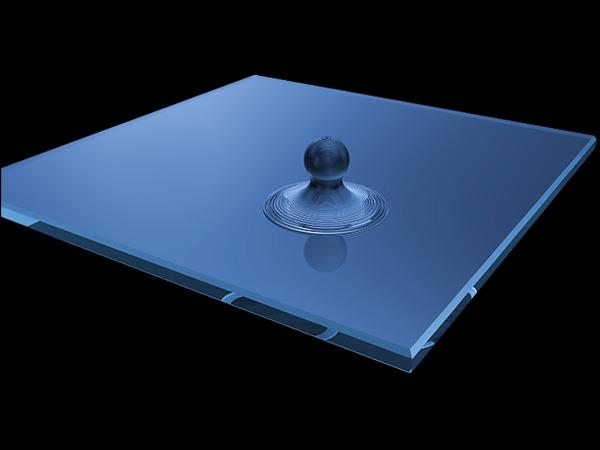
Date: 7 October 2020
Metals, concrete, and plastics are all materials which can be printed. But what about glass? Companies, institutes, and universities are researching the possibilities and have been able to gain experience from experimental procedures. The most common materials used here are silica glass or borosilicate glass, while applications using soda-lime glass are less common. Printed glass can be used in many applications, which is why it is certainly worth investing time and money into research.
Glass is becoming ever more popular in building architecture as it is deemed a modern and elegant material. The growing demand for large and custom glass façades which can take on additional functions is spurring on designers. Glass fronts must not only be aesthetically appealing, but also securely installed and durable, as well as being able to permanently withstand the enormous loads they are under.
However, visible joints and load take-up points disrupt the image of a homogeneous, transparent façade. In general, attaching the panes requires holes to be drilled in the individual elements, which harbours the risk of damaging the glass and thereby reducing its strength. Another option is to use adhesives to join components, but this has the disadvantage that the adhesive materials can age quicker than the joined parts due to UV radiation.
A further aspect is that joined elements with different mechanical and thermal properties are used for both drilled and glued joints. Using glass from a 3D printer as a joint material, for example for point fixing, results in two identical materials with the same properties being joined together. This avoids different heat expansion factors between the materials, and the risks inherent with using drilled holes or adhesives are no longer a factor.
The Glass Competence Center (ISM+D and MPA IfW) at the Technical University of Darmstadt is conducting research on how to create a substance-to-substance bond on float glass using additive manufacturing (3D printing), while simultaneously increasing its rigidity. The scientists here are testing fused deposition modelling, amongst other approaches. Their aim is to enable glass panels with an area of up to 3.25 x 20 metres in the future.
Two important factors are the process temperature and the viscosity of the glass. In order to create a joint between a pane and a glass structure, the pane must be heated significantly beyond the transformation temperature of glass at the join. If insufficient heat is applied, the structures will not join together, while if the temperature is too high, unwanted deformation can occur. Internal tension in the joint reduces its strength and ability to support loads.
Brittle material behaviour and a combination of individual process and material parameters can also have a significant impact on the result. It is, however, absolutely possible to manufacture a homogeneous joint in a desired geometry with an appealing and transparent appearance using 3D printing. The scientists at TU Darmstadt also hope to find an answer for the question of how to convert this procedure into an automated process.
Visitors to glass technology live at glasstec 2021 can also look forward to a further research project, as the scientists are planning to exhibit a 3D printed glass staircase with glass brackets.
Just like glass
When comparing the material properties, environmental impact and raw material properties of glass and plastic, glass comes out on top across the board. Unfortunately, melting glass is both complex and expensive, which is why the industry prefers plastic in part. The general methods used to process glass have hardly changed over the centuries, with the most common being grinding, polishing or etching.
Glassomer GmbH develops materials and technologies which first enable the shaping of polymer nanocomposites at room temperature, before they are subsequently converted to glass at temperatures between 700°C and 1300°C. Glassomer® is a silicate nanocomposite, which enables highly pure quartz glass to be manufactured from a solid, paste or liquid state.
Liquid Glassomer can be used to duplicate components at room temperature through casting or stereolithography. Solid Glassomer can be structured using traditional subtractive techniques such as drilling, milling and turning, or even with a knife. Thermal polymer transformation technologies such as nanoimprinting, thermoforming or roll-to-roll replication are also possible.
