ASTM C1651-11 (2018) “Standard Test Method for Measurement of Roll Wave Optical Distortion in Heat-Treated Flat Glass” and the European standard EN 12150-1 “Glass in buildings – Thermally toughened soda lime silicate safety glass”.
These standards set measurable limits to the tempered glass attributes that effect flatness and clarity. This technical presentation will address the ways and means to make flat glass a standard through the tempering process.
It should be noted that there are other factors that can affect the flatness of the glass on a building. Roller wave, for instance, should always be parallel to the glazing systems’ horizontal members. If run vertically it can be more visible on the building façade. It is for this reason the glass sizes and orientations are important as it is loaded into the tempering furnace or oven.
Also, when the heat-treated glass is configured into an insulating glass unit (IGU) the dead air, or gas in the unit, can be affected by barometric changes. The air can expand or contract if transported to higher elevations causing the outboard lite of glass to bow inward or outward. Breather tubes are typically used if there is a significant change in elevation to equalize the air in the IGU.
Exceeding industry standards for glass flatness
The industry specifications and standards that dictate glass flatness are guidelines that should be absolute minimums. Equipment manufacturers and glass fabricators continually strive to exceed the current industry standards. As they achieve this, new standards and specifications evolve to create even flatter glass!
There are several areas to address that help make glass flatness an everyday standard in today’s marketplace. These areas include the tempering ovens or furnaces, digital inspection systems, annealed float glass quality, statistical process controls, preventive maintenance, glass manufacturer’s certification programs and training and education for professional operators and technicians. One of the most important keys to achieving the flattest glass possible is the tempering oven itself.
Tempering furnaces/ovens
Over the years there have been many technological advancements made to tempering oven equipment. These improvements allow the glass to come out of the tempering process much flatter. There are two types of tempering ovens. One is an oscillating oven where the glass goes back and forth inside to reach the needed temperature. It has an advantage in that it has a smaller footprint than a high-speed continuous oven.
The high-speed continuous ovens generally produce better results, particularly for architectural quality glass in the thickness ranges of 6mm to 10mm. Oscillating ovens are often used for thicker glass. Running a wide range of thicknesses in the same oven presents greater challenges for a quality glass flatness since they require different temperature settings and durations. Leading glass fabricators generally have more ovens that can be dedicated to glass thicknesses and glass types.
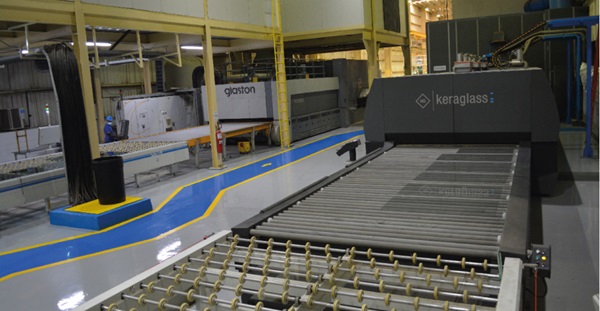
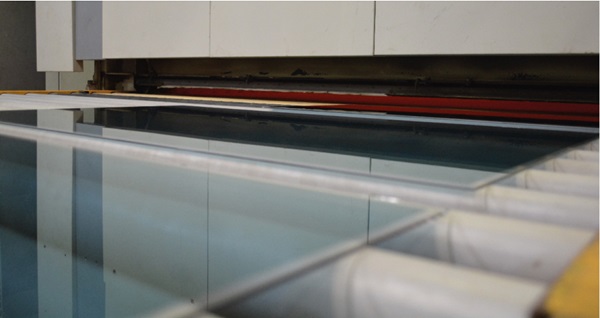
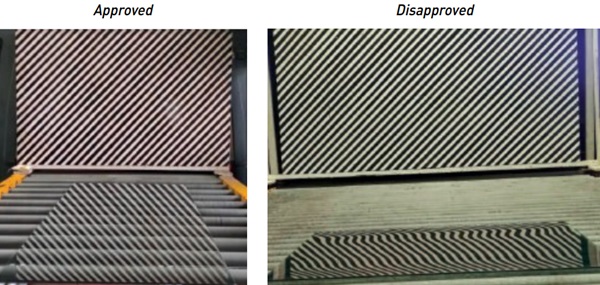
The tempering processes
The tempering process has several steps to get to the finished product. The first step in the process is the cutting of the glass. The raw annealed glass to be cut must be free of defects as described in ASTM C1036. The edge quality is especially important, the edges are seamed with a belt sander. The glass is then washed.
