This paper was first presented at GPD 2019 by Carlos Machado e Moura and Pedro Borges de Araújo.
Today’s architectural demands, dictated by the aim for transparency and spatial continuity between inside and outside, always push for better performances — more efficient and dynamic systems — and ever-larger full-height sizes — with oversize glass panes often above the Jumbo dimension.
Large windowpane dimensions impose new technical challenges, requiring prior meticulous calculation and compelling each element to be re-engineered, and sometimes obliging appropriate machinery to be built for their installation. This paper focuses on this challenge, with ever-increasing precision in manufacturing and assembly to ensure glass panels to be operated with lightness and provide ease of maintenance, despite their size and weight.
Taking a 2015 UK-based residential project as a case study, this paper illustrates the challenges in terms of planning, engineering, supply and assembly of motorized 26 m² double glass sliding panes 8m-high, weighing 3 tons each.
Despite the exceptional character of these limit situations, the problems raised by operating with massive elements are fundamental to raise awareness about aspects that are not so evident at a smaller scale or standard solutions, ultimately leading to improving products. Indeed, this customized solution formed the prototype for a new sliding door series, combining large glass sizes with strict thermal performance requirements, designed according to Minergie-P and Passivhaus standards.
1. Introduction
So-called “minimalist windows” have known a remarkable success over the last two decades, taking advantage of the potential of structural glass to provide large sliding glass doors and windows with ultra-thin frames. The decision to use tempered glass — calculating its mechanical strength to play the role of the main component — and reduce aluminium profiles to mere finishing components, allowed the enlargement of glass surfaces, in tune with architectural demands, dictated by the aim for transparency and spatial continuity between inside and outside.
Over the last years, performance has been a significant driver in this field — continually pushing for higher efficiency and more dynamic systems — but also has size, with extra-large glass panes for full height doors and windows being required by architects for many residential projects, often with oversized windowpanes above Jumbo size. Large glass dimensions impose new technical challenges to ensure the panels can be operated with lightness and provide ease of maintenance, despite their size and weight. Their installation requires a prior meticulous calculation and, sometimes, the construction of appropriate machinery.
This paper’s case study, an UK-based residential project, allows focusing on this qualitative leap, with increasing precision in manufacturing and assembly and the challenges in terms of the design of motorised 26 m² 8 m-high double glazing sliding panes, each weighing 3 tons. [figure 1]
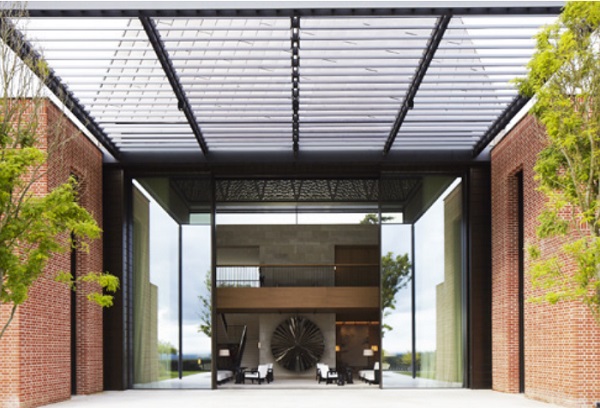
By analysing the steps of preparation, supply and installation of this project, the article stresses the fact a considerable enlargement in size implies a full reengineering process, culminating in a different product with entirely altered components. However, despite their exceptional character, these experimental works are fundamental to test the limits of materials and to introduce a change of scale, compelling a vision that sometimes reveals possible improvements which are not evident in standard or smaller projects.
This ability is perhaps their more relevant aspect, the way these projects contribute to improve the product and to create new opportunities and future uses. Indeed, this customised solution became the prototype for a new panoramah!® series, combining large dimensions with performance, specifically designed to respond to strict thermal requirements, meeting Minergie-P standards.
2. Extra-large sliding doors and windows
panoramah!® had been developing extra-large window dimensions in aluminium sliding doors and windows over the years. Jumbo size glass panes, six-metre-high up to a surface of 19 m², were used in several projects in India, namely the single glazed doors of a house in Juhu Beach (Mumbai), the most massive sliding windows ever built back in 2011 [figure 2]. One year later, also in India, a 7.2 m-high double-glazing was installed in another house in central Mumbai [figure 3].
