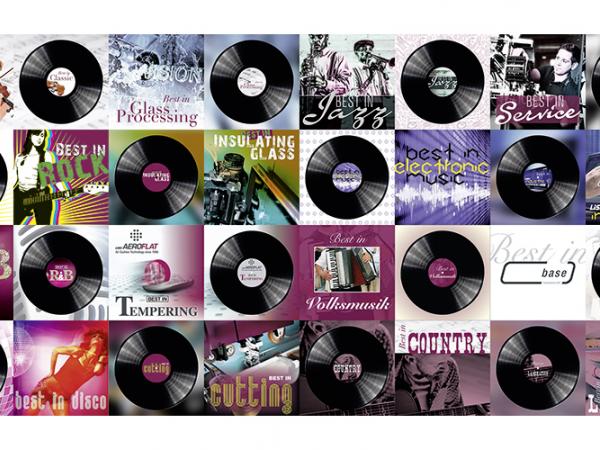
Date: 8 July 2016
Under the motto “best in glass processing”, which is also the new claim of the company, the plant manufacturer will present bestsellers which are hits in the fields of software, cutting, tempering, insulating glass manufacturing, glass processing, logistics & handling as well as service.
LiSEC Hits – the Trade Fair Concept
LiSEC associates its hits with “the best in“ from different music genres – the central idea of music, hits and instruments is not only taken into consideration at the exhibition stand’s design, but also already at the invitations to the trade fair. This will be a different kind of trade fair appearance. Experience LiSEC and its hits in hall 17, stand A20!
Best in Tempering: AEROFLAT
In August 2013, the LiSEC development team started a major project with the mission to redesign the tempering furnaces in order to save manufacturing costs and at the same time increase the process reliability.
Result: the AEROFLAT. Internorm, Europe’s leading window brand, has already bought the new AEROFLAT – the tempering furnace has been running at full capacity at Internorm since March 2015.
„It was a large and especially exciting task because we knew: we won’t achieve the objective with minor measures so we pretty much started from scratch“, says Manfred Spreitzer, LiSEC project manager.
The new AEROFLAT is technically more sophisticated and weighs almost 50 % less than its predecessor.
Technology 1: The evenness
The team achieved an almost 100% evenness by the still better design and the technically more sophisticated implementation of the ceramic air cushion bed in the furnace.
This did not only lead to a processing result of the glass sheets with an even higher quality but also to an increased process reliability because the risk of damaged sheets is reduced.
Technology 2: The convection current
The convection current in the furnace was optimized by means of a computer-aided flow calculation tool, which simulates the convection.
With the resulting lessons learned, the development team constructed a prototype as a model by means of which the team carried out the corresponding tests and again and again compared theoretical and practical values.
Technology 3: The light-weight construction
The team has revised the entire construction and, for this purpose, has used concepts from the light-weight construction. All in all, the developers were able to save approximately half of the weight without impairing the performance of the AEROFLAT.
This weight reduction has advantages for the assembly (lighter engines and tools as well as simpler handling) but also for the customers due to lower transport costs and generally lower production costs.
Spreitzer: „We have determined the optimum component strength and designed the construction so that we were able to save as much material as possible. Thus we were able to realize a reduction of the manufacturing costs of approximately 20%!“
An important aspect of the redesign was also the service and maintenance friendliness at the customer’s. Now, wear and maintenance parts can be removed and installed more easily due to the corresponding working height (ground level).
Another plus factor which brings benefits already during assembly due to the simplicity and optimum set-up times. „The redesign project has gone extremely well along our meanwhile very well established development process: we had a perfect cooperation of the different departments in a small team at one location“, says Spreitzer.
What is particularly pleasing is the fact that the first tests have already been very successful and that the engineers had to do only minimal retouching. Spreitzer: „The first AEROFLAT was installed at Internorm and has been running smoothly for more than one year!
AEROFLAT: one technique – many advantages
- No waiting time when the types of glass are changed
- Wear-free ceramic components
- Significantly shorter heating time
- No cooling of the heating zone required in case of glass breakage
- Identical cycle time for coated and uncoated glasses
- Operators trained in only five days
- 50% less staff required compared to conventional plants
- No touching of the glass surface throughout the entire process
- The tempering of double-sided coated and printed glass sheets is possible
- Thermal tempering of glass is possible from 1 to 10 millimeters
Best in software: Industry 4.1 à la LiSEC
Industry 4.1 by LiSEC allows transparent and efficient production processes in the sector of the glass machining and processing industry.
The integrated networking from the preparation of offers to the delivery supports the optimization of the production process and allows a seamless product tracking.
Integrated quality checks along the production process beginning with the incoming goods inspection to the final check at the end of production allow a consistent quality report thanks to the networking which may act as a quality proof for a specific order.
Learning and self-optimizing production machines and plants autonomously make decisions about the tools to be used and machine settings and thus increase the efficiency.
Predictive and preventive maintenance is possible due to the permanent and consistent monitoring of the plants by means of integrated sensor and assistance systems.
This maintenance helps to prevent unplanned downtimes and thus increases the availability of the plants. It is also possible to plan and organize service calls and required spare parts in an automated way.
The evaluation of the collected data in real time results in receiver-oriented reports which continuously provide the acting persons with relevant information and thus the basis for decisions.
At the glasstec trade fair, LiSEC will present its concept Industry 4.1 on the TPA line. The centerpiece here will be the LiSEC Line Coordinator: all data of the line and its plants are collected and processed there.
Best in Insulating Glass Manufacturing: Fast Lane Concept for TPA
LiSEC will present another hit at the glasstec 2016: The leading manufacturer for plants and software for the flat-glass processing industry has developed an entirely new concept for the production of insulating glass units with thermoplastic spacers. The concept is designed with respect to cycle time, high quality and accuracy.
Key features:
- From the cutting to the completion of the insulating glass unit, no manual intervention will be required under normal circumstances,
- The concept only provides for one applicator and achieves a cycle time of 35 seconds for standard triple-glazed insulating glass (size: 1m2)
- High-Speed due to an innovative LiftOver system
- Saving of investment-intensive core machines
- New industrial design
Core plants of the fast lane TPA line:
Assembly press: The press used in this concept is a completely new development. The title AGP press (AGP stands for assembling, gas filling, pressing) ensconces a press which is, on the one hand, fast – we guarantee a cycle time von 35 seconds for triple-glazed elements in paired operation (basis: triple glazing – one sqm size) - and which features an extremely high pressing accuracy on the other hand.
The tolerance for insulating glass up to a size of 2.5m2 amounts to a maximum of 0.5mm with reference to the element thickness. The press may be used in a very large range of applications due to the fact that the new AGP press can process elements of 350 kg/running meter (and up to 200 kg/running meter for the first two glass sheets).
When producing step(ped) elements, the step bottom edge may be 150mm and the step upper edge may be up to 700mm. A particularly important feature of this press: up to triple-glazing insulating glass, all glass sheets are supported at any time during the assembly which prevents any sliding down.
The AGP press also scores in terms of ease of servicing: an exchange of the press plates is possible without losing the accuracy.
The AGP also features the LiSEC gas filling technology in case of which the gas is, by means of a laminar flow, filled from the bottom across the entire width of the insulating glass element without bending the glass during this process.
CleanSeal technology: the LiSEC sealing solution features a highly dynamic self-regulatory servo-controlled dosing system. It recognizes temperature variations and changes in the viscosity among other things caused by differences between batches and downtimes and it adjusts itself.
The CleanSeal concept also includes an unwinding device which finishes off the corners instead of only correcting them. The overall system is so elaborate that one operator is able to cover all work steps.
Especially the so-called “dabbing of the corners” is almost entirely obsolete. The dosing of the CleanSeal is a robust solution in case of which LiSEC relies on approved technologies.
Thus, LiSEC does not use any prone to wear and therefore relatively expensive and inaccurate gear pump but a servo-controlled throttle valve: sealing material is applied with an open controller as long as possible, i.e. the material is optimized and controlled via an open discharge flow, the material feed is only throttled in the corner areas.
New in the CleanSeal concept is the patented full support belt – a transport belt which is able to process elements with a weight of up to 350 kg/running meter and the same steps as the press.
The fast lane principle: The TPA line exhibited at the glasstec 2016 has an elaborate lift over system allowing the overtaking / passing of glass sheets on which no spacer needs to be applied: sheets of an average construction window size are, by means of a lifting system and on the same roller back wall, transported over and past the sheet on which a spacer is currently being applied up to the press where they are lowered – a maximum of gained time!
UTS: the finished insulating glass units are automatically lifted on the TPA line. Insulated glass units remain in the curing buffer until they are cured so that any manual handling (packing) won’t have any influence on the accuracy of the element thickness.
LiSEC has developed a new industrial design which will presented at the glasstec for the first time. The design conveys LiSEC’s clear, strategic message: “best in glass processing” and makes the LiSEC brand values a tangible experience directly at product level. The exhibited TPA line is wearing this new, really awesome dress!
Best in Glass Cutting
LiSEC presents the fastest cutting technology worldwide! The revised RS cutting technology 2016 (grinding & cutting in one working operation) constitutes the worldwide fastest solution in terms of production runs with a high percentage of coating (>60%).
For typical cutting patterns, our ESL-RS is by approx. 10% faster than the fastest cutting plants in the market. Combined with the new innovative glass storage solutions such as the package loading system and the revolutionary FlyOver glass loading, the glass storage costs and the cycle times are reduced to a minimum thanks to the highest storage density.
This optimally coordinated LiSEC glass cutting plant is rounded off with a breaking plant designed for the application purpose. From the simple breaking table to the fully automatic high performance tandem (double) and triple dispatch: LiSEC provides a solution matching the customer’s requirement. And the best thing is: LiSEC plants are indefinitely extendable.
Thus, our customers’ security of investment remains guaranteed even in case of future increases in capacity or any shifting of the fields of work.
Best in Glass Logistics
The flat-glass-processing industry and the world of insulating glass manufacture are changing rapidly. Increasingly shorter delivery times combined with increasing quality requirements generate the pressure to produce free from defects. This is why LiSEC pays particular attention to quality in the production, downtime management and part tracking.
LiSEC’s overall objective is a one hundred percent automated production which means that as few as possible manual handling is required in order to prevent production faults due to scratches, mixing ups or damaged and/or broken glasses.
At LiSEC, this approach starts with the truck which delivers the raw glass. This truck is automatically unloaded by a ground-based or overhead storage system.
This system is combined with a fully automatic warehouse management, glass cutting and breaking plants as well as an autonomous residual plate management.
In terms of glass sorting, our customers may choose between the approved stationary solution which consists of a glass buffer and a shuttle and the mobile sorting system MSB which may be loaded and unloaded fully automatically.
Perfect logistics plays an important role, in particular when it comes to insulating glass elements with thermoplastic spacers (TPA). The insulating glass elements are generally very sensitive until the sealing material is cured.
In order to prevent deformations, tolerance errors or even the destruction of the product, LiSEC has developed the fully automatic glass removal system UTS which carefully removes the elements and takes them to the curing zone at which end it is possible to perform the dispatch as usual.
At the glasstec trade fair, LiSEC will present a logistics innovation: the new tilting shuttle SHL allows layout plans in even the most confined spaces which would not be possible otherwise.
The tiltable glass shuttle covers standard inclination of 2-6° but it also tilts horizontally (90°) if required. The tilting shuttle uses the approved SHL system’s rail system and may therefore be operated highly dynamically with speeds of up to 300m/min and accelerations of up to 3m/s².
The innovative combination of a shuttle with a tilting table allows the connecting of horizontal lines such as a curing oven or cutting lines with vertical lines such as machining centers or insulating glass lines.
Customer benefits:
- It is now possible to realize customer wishes which have so far been impossible due to confined space conditions.
- Saving of at least one tilting table including safety fencing per line
Best in Glass Processing – no Compromises in Terms of Processing
In the field of flat glass processing, LiSEC has been pursuing a clear objective for years: the best vertical processing quality at the lowest life cycle costs.
Operators of glass processing plants benefit from many years of experience of the pioneer in the vertical processing in particular in terms of the edge processing with peripheral wheels.
Sheets with dimensions exceeding the jumbo format as well as glass thicknesses of less than 3mm are already successfully processed on LiSEC plants.
Needless to say that the high technical standards of the KBU plants are also reflected in the machined end product, the excellent quality of the polish – irrespective of the shape of the glass sheet – is still setting standards in the industry.
With the integration of a drilling and milling station, the KBF, LiSEC provides a general-purpose tool for almost all applications and glass sizes. The production of bores as well as inside, edge and corner cutouts complete the processing of the glass sheet in only one clamping operation.
In doing so, LiSEC is the only manufacturer who banks on only one processing spindle. This guarantees the customers a simple and stable system with minimal downtimes.
The second processing spindle is replaced by an elaborate software and process control; this way it is in many cases even possible to realize the lowering on the back side of the sheet.
In the last few months, the team processing has intensively and consistently worked on the increase of quality, cycle times and the expansion of functions of those types of machines which allowed a drastic reduction of the life cycle costs.
As a result, LiSEC customers will produce throughout the entire machine service life in a considerably more cost-effective way than with comparable plants. And the success proves us right – we expect that we will deliver the 400th processing machine until the end of the year.
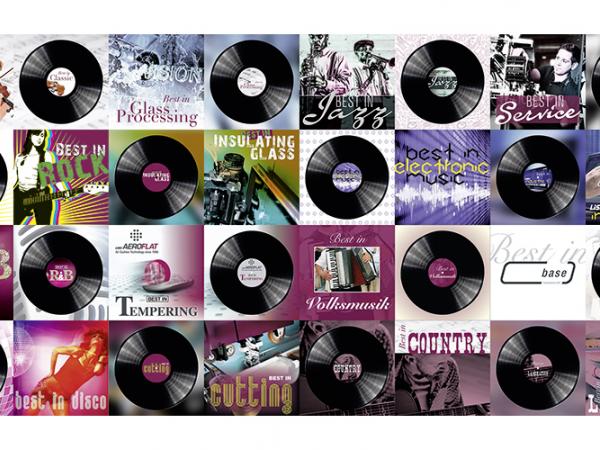

Add new comment