Authors: Esther Geboes, Waldo Galle & Niels De Temmerman
Source: Glass Structures & Engineering (2022) | https://doi.org/10.1007/s40940-022-00211-y
Abstract
End-of-life insulating glass units (IGUs) continue to follow a linear, wasteful path from renovation and demolition sites into landfills or low-value recycling. To get one step closer to the question of how to close the glass loop, this exploratory research outlines a cross-practitioners review of glass circularity in conventional Flemish and Brussels practices. A series of semi-structured interviews with network actors and an extensive literature study is conducted to identify existing and missing circular practices and to pinpoint the key barriers and opportunities.
In general, the circular strategies repurpose and open-loop recycling of end-of-life IGUs are successfully applied in Flemish and Brussels construction practices. Repair, reuse, and closed-loop recycling remain unexplored. The main barriers are the lack of collaboration, logistic and labour costs to collect end-of-life IGUs, its complex disassembly, the lack of legal incentives and the conservativeness of the construction sector. Case studies, the high recycling potential and the scale of projects are found to be the main opportunities for glass circularity. The cross-practitioners’ insights in this paper contribute to close the glass loop and to further development and up-scaling of circular strategies.
Introduction
In the Belgian region of Flanders, like in other European regions, policy is shifting from waste to sustainable materials management by establishing an economy of closed material loops by 2025 (European Commission 2020; Galle et al. 2017; OVAM 2014). The construction sector plays a crucial role in the realisation of those ambitions due to its material intensity and its potential to use recycled materials. In Europe, this sector is responsible for 20 to 30% of the total mass of generated waste (Ellen MacArthur Foundation, McKinsey Center for Business and Environment, and SUN 2015). Whereas most stone and concrete waste are already being recycled for various applications, still 54% of the construction and demolition waste is sent to landfills (Ibid.).
In Flanders and Brussels-Capital Region (BCR), these landfilled materials mainly relate to waste fractions of wood, PVC, plasterboard, insulation materials such as glass wool, and flat glass (Debacker et al. 2021; OVAM 2014; Romnée and Vrijders 2018). Architectural flat glass, for instance, is a fully recyclable material and yet, it follows a linear, wasteful path from renovation and demolition sites into landfills or low-value recycling (Debacker et al. 2021; DeBrincat and Babic 2018; Hestin et al. 2016; Westbroek et al. 2021). In Flanders and BCR, it is it is typically crushed together with other building rubble. This mixed waste is then either brought to the incinerator, put into landfills, or used as an impurity in recycled aggregates for low-value applications such as concrete for pavements, foundations, or road constructions (Debacker et al. 2021; DeBrincat and Babic 2018; Dubois et al. 2013; Glass for Europe 2013; Hestin et al. 2016; Nodehi and Mohamad Taghvaee 2022).
In 2007, the global flat glass production reached 44 million tonnes, of which 70%—or almost 31 million tonnes—was architectural flat glass (Hubert 2019). Architectural flat glass implies the glazing used in buildings and structures, such as insulated glazing, interior glazing, etc. (Belis et al. 2019). A commonly used insulated glazing in the building envelope is the insulating glass unit (IGU), a unit composed of two or more glass panes separated by a space bar that is glued with a sealant (Ibid.). The development of the IGU has been driven by reducing the operational energy need for heating and cooling buildings while optimizing the use of daylight (Glass for Europe, 2012). As a result, the importance of flat glass has been growing in both new buildings and renovations.
Replacing outdated glazing with new two-layer or three-layer IGUs has become a standard intervention to meet energy requirements. Yet, these interventions have led to an almost exponential increase in the consumption of glass material per window (Lendager and Pedersen 2020). For Flanders, as well as for other European regions, a significant increase in both flat glass consumption and waste is expected. To illustrate, Dubois et al. (2013) estimate that 127 to 151 kt of flat glass waste was generated in Flanders in 2011. Four years later, in 2015, this amount was increased to 172 kt according to Debacker et al. (2021).
