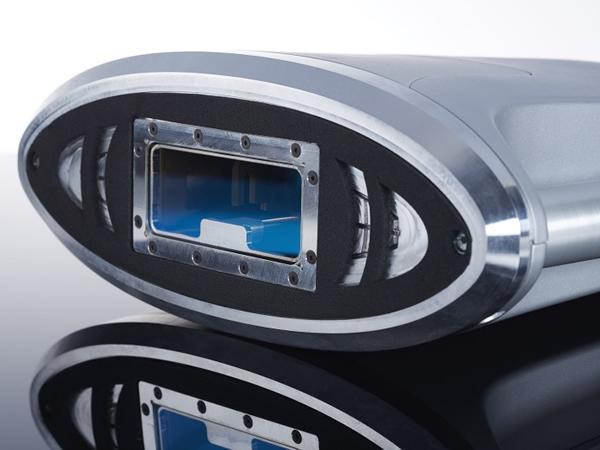
Date: 26 June 2020
This year we are proud to celebrate the 20th anniversary of Sparklike. Over the years our Sparklike Handheld™ and Sparklike Laser™ devices have become the de facto world standard for gas fill measurement of IGUs. To mark this occasion we have created a Sparklike 20-year anniversary series, where we take a closer look behind the scenes.
In this third article of the series, we dive into the breakthrough technology used in the manufacturing of our non-destructive insulating gas analyzers. In our first article of the series, we described the advantages of gas fill for thermal performance and the developments in gas fill measurement while the second article discussed the applied research and the partnering entrepreneurs behind Sparklike.
Taking gas measurement further
While the spectrum analysis technology applied in earlier Sparklike devices solved the issue of measuring the insulating gas content in a unique non-invasive way, it was however faced with limitations due to continued industry development. New types of high-performance glass products were introduced and new coating solutions brought substantial savings in energy inflow from solar radiation.
The original high-voltage spark technology had held out well on the market but the increasing use of products with multiple Low-E coatings or thick spacer cavities, such as many triple-glazed IGUs, raised the need for new, additional measuring capabilities. The challenge was to measure through the coatings and lamination, as well as triple glazing using a single measurement. Additionally, what was needed was the possibility to measure a full range of argon from 0 % to 100 %, as well as including the product as part of the manufacturing process, preferably on-line.
The glass industry and IGU manufacturers, in particular, had high hopes for new developments in IGU gas fill measurement and the Sparklike product development team paid close attention to the signals from the market. With the new advanced product developments in view, Sparklike placed specified demands on the criteria for the new product that was needed to meet the measuring challenge.
Breakthrough technology
In 2011 Sparklike set out for a new technology breakthrough in initiating development work based on laser application. This resulted in a new product line – Sparklike Lasers ™ – launched on the market in Spring 2015. Today this product line consists of Sparklike Laser Portable ™ and Sparklike Laser Standard ™.
We were able to develop a laser system to meet the market demand that focuses on the measurement of oxygen absorption. The technology is based on TDLAS, which is short for Tunable Diode Laser Absorption Spectroscopy in the 763 nm range. The method is indirect in measuring the oxygen absorption in the IGU and deducing that the rest of the contents consist of gas – argon, krypton, xenon – whichever is applicable.
This measuring technology is based on oxygen absorption. A laser beam from a laser diode is focused into the IG, resulting in reflections from the IG surface being detected. The device is operated from a single side of the glass. The measuring time is 18 – 28 seconds, depending on the IGU structure.
The maximum IG thickness for this application is 51 mm (from surface 1 to 3 (DGU), from 1 to 5 (TGU) measured from one side), the glass thickness range is 2-23 mm, spacer bar 4-40 mm. The new laser-based technology is capable of non-invasive measurement through both coatings and laminations. Furthermore, the technology allows testing of complicated structures, such as energy-efficient triple glazed units. This brings the level of quality assurance of these high performing glazing units at pair with advanced product expectations.
In order to make an analysis, the laser needs to penetrate the coating. Therefore, the coating transmission sets boundaries for the signal to be detected. The final limit depends on the full structure, but as a guideline transmissions above 30 % on 763 nm wavelength are measurable.
