This paper was first presented at GPD 2023.
Link to the full GPD 2023 conference book: https://www.gpd.fi/GPD2023_proceedings_book/
Authors: Sagar Vanapalli & Stefan Reich
Abstract
Glass is non-reactive to most chemicals including solutions of inorganic alkalis and acids such as ammonia and sulphuric acid. Due to this glass has various applications in everyday use such as windows, doors, building skins, furniture, drinkware, automotive windows etc. Cleaning glass is also easy with nonabrasive cleaners including many antibacterial cleaners.
Wood on the other side gives a particularly high quality, natural and noble appearance. Although wood has high design requirements, it needs a lot of maintenance and is very sensitive to most cleaners. Particularly in healthcare institutions, the application of wood is even more limited. Intensive use of aggressive disinfectants and mechanical abrasion damages the surface finish.
According to the German Federal Institute for Occupational Safety and Health (BAuA) TRBA 250, all the surfaces in health care and welfare facilities must be impermeable to water, easy to clean and resistant to disinfection and chemicals used. These specifications mean that only surfaces made of ceramics, metal or plastic are used in furniture and work surfaces in the healthcare sector.
Glass timber panels (GTP) combine the visual effect of noble and high-quality wood materials at the same time meet-ing the hygiene requirements for the health and welfare sector. This paper describes the fabrication requirements and techniques of GTP.
1 Introduction
1.1 Psychological impact of use of wood in health care
Wood has a long history of use as a construction material and for fine crafts. Despite its positive psychological effects, its use in healthcare settings has been limited. Although research on the psycho-physiological impact of wood is not extensive, existing studies have utilized contemporary methods and focused mainly on the autonomic nervous system responses. These investigations have shown that incorporating wood into built environments can have a distinct influence on physiological stress markers, such as skin conductivity, heart rate, and blood pressure.
In particular, four out of five studies have indicated that wood has an instant effect on reducing the reactivity of the sympathetic nervous system, which can help individuals avoid heightened stress in response to their surroundings. For example, Kelz et al. 2011 found that heart rate variability increased in students exposed to wood-dominated classrooms over the course of a school year, indicating parasympathetic nervous system activation. Fell 2010 observed lower sympathetic nervous system activation in wood offices during a stressful mental task, as well as lower skin conductance levels when participants were alone in the room. Park et al. 2010 found that diastolic blood pressure was lowest in a room with 90% wood coverage, while participants reported feeling most comfortable in a room with 45% wood coverage. In another study, Sakuragawa et al. 2005 showed that people who liked wood as a building material experienced a significant drop in blood pressure when facing a wooden wall, whereas those who disliked it did not. In contrast, liking or disliking white steel as a building material did not significantly influence blood pressure levels when participants viewed a white steel wall.
Overall, these findings suggest that using wood in medical environment and areas with patient traffic can have clear psychophysiological benefits, including decreasing stress reactivity and lowering stress levels over the longer term.
1.2 Scope of Glass Timber Panel (GTP)
Glass Timber Panel (GTP) Glass Timber Panel (GTP) is a surface application specifically designed for use in the healthcare industry. In healthcare settings, strict hygiene standards are required to ensure the safety of patients and staff. These standards are outlined in TRBA 250 which classifies surfaces used in healthcare based on their hygiene requirements.
Surfaces in Protection class 1, which include floors and work surfaces, must be easy to clean and resistant to the cleaning agents and disinfectants used. Surfaces in Protection class 2, which include work surfaces and adjacent wall surfaces, must also be resistant to disinfectants. Service rooms and special insulation stations have additional requirements for impermeability, smoothness, and seamlessness.
To meet these standards, surfaces made of ceramic, metal (usually stainless steel), or plastic-coated fiberboard are com-monly used in healthcare furniture and work surfaces. However, these materials may not always be suitable for every application.
GTP offers a high-quality wooden surface that meets the same hygiene standards as ceramic, metal, or plastic. This allows for greater design flexibility and a warmer aesthetic while still ensuring that hygiene standards are met. GTP is a promising alternative to traditional healthcare surfaces, offering a combination of functionality and aesthetic appeal.