To meet the current and future demand, more flat glass needs to be manufactured. However, manufacturing flat glass—the float process—is an energy-intensive process in which primary raw materials, principally silica sand, soda, lime, and dolomite, are melted at high temperatures between 1500 and 1600 °C (Souviron and Khan 2021). Westbroek et al. (2021) compare: “the energy intensity of glass production is estimated to be around 7–8 GJ/t. This is less than other energy industries such as steel, 20–30 GJ/t and aluminium, 90–100 GJ/t, but more than cement, 3–6 GJ/t.” It contributes to significant global CO2 emissions, contributing to annual CO2 emissions of approximately 86 Mt (Westbroek et al. 2021). Moreover, raw materials are running out: roughly 32 billion to 50 billion tonnes of suitable sand are depleted globally each year, mainly for making concrete, glass, and electronics (Bendixen et al. 2019). By 2050, this demand could outstrip the supply (Ibid.).
The circular economy as an alternative model
Conventionally, the construction industry adopts a linear take-make-waste model (Romnée and Vrijders 2018). In this linear economy, all investments end up as waste one day. The circular economy is an alternative model that strives for an economy without waste by keeping materials in circulation for as long as possible (Ibid.) For instance, by implementing circular strategies such as repairing, reusing, repurposing, and recycling flat glass, the material loop is closed and consequently, waste is minimised (Ellen MacArthur Foundation et al. 2015).
In theory, glass is a 100% recyclable material. Concretely, this means that IGUs can be processed into flat glass cullet—or in other words, crushed and processed flat glass—and can then be reintroduced in the production process to produce new flat glass products or other glass products. The first is also known as closed-loop recycling, defined by Debacker et al (2021) as “the material is recycled and used in the same application without changing the original properties of the recycled material”. However, the flat glass used for recycling must be free of contamination (e.g., ceramics, stones and porcelain (CSP), glass ceramics, metals, organic substances, and hazards) that might originate from IGU components (e.g., metal spacer bar) or other building materials (concrete, bricks, steel, etc.) on the demolition or renovation site.
As DeBrincat et al. (2018) warn: “Once introduced into a furnace contamination can take several days to pass through the system. Thus low levels of contamination can result in several days of lost production which will cancel out the environmental and cost benefits of recycling.” The second, open-loop recycling, implies that flat glass cullet is used to produce other glass products, such as container glass, glass wool insulation, and foam glass. Recycling, therefore, eliminates the need for more and more raw materials. However, important to notice is that once flat glass is open-loop recycled into container glass, which implies it is mixed with container glass cullet, it can never be recycled back into flat glass.
This is due to certain impurities that may be present in bottles and jars and do not meet the high-quality requirements of flat glass production (Rodriguez Vieitez et al., 2012). For instance, metal contamination in bottles originate from cans or caps that are thrown in the waste collection banks (Ibid.) The same logic applies to applications like glass wool or foam glass. These contaminants may cause damage to the produced glass, as well as to the furnace (Dubois et al. 2013; Hubert 2019). For instance, CSP and glass ceramics have a higher melting point than glass components and might not melt with the glass. As a result, defects may occur in the final glass product, in particular aesthetic and technical quality losses (Debacker et al. 2021).
Additionally, the use of cullet has many environmental benefits. First, for every tonne of cullet used in the manufacturing process, 1.2 tonnes of primary raw materials are saved (DeBrincat and Babic 2018; Lebullenger and Mear 2019). Second, compared to the energy needed to convert primary raw materials into glass, less energy is needed to melt the glass cullet. Consequently, the furnace temperature can be lowered. In general, every 10% glass cullet added to the melting process reduces the energy consumption by approximately 3% (Dubois et al. 2013; Hestin et al. 2016; Lebullenger and Mear 2019; Westbroek et al. 2021). Summarised, replacing all primary raw materials with glass cullet would result in about 30% furnace energy savings. At present, however, only a third of the batch consists of secondary raw materials, being the internal production waste (e.g., cutting losses, melting losses) of the flat glass manufacturers and processors (Butler and Hooper 2019).
Altogether, the case for recycling flat glass is strong. Yet only 11% of flat glass is recycled worldwide (Harder 2018), while other circular strategies, like the repair, reuse, or repurpose of IGUs, remains a niche practice. Taking into account the significant growth in both flat glass consumption and waste generation, and the potential savings of energy, raw materials and CO2 emissions of a closed material loop for flat glass, urgent questions arise about how we will manage today’s and tomorrow’s architectural flat glass waste in a sustainable manner.
Research objectives and scope
In the last few years, main barriers and opportunities of circular strategies have been studied extensively for the building sector. Some papers focus on the entire building sector (Giorgi et al. 2020; Harder, 2018), while others narrow it down to materials and systems (Hobbs and Adams 2017; Hartwell et al. 2021). Yet, none of them covers the circular strategies and practices related to the management of end-of-life IGUs. Therefore, this work addresses three, so far unanswered, research questions:
- What is the present level of application of circular valorisation strategies, not only recycling, but also reuse, repair, and repurpose, for IGUs in Flanders and Brussels?