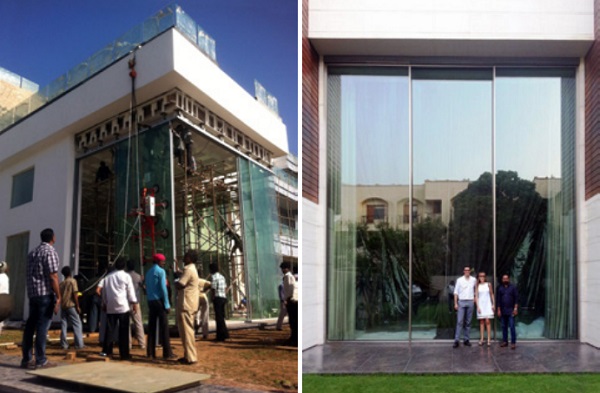
The IGUs used on these projects fitted a series with 38 mm thick profiles. However, accommodating larger double-glazing dimensions or triple glazing required thicker profiles since the 38 mm thickness of the glass is limited to a maximum surface area of 7 m² with triple glass units. The 38 mm series was therefore adapted to 54 mm in 2012, mostly by the introduction of polyamide elements in its profiles [1]. [figure 4] Projects with larger glass dimensions have used this series since then, reaching the size of 3 x 5.50 m triple-glazed panes, as installed in a villa in Switzerland [2].
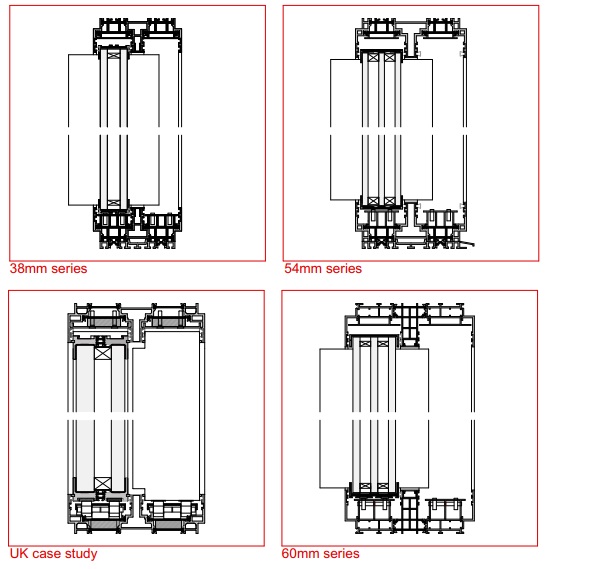
However, a 2015 project for an environmentally friendly mansion designed by Pringle Richards Sharratt Architects in the Surrey Hills, to the south west of London, more specifically in a park in the Area of Outstanding Natural Beauty, challenged this limit and revealed to be an extraordinarily challenging and productive job [figure 5]. In the new house, two imposing courts act as giant lungs for the building moderating the environment in the environmentally closely controlled spaces arranged around them.
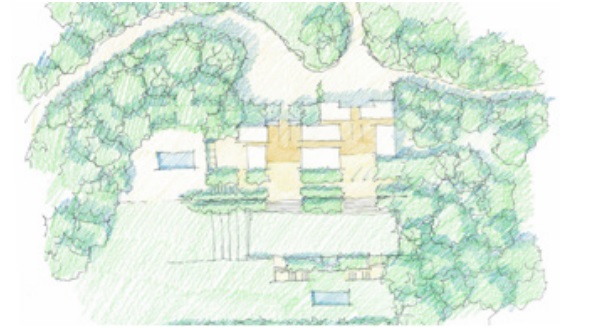
The courts serve as both solar collectors in winter and repositories of cool night air in summer; from these spaces air, naturally tempered by a labyrinth of ducts in the ground below the house, is circulated through the living and sleeping accommodation. The structure of the house is clad in locally sourced brickwork, the large roofs have a glulam structure and are clad in a bronze roofing system with integral solar thermal water heating system [figure 6].