There is also a ceramic frit “bug” painted onto the corner of the lite of glass. This “bug” or logo identifies the glass as safety glass and references the glass fabricator and American National Standards Institute standard ANSI Z-97.1.
The next step is the inspection of the glass for any blemishes. The surface must be exceptionally clean before entering the tempering oven. The glass is then conveyed on ceramic rollers into the oven. The ceramic rollers require special attention as they must be free of any defects or blemishes that could impact the glass and cause rejection. The glass is heated to 630 degrees Celsius (1165 degrees Fahrenheit). At this point, the glass is pliable and can sag on the ceramic rollers. The depth and length of the sagging is the roller wave distortion. For architectural quality glass the depth of the peak-to-valley roller wave should not exceed .003 of an inch in the center and 0.008 of an inch in the border.
The heating of the glass can also create a bow in the glass. The limit of the bow is based on the size and thickness of the glass and is referenced in the listed standards and specifications.
The final step in the process is the air quenching of the glass. The glass lites are slowly moved along the rollers through the quench section of the oven. While there, forced air is blown onto the glass surface. If the glass is to be heat-strengthened the glass temperature slowing reduced. If fully tempered, the glass is more rapidly cooled to create more stress in the glass (more than 10,000 psi). After the glass is cooled in the quenching process the glass exits the oven and goes through another inspection process.
Historically, tempering oven operators relied on “zebra” boards.
These had black diagonal stripes on a white board that was hung at the end of the oven. Glass with excessive distortion from roller wave and/or bow could be seen as wavy stripes on the “zebra” board. This tool is still used but only as a secondary visual aid. Handheld micrometers are also used to roll across the surface of the glass to measure the peak-tovalley roller wave.
Many new digital imaging inspection systems are employed on state-of-the art tempering lines. These systems can read the glass surface much like a topographical map and create images and measurements in Millidiopters. Generally, glass with less than 120 Millidiopters can be achieved with current equipment.
Another benefit of the digital inspection system is the ability to track results and adjust and manage the heating and cooling processes of the tempering oven. State-of-the art ovens provide exceptional convection heating that is uniform and consistent. This is a key element in achieving the flattest glass possible.
Still another benefit of digital inspection systems is the ability to provide records of readings on each piece of glass that progresses through the tempering process.
Statistical Process Control (SPC) is an additional way glass fabricators deliver superior glass flatness. SPC is a method of quality control which employs statistical methods to monitor and control the tempering process. This helps to ensure that the process operates efficiently, producing more specification-conforming glass products with less waste (rework or scrap). Sensors in the oven provide continuous monitoring to the systems computers and the oven operators.
This allows the oven to be accurately adjusted during the tempering process.
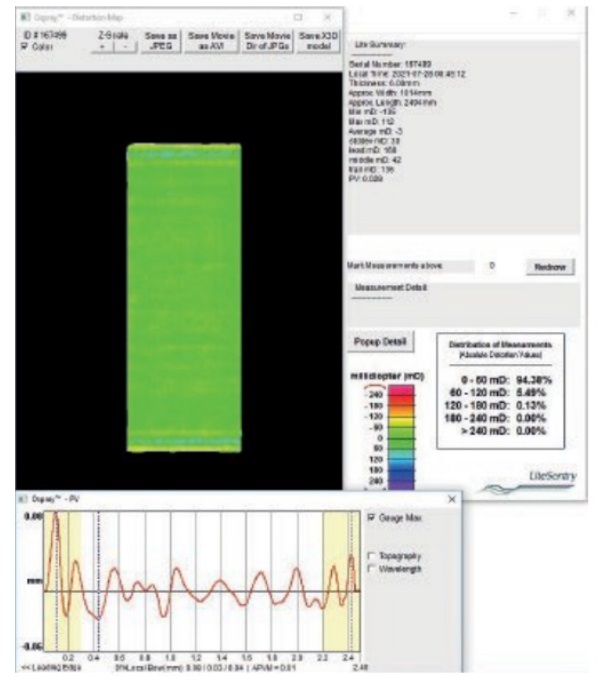
QA/QC
The inspection of the glass should be 100% of each lite that goes through the tempering oven to ensure the flatness exceeds the requirements listed in the ASTM C1651 and ASTM C1048. At times, industry glazing consultants or architects may specify target values that exceed these standards. It is important that the glass fabricator and specifier agree on these values before producing product.
An exceptional QA/QC program is a key component to ensuing the flattest glass possible. Float glass manufacturers may offer certification programs that provide industry leading advanced training and education on glass handling and fabrication to maintain consistency in the production process. Regular audits and training should be a scheduled part of the QC/QA regimen.