- Which circular valorisation strategies for IGUs are still missing in Flemish and Brussels’ practices and what does this mean locally and globally?
- What are the related barriers and opportunities for end-of-life IGUs?
To answer these questions, we must look beyond the technical properties of glass and glass production theory. Like all sustainability transitions, a shift from a linear to a closed-loop economy requires to change day-to-day practices as well as underlying values (Geels et al. 2011). Those practices and values also explain why making the transition is so difficult. To get one step closer to the question of how to close the glass loop, this article creates on the one hand a complete and thorough overview of the current linear waste management practices for end-of-life flat glass in Flanders and BCR. On the other hand, this study discovers which innovative, inspirational circular strategies are already implemented in the regions and which are still missing in today’s practices compared to other regions. In total, four circular valorisation strategies within flat glass management—namely, repair, reuse, repurpose, and recycle—and the related barriers and opportunities are studied in more detail.
The focus of this article is set on Flemish and BCR. Both regions are forerunners in applying circular strategies in the construction sector. Initiatives such as Circular Flanders or Brussels-Capital Regional Program for a Circular Economy (BCRPCE) have proved to be successful in practice so far. Introduced in 2011, the Flanders Materials Programme “provides Flanders for a future-proof economy where material cycles are closed”, building on three pillars: a long-term vision, policy-relevant scientific research and actions and projects in the field (Ellen MacArthur Foundation 2016).
Furthermore, the regions Flanders and BCR host 17 insulating glazing manufacturers (members of Verbond van de Glasindustrie VGI) (Verbond van de Glasindustrie 2019) and two flat glass recyclers. The regions play an important role in the international sustainable management of today’s end-of-life flat glass, especially for the export and import of recycled flat glass (cullet). Almost half of the recycled flat glass in Flanders—123 tonnes out of 295 tonnes—was imported from neighbouring regions in 2015 (Debacker et al. 2021).
With the insights of this exploratory research, it is possible to explore under which conditions the circular practices can be replicated and upscaled in Flanders and BCR; but also, which other niche practices (from abroad) could find ground in the Flemish and Brussels region. Although the article focuses on the practices in Flanders and BCR, the insights are presented in this paper as a basis to further question construction practices in other regions in Europe and beyond. For example, inspirational circular practices and the related barriers and opportunities might be of interest to other regions with similar climate and material scarcity challenges.
First, section two (cf. 2) explains how the studies and interviewees were selected (cf. 2.1) and how the data was analysed (cf. 2.2). Then, in section three (cf. 3) the key results of the reviewed papers, reports and interviews are highlighted. An overview is given of the conventional practices—quantities of waste, origin and collection of waste, and their application—for both pre- and post-consumer flat glass waste (cf. 3.1). Then, the encountered circular practices for managing pre- and post-consumer glass are discussed and missing circular practices are identified (cf. 3.2). Next, section four (cf. 4) discusses, per theme, the barriers that hinder these circular practices, as well as the opportunities that are created. Last, a conclusion and further research possibilities are given (cf. 5).
Throughout this paper, the terms insulated glazing and insulating glass unit are used interchangeably. Insulated glazing refers to a more overarching term, e.g., vacuum glass unit and insulating glass unit (IGU), while IGU refers to the system of assembly whereby two or more glass panes are separated by a spacer bar and a cavity filled with insulating gas. The study has a specific focus on the IGU, and more specifically on the glass of this product. The other components—the spacer bar, coatings or films, and the seals—are not considered.
Method
Data gathering
First, to create a representative, general overview of the flat glass management practices in Flanders and Brussels, literature material was selected based on three criteria. The first selection criterium was “relevant for the Flemish and Brussels building sector”, which relates to the location context of this study. For instance, several included papers conducted a material flow analysis at a global scale (Butler and Hooper 2019; Westbroek et al. 2021), at European scale (Hestin et al. 2016) and at a local scale (Debacker et al. 2021; Dubois et al. 2013).
