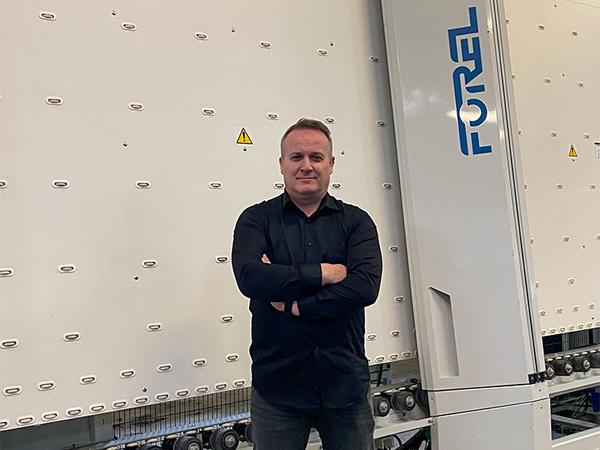
Date: 11 February 2021
One of the most remarkable and growing companies in Polish glass business, Glasskon has been established in the eighties, focusing on glass processing and mainly on the production of insulating glass units. Nowadays, Glasskon owns two productive plants in Palubice (the first one) and in Grodzisk Mazowiecki (inaugurated two years ago), employing approximately 200 people and offering the glass market a remarkable quality products for both residential and commercial segment.
To increase their productivity and to give their customer an ever better product, in 2019 Glasskon has installed two special-focused insulating glass lines by Forel. The first one is called Residential IG Line, and is dedicated to the production of double and triple glazing units up to 2.500 mm x 4.000 mm, ensuring a perfect result and an high productivity for the most common residential market requests.
The second one is an High Tech Jumbo IG Line, and represents the top of the range of Forel for insulating glass manufacturing: this machinery has been designed to successfully manage many kinds of requests, offering the highest possible flexibility. It is a complete solution, developed for glazieries which need to be competitive on different requests of IG units.
The line in use by Glasskon, thanks to its choice of options and features, caters comprehensively to a wide range of needs about sizes (up to Jumbo size, with load capacity of 400 kg/linear meter), spacers (it can process conventional rigid spacer or, with the addition of a specific applicator, flexible spacer, standard or t-shaped), curvatures control (it can handle panes that are not completely planar), offsets (up to 100 mm on front and lower sides, up to 300 mm on rear and upper sides) and chambers (up to 3, quadruple glazing).
We ask Mr. Wojciech Gwadera, Managing Director of Glasskon, to tell us about his company organization, its goals and future projects.
Mr. Gwadera, what is GLASSKON today? Which are its main productions?
Glasskon is currently composed of two production plants. The main activity of the plants is flat glass processing for the broadly understood construction industry.
The first plant located in Palubice, in its present shape, was launched eight years ago and provides customers with IG units and tempered glass.
In 2019 we started manufacturing in our new branch in Grodzisk Mazowiecki. We decided it was time to expand and apply innovative technological and process solutions.
Glasskon Palubice focuses largely on providing services to companies producing PVC joinery. On the other hand, the plant in Grodzisk Mazowiecki, which is capable of processing Jumbo size glass (3210 x 6000 mm), mainly serves investment customers and aluminum joinery manufacturers. We are also gradually building a network of foreign consegnees and customers.
Glasskon is a team of about 200 people who take care of delivering the highest quality insulated glass, structural glazing, tempered glass, and soon also ESG / VSG glass, to a wide range of customers, both in the B2B and B2C sectors.