1.3 Development of GTP
The concept behind GTP is to create a protective layer for wood by laminating glass onto its surface. However, initial attempts to laminate raw wood proved challenging due to its uneven surface, resulting in delamination. As a solution, a plain veneer surface is used instead of raw wood, as it provides a smoother and flatter surface for lamination. While veneer surfaces can still have some roughness, a thicker EVA foil is used to compensate for any grooves or imperfections. The foil melts and fills in these areas during the lamination process, resulting in a strong and durable bond between the glass and wood. The end product is a high-quality protective layer that can withstand wear and tear, while also enhancing the visual appeal of the wood.
The development of GTP is carried out in three phases of lamination, 1D, 2D and 3D (Figure 1), where 1D involves lamination on one side, 2D on two sides, and 3D on all sides. However, in the current paper, the focus is only on the 1D lamination phase.
Glass
All the specimens are fabricated using 4 mm float glass. Specimens with 2 mm and 3 mm float glass are also tested and is feasible for lamination.
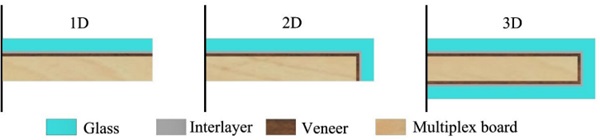
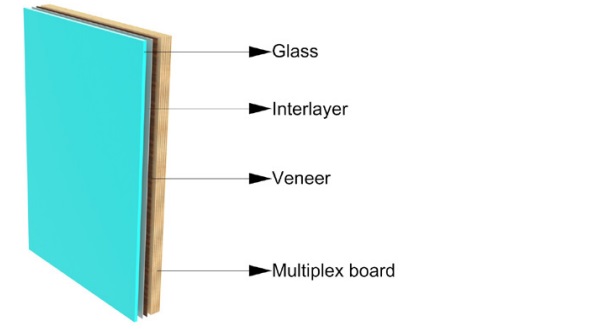
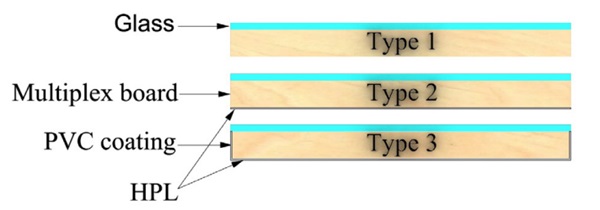
Interlayer
EVA foil with 1.52 mm and 0.76 mm thick are tested. Thicker foils were found to cause glass breakage either during or after lamination due to high stresses in the interlayer during the lamination process. As a result, the 0.76 mm EVA foil thickness was found to be the most suitable for the lamination process and was subsequently used for all GTP specimens.
Veneer
Within the framework of the project following veneer, types are tested based on the market trend from the project partner. Based on the type of wood thickness of veneer various from 0.5-1.5 mm.
- Oak
- Walnut
- Elm
- Core Ash
- Teak
- Larch
Multiplex Board
Multiplex board of 12 mm thick is used for all the specimens as recommended by the project partner.
1.4 Test specimen types
In order to assess water permeability, three types of GTP specimens measuring 200 mm x 300 mm were evaluated. Each specimen has one large side laminated with glass, while the other large surface and edges are treated in different ways as shown in Figure 3.
Type 1 specimens have open edges and an untreated large surface, allowing for unobstructed water flow.
Type 2 specimens have a high-pressure laminate (HPL) coating on the large surface, but the edges remain untreated.
Type 3 specimens have large surface coated with HPL, and the edges with PVC creating a barrier to water permeation.
Specimens are named accordingly with type of veneer used, thickness and type of specimen followed by the number as shown in the Table 1 for the specimen E0T11.
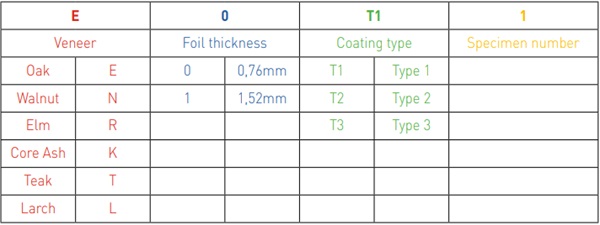
1.5 Lamination process
Safety glass is created by laminating two glass layers together with an interlayer that is melted at a temperature range of 120°C-140°C, depending on the thickness of the glass and foil. The lamination process takes place under vacuum conditions to ensure that the final product is free from any air bubbles or impurities.