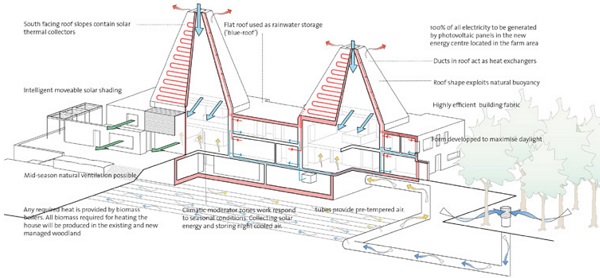
Accordingly to Passivhaus standards, the house is designed to achieve Code for Sustainable Homes Code 6. These two courts around which the house is organised are introduced to the site in a manner that responds to the mature designed landscape and gardens and exploiting the rich topography and generating a wealth of external spaces and relationships between inside and outside [figure 7].
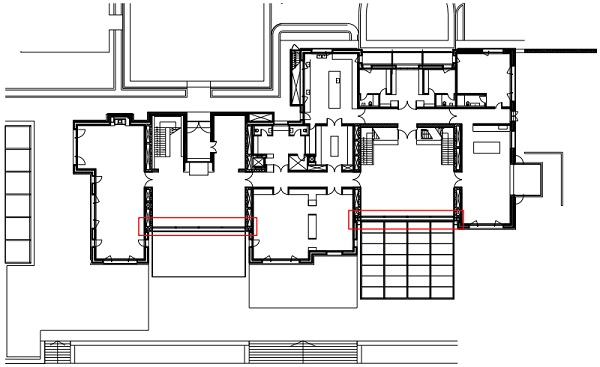
From the beginning the client wished the internal and external elements to blend and to bring the landscape into the house. The large openings and large uninterrupted panes of glass were essential in delivering this and the option for large openings to the courtyard south facing elevation was explored from very early on, the challenge was identifying a specialist company that would be able to deliver the ambitious requirement [figure 8].
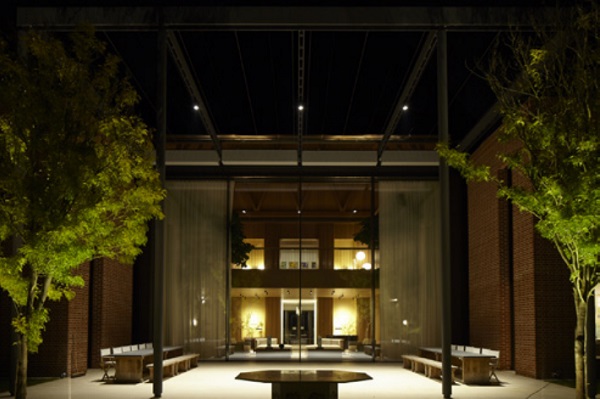
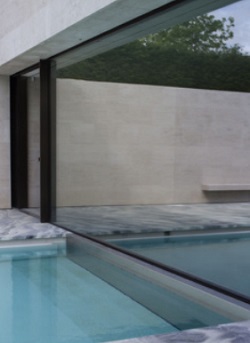
Indeed, with two full-height glass doors with four double-glazing panes measuring 3.10 x 8.30 m and weighing almost 3 tons each, this project compelled panoramah!® to rethink a series of processes and procedures.
Several other sliding doors and windows were installed in the house, one of which with an even larger surface of glass — 8.30 x 3.30 m, yet horizontal — sliding over the pool with a sill which functions as a vertical lift submerged gate between the interior and exterior pool areas [figure 9].
Despite these technical peculiarities, the full height 8 m sliding doors remain the most impressive and sophisticated feature of this work and the ones that paved the way for the engineering of a new series for installing large glass dimensions.
3. Planning and Engineering
The composition of the DGU was carefully engineered to meet the needs for structural resistance. In particular, given the minimum dimensions of the door and window frames, covering the glass for only a few millimetres, excessive deformation could allow the glazing to come out of the frame under high pressures. Therefore, these large glass plates had to offer a maximum deflection of 36.5 mm for service wind loads around 1,050 Pa, which corresponds to 1/226 of the maximum glass dimension.
