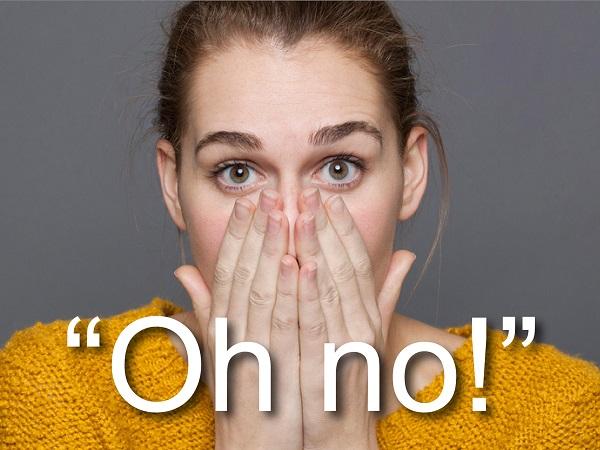
Date: 20 March 2019
Four thousand units had to be scrapped because a customer service representative entered one dimension incorrectly by an eighth of an inch.
That’s on the CSR, right? Not your fault if it happened in your operation?
Actually, chances are you could have reduced or removed the possibility of such an error with procedures or systems put in place before it happened.
No matter how you look at it, it is certainly your issue. Because it’s your plant and you don’t want it to happen again.
What goes wrong that you can control?
- You routinely blame and fire employees for errors, increasing stress and eroding trust. This can lead workers to keep to themselves observations about systematic production, quality and safety issues.
- You expect perfection rather than planning for the inevitable human errors.
- Your procedures or systems allow un-manufacturable configurations or dimensions to be entered.
- You rely on the customer to confirm proper data entry, but when it’s wrong, you fix it to protect a valuable relationship.
- It’s happened before and you haven’t implemented systematic solutions.
- If you’re the owner or boss, of course, you’re ultimately responsible.
Speaking of responsibility … that CSR was me. The order was 16,000 units. Fortunately, someone noticed a quarter of the way through.
Can you prevent every error?
You might be saying to yourself that it’s unreasonable to anticipate every possible error— that the cost of any solution must be weighed against the cost of business as usual.
And you would be right.
But in any manufacturing environment—particularly one where each item or job is unique and made-to-order—your order entry process should have systematic methods to reduce errors.
In my eighth-of-an-inch-nightmare, the immediate solution was for me to go back a few hours later to each order to double check inputs. We also added a requirement that orders over a certain value were always checked by another person.
Common sense, right? Apparently not enough to have been implemented before.
Long-term, we removed manual data entry altogether. I implemented customer / dealer portal and EDI solutions.
A side benefit? Customers who enter orders themselves do not usually call and ask you to fix their mistake for free. Instead, they often ask for a rush remake and are willing to pay a premium to get it.
ORDER ENTRY ERROR SOLUTIONS
Each manufacturer is different and the solutions will vary. But the following steps can help reduce errors in your shop:
Solutions for smaller MTO manufacturers
- If there is one data entry person – After they enter orders, have them take a break and then check the entries. Add controls when an order is over a certain TAV: perhaps someone else in the office double checks. You can use the production manager for this because they don’t want it made wrong the first time either.
- If there is a data entry team – Enter orders and queue them to be double checked by another resource. Depending on the volume, implementing a double-entry system where two different CSRs enter the same order and a utility checks for changes will make this practically fail-proof.
- In any situation where your staff enters or re-enters data, insist on comparing the inputs with the original request.
Solutions for larger MTO manufacturers or more sophisticated clients
- Customer portal – Have the customer enter the orders. Add controls that prevent the customer from entering something that cannot be manufactured or warrantied. Create a reference guide to ensure the right information is entered. If they resist, evaluate how easy the entry tool is to use. You can also offer a discount on orders entered in the portal. Additional training also can help.
- EDI import –Transfer the order information from their system. If the customer has an ERP system, they must create a PO for orders. EDI eliminates the need for them to enter an order in their system and yours. With EDI, their PO is output from their system into your system.
Solutions for ETO manufacturers
- Require multiple engineers to sign off on the design and any change requests before sending to the customer.
- Ensure drawings and BOMs are saved at the job level. Reuse of global instructions causes issues if not incorporated into an ERP.
- Integrate the ERP with the design tools.
- Choose an ERP with the design tools included.
The bottom line? Expect errors. Create systems to reduce them.
By the way, 22-year-old me didn’t get fired. I thought of how to fix it, which I took to the president. And I got really interested in manufacturing systems and error reduction!
FeneTech, Inc.’s Q2S Director Ryan Anderson has spent 10 years working with manufacturers to get the most out of their ERP investment. Prior to working with FeneTech, Ryan served for two years as the ERP specialist at a startup. As both a user and an advocate for the customer, Ryan has spent years facilitating the transition from ERP implementation to ERP maintenance all while building long-term partnerships. To recognize her dedication to customer support, in 2016 Ryan was nicknamed ‘The Customer Whisperer’ in a trade publication article recognizing outstanding women in manufacturing. Ryan received her undergraduate degree in mathematics from Bowling Green State University and her MBA from Kent State University. Since 1996, FeneTech, Inc. has been working exclusively with manufacturers to provide flexible solutions, best practices, and 24/7 support. Q2S ERP is developed and supported through their Aurora, Ohio and Luxembourg offices.
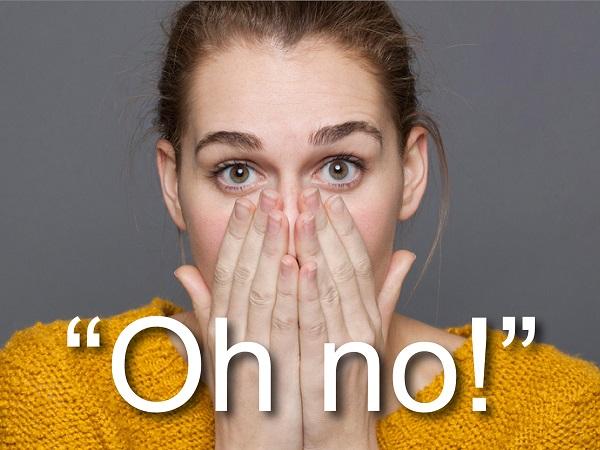

Add new comment