GTP uses a similar lamination process that of safety glass, but instead of laminating both sides with glass, a wooden board that has already been glued with veneer on one side is used. To protect the vacuum bags from the sharp edges of the glass and wooden board during lamination, the specimens are packed in fleeces (as shown in Figure 4). The packed specimens are then placed in silicon vacuum bags and heated in an oven (as shown in Figure 4). The temperature is maintained constant at different stages to ensure uniform heat distribution. Throughout the lamination process, the specimens are under a contact vacuum pressure that guarantees optimal lamination. Once the lamination is complete, the vacuum and heating are both stopped, and the specimens are gradually cooled to room temperature. The lamination process results in a water loss of 3-7% in each specimen.
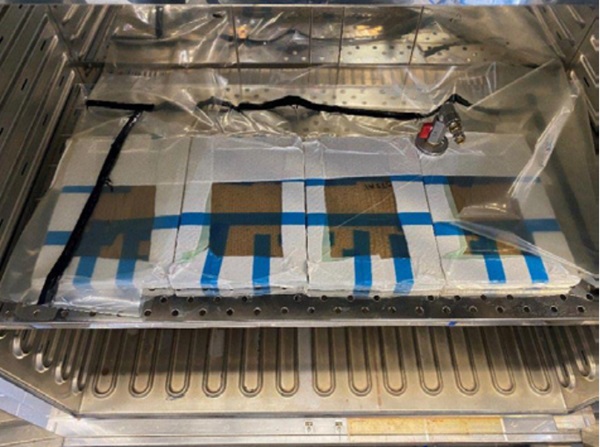
2 Lamination durability test
Even though indoor furniture is not typically exposed to extreme environmental conditions, the surfaces in health care are often subjected to frequent cleaning and disinfection, which can lead to chemical exposure and moisture penetration. To ensure the durability of GTP, the laminating joint between the glass and veneer is thoroughly evaluated for resistance to moisture penetration. Two tests are conducted to assess its durability. The first test evaluates the lamination’s resistance to temperature and humidity, while the second test involves immersing the specimens in water and disinfectant to assess the penetration of moisture into the laminating joint.
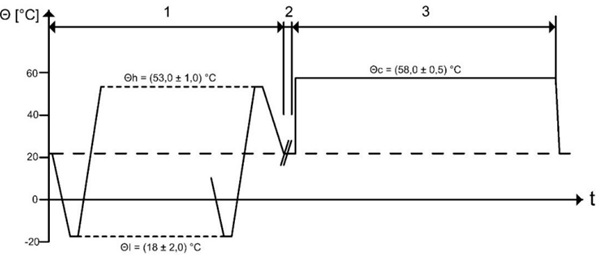
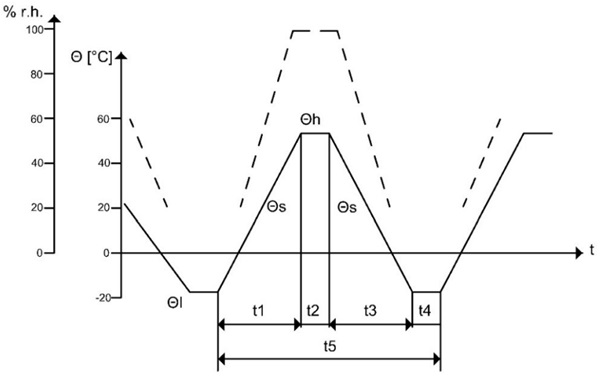
Legend for Figure 5
- 56 temperature cycles of 12 h each (corresponding to four weeks).
- Interval of two to four hours for the transposition of test discs when two test chambers are used.
- (1 176 ± 4) hours (seven weeks) of constant temperature and one relative humidity during the temperature cycle.
Legend for Figure 6
- Relative humidity during the temperature cycle. Maximum value of RH ≥ 95 %. High humidity is interrupted during the cold phase of the cycle. Temporary condensation on the test discs is permissible.
