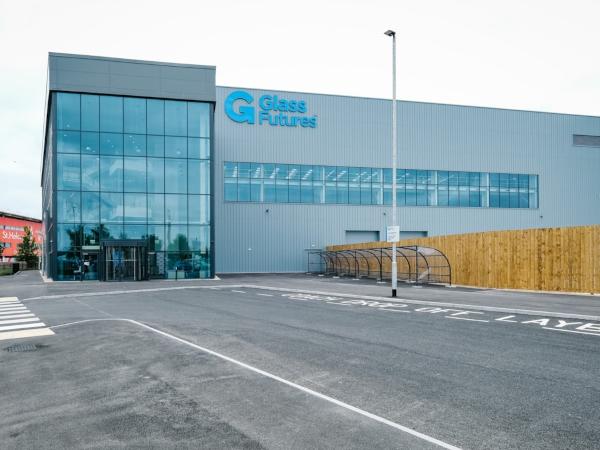
Date: 2 May 2024
- The £54 million facility will develop and test advanced glass-melting methods, supporting future innovation in the industry around the world
- The experimental R&D, innovation and training centre will be run entirely by Siemens’ software platform, PCS Neo
- The technology’s cloud-based, zero-install user experience will support efforts to reduce carbon emissions from glass manufacturing
An experimental glass-making facility in St Helens, Merseyside is set to pave the way for significant emission reductions in glass manufacturing with support from Siemens technology.
The £54 million R&D project – funded by a combination of government support and its membership businesses – will model and develop an optimised approach for ‘boosting’ glass furnaces with electrical heating. Industry body British Glass estimates this approach will cut UK emissions from glass manufacturing by 56 per cent.
The site, which will have capacity to produce 30 tonnes of glass per day when fully operational in late 2024, is the first facility to adopt Siemens’ newest digital control system, PCS Neo, to unify and manage all its plant operations.
The technology will manage all processes across the site and provide end-to-end monitoring and control, which Glass Futures will be able to modify and build on as the facility is developed.
George Myers, control systems engineer at Glass Futures said: “Decarbonising the manufacturing process is vital with global demand for glass set to keep rising in the years ahead.
“Using electric boosting and hydrogen to melt glass provides us with a route to achieve that, and our ambition at St Helens is to model and develop a solution that large-scale manufacturers can adopt or learn from, paving the way for more efficient furnaces around the world.
“Our partnership with Siemens will provide the technology to make this possible. People working from anywhere in the world will be able to monitor the entire facility from one unified communications pathway, which will generate new insights and enable people across the world to learn about the project and process.”
Stephen Haigh, head of glass industry UK & Ireland at Siemens, said: “This revolutionary project will leverage the power of cross-industry collaboration and the potential of new digital technologies to deliver much needed, significant emission cuts across glass manufacturing.
“PCS Neo represents the culmination of three decades of development and real-world testing. By reducing the complexity of data collection and analytics at the site, and by simplifying operations at this test stage and subsequently in full-scale glass plants, PCS Neo will play a vital role in unlocking the ambition at the heart of this project.
“Importantly, it will provide Glass Futures – other future projects across the world - with flexibility when it comes to deploying their people, independent of role or location, and enabling global engagement and learning.”
Glass Futures is a global not-for-profit research and technology, membership organisation that connects the glass industry with academia to use technologies that will make glass making more sustainable. Its member businesses include the world’s leading glass manufacturers, along with Siemens and other industry partners.
Siemens will be showcasing more about digitalisation of industry at its Transform event on 17 and 18 July. To register to attend the free event visit here: https://www.siemens.com/uk/en/company/transform.html
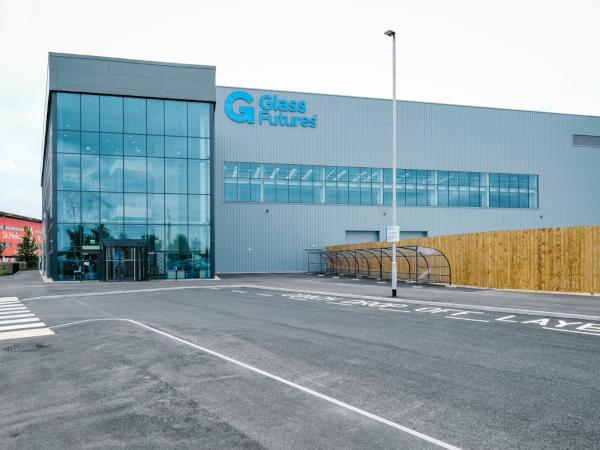

Add new comment