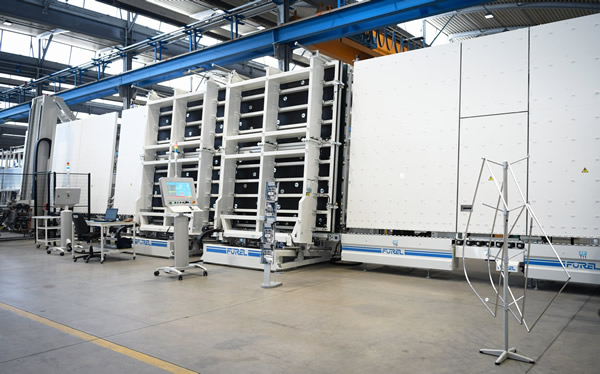
Two years ago, you invested in a new plant in Warsaw area. What is the target of this new site and how do you plan to reach it?
The investment in Grodzisk Mazowiecki was a natural consequence of the company's development and production growth.
Our goal is to provide our customers with comprehensive services in the field of building glass and interior glazing supplies in order to fill the market niche.
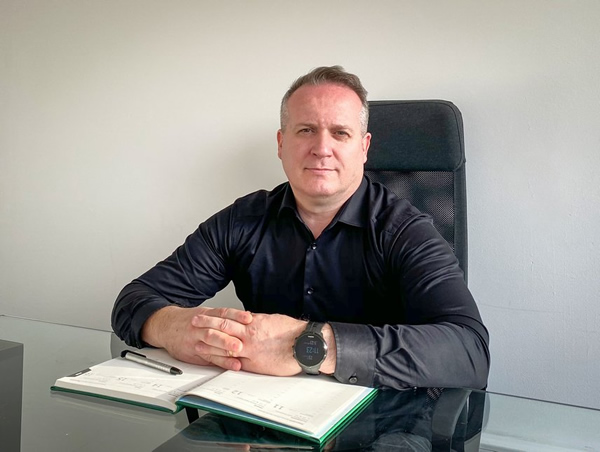
The Polish market is currently dominated by large, I would even say corporate companies, compared to them, small producers have so far been an inadequate alternative. Glasskon builds a brand that fills the market gap, allowing customers to implement ambitious assumptions in an atmosphere of partnership and good cooperation.
Glasskon Grodzisk Mazowiecki goes beyond standard IG units and tempered glass. The investment in modern equipment for processing large-size glass included advanced lines for edge processing, a laminating line and an autoclave.
The chosen strategy allows us to process complex production orders in non-standard dimensions. The entire machinery park has been designed in such a way as to give us the possibility of cutting, processing, tempering, laminating and coupling jumbo size glass.
Therefore, it is one of the few, comprehensively equipped production plants in Poland, with a very flexible production organization, in which the size and type of glass used is not a major limitation.
An additional advantage, from the point of view of logistics, is the location of the plant, which allows for efficient and timely delivery of our products pretty anywhere in Poland.
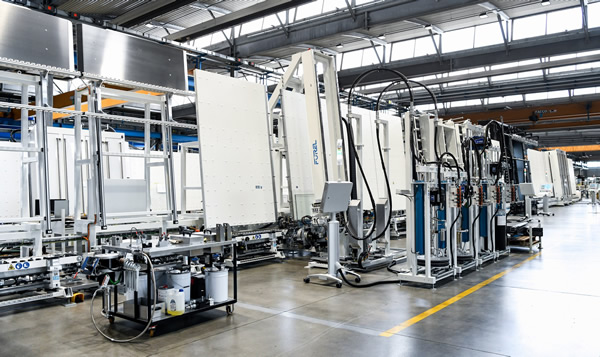
You installed two new IG lines by Forel: a “Residential” line able to process IG units up to 4.000 x 2.500 mm, and “High Tech” line, to also assembled Jumbo size units. Currently you can manage many different requirements and orders, offering also the biggest size now available in Poland for IG. Also, we know you made investment in human resources, hiring people with strong skills and experience in glass processing. How is this strategy working?
As I have already emphasized, for both Glasskon aim at delivering comprehensive customer service and the highest quality product, adequate to the market expectations.
Glasskon Pałubice and Glasskon Grodzisk Mazowiecki cooperate, complementing each other and offering our customers tailored solutions.