All glazing was tempered for more resistance and safety in case of failure. Furthermore, the glass had to be solar control coated to respond to thermal efficiency performance and extraclear for aesthetic requirements. Therefore, the composition was determined as follows: DGU 19 mm tempered lowE coating + cavity 24mm with argon and a warm edge profile + 1212.4 tempered laminated.
The first challenge regarded the sourcing of the oversize insulated glass units. Back in 2015, several companies were able to manufacture monolithic tempered glass that large but not double-glazing units, extra clear glass, or adequately coated. Those requirements likely reduced the array to a single manufacturer, which formulated an offer for the job but was unable to specify a delay for delivery, as it depended too many variables and other manufacturers’ production.
The company hired a specialised third-party consultant in Dubai to look for alternatives, who came up with three manufacturers. Despite the interest of those companies in performing the job, and complying with the technical requirements, only one was able to engage with a specific cost and delay. The company, based in China, was awarded and the glass units were manufactured in 3 months, as planned and according to the technical specifications, including a perfect flatness [3].
Also, although it was not strictly necessary, the glass was Heat Soak Tested (HST), as a complement of the tempering process, to eliminate glass carrying the risk of spontaneous breakage due to non-dissolved nickel sulphide inclusions. Despite this precaution — as mentioned afterwards — one of the glass panes broke after installation given the presence of a rare chemical element not yet covered by norms.
To reduce the risks associated with shipping, packing and handling these oversize units, the U-channels structural bonding to the glass was done in the glass manufacturer factory by Portuguese panoramah!® teams, which travelled to China and had the support of an interpreter. Overseas freight transport was afterwards organised directly from China to the UK, requiring special transport operations both by sea and ground, with on-deck shipping and specialised trailers.
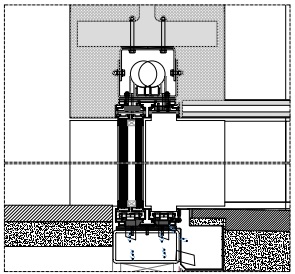
The second step of development regarded the engineering and manufacture of the aluminium elements of the frame, and the reinforcement of a series of components.
Although initially, it seemed a task of adapting a sliding door structure to a larger dimension, in the end, no element of the original window remained in this specific solution [figure 10].
8 m long profiles are complicated to produce as 6.5 m sets a pattern size for aluminium extrusions, possibly according to transport dimensions [4].
Indeed, in this case-study, special extrusions with stainless steel reinforcements, aluminium tempering and anodising had to be performed in three factories, located in different places of Spain. Elements this size are often used in the aeronautical industry, but seldom in the construction sector, and generally with aluminium leagues which are not anodisable.
Therefore the treatment companies that regularly collaborate with panoramah!® were unable to provide both a tempering furnace and an anodising tank large enough for these profiles. They were bronze anodised, with some elements powder coated with a similar RAL, and their final transformation was done afterwards in Portugal.
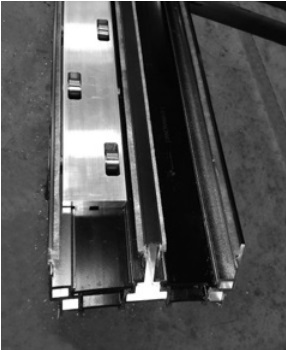
The frame’s aluminium profiles were enlarged with polyamide elements — as previously done in the 54 mm series —, to accommodate the thickness of the DGU.
However, the previous experience had revealed that the impact of heavy glass during installation shattered the polyamide bridge on the sill.
Therefore, although it compromised thermal break, the sill incorporated a stainless steel element beneath the polyamide bridge to protect it, since the first stages of development.
However, polyamide was still damaged after testing, rendering inevitable a solution with a solid stainless steel profile and a different polyamide bridge, to minimise its thermal conductivity [figure 11].