- Time intervals: t1 = 2.5 h, t2 = 1 h, t3 = 2.5 h, t4 = 1 h, t5 = total cycle time 7 h
- Θh = (53.0 ± 1.0) °C (High Temperature)
Θl = (–18.0 ± 1.0) °C (Low Temperature)
Θs = (14 ± 2) °C/h (Temperature gradient)
2.1 Temperature-Humidity resistance
The temperature-humidity storage for multipane insulating glass according to DIN EN 1279-2 is used as a reference. This standard specifies requirements for temperature and humidity that are far above those of interior rooms. It is used for the proof of durability of multi-pane insulating glass. Therefore, the results show a qualitative comparison of the durability of the different laminates. However, failure during this test does not necessarily indicate failure in the interior application, the field of application of the glass-wood laminates.
The DIN EN 1279-2 standard outlines a two-phase test procedure. During phase 1, the temperature is continuously cycled between 53°C and -18°C with a relative humidity of ≥95 % (Figure 6). This process is repeated 56 times over a four-week period. In phase 2, the specimens are kept at a constant temperature of 58°C and 100% humidity for a dura-tion of 1176 hours, which is equivalent to 7 weeks.
2.2 Results from durability test
After testing for 11 weeks with continuous exposure to moisture, glass delaminated for 9 out of 36 specimens with veneer (Figure 7), as indicated in Table 1. Although the moisture had caused the veneer to deteriorate, the glass did not delaminate (Figure 8).
Each specimen’s weight is evaluated before and after test and an increased weight of 3-5% due to moisture absorption is observed. Interestingly, no clear patterns of moisture absorption were observed in Type 1, Type 2, and Type 3 specimens, as shown in Figure 9. Notably, only 1 out of the 12 Type 3 specimens delaminated, while no clear delamination s patterns were observed in Type 1 and Type 2 specimens across different veneer types tested.