The second selection criterium was “circular valorisation strategies for flat glass”. Included papers focus on specific circular alternatives like closed-loop recycling (DeBrincat et al. 2018; DeBrincat and Babic 2018; Glass for Europe 2013; Rodriguez Vieitez et al., 2012; Wittekoek 2020), repair practices (Mohamed 2020; Souviron 2021), and reuse practices (Gorgolewski 2008; Hartwell et al. 2021), and/or highlight pioneering projects (Jackson and Lanzarotto 2021; Bowers and King 2013).
The third and last selection criterium was “recent, up-to-date research and products”. Consequently, the selected papers and reports were published in 1999 or later. The limit of 1999 relates to the introduction of the EU Landfill Directive in 1999. It introduced stringent technical requirements that resulted in a significant reduction in the amount of waste ending up in landfills. Furthermore, Hartwell and Overend (2020) illustrate “that at 25 years, it would be expected that at least 86% of IGU units would fail to meet their initial functional performance requirements”.
Second, interviews are conducted with experts in circularity and with network actors active in circular practices of flat glass management in Flanders and BCR. The aim of the interviews is to collect the qualitative experiences of the actors and their practices and to obtain a thorough understanding of the main barriers and opportunities they encounter when implementing circular strategies for flat glass. The interviews were semi-structured, with a common set of predetermined questions focussing on:
- The role and responsibility of the interviewees in the flat glass supply chain;
- The existing (non-)circular operations, processes, and interactions of the interviewees in the supply chain;
- And the experience of the interviewees with the implementation of circular valorisation strategies (e.g., barriers and opportunities).
The interviews took place between November 2019 and October 2021 and each interview lasted 45 to 60 min.
An overview of the major network actors of the current flat glass supply chain (for the IGU specifically) and the material and intangible flow between them is mapped in Fig. 1. From these major actors, only the network actors with experience in implementing circular practices are targeted: three flat glass or insulated glazing manufacturers active in glass recycling, three glass recyclers or collectors for recycling, one architect with experience in glass recycling, two deconstruction contractors with expertise in disassembly for reuse or repurpose, and four researchers on glass sustainability. In total 13 network actors and researchers were interviewed. Ten of the targeted network actors are based in Belgium and three in European countries outside Belgium, namely France, the United Kingdom, and the Netherlands.
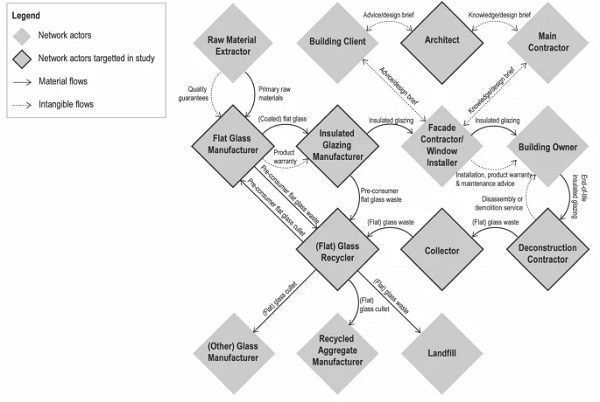
Analysis procedure
The data emerging from literature research and the interviews was analysed through qualitative coding analysis, which consists of categorising data in themes (i.e., coding), constant comparison and exploring the links between those themes. By comparing the results, a comprehensive understanding of the key barriers and opportunities could be created. An early estimate of themes was set up based on the draft notes made during the interviews. Then, the coding process was done manually by highlighting the data and linking them to the most appropriate theme. The themes were further adapted during this process. This resulted in five themes: organisation, (material-) technical aspects, legislation, financial aspects, and mentality and knowledge. The results were then compared to create a comprehensive understanding of the key barriers and opportunities encountered.
Management of end-of-life IGUs in Flanders and BCR
Mohamed (2020) points out that IGUs are mainly being replaced due to failure of the assembly (e.g., seal failure) even though the technical life of the glass sheets themselves has not been reached. Due to the degradation of the primary seal, the insulating gas in between the glass sheets can escape and external air can enter the cavity. This results in a significant drop in thermal performance of the IGU and it might lead to condensation issues between the glass panes, lowering the transparency of the window (Ibid.). Hartwell and Overend (2020) mention a predicted service life of only 25 years for IGUs.
In general, the end-of-life IGU can be categorized into two types of glass waste: pre-consumer and post-consumer flat glass waste. The former is “waste glass resulting from the manufacturing of products that contain glass as one of their components, and which leaves the specific facility where it was generated, becoming waste but not reaching the consumer market” (Rodriguez Vieitez et al., 2012). Examples of pre-consumer flat glass waste are offcuts and pieces from defective manufacturing or surplus manufacturing. The latter is “waste glass originated after the use of the glass products at the consumer market”, for example from renovation, deconstruction, or demolition of a building (Ibid.).
