The quality and the processing of the glass edge is extremely important, because it has a decisive influence on the strength - and therefore also on the service life - of the glass.
CORRECT GLASS EDGE PROCESSING IS VITAL
Processing the glass edges of the shaped sheets is a highly complex process, which demands extensive expertise and the use of the right tools or machines. It is only possible to produce high quality end products that end customers will enjoy for a long time through glass edge processing that is suitable for the respective application.
Furthermore, due to its physical properties (such as its heavy weight, brittleness and possible material tensions) glass tends to break if there are defects at the glass edge - in particular due to improper handling or stresses caused by heat or wind loads. Professional glass edge processing hugely reduces this risk, and in turn has a highly positive effect on occupational safety and any after-sales costs. Moreover, it can also deliver a decisive reduction in wear costs during subsequent processing steps, because a smooth edge not only makes transport itself safer, but also safeguards the transport equipment such as rollers and belts.
WHAT YOU NEED TO KNOW ABOUT GLASS EDGE PROCESSING
Leading-edge machines are used for glass processing, alongside grinding belts or grinding wheels produced with corundum or diamond.
Seaming is the simplest method for processing the cut glass edges, whereby the edge is broken to a greater or lesser degree by means of a grinding tool in order to largely remove overbreaks and underbreaks, as well as micro-cracks. The edge subsequently exhibits a bevelled edge. Edges are primarily seamed for the production of partially tempered or toughened safety glass, in order to prepare the glass for the tempering process or a hardening system. But this type of glass edge processing is also used for insulating glass sheets whereby the glass edges will not be visible once installed.
Grinding is another method of glass edge processing, and is also referred to as glass edge adjustment. We also refer to dimensional grinding as fine adjustment. During this process, the glass lites sheets are ground to size with stock removal, after which they have a finely structured edge. This type of glass edge processing is used, for example, for glazing in buildings where edges will be visible as well as for interior applications.
Polishing is the highest quality glass edge processing method; it is the finest form of processing and delivers very smooth and transparent results. Polished glass edges are primarily used when the glass sheets are intended for decorative purposes, for example for mirrors or table tops. The glass edge is optically transparent and exhibits a very fine, homogeneous polish.
THE DIFFERENT GLASS EDGES
Fully unprocessed glass edges have irregular, sharp edges with slight wavy lines (also called Wallner lines) in the edge zones. Furthermore, the finest micro-cracks can be found here, which can sometimes lead to glass breakage under load. For this reason, glass sheets with unfinished edges are essentially only used if they are in a frame.
SEAMED GLASS EDGES (KGS)
Seaming eliminates the sharp ridge on the glass edge and creates an angled transition between the edge and the glass surface. Glass sheets with seamed edges are predominantly used for windows, because the processing significantly reduces the danger of injury when installing the glass sheets. However, it also significantly reduces the risk of breakage resulting from mechanical or thermal stress, for example during tempering.
Typical product applications of seamed glass edges:
- Insulating glass
- Single-sheet partially tempered glass
- Architectural glass
- Mirror
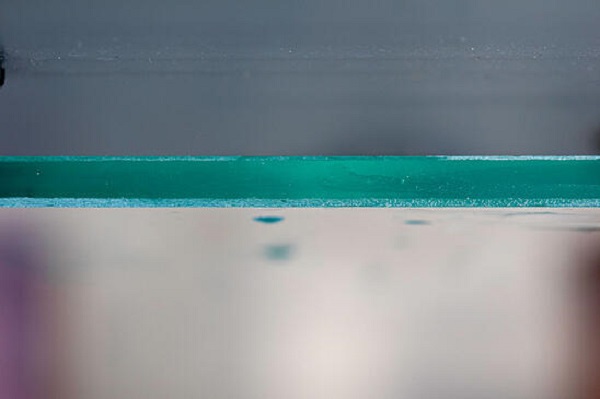
ROUGH EDGE (KMG)
We refer to a rough cut edge if prominent irregularities are rectified after seaming, whereby bare areas and conchoidal fractures are permissible as long as the final dimension is correct.