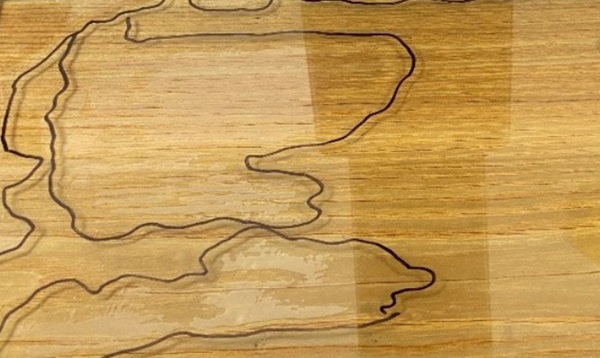
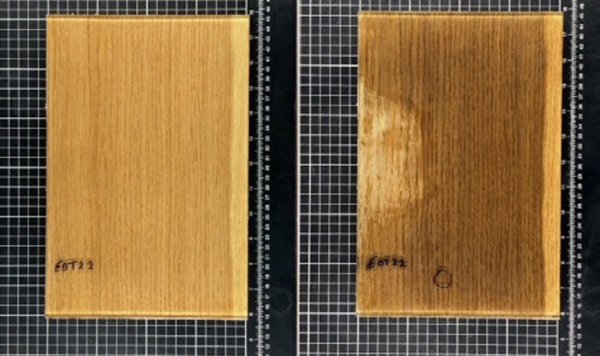
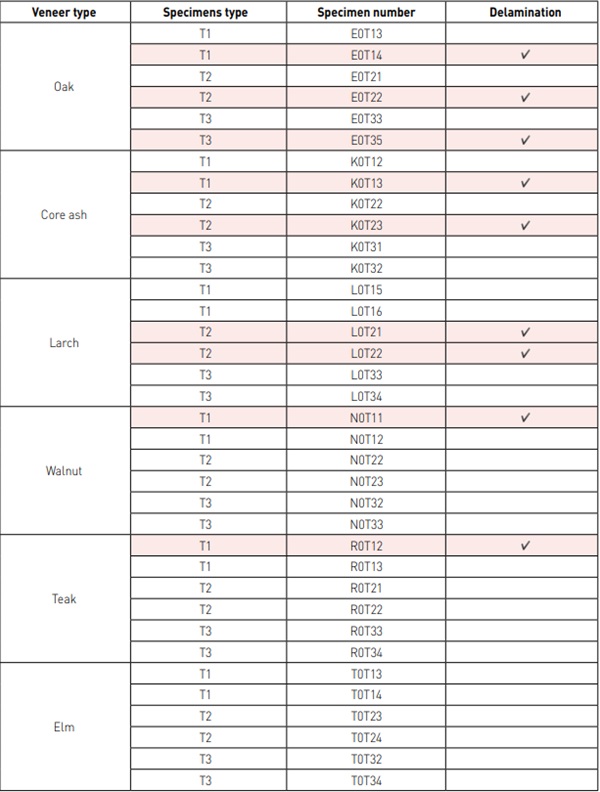
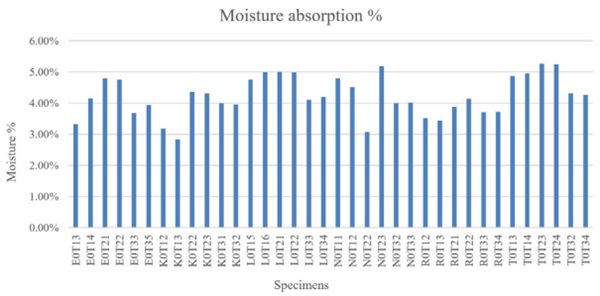
2.3 Immersion test
As the edges of T1 and T2 specimens are untreated, they are susceptible to damage during the immersion test. There-fore, only T3 specimens were selected for evaluation. During the test, one specimen from each wood type was im-mersed in water and disinfectant for 60 days, with a 10 mm immersion depth as shown in Figure 10 left. Interestingly, neither water nor disinfection caused any delamination in the specimens. Although one can observe the penetration of the moisture as shown in the Figure 10(right).
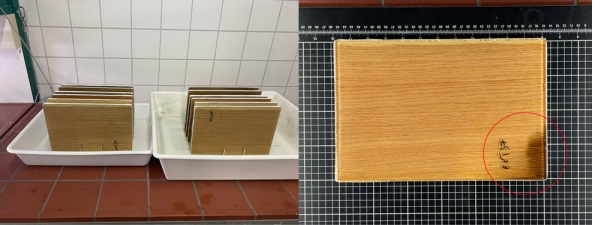
3 Challenges
3.1 Cracks
During the lamination process, certain specimens, particularly those laminated with larch, have developed cracks, most likely due to the drying of the veneer. Another possible reason for cracks is due to pressure exerted by the foil when melted at high temperatures. Foil melts and due to the vacuum pressure on the specimen, the foil tends to flow out pulling the fibers apart that result in cracks. While some specimens of walnut also showed signs of cracking, this was prevented by drying the veneer prior to lamination; however, these cracks, although relatively minor, can still detract from the overall aesthetics of the product as shown in Figure 11.
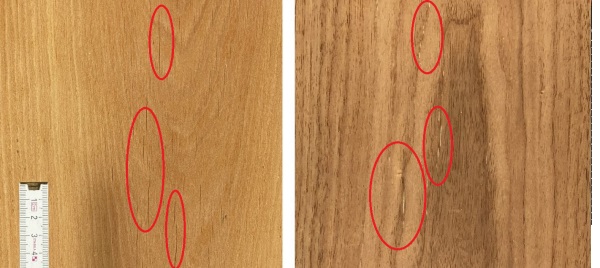
3.2 Air bubbles
During the lamination process, it is important for any air trapped between the glass, interlayer, and veneer to escape from the edges, which is achieved by placing the entire specimen under vacuum. However, air bubbles can still occur due to several factors such as air trapped in grooves or cracks of the veneer (Figure 12 A,B), insufficient lamination waiting time for air to escape (Figure 12 C) and unclean surfaces during lamination.