Besides, a distinction is made between internal and external flat glass waste, which indicates ownership of flat glass waste by the flat glass producer (internal) or an external company, such as an independent insulated glazing manufacturer or contractor (Dubois et al. 2013). Looking through the lens of construction practices, the analysis below will show that this ownership is deciding for the further reapplication of the waste (cf. 3.1).
Conventional practices: business-as-usual waste management
Pre-consumer flat glass waste from IGUs
Quantities per origin and application
The Sankey diagram in Fig. 2, from a recent study conducted in the context of the Flemish Living Lab on circular construction (Galle et al. 2019), shows that pre-consumer flat glass waste—which amounted to 92 kt in 2015—follows a circular path into recycling and reuse. Most of the pre-consumer flat glass waste (57 kt)—consisting mainly of internal waste—is re-applied to high-value applications like closed-loop recycling (56 kt or 61%) or reuse (1 kt or 1%) (Ibid.). The other 35 kt (or 38%), mainly external pre-consumer waste, is open-loop recycled to other glass applications, e.g., container glass, glass wool insulation or foam glass (Ibid.).
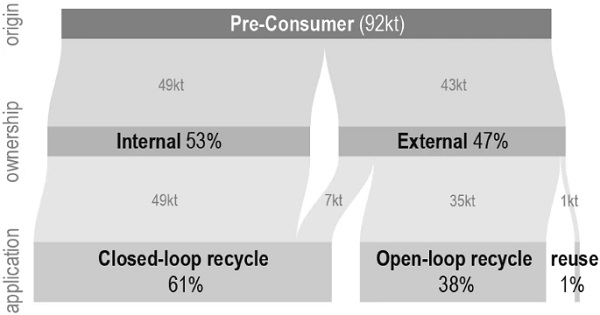
Collection and applications
The interviews with recyclers and collectors show that four pre-consumer glass flows can be distinguished—based on how the glass is collected and brought to the recycler—for the recycling process: monolithic glass, laminated glass, insulated glazing, and mixed glass.
The first flow, monolithic glass, refers mainly to the collected internal waste originating from the manufacturing process (e.g., melting and cutting). This glass is unprocessed, i.e., without films or spacers, and is also known as annealed glass. According to the interviewed recyclers and manufacturers, this flow is typically reintroduced as a secondary raw material to manufacture flat glass.
The second flow refers to the collected laminated glass waste. This is mainly generated during the processing of annealed glass into laminated glass. Laminated glass is a type of safety glass that contains a polyvinyl butyral (PVB) interlayer between two or more glass panes (DeBrincat and Babic 2018). After removing the PVB interlayer and separating the glass panes with a pre-treatment, the interviews with recyclers and manufacturers indicated that this flow is generally closed-loop recycled to flat glass.
The third flow, insulated glazing, originates from order surpluses or damage during installation or transport of the panes. The interviews with flat glass recyclers and manufacturers stress the importance of not damaging the spacer bars of the IGU during collection. These spacers bars often contain metals, such as nickel sulphide, that need to be removed carefully prior to the recycling process (Debrincat et al. 2018). Nickel sulphide inclusion can cause spontaneous breakage of glass after manufacture and toughening processes (Kasper 2019). According to the interviewed recyclers, this contaminant cannot be detected with the current infrastructure of the recycling plant. Consequently, the interviewed flat glass manufacturers are not willing to take the risk and do not accept this flow for closed-loop recycling. Instead, this flow is typically open-loop recycled to container glass, glass wool insulation or foam glass.
The last flow refers to a combination of the above-discussed collected flows: laminated glass, non-laminated glass, insulated glazing, and depending on the case, sometimes mixed with other building materials (e.g., other types of glass, stones) from the installation process. One interviewed recycler mentioned that with the current infrastructure at the recycling plants, it is not technically or financially feasible to separate them. Accordingly, this fraction is open-loop recycled to container glass, glass wool insulation or foam glass.