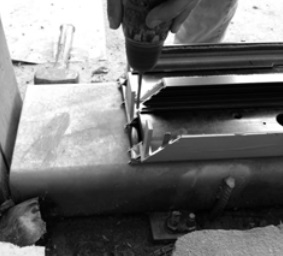
To ensure the perfect planarity of the sill — determinant to achieve light operability of the sliding panes — a preframe was installed underneath the structure with a thick metal tubular profile. Given the weight of the unit, aluminium shims replaced the standard PVC ones, with a reduced distance between them (20 cm instead of regular 30 cm). Furthermore, the sill was mechanically anchored to the underneath preframe to ensure safety [figure 12].
Generally, minimalist systems avoid this solution as screwing inferior elements might compromise waterproofing. Therefore a different system was developed and adopted, using the tubular preframe as a watercolumn and implementing separated water channels to minimise risks and provide more efficient drainage. Additionally, customised mullion and pull-handle covers were adapted to eliminate any possibilities of water penetration through handles and glass lids.
Vertically, stainless steel components (228 mm long 8 mm thick) reinforced central mullions internally to sustain the glazing weight and resist wind loads. These were also adapted to create a more significant gap, ensuring no friction on the adjacent glass panel when sliding, if it is subject to a considerable deflection, something likely to occur in large glass panes.
Roller bearings had to be carefully chosen and combined to operate such massive glasses, increasing to the triple of their standard dimension, as the first attempts — with ball bearings, plain bearings, needle roller bearings, cylindrical roller bearings, etc. — broke due to the weight. Also, the motors were upgraded to more performant ones.
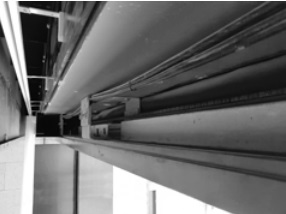
Indeed, the significant distance between the roller bearings in the sill, and the engine on the top created a considerable momentum at the start movement, impeding soft progress and forcing the structure of the building. Only a more powerful motor equipped with chains instead of ordinary belts and a carefully determined number of fixations of the engine to the door were able to respond to this question [figure 13].
These and many other decisions emerged from tests performed in a metal factory mockup with the same geometry and weight of the sashes, which ran the motor for a series of 15,000 test cycles [figure 14]. The last change regarded the location of the safety sensors, which were placed laterally, instead of the standard bottom and top position since the vertical distance could compromise their effectiveness.
4. Installation
The installation process proved to be a challenge as complex as the preparation. Besides the calculations required to determine the safer way to carry the structure to the building site through existing road infrastructure, with a route involving narrow roads and sharp bends, several accesses had to be specially adapted for this transportation. A bridge was reinforced, and the paths which led to the site were covered with thick metal plates as the trucks weighted more than the road could sustain.
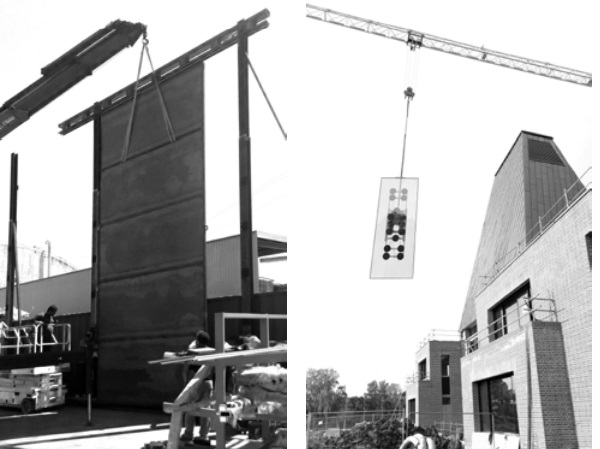
Additionally, the soil composition of the garden dictated the position of the crane by the rear façade, opposite to the operations [figure 15].
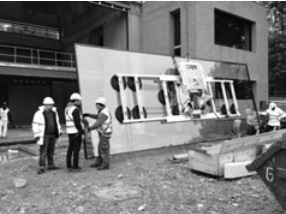
Only two companies were able to provide glass lifters robust enough for moving each 3-ton glazing panel. Furthermore, their machinery had to be adapted with 16 suction cups to lift and move elements of this dimension [figure 16].
The factory mockup allowed previous training of the team and the determination of the most efficient way of installation. However, especially given the fact that the process took place in October in the UK, atmospheric conditions and daylight had to be taken into account as well.