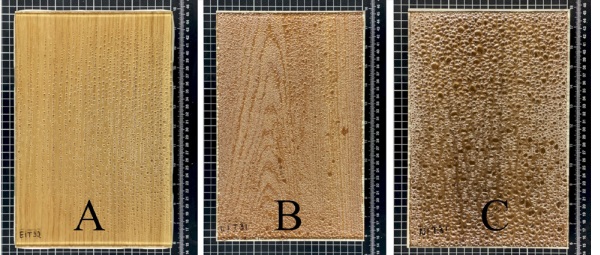
3.3 Warping of specimens
As wood absorbs moisture, it swells and as it loses moisture, it shrinks. If the moisture is unevenly distributed across the wood, it can lead to warping. The majority of the specimens experienced warping, resulting in a difference of approximately 0.5 mm for a 200 x 300 mm specimen. Extrapolating this to 1000 mm, this would result in a 2.5 mm warping, which is unacceptable for the development of accurate joints and furniture.
Two types of warping were observed during the study, one caused by uneven moisture distribution and the other due to foil thickness. Because of moisture loss, the wood swells and warps, as depicted in the figure below. To mitigate this, one possible solution is to predry the specimens and add an extra layer to on the back of the multiplex to compensate for the glass thickness during lamination, which could enhance the stability of the board.
Another type of warping observed was due to thicker foil. In the figure below specimen E1T32 is presented, which was laminated using 1.52 mm thick foil (i.e., two 0.76 EVA foils), the melted interlayer was pressed between the layers, causing the interlayer in the corners to be squeezed out more than that in the center, leading the glass to bend. This developed stress in the glass, ultimately causing it to break. Unequal distribution of vacuum pressure may also contribute to this issue. Although the use of 0.38 mm thick foil helped to reduce warping, the effect was still significant.
Despite various attempts to address warping in GTP development, including modifying the lamination baking process, use of different vacuum bags for uniform distribution of pressure and drying the specimens, these methods have been ineffective. However, a promising approach was found by using an interlayer to laminate only the veneer with the glass, without the multiplex. Nonetheless, the glass-veneer laminate still exhibited a warping effect. However, after gluing the multiplex board to the glass-veneer laminate with a high-pressure laminating device, the specimens no longer exhibited warping. While warping remains a significant issue, using 0.38 mm thick interlayer and gluing multiplex board after lamination provides a potential solution for further development and refinement of the GTP process.
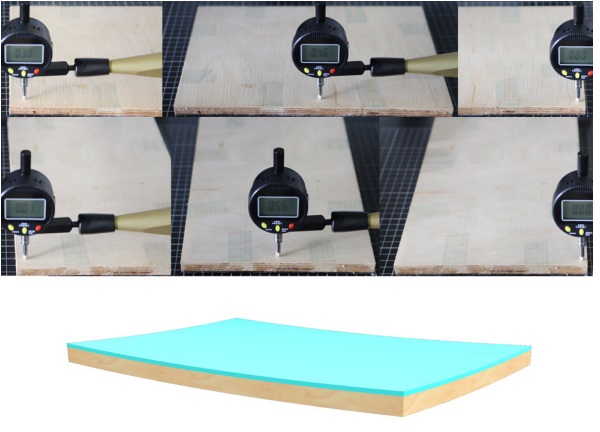
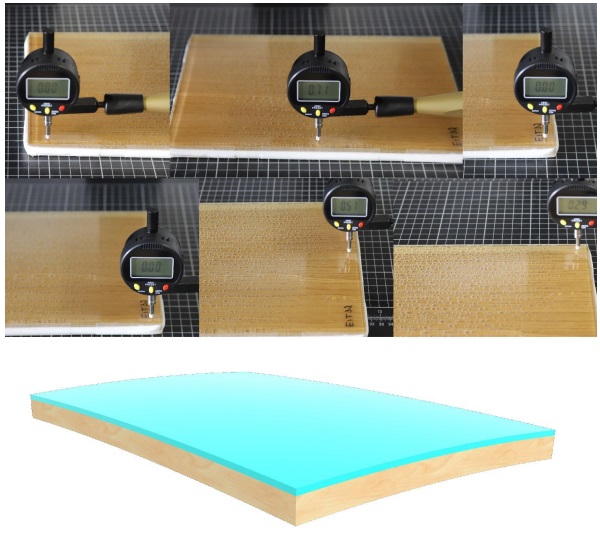
3.4 Broken specimens
During the lamination process, glass breakage was observed either immediately or a few days after lamination. It was found that specimens laminated with a 1.52 mm thick interlayer were more prone to breakage compared to those laminated with a 0.76 mm thick interlayer. Additionally, all broken specimens exhibited warping, likely due to uneven moisture distribution.