Glassomer components are chemically and physically identical to commercial quartz glass. They have comparably high optical transparency in the visible, UV and infrared spectra, as well as equal thermal and chemical stability and mechanical strength. Additional solids in the starting material help prevent the glass from shrinking during manufacturing. It is also possible to manufacture components with threads.
Simple technologies, such as casting, enable uncomplicated replication, and smaller components can be created using simple 3D printers. More complex tasks require high-resolution microstereolithography. Using this procedure, extremely fine structures with diameters of just tens of micrometres can be created without transitions. Glassomer is the first product to enable the structuring of high-quality quartz glass using polymer processing technologies.
The replication is accurate right down to just a few micrometres and the resulting glass has a surface roughness of a few nanometres, which meets the demands of both optics and photonics applications. Users can create voids in bodies using sacrificial templates and extremely fine structures in bulk materials.
Melt first, then print
The Günter Köhler Institute for Joining Technology and Materials Testing (ifw Jena) in Jena collaborated with FH Aachen University of Applied Sciences to analyse laser powder bed fusion (L-PBF) of borosilicate and quartz glass powders within the process chain of 3D printing. This procedure has benefits including free geometric shaping, low production costs in small and medium-sized production runs and comparable component properties of the glass bodies.
The scientists characterised the glass powder classes based on their geometric, thermal and mechanical-physical properties, and analysed how they can be processed at different laser wavelengths in the L-PBF process. To this end, the plant technology was adapted to the conditions of processing glass using CO2 laser radiation. The effort is worth it, as glass meets requirements in glass equipment or chemical plant construction that metal cannot. Glass has a high temperature resistance, thereby requiring a high energy input to melt, and is a poor conductor of heat.
Scientists wish to investigate how they can overcome this factor and the poor absorption at the wavelength of 1,064 μm. They were already able to prove that it is generally possible to process glass powders and define process parameters, such as laser power, scan strategy, powder coat thickness, chamber heating and much more.
Researchers manufactured test specimens made of borosilicate and quartz glass and subsequently assessed their quality. The parameters were strongly dependent on the geometric shape of the specimen due to the heat agglomeration. Tempering can help improve the quality of the glass components. Further experiments aim to test the porosity, roughness and density in relation to the L-PBF parameters and clarify the possible application areas for the components.
The thermal and chemical resistance inherent to quartz and borosilicate glass have resulted in them becoming proven materials in glass equipment construction, microfluidics, microelectronics, optics and medical technology. A further research project at ifw Jena aims to develop an additive process based on laminated object manufacturing (LOM) with the goal of enabling additional industrial applications.
In this project, complex glass components – for example with interior cavities – are constructed which could not be manufactured using conventional fabrication technologies. The procedure is intended to combine laser cutting and diffusion welding. Aside from quartz glass, CO2 laser cutting (λ = 10.6 µm) causes the glass composition in the area of the cut edge to change, the thermal expansion coefficient to shift and a bead to form. The research goal is to define process parameters for the respective glass in order to remove these effects.
Important links:
glass.vdma.org
If you have any questions, Gesine Bergmann, Technology Consultant at the Glass Technology Forum (+49 69 6603 1259 or gesine.bergmann@vdma.org) will be happy to assist.
VDMA represents around 3300 German and European companies in the mechanical and plant engineering industry. This innovative industry is export-oriented and predominantly made up of SMEs, employing around four million people in Europe, including more than a million in Germany alone.
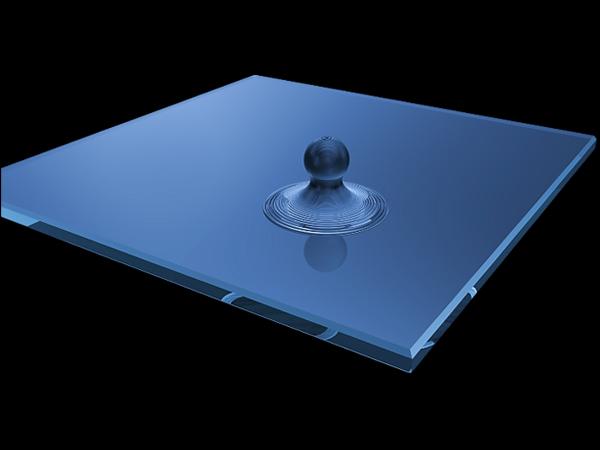

Add new comment