This paper was first presented at GPD 2023.
Link to the full GPD 2023 conference book: https://www.gpd.fi/GPD2023_proceedings_book/
Author: Thomas Rainer
The demand for new functions and smart window applications has grown increasingly over the last few years. The realization of these new functions leads to the development of new glass processing technologies using laser radiation. By means of laser radiation it is possible to change a broad range of properties of the glass product. Depending on the case, these laser structures can be both visible and invisible to the naked eye. For those laser induced processes with the aim of producing new architectural glass products, special laser machinery has been developed and well established. New glass facades now have those additional laser induced functions.
But there are a lot of existing facades with requirements of additional functions to fit the modern demand of living and working in modern buildings. For the first time, a "laser upgrade" for façades, balustrades and windows in their installed state is possible by using mobile laser technology. Thermal insulation and other functional layers can be provided with new functions and even uncoated glass surfaces can be upgraded. This is made possible by laser-supported functional layer modifications and, alternatively, laser transfer printing.
By using special mobile laser equipment developed for outdoor use, the "laser upgrade" can still be carried out on buildings at a later date. This extends the life span of architectural glass products, as they do not have to be replaced due to new requirements for the building envelope or due to missing comfort functionalities.
Upgrades or legally required functions such as improving cellphone phone reception or adding structures to minimize bird strike are examples of the broad possibilities for laser processing. This is the first time a sustainable solution for the use of architectural glass beyond a maximum or extended lifetime is presented.
Laser induced process examples of laser applications will be presented as well as different mobile laser tools.
Laser-treated glass suitable for wireless communications
The laws of physics cannot really resolve it: glass that features a low-E or another type of functional layer to improve its insulating properties, has a significantly reduced heat transfer coefficient, which improves the pane’s thermal insulation. The downside, however, is that the layer minimises the pane’s level of penetrability for high-frequency wireless communication waves. Communication with cellphone phones or tablets is only limited in the best-case scenario and impossible in the worst. Physically speaking, the problem is easy enough to identify. If the panes or the glass front are finished with a metallic coating, the building envelope acts like a Faraday cage involving a large proportion of glass and metal. This either prevents the penetration of wireless communications entirely or severely impairs them as a result of the unintentional reflection of the signals.
A new finishing process from HEGLA boraident has broken through the fundamental conflict between thermal insulation and the requirements of wireless data communication. The process involves partial modification of the low-E or functional layer by laser in extremely thin lines to allow the high-frequency waves to pass through. The modification process follows a newly developed organic pattern consisting of overlapping dodecagons or circles. As a result of the fine line width, the finish is barely visible to the naked eye. If the pane is processed into an insulated glass unit in a further step, the texture can be described as virtually invisible.
Laser segmentation significantly increases the level of penetrability for wireless and data communications. Once the finishing process is complete, the energy transmittance for high-frequency waves is comparable to that of uncoated glass. Even at the higher frequencies and bandwidths of the 5G standard, the limitations do not become greater. The surface treatment designed to enhance the penetrability of glass for wireless communications has proven advantageous in environments where wireless communication is featured, such as conference rooms or hotels.
In terms of quality, the glass surface remains undamaged by laser processing, and its strength is not negatively affected by float glass, toughened glass, or tempered glass. The insulating properties and energy efficiency of the glass remain virtually the same. The added functionality of smart glass is an important area to retrofit existing glass facades in our world of digital communication. Now glass facades or window products can be retrofitted using laser techniques to increase the permeability to mobile communication radio waves – perfect for use in areas such as conference rooms and offices. The laser processing method for creating a glass finish for wireless communications can be done by the CELLFree mobile.
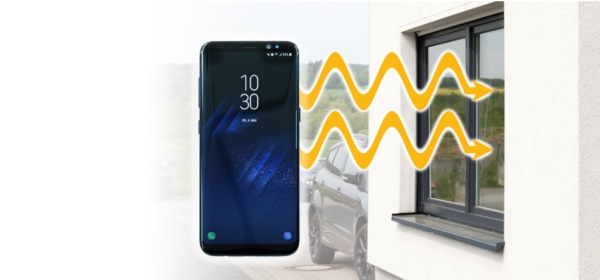
Bird protection glass with intelligent laser printing
Up to 100 million birds die in Europe each year because they cannot detect glass façades, bus stops, balcony glazing, greenhouses and windows as obstacles. Collisions with glass are the biggest unnatural cause of bird deaths – despite the fact that bird strikes can be prevented.