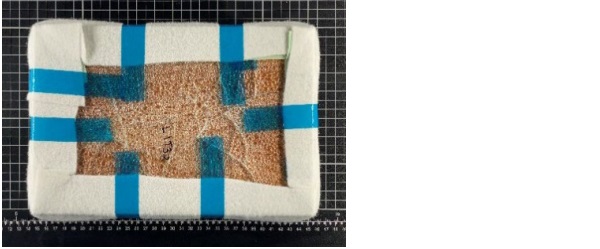
4 Discussion and further recommendations
The initial phase of GTP development has yielded promising results, as evidenced by the successful adaptation of the safety glass lamination process for glass and timber without compromising the aesthetic values of the wood. Moreover, the durability tests confirmed that the lamination could endure continuous exposure to harsh cleaning agents. Despite warping, being a persistent issue, the proposed technique in section 3.3 holds potential in controlling warping. Test using this new approach need to be evaluated further for durability test.
Moving forward, the next phase of GTP development will focus on testing and evaluating the durability of 2D and 3D lamination as mentioned in the section 2.2. Additionally, further testing using thin glass needs to be evaluated for producing lighter panels.
Due to Corona, hygiene standards are revised and stricter than before. These hygiene requirements apply not only to the health sector, but also to all public areas such as hotels, restaurants, public transport, old people's homes, etc. This will increase the scope of the GTP. This increases the scope of application of the GTP. The illustration below clearly demonstrates the application of GTP. Three different wooden boards (A-without treatment, B-linseed oil and C-GTP) are compared in contact with coffee and wine residues. After cleaning, it can be seen that GTP leaves no residues (Figure 16 right below).
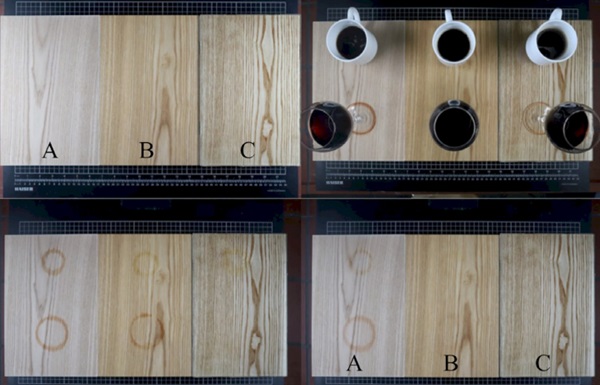
5 Acknowledgements
The research is conducted as part of a research Project supported by the German Federal Ministry for Economic Affairs and Climate Action. The authors would like to thank the project partner Geilert GmbH and Glaswerkstätten Frank Ahne GmbH for support with respect to the production of all needed test specimens.
6 References
DIN EN 1279-2:2018-10, Glass in building - Insulating glass units - Part 2: Long-term test methods and moisture absorption requirements. (2018). Beuth.
Fell, D. R. (2010). Wood in the human environment: restorative properties of wood in the built indoor environment. https://open.library.ubc.ca/collections/24/items/1.0071305
Kelz, C., Grote, V., & Moser, M. (2011). Interior wood use in classrooms reduces pupils’ stress levels.
Park, B. J., Tsunetsugu, Y., Kasetani, T., Kagawa, T., & Miyazaki, Y. (2010). The physiological effects of Shinrin-yoku (taking in the forest atmosphere or forest bathing): evidence from field experiments in 24 forests across Ja-pan. Environmental Health and Preventive Medicine, 15(1), 18–26. https://doi.org/10.1007/s12199-009-0086-9
Sakuragawa, S., Miyazaki, Y., Kaneko, T., & Makita, T. (2005). Influence of wood wall panels on physiological and psychological responses. Journal of Wood Science, 51, 136–140. https://doi.org/10.1007/s10086-004-0643-1
Technische Regeln für Biologische Arbeitsstoffe - Biologische Arbeitsstoffe im Gesundheitswesen und in der Wohl-fahrtspflege, (2014).