Operations could not take place under rain or wind, each sash installation took over 1h30 and each crate contained two panels. Therefore, the decision to assemble each panel had to be well pondered, guaranteeing the conditions were met for two installations. The eight sashes were finally installed after two and a half days of work. [figures 17, 18, 19, 20, 21, 22]
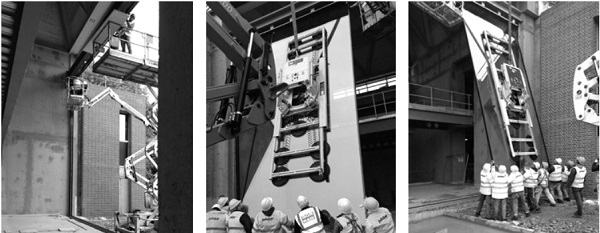
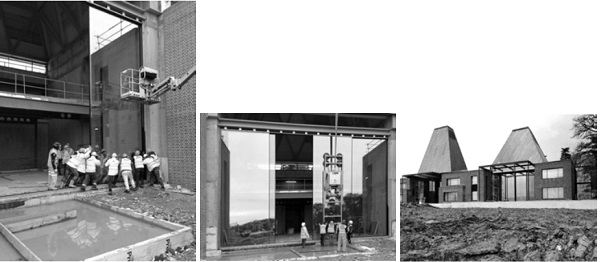
5. Risks involved
Whereas in the case of traditional windows, component sourcing and assembly can generally be confined to a relatively reduced geographic area — extrusions, glass manufacture and aluminium treatments can be assured by local suppliers — with oversize windows the opposite occurs. These involve a unique work and a very disperse supply chain, with several components manufactured by a single or very particular companies, resulting in a much more complicated process involving risks which are extremely difficult to calculate.
In this case study, the installation of glass doors near London was commissioned to a Portuguese company, involving special aluminium extrusions and anodizing in Spain, transformation in Portugal, glass manufacturing in China via a Dubai consultant, U-bonding in China by Portuguese teams, specialized transportation to the UK, reinforcements in the accesses to the building site, adaptation of installation machinery, etc.
This complex supply chain, with all the details regarding predictable and unpredictable aspects, renders this project’s risk very high. Indeed, despite all the precautions with risk identification and mitigation, several issues are still not foreseeable. An excellent example of hidden risks is the HST test performed to dismiss the dangers of spontaneous breakage after installation. Orientating numbers for breakage rate in a typical HST are around 1%. However, this number is determined with reduced glass surfaces whereas in large glass panes like this case study’s the probability of critical inclusions is by far superior.
Furthermore, the average considers glass from many different furnaces, while in this case all panes are manufactured in the same furnace, whereas an unfortunate combination of factors might render nearly all glass production defective. Despite all the precautions with choosing the most technologically reliable solution and performing HST testing, one of the glass panes broke after installation and had to be replaced. Analyses later confirmed that no nickel sulphide inclusions were present in the broken glass, but revealed an extremely rare chemical element that has not yet been studied and therefore no norm presently covers this phenomenon.
Given their exceptionally high risk, these works require very high prices, incomparable with the range of any other standard product. In 2015, this project corresponded to state of the art, with the best glass and components available and a client that was willing to take the risk and to pay for having this unique solution at home.
6. Lessons learned, new opportunities and future developments
Above a certain dimension or configuration, one can hardly distinguish between a window, a door and a sliding glass wall. These projects challenge materials’ limits and require extreme care during all stages of development and assembly, revising a series of procedures, especially those often neglected in more traditional solutions. Indeed, what initially seemed a task of adapting a sliding door system to a more massive structure, revealed at the end to have no component of the original window being used in this solution. However, these works are fundamental for testing the limits of materials and measuring the state of the art technologies.
The first attempts at installing large sliding glass doors in India revealed the difficulties and the limits of the system. Back in 2011, in the Juhu Beach house project, 1919 tempered laminated six-metre-high panes had a considerable deformation, as the existing technology hadn’t yet achieved the level of perfect flatness of the 2015 UK case study. This irregularity, combined with the weight of the glass, shattered and torn the polyamide profiles and damaged roller bearings.