Typical product applications of rough edge:
- Insulating glass
- Single-sheet partially tempered glass
- Architectural glass
- Mirror
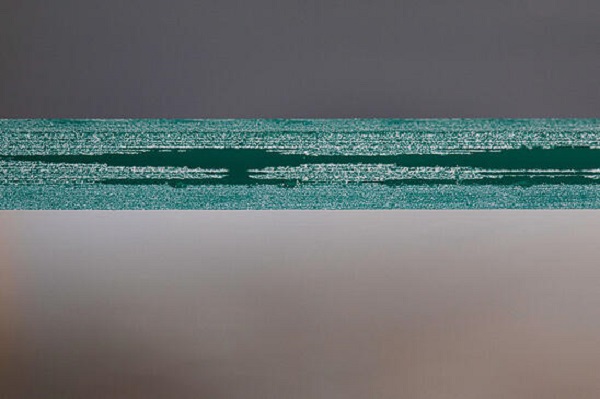
GROUND EDGES (KGN)
The seamed glass edges are processed over the entire surface by means of grinding here, in order to remove overbreaks and underbreaks. This brings the glass sheet to precisely the required (installation) dimension and compensates for manufacturing tolerances. This form of processing step results in a matt ground edge surface with seamed edges. Grinding optimises the physical and optical quality and reduces the risk of breakage.
Typical product applications of ground edges:
- Exterior architecture including LSG (façade and roof structures)
- Interior design including LSG
- Photovoltaics
- Automotive industry
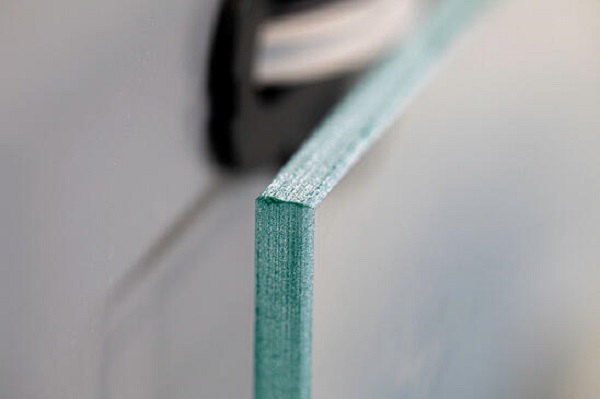
POLISHED EDGE (KPO)
The polish further refines the ground edges, giving them a shiny surface. Grinding marks are permissible, although they must not be matt. Polishing the glass edges is primarily carried out if there is a requirement for the finished glass sheets to be of the highest optical quality. The edge can be further refined by a so-called facet cut, whereby it is possible to obtain interesting optical effects through light reflections.
Typical product applications of polished edges:
- Interior design including LSG (balustrades, stair railings, staircases, glass panelling, glass doors and shower screens, room layouts, kitchen components, etc.)
- Furniture industry
- Single-sheet fire protection
WATER JET CUT EDGE (KGNW)
Glass edges can also be processed over the entire surface by means of a water jet. This also results in a matt ground edge appearance. This method facilitates glass cutting of the glass sheets in almost all variations without a requirement to change the tool.