Post-consumer flat glass waste from IGUs
Quantities per origin and application
Debacker et al. estimate that approximately 80 kt of post-consumer flat glass waste was collected in 2015 in Flanders. Approximately 22 kt through the advanced selective deconstruction method, and 58 kt through the minimal selective deconstruction method. The first method implies the separate collection of wood, soil and stones, mixed stone waste, mixed residual waste, roofing, rigid plastics, plasterboard or gypsum, and glass waste (Debacker et al. 2021), while the minimal selective deconstruction method only includes the separate collection of four fractions: wood, soil and stones, the mixed stony fraction, and the mixed residual fraction (Ibid.) (Fig. 3).
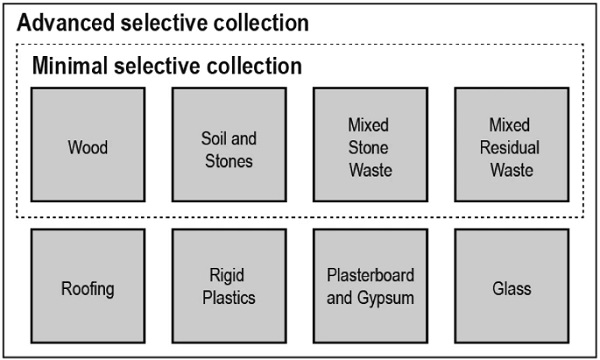
Only a small fraction, approximately 21 kt (27%) of the collected post-consumer flat glass in Flanders, is open-loop recycled to container glass (e.g., jars, bottles, etc.), glass wool insulation or foam glass (Debacker et al. 2021). The majority of post-consumer flat glass waste—which amounts to 59 kt (73%)– ends up in low-value applications (Ibid.). Multiple studies on a regional Flemish level (Dubois et al. 2013), and European level (DeBrincat and Babic 2018; Glass for Europe 2013; Hestin et al. 2016) confirm that post-consumer flat glass waste is almost never recycled, reused or repaired.
Instead, in Flanders, about 1 kt ends up (optionally through incineration) in landfills, while 58 kt (72.5%) is downcycled to low-value applications. More specifically, the glass waste is used as filler in recycled aggregates to produce concrete (e.g., for applications such as road constructions, foundations, pavements, etc.) (Debacker et al. 2021; DeBrincat and Babic 2018; Dubois et al. 2013; Glass for Europe 2013; Hestin et al. 2016; Nodehi and Mohamad Taghvaee 2022). The Sankey diagram in Fig. 4 illustrates the post-consumer flat glass flow for Flanders per origin, collection method, and application, based on Debacker et al. (2021).
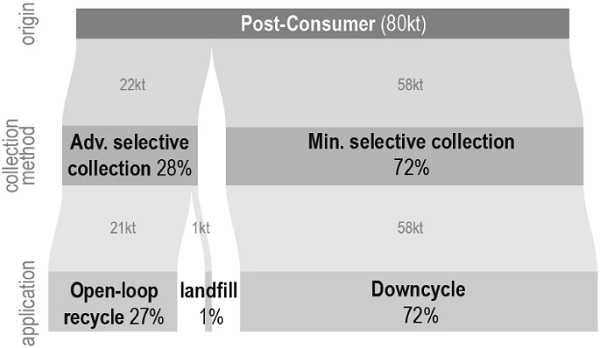
Collection and applications
According to Debacker et al. (2021) and confirmed by the interviewed deconstruction contractors, the minimal selective deconstruction method is typically used for partial or complete demolition of buildings in small-scale projects. This results in the non-selective collection of flat glass. The interviewed deconstruction contractors explained that the flat glass is crushed together with the mixed (stony) fraction during the minimal deconstruction method. This fraction is then sent to a recycling centre, where the most valuable materials (such as aluminium frames) are sorted out.
However, the interviewed recyclers pointed out that it would be extremely costly to sort out the glass from the waste stream when it is crushed and mixed already. The contaminated batch is typically downcycled (Nodehi and Mohamad Taghvaee 2022; Rodriguez Vieitez et al., 2012). However, only moderate volumes of waste glass can be absorbed with downcycling because the flat glass waste acts as an impurity in the aggregates (Debacker et al. 2021; Heriyanto et al. 2018). These are thus low value, non-circular material streams and cannot be recycled again at their end-of-life. Accordingly, they are not considered circular or sustainable processes (DeBrincat & Babic, 2018).
