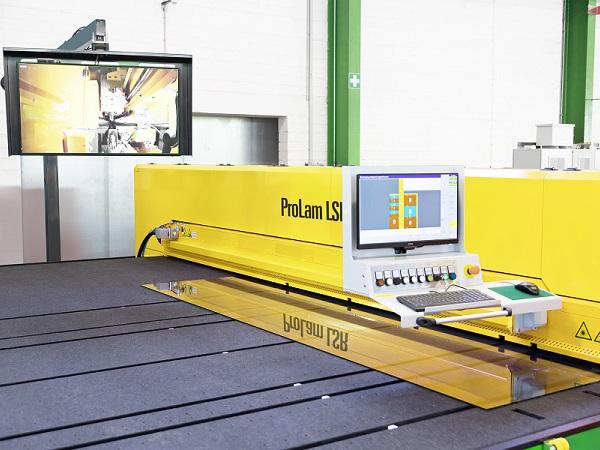
Date: 2 August 2021
The HEGLA Group’s range of topics at Vitrum could scarcely be wider, but it is an example of just how diversely the glass industry has developed in recent years. On the one hand, the focus is on glass cutting, its automation and performance increase. Interested visitors gain insight into HEGLA’s mechanical engineering. On the other hand, the opportunities of networking, digitalisation and integrated processes will also be showcased, making it clear how important these issues currently are from the Group’s point of view.
Laser diode heating increases productivity in LSG cutting
HEGLA is showing the ProLam LSR, a newly developed cutting system for laminated safety glass equipped for the first time with the time-saving laser diode heating system as a machine in series production. “Productivity in LSG cutting can be increased by twenty per cent or more with the new heating process,” said HEGLA Managing Director Bernhard Hötger, emphasising one of the advantages of the new technology. The laser applies the bundled heating energy precisely to the cutting contour, reaching the PVB inerlayer’s transformation temperature much more quickly than the usual heating tubes.
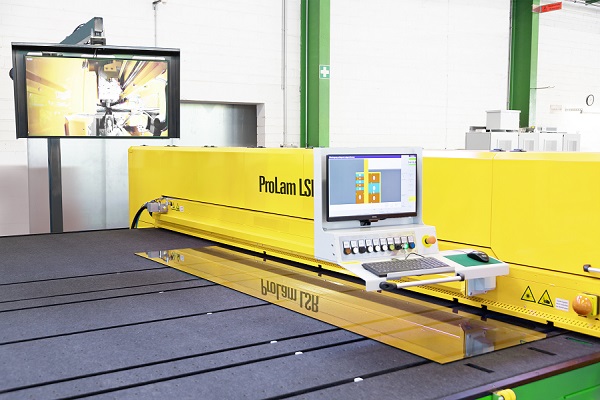
The laser beam weakens only slightly as it passes through the interlayer, so that even demanding glass laminates of up to ten-ply interlayer can be separated with shorter processing times. The new process also has a positive effect on edge quality: the interlayer remains cold outside the cutting area, thus preventing later delamination and enabling additional cuts without cooling times. The system reduces energy costs as well. “The laser diode strip has a divided design, automatically adjusts to the cutting length, and requires only a short boot-up time,” Bernhard Hötger added.
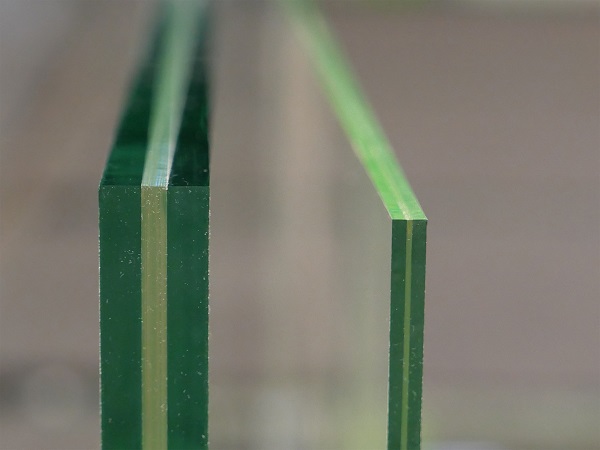
Unique glass marking for digital added value
Individual glass marking, data capture and storage, and product tracking are the main focus at HEGLA boraident. In line with this, the mobile laser printing solution ESGuardM will be shown together with the UniColor laser printing process. Compared to CO2 laser marking, this technology leaves the surface completely undamaged. Once the scratch-, smudge- and weather-resistant marking consisting of a logo, QR code or alphanumeric characters has been applied, it remains firmly attached to the glass.
“Depending on the integration, the captured data on the product can be stored either in the ERP or another system. All it takes is one scan to retrieve the information, call up a fire protection certificate or reorder an identical product,” explained Head of Development Dr Thomas Rainer. As a rule, laser marking is integrated into operations step by step with the aims of triggering production steps through automatic scanning, simplifying shipping processes or tracing process steps from production and shipping to the construction site. “With marking and unique identification, it's also possible to fully digitise and track production,” said Dr Rainer.
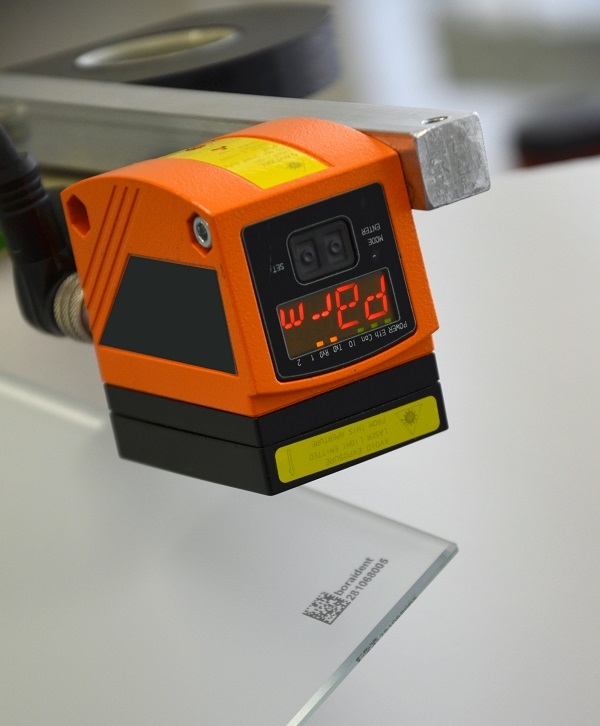
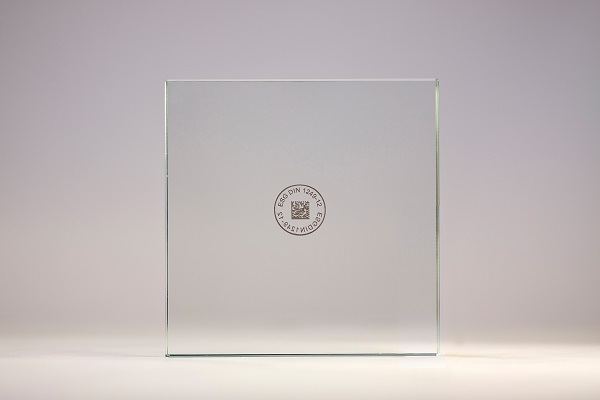
Real-time tracking for the optimisation of integrated processes
“Capturing processes in real time is also advantageous for higher-level software such as ERP, MES, waste optimisation and capacity planning,” said Dr Jan Schäpers, Managing Director of HEGLA-HANIC, the software specialists. The large amount of data collected by scanning and sensor technology can be used to analyse and optimise processes in depth.
The display of information in a HEGLA-HANIC Cockpit helps to improve the employees’ overview and gives production managers an improved basis for decision-making. With appropriate integration into ERP and production planning software, many of these interventions take place automatically. For example, the continuous optimisation system continuously adjusts the cutting plans or rearranges the sequence of units at the processing steps according to current demand.
For visitors who want to get a personal impression of HEGLA-HANIC’s solutions on site, the company will show demo views and test systems at Vitrum – systems featuring even better performance and usability on a new platform with inclusive updates.
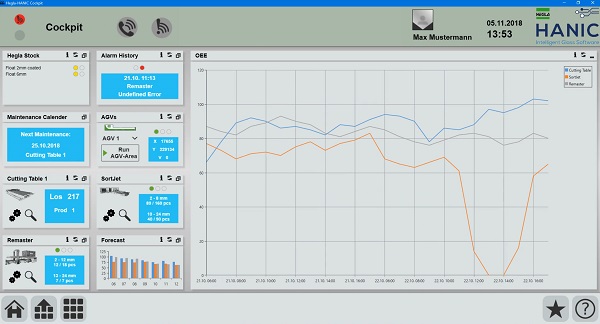
Perfect flatness and glass quality
Tempered glass in perfect optical quality and flatness is the passion of HEGLA-TaiFin, the HEGLA Group subsidiary that will also be represented at the joint stand. With the CTFe, the company offers a unique tempering furnace in which the thermal heat is transferred by air circulation from closed convection boxes. The glass surface is never exposed to the direct radiation of the radiant heaters, so that both coated and uncoated glass can be finished with the highest optical properties.
“The Viprotron and LiteSentry scanners, for example, consistently confirm the premium quality of the tempered glass with isotropy values above 95 per cent,” said Jarno Nieminen from HEGLA-TaiFin. While the CTFe is ideally suited for demanding facade glazing, the Finnish company is now introducing three new furnaces that have been specially designed to meet the requirements of insulating, interior or sanitary glass.
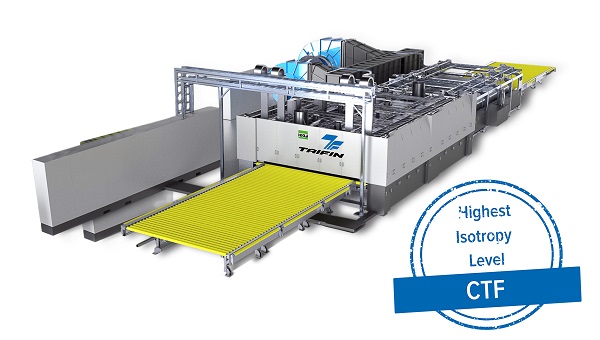
You will find the HEGLA Group at Milan's Vitrum in hall 22P at stand U01-Z08.
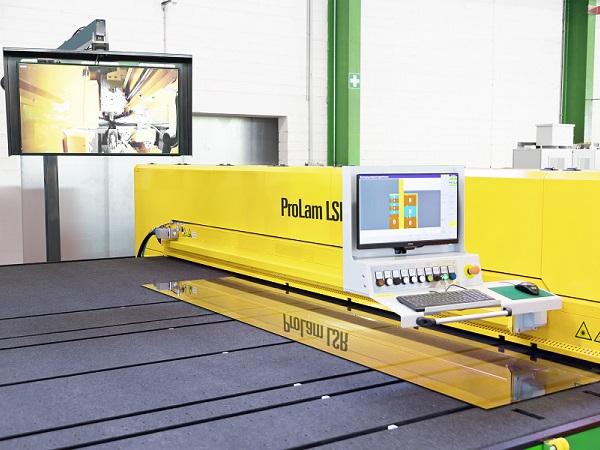

Add new comment