With the laser printing technology, a retrofitting of existing facades with bird friendly function is possible, whose two fundamental characteristics cover the range of possibilities. If aesthetics are the top priority and the bird protection finishing treatment must be subtle, tiny dots or even geometric shapes can be applied to the surface. The resulting pattern is almost imperceptible to humans. The printed pattern’s high level of transparency does not affect the overall visual impression. If a more obvious pattern is desired or the bird protection finish is to be integrated into the façade design, then logos, complex designs and symbols can be printed to be highly visible. The surface of the pane is not impacted by the laser printing method.
The elements, dots or designs are applied by a laser in conjunction with nanoparticle tape. The generated print cannot be felt and is wafer-thin, colourfast, lightproof, smudge-proof, and scratchresistant. Its protective properties include the print’s slight reflection, whose broad diffusion of light makes obstacles perceptible. The printing result used is very subtle for humans, but to birds’ eyes, it points out an obstacle. The finishing treatment is implemented on the outside to negatively impact the mirroring of trees and plants in such a way that birds do not attempt to fly through them.
The laser print can be made with the BIRDFriend mobile device mounted at existing facades at all kinds of architectural glass products IGU’s, facades plates or laminated glass.
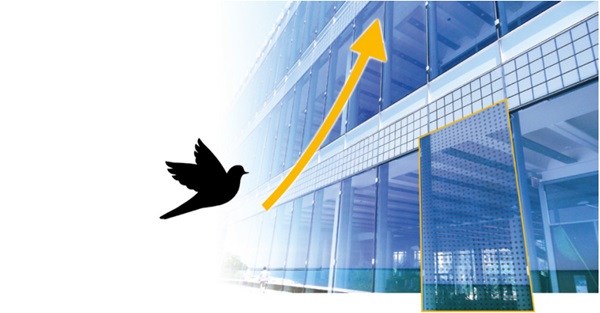
Antibacterial laser-treated glass
Humid conditions and medium-to-high room temperatures in indoor areas such as kitchens, bathrooms or saunas promote the growth of fungi and bacteria. HEGLA boraident’s innovative process of creating antibacterial glass relies on the laser-assisted release of silver ions into glass surfaces to create an antibacterial function. This ion inoculation leads to the killing of bacteria that are transported to the glass surface as the glass product is used (e.g. due to contact with human skin). Manufactured antibacterial glass is ideally suited for use in environments that are subject to special hygiene requirements or are particularly at risk from germs.
With a mobile laser transfer printing device, the antibacterial function can be retrofitted on existing glass products using a printing ribbon with silver-plated material.
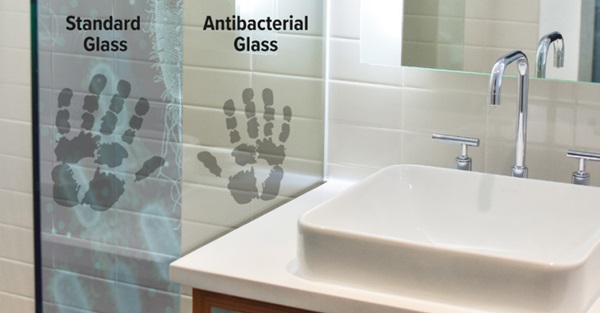
Clear markings for traceable glass and product identification
If the laser-assisted functionalization of glass products is used for installed glass products the modification of the product must be marked. For this application laser technology is becoming more important for usage in identification processes.
The products are marked with a unique, machine-readable QR or data matrix code (and often a logo) after retrofitting the glass with a new function. Marking the glass using the UniColor laser printing process, for example, leaves the surface undamaged and permanently bonds the marking to the pane without scratching it. This individual marking allows access to the information about the retrofitted function.
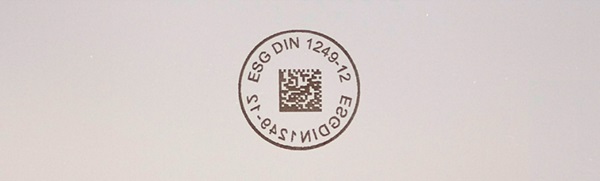