Glass tempering ovens and inspection equipment have come a long way, however the people that operate and maintain the ovens and associated equipment are vital to keeping the glass as flat as possible. The best producers of tempered glass use a variety of training and certification programs for their employees. Several glass tempering equipment companies offer these services as does the National Glass Association (NGA).
Training should be held regularly, and certifications updated. New employees should have a comprehensive training manual and existing employees should be required to have expert levels of knowledge on their processes. Staff must be trained on the importance of quality and not only production output. The culture of “total quality before production” targets must be well ingrained to ensure the glass exceeds the established target values.
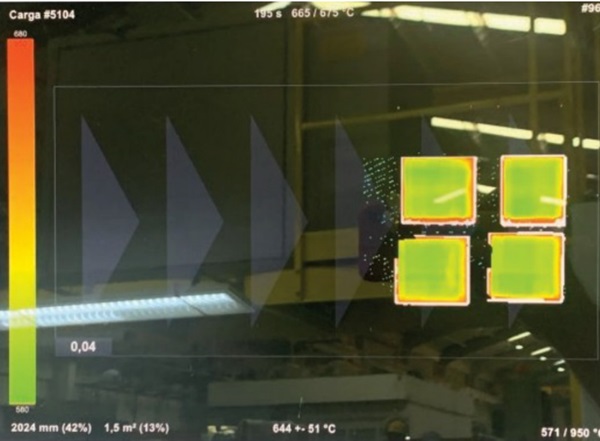
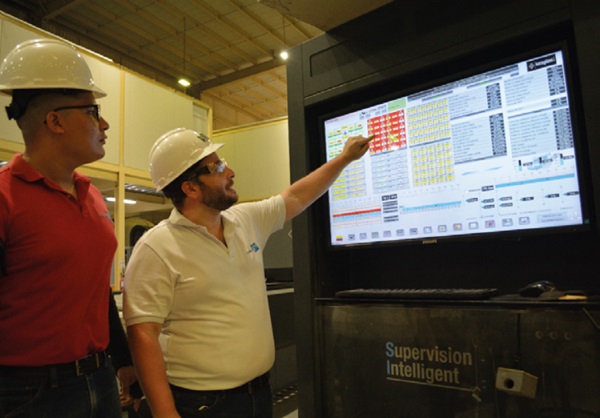
Maintenance
Preventive and regular maintenance is necessary to provide optimal performance of the tempering oven. Large glass fabricators will typically have multiple ovens. This allows to continue production while an oven is down for scheduled maintenance.
Conclusion
Making glass flatness a standard means to achieve an everyday, repeatable, and consistent processes to produce it. As you can see there are several important elements to achieving this goal. Understanding the processes and continuously improving them delivers the quality of glass that customers, architects, and owners expect. The importance of the latest tempering oven technology cannot be overstated.
How the equipment is controlled and maintained is crucial to producing flat glass. Operator knowledge and training should be amplified to produce the best results possible.
The “3P’s” are critical to making glass flatness a standard. “People” are the key ingredient to quality. They should be trained and empowered to know the “Process” of producing the best quality tempered glass. The Process should be ISO certified as well as consistent and repeatable. The Process should always strive for continuous improvement in quality. It should also be supported with the latest tempering oven technology. The third P is for Product. The first two P’s help create the Product that exceeds customer expectations. Innovation drives new “Product” development. The “3P’s all come together for “Making Glass Flatness a Standard”.
As demonstrated in this article, our industry would have a better glass product, if more strict and updated flatness standards were implemented.
References
ASTMC1048
Standard Specification for Heat Strengthened and Full Tempered Flat Glass.
ASTMC1651-11 (2018)
Standard Test Method for Measurement of Roll Wave Optical Distortion in HeatTreated Flat Glass
EN 12150-1
Glass in buildings-thermally toughened soda lime silicate safety glass
TD 04-0326
Standard Test Method for In-Plant Measurement of Roll Wave in Heat-Treated Architectural Glass
ASTM C770
Standard Test Method for Measurement of Glass Stress- Optical coefficient.
ASTM C1279
Standard Test for Non-Destructive Photoelastic Measurement of Edge and Surface Stresses in Annealed, Heat Strengthened, and Fully Tempered Flat Glass
Comments
Establishing a standard for glass flatness is a pivotal step towards ensuring quality and precision in various industries, from architecture to electronics. Consistent flatness not only enhances aesthetics but also promotes reliability and efficiency in manufacturing processes. It's a measure that underscores the commitment to excellence and innovation in material engineering. elevator consultant