Typical product applications of water jet cut edges:
- Exterior architecture including LSG (façade and roof structures)
- Interior design including LSG
- Fire-resistant glass
- Bulletproof multi-laminated LSG
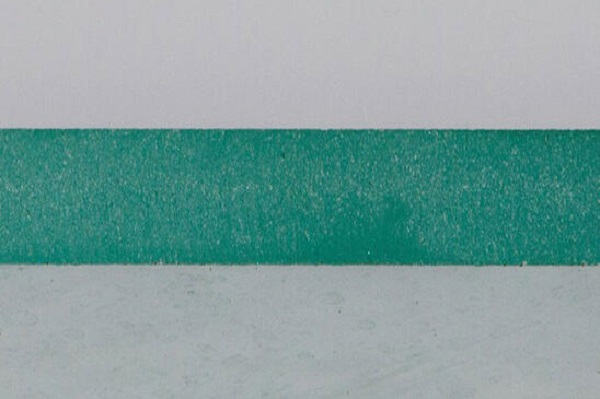
THE RIGHT MACHINE FOR OPTIMUM GLASS EDGE PROCESSING
A distinction is also made between straight edges, bevelled edges, C-edges (round edges), facet edges, etc. With all this variety, the choice of method and the plant or machine is naturally also hugely important when it comes to achieving the best possible results.
As a leading glass processing machine manufacturer and insulating glass producer, LiSEC has been developing equipment, software and services for the efficient and high-quality processing of flat glass for the construction glass industry for more than 60 years. To make sure that production is both seamless and safe, LiSEC relies on a vertical processing line for the edge and interior processing of flat glass lites sheets: the in-house products KSR, KSD, EPS and SplitFin! These DIN 1249-certified systems are perfectly suited for the respective edge processing operations.
VERTICAL GLASS EDGE PROCESSING SYSTEMS AT A GLANCE
Glass edge seaming - KSR: The vertically aligned fully automatic compact grinding machine KSR from LiSEC trims the edges of glass sheets on all four sides - and it does so with the simultaneous help of the 360° rotatable grinding device and the diamond-tipped wet grinding belts on the front and rear of the glass edge. Due to the vertical design, the cycle times are significantly shorter than with horizontal systems and particularly long service lives of the abrasive materials are achieved.
Glass edge grinding - KSD-A: The KSD-A edge seaming and grinding machine also offers the advantages of the vertical design, and is additionally equipped with the innovative LiTEC slider technology. The KSD-A is currently the most flexible seaming and grinding machine available, combining massive flexibility in processing with stable and reliable process execution, as well as very high quality for both shapes and rectangles.
Glass edge polishing - EPS-B & MRX-B: This edge processing system is divided into two processing towers, with the first (EPS-B) performing the complete edge processing and the second (MRX-B) taking care of all internal processing. The two stations together make up the LiSEC SplitFin, which is currently the fastest vertical processing line on the market.
The advantages at a glance:
- High productivity and therefore high return on investment
- Significantly reduced processing cycle time
- Flexible configuration
- Easy to operate and maintain
- Autopilot for processing
- Final polish without tool change
- Integration of a second system is possible at any time
THE ALL-IN-ONE SOLUTION FOR ALL GLASS EDGE PROCESSORS
The SplitFin is also an all-in-one solution for grinding, polishing and cut-outs, and it therefore simplifies large parts of the intralogistics - a very delicate issue in glass processing in particular. Every process required for producing a shower screen or glass partition with cut-outs is possible within the shortest cycle time on a single system with the LiSEC SplitFin. Thanks to its modular build-up, the SplitFin facilitates the production of drilled holes, countersinks and ground cut-outs and has ten tool change positions on the front and rear sides respectively.

As such, the SplitFin is designed for all glass processors who require a professional and fast solution with very high sales volumes in both interior and exterior areas. With respect to production costs in particular, the vertical orientation of LiSEC's SplitFin delivers a huge advantage over all horizontal systems.
While horizontal systems work with up to 34 spindles - all of which have to be readjusted and equipped with different tools for each glass thickness - the SplitFin operates with 1 to 2 spindles. This saves a considerable amount of time during production, whilst also noticeably reducing maintenance costs. Furthermore, LiSEC's vertical system requires significantly less space.
CONCLUSION
Achieving optimum quality in flat glass processing, in conjunction with low costs, requires the use of various glass edge processing methods. The glass edges must be processed individually and the correct system and method must be used, depending on the area of application. These parameters also have a major impact on efficiency and the cost of production.