According to Debacker et al. (2021) and the interviewed deconstruction contractors, the advanced selective deconstruction method is typically used in large-scale renovation or demolition projects or sites that include a large amount of flat glass. Selective collection of glass is the result of advanced selective deconstruction methods. However, the interviewed recyclers mentioned that flat glass is often mixed with other types of glass, like glass ceramics or glass wool insulation (Dubois et al. 2013). Furthermore, often other contaminants, such as stones and metals, end up in the glass container as well. Figure 5 shows a contaminated glass container at a typical Brussels site where the glass façade of an office building was demolished. This fraction is typically open-loop recycled to produce i.a. container glass, glass wool insulation or foam glass (Debacker et al. 2021). In some cases, fractions are so contaminated (e.g., by the metal-containing spacer) that it ends up in landfill (Ibid.).
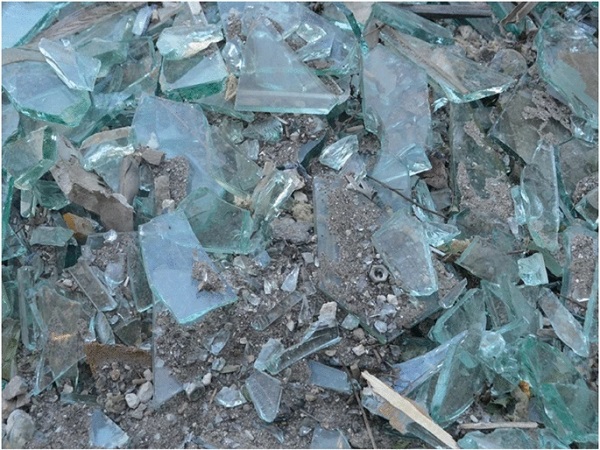
Circular practices: sustainable waste management
While some circular strategies are already part of the business-as-usual (e.g., closed-loop recycling an open-loop recycling), most of the (post-consumer) end-of-life IGUs are still managed in an unsustainable way. Based on the interviews and literature study, this section highlights the circular (niche) practices for end-of-life IGUs already present in Flanders and BCR. Furthermore, additional circular practices are discussed which are now absent in Flanders and BCR as well as the circular practices that are already implemented in pioneering projects outside Flanders. Figure 6 explains the four considered circular strategies—adapted to end-of-life IGUs after Potting et al. (2017)—and their actions—as discussed in the interviews with network actors.
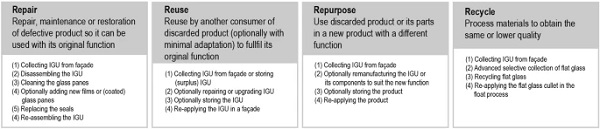
Existing circular practices in Flanders and BCR
Reuse of pre-consumer IGUs
Besides the closed-loop and open-loop recycling practices of collected pre-consumer glass (cf. 3.1.1b), the reuse of pre-consumer flat glass was pointed out as an alternative practice in Flanders (Fig. 2). Practically, this implies the reapplication of brand-new IGUs that are discarded due to for instance surplus production or incorrect orders.
The environmental impact or benefit of the reuse strategy is mapped by Debacker et al. (2021) and is illustrated per application in euro per tonne in Fig. 7. After the MMG monetisation method (OVAM 2018), the outcomes clearly show the environmental benefits of reuse compared to the environmental losses of downcycling, landfill, or incineration. However, the reuse of pre-consumer IGUs represents only one percent of the total collected pre-consumer waste (cf. 3.1.1a).
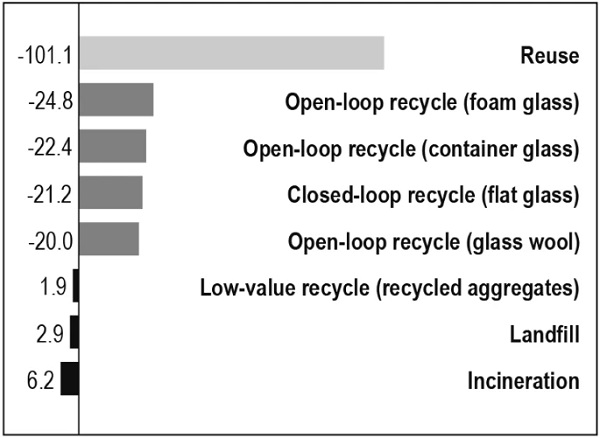
Repurpose of post-consumer IGUs
One of the interviewed deconstruction contractors shared that they sometimes reclaim IGUs from a building’s façade to repurpose them into furniture, