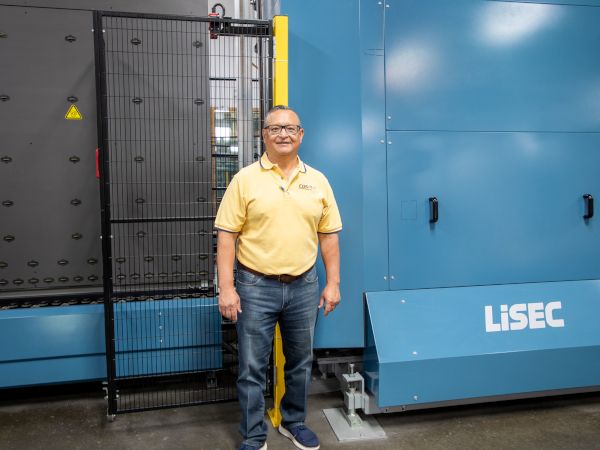
Date: 29 January 2025
In the heart of the refrigeration door industry, a unique opportunity was spotted by three partners with over 75 years of combined experience. They noticed a niche market of customers who were often overlooked by larger suppliers. Recognizing the potential, they founded Commercial Display Systems (CDS) in 2002 in Los Angeles, California. Today, CDS stands as independent refrigeration door company, experiencing strong growth year after year. When looking to increase productivity CDS came across LiSEC, which had the right solution for their special use case – an insulating glass line.
About the company Commercial Display systems
CDS specializes in manufacturing display doors and windows for refrigeration with 75 dedicated employees. How one can recognize this dedication? Every CDS Employee was sporting their best company outfits adorned with their logo, when the LiSEC team visited for this interview! Chapeau! The company sells most of its products in the USA, Canada and Mexico, as well as Central and South America through their Mexican distributor. Their focus is on small customers and specialty applications. For CDS, 100 small customers are more important than one large customer. This customer-centric approach has been the driving force behind their success and growth making the company unique. Refrigerator display doors and windows with heating, often used in commercial establishments, are designed to keep products at low temperatures while providing clear visibility to customers. Their products may seem simple but there is a lot of technology behind them, as the doors and windows have integrated lightning and anti-condensation-heaters, so the glass does not frost up when the door or window is opened.
Tailored for Success: CDS’s Unique Use Case with LiSEC’s Glass Processing Machinery
In 2016, CDS began its cooperation with LiSEC, a leading provider of glass processing machinery. The partnership was initiated at the GlassBuild trade show in the United States, where CDS was impressed by LiSEC’s insulating glass line and its accompanying software. After visiting a glass processing facility in Northern California, CDS was convinced that LiSEC was the equipment of choice. CDS Partner Fernando Calderon states: “We were falling behind our production schedule, so we looked at equipment to increase our productivity. At first, we did not consider a glass assembly line for our special use case. We just considered achieving a higher output through multiple glass washers with the ability to assemble more glass units. At that time glass assembly lines were introduced to us at a trade show, and we began to investigate. The response from LiSEC was very positive and we got the opportunity to see the equipment at a customer. We were very satisfied and impressed with the quality of the LiSEC equipment that we immediately decided what equipment we were going to purchase. That's where our relationship with LiSEC began.”
How LiSEC Products Enhanced CDS’s Production and Productivity
For the frame processing of the refrigerator doors and windows, CDS uses a LiSEC A1RL-F desiccant filler and a LBH-25V semi-automatic coating extruder for butyl. The LiSEC BSV-45NK is an automatic spacer bending machine, which helped CDS to more efficiency. Mr. Calderon highlights: “Before having a LiSEC bender we used to manufacture the spacer in four pieces, which was quite time consuming. The bender is excellent and allows us to be more efficient.” The bending head is designed with a maximum expansion stage, allowing for the processing of various materials. In addition to aluminium, it can also handle stainless steel and plastic materials, which are cold bent. The machine is equipped with a profile magazine that has 4 slots and clamping mechanisms. These mechanisms relieve the lowest profile bars, ensuring frictionless removal.
The IG line is equipped with a VHW-D20/V6 automatic washing and drying system, which guarantees that each glass pane is cleaned and ready for the next stage of processing. The SAF-1000 filter system significantly reduces water consumption and efficiently supplies the VHW-D20/V6 with recycled pure water. For the purposes of frame mounting and inspection, an RSV N-25/20S is utilised. The FPS-25/20U2B gas filling press with lifting spindle drive and fixed seal bar is employed for the assembly and gas filling of the units. Subsequently, the units are conveyed to the LiSEC VL-1N sealing system, which guarantees a perfect seal. Due to its uncomplicated mechanical construction, the sealing station ensures process safety and stability, as well as a high degree of operator and service-friendliness. The line also has LiSEC software integrated to guarantee the highest quality of the processed units. GPS.perfectscan enables the inspection of each individual glass sheet for visual defects. “At the insulating glass line, we insert a low-e-glass with a clear piece of glass, and with the glass spacer into the line. The glass is processed by the IG line and we end up with a completed sealed glass unit. Then we transport the glass units to the door assembly area, and we assemble the glass door,” says the CDS Partner Calderon about the production process at the insulating glass line.
The LiSEC machinery has led to a notable increase in productivity at CDS. Prior to the introduction of the LiSEC insulating glass line, each piece was washed and sealed by hand. The production time for what previously took a week has now been reduced to just three days. The quality of the glass units produced has also improved, providing CDS with a competitive advantage in the market. Calderon of CDS states: “From the washer all the way to the final sealing of the glass unit, that whole piece of equipment is very impressive, and it is able to do what we require.” At CDS they take very good care of the LiSEC equipment. Each machine is cleaned at the end of the day, so the six-year-old insulating glass line looks like it was placed in operation last week. As mentioned above, the products of CDS are complex and electrical components need to be installed before sealing the unit. This special case showed that LiSEC machines can master this challenge successfully.
A Commitment to Future Growth and Excellence with LiSEC
But the partnership between CDS and LiSEC is not just about machinery. It’s about shared values and a commitment to customer service. CDS appreciates LiSEC’s excellent customer service and maintenance support. When a part needs replacement, it arrives at CDS’s facility the next day, ensuring minimal disruption to their production. As CDS continues to grow, they look forward to further collaboration with LiSEC.
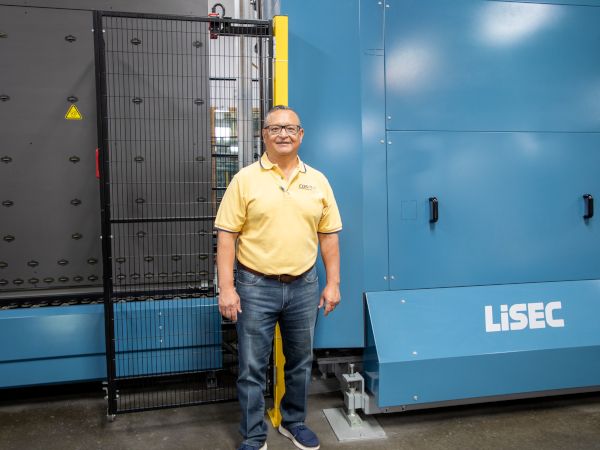

Add new comment