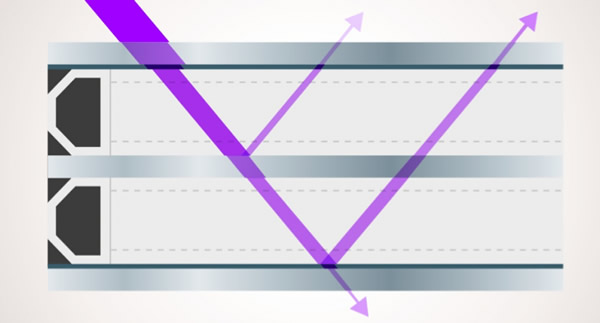
Oxygen absorbance
Oxygen, like other gases, has certain absorption lines, (wavelengths). Sparklike Lasers utilize a tunable and narrow-linewidth (monochromatic) diode laser. The diode laser operations current laser frequency can be tuned over an absorption line to measure the variations in transmitted intensity. Techniques for laser modulation are extensively used to improve the performance of the TDLAS-system.
A sinusoidal component is added to the diode laser operation current, resulting in a sinusoidal wavelength and amplitude modulation of the laser output. Interaction with a wavelength-dependent and non-linear transmission (absorption lineshape) results in a periodic, but non-sinusoidal transmission signal that consists of the modulation frequency itself as well as its harmonic overtones.
The amplitude of the harmonic component is proportional to the absorbance, i.e. the amount of oxygen. The reading is then displayed as the insulating gas content percentage. Additionally, this new method also measures the thicknesses of the glass and spacer cavities. This information is received with high accuracy of +/- 50 micromillimeter and is reported with the gas reading.
Sparklike Lasers ™
The Sparklike Lasers consists of three parts:
i) the main unit that includes the power source electronics and does the calculations in the background.
ii) a measuring head including the more sensitive electronics and optics.
iii) a screen for the user interface.
The system has the capability of saving and exporting results as well as identifying data.
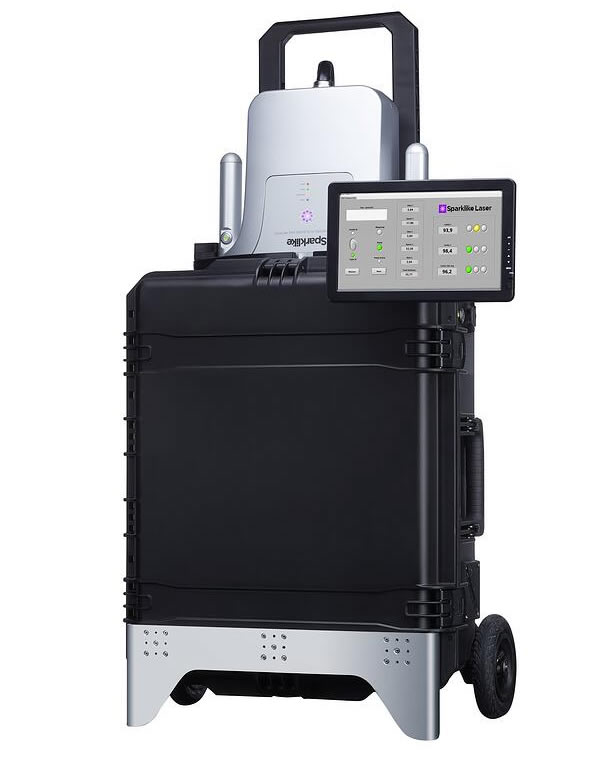
ADDITIONAL INFORMATION ON THE SPARKLIKE PRODUCT RANGE:
Sparklike Handheld™ – Portable and battery-operated gas fill measurement of standard double glazed IGUs
Sparklike Lasers™ - Measuring IG gas fill of triple and double glazed units
Sparklike Line Integrated Solutions™ - Sparklike Online(™)
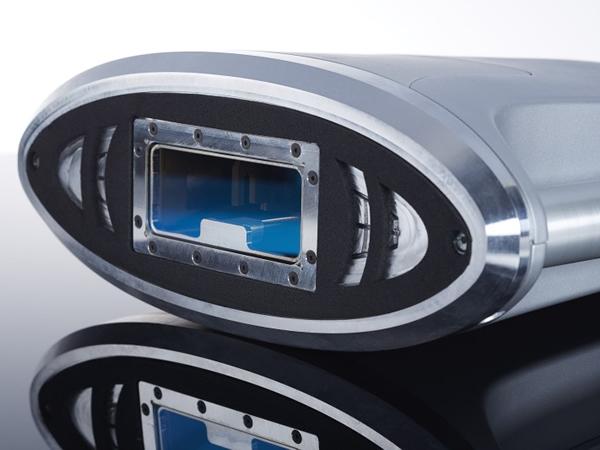

Add new comment