The implementation of the new investment in the assumed dimension allowed us to expand the range of solutions we have offered so far, in consequence giving us greater production flexibility and freedom of action. Such a strategy translated directly into an increase in the client portfolio.
Today, we successfully implement projects that cover the full range of building glazing, both standard and structural.
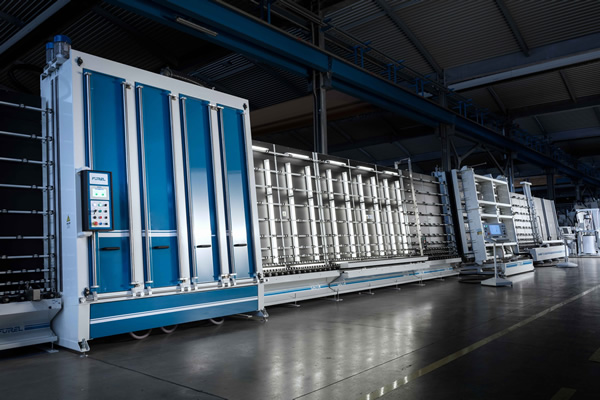
What do you think about your investment in Forel machinery?
Being equipped with high quality IG lines like Forel’s was crucial in terms of optimizing the course of the production process. The choice of two dimensional options, the possibility of using two types of sealant or the function of automatic processing of stepped glass, facilitate production planning and allow us to take up new challenges, especially in the context of Jumbo size and structural glazing.
You are clearly increasing your competitiveness in the market: which are your future plans?
Our plans are the consequence of internal development and an efficient response to the evolving market demand. They include continuous improvement, care for high quality products and satisfaction of our customers.
Covid-19 emergency is changing many aspects of our lifes, and also of our business. In your opinion, how will Polish market evolve in the future?
The dynamic changes we have recently experienced prove that even the most carefully made plans can be simply turned upside down.
At the moment, we do not feel a significant slowdown in the sector, we hope that the situation will also stabilize in the industries that suffered the most due to COVID-19.
As a company that has focused on the diversification of production and on a significant expansion of our existing capabilities, I would say we look forward to the future with a dose of reasonable caution, yet hopefully.
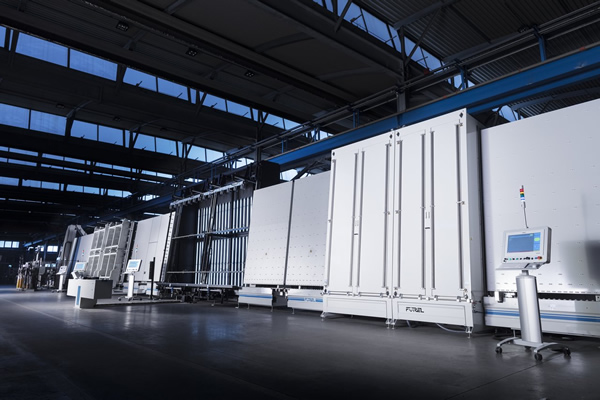
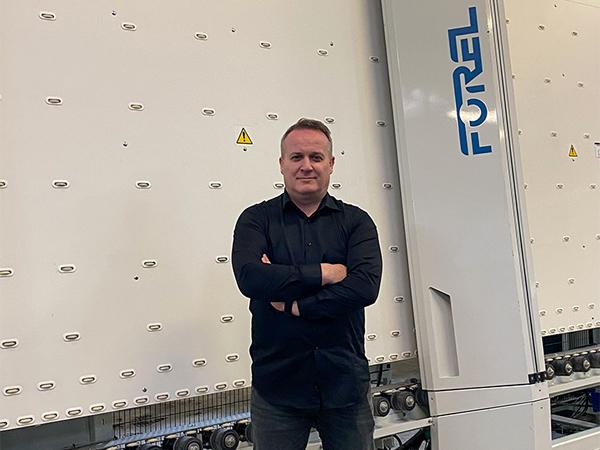

Add new comment