Furthermore, aluminium composite extrusions reinforced with high strength stainless steel supporting elements were not yet available, so all reinforcements were done in an artisanal way, with bent steel plates additions and complicated bonding, which resulted in the window to operate unsmoothly and to require adjustments after installation. In 2012, the industry was getting ready to transform oversized glass panes, and the 7.2 m doors of the other Mumbai house were already double-glazed, although the sealed unit was still manually manufactured and assembled.
By 2015, when panoramah!® installed the UK 8 m-high glass doors, the previous experience of these two projects and others — ranging from 5.5 m to 6 m high doors — allowed to optimize several procedures: better extrusions and reinforcements, hybrid fixations combining mechanical assembly and bonding, testing different roll bearings gauges, combination of solid elements with water jet and laser cut parts, etc.
Therefore, with this experience, conditions had emerged to conceive and produce a new series of sliding doors and windows, optimised to resolve many of the questions raised in large sliding panes. The new series renders much easier the installation of glazing around 20 m² per pane in double-glazing. Maximum surfaces can theoretically go up to a maximum of 29 m² and triple glass units up to 19 m² per panel — although with a more complicated installation — while maintaining 20 mm vertical profiles: an exponential surface growth achieved only through the reinforcement of the frame.
Instead of enlarging current aluminium profiles with polyamide elements as performed before, the engineering of the new 60 mm thick series altered significantly their section, changing the position of the polyamide profile — now between each rail instead of being placed in the axis of each track — in a way that it ensures a very efficient thermal break [figure 4].
Many of the problems raised in previous works that were particularly stressed in projects like this UK case study could, therefore, be eliminated in this new panoramah!® 60 series. Among the issues that were better understood and improved, we could stress three. The relevance of the stiffness and perfect planarity of the layer under the sill, with no deformations, is fundamental to ensure ideal operability of the sashes even with motorization.
Care with this issue had been a significant concern in the first minimal windows installations but had progressive been neglected as the evolution of the product and the improvement of its various components rendered it less perceptible. However, the larger and heavier the panes are the more evident this aspect becomes. A second aspect relates to air and water tightness. So far, improvements on water tightness tended to render air tightness less effective and viceversa.
With the need for altering the water column and the drainage system to screw the sill to the underneath structure, both air and water tightness were significantly improved. A final but central aspect that was carried to the new series regards the redesign of the central mullion. Its more significant gap between the two sashes allowed to prevent friction in the other sliding pane — something that occurs with the deflection of oversize or not so large square-shaped glazing — but also to eliminate possible thermal transfers by radiation. Together with the improvements in the frame and the new position of the polyamide profile, this contributed to significantly improve the thermal performance of the new series, awarding it a Minergie-P certification.
This comes to prove those limit situations are crucial steps to develop better products, imposing a shift of scale that raises awareness about aspects that are not so evident at a smaller scale or standard solutions. Somehow Verdi’s motto that you need to step back to move forward [5] seems particularly accurate.
References
* The title of this article is a deliberate twist at the song “The Biggest, Loudiest, Hairiest Group of All” by The Velvet Underground.
[1] Developed by panoramah!® for Villa NHV in Vandoeuvres (Geneva, Switzerland), a dla designlabarchitecture project. The new 54 mm series, quickly became the most award-winning minimalist series, with Minergie and Passivhaus certification for improved thermal performance.
[2] Villa D in Vaud (2015) designed by architect Grégory Garcia.
[3] Yet 50% of the manufactured glass was wasted: 9 oversize glasses out of 13 were discarded for being defective; therefore the total glass manufacture for these doors was 22 panes.
[4] Trucks with 13.5 m-long capacity can carry two charges of 6.5 m profiles, while sea transportation sets a 5.80 m limit with 22-foot containers.
[5] “Torniamo all’antico e sarà un progresso”, as wrote Giuseppe Verdi in a letter to Francesco Florimo in 5th January 1871.
Acknowledgements
Figures 1, 5, 6, 7, 8 and 9 reproduced courtesy of Pringle Richards Sharratt Architects.