First presented at GPD 2019
Curved glass has been in use for many decades. Modern architecture, incorporating more glass and organic forms, is always pushing the limits of what can be accomplished. New technological advances in glass have taken curved glass fabrication to different levels of complexity and performance in the last few years, and design continues to drive into new frontiers.
Keeping up with the most modern aesthetics, structural, safety, and performance requirements has been very challenging when it comes to curved glass. However, the new architecture movement continues to demand glass with forms and shapes, therefore generating an increase in architectural curved glass structures.
The following showcased projects demonstrate examples of how it is possible to accomplish complex curved glass applications when on the front-end manufacturers, fabricators, glaziers, and especially, the design team work in coordination to research materials and the best possible design solutions.
Introduction
In recent years modern building architecture has been designed around diverse stringent performance needs. Some of these buildings have required greater advances in glass to meet such criteria, which have been curved glass.
With new fabrication technologies and a broader range of low emissivity coatings availability in the market, exists a window of opportunity to facilitate the architectural intent of having organic shapes, curved features, or dimensional façade skins. The key to success with these types of unique projects is collaboration amongst the design, building, and manufacturing teams. The following are examples presented in further detail.
Corporate Headquarters Facets of a diamond or slices of pizza in Glass?
The façade of a newly constructed Headquarters building in Detroit, Michigan was designed to create the facets of a diamond. To achieve the large diamond facet formation the architects desired, the glass would require a nine (9.0) meter height and split into large triangular forms. The glass required a very tight curve radius and two flat legs as shown in the drawing (Fig. 1).
This type of curve in a triangular shape, created a stunning constellation of diamond facets or subsequently individual slices of savory pizza folded to a structural shape that allows one to easily hold and fold this Italian delight. Please see below the shape and curve profile for a better understanding:
Such an all glass “textured” façade installation in Detroit required to have certain thermal and solar values specific to its northern territory. Accomplishing these stringent values required glass compositions with the use of coatings. It is known in the industry that glass coatings, predominantly Low E coatings, do not withstand tight radii bends.
Offering solutions in the interest of architectural design, the curved glass fabricator developed numerous configurations and trials over a six (6) month period in order to fabricate the ideal glass make up with the greatest visible light transmission, the most neutral color appearance, the best possible solar and thermal performance, and specifically, consistent quality results given the use of coatings.
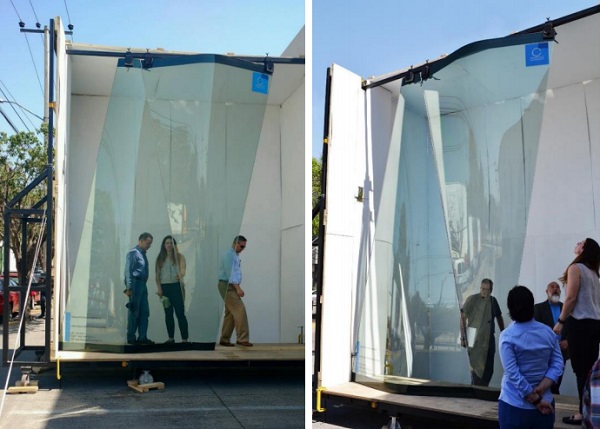
The preliminary design called for a unique shape and curvature with an 8" radius. Various coatings were tested using the required radius, including hard coatings, and coating damage was visible after the trial runs. Understanding the design intent, the geometry proposed, and the fabrication challenges, the curved glass fabricator´s technical team laid out different curve profiles per the drawing (Fig. 2), where the radius could be larger in order to decrease the stress on the coating and the design intent would still be achievable. While the radius seemed to have a large change, from 8” to 16”, the difference in geometry did not present any major change to the design intent.
The curved glass fabricator ran internal trials with the new radius to see if better results could be accomplished. After a number of experimental runs, the hard-coated Low E tested demonstrated consistent results using the 16” radius and the suggestion to modify the radius was proposed to the design team, as seen in the photos (Photos 1 & 2).
The low E coating utilized during the successful trials, Energy Advantage from Pilkington, is very clear and neutral in color, and while it does not offer the best solar performance, it helps lower the U-value of laminated glass, from 1.01 to 0.72 BTU. To accomplish better solar performance and the curve requirement, the curved glass fabricator used an XIR® film interlayer by Eastman which enabled the glass to be highly transparent, very neutral in appearance, and achieve the solar performance shown in chart (Table 1).
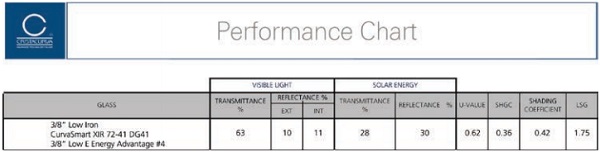
The glass installation details consisted of only top and bottom structural supports, and the vertical edges were butt glazed, circumventing the visual obstruction of vertical structural elements. The shape and radius required the glass to be annealed.
Taking these two (2) elements into consideration, it was critical that the interlayer offered additional structural support and compatible with the film interlayer. Eastman’s DG41 was selected to add structural strength and compatibility with the XIR® interlayer that offered solar performance.
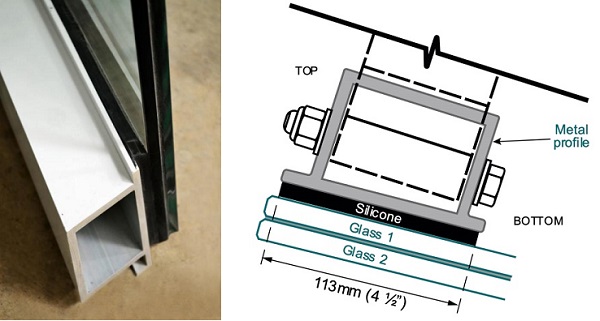
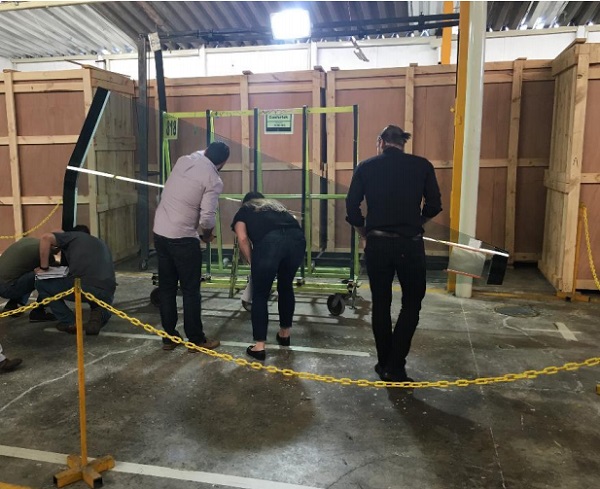
Production of the one hundred and two (102) panels was completed in the time required, and the results obtained in the initial trials were consistent throughout the manufacturing process. To assist the installation process, heavy duty custom metal profiles were shaped and shipped to the curved glass fabricator to be glazed. The structural performance required a 4 1/2” thick layer of silicone that had to be applied following strict quality guidelines and complexity per the figures (Fig. 3).
Performing the glass to metal assembly process in the same factory where the glass was curved, insured that all lites perfectly aligned with the shape of the metal structure and simplified glazing the façade.
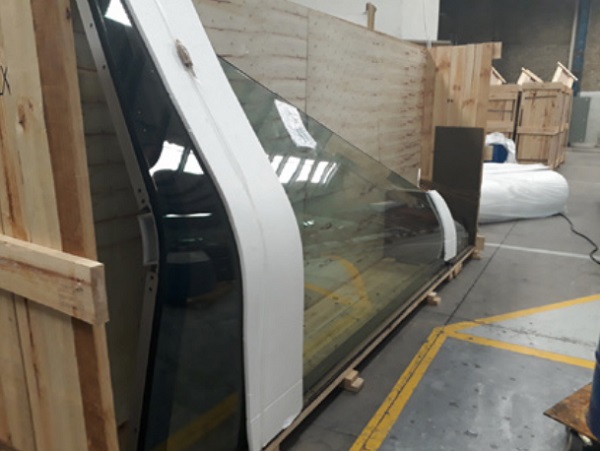
The design and building team visited the curved glass fabricator facility to review the manufacturing process and participated in the inspection of 100% of the units.
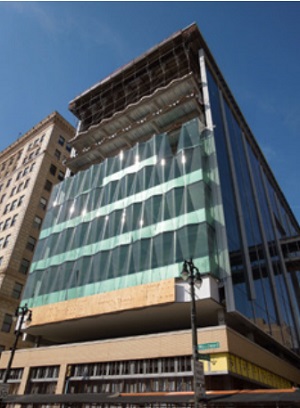
The fabrication of this project exemplifies the strict design requirements demanded from glass in modern architecture and in parallel has to meet safety and thermal milestones. The process of curved glass adds many variables and complexities to coatings and interlayers available, and poses installation challenges.
However, through extensive pre-project research and development, and construction joint efforts, most of the obstacles can be overcome proposing many different products available today worldwide and occasionally conceding on the initial design proposed. Curved manufacturing techniques and knowhow can make some of the most paramount architectural designs possible.
University of Iowa Stead Family Children’s Hospital
Shielding a healing atmosphere with Tornado resistant glass
This particular building designed by Foster and Partners is a Children’s Hospital in Iowa City, Iowa. The end client sought to offer a safe surrounding for the patients and families within the walls of the curvilinear healthcare facility with enhanced protection during severe weather conditions specifically tornados. Testing to find the precise glass formulation to withstand a tornado required a significant amount of time and extensive research, in addition to a strong collaboration between the client, interlayer manufacturer (Kuraray), and curved glass fabricator. Different glass configurations were tested at a certified laboratory to withstand impact and high wind speeds. Once the specific glass construction that met the safety and resistance requirements was determined, it all came down to the fabrication and logistics of the glass scope (Fig. 4).
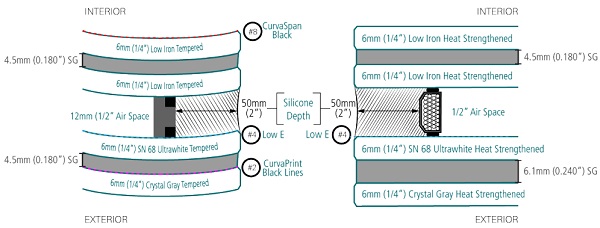
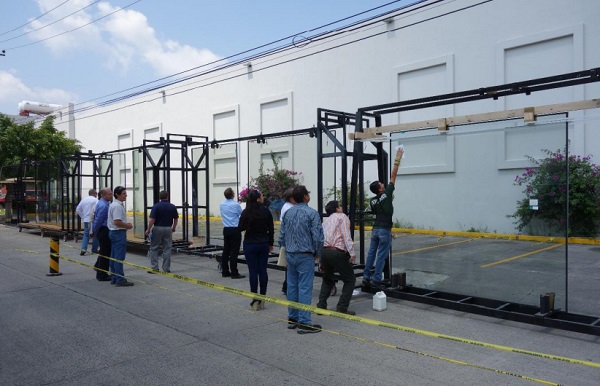
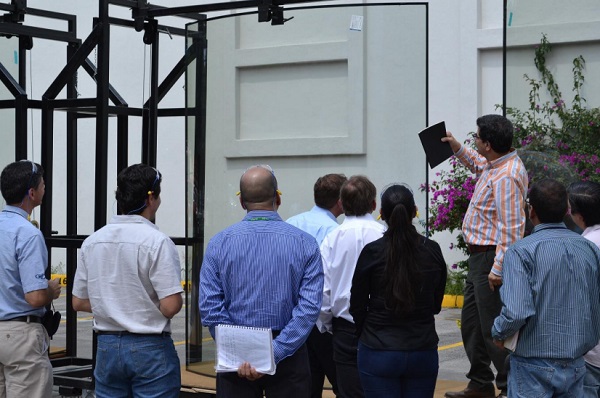
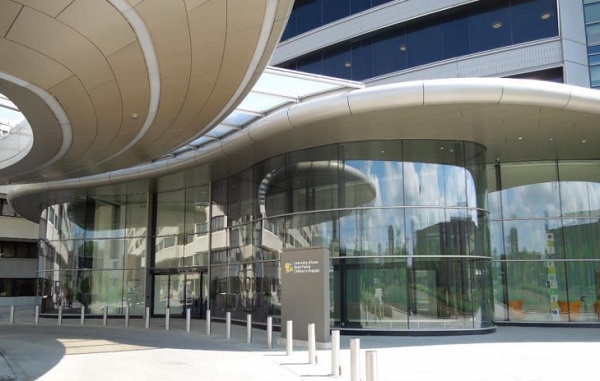
One of the initial challenges in the fabrication of the curved glass was the secondary sealant requirement of 2” depth in order to withstand the strength of a tornado.
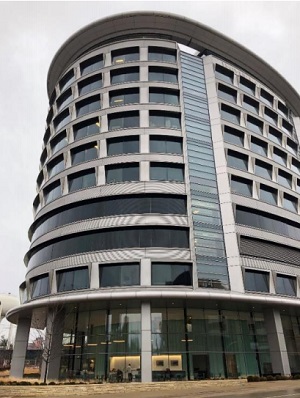
Both curved and flat glass with such a deep silicone infill entail special tooling equipment capable of injecting an impacting amount of silicone. Consequently, this technique required additional exploration and investment that through the joint works of the glazier contractor and building team was possible to accomplish.
The design and building team reviewed and inspected a number of mock ups to determine the best glass make up that met the safety, structural, and aesthetics requirements. This process was significant in securing the success of the execution of the job.
The glass manufactured for the windows is not only large in format measuring at 141” x 90” and able to withstand a tornado, but it also meets energy code. The combination of glass size, volume, quality, performance, flat Table 2: University of Iowa Children’s Hospital Performance Chart and curved, and tornado safety requirements posed a great glass fabrication challenge.
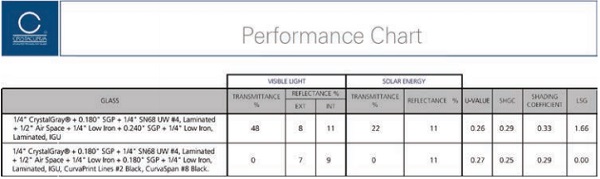
The importance of having a very close collaboration between the building owner, the design team, the glazing contractor, and the glass fabricator, enabled this intricate project that had very complex glass make-ups, to be executed on time and seamlessly.
Conclusion
There are many existing projects beyond the two prime showcases discussed in this paper where performance and aesthetics have played equal principal roles with curved glass applications. The design and performance possibilities that curved glass offers architects and building users is very extensive. Curved glass is not a simple product to manufacture; advanced technology combined with in-depth know how is essential to solve many special design features.
A fundamental element in achieving success with these one-of-a-kind curved glass creations is time allowance to develop the correct glass configurations that can solely derive from close partnerships between project key players.
An extended development process may be necessary in order to achieve a well-executed project and as a result, a collaborative effort initiated at the design stage between the architectural team, the curved glass manufacturer, the glazing contractor, and even other manufacturers of key components such as interlayers or coatings are essential to shaping the footprint into new architectural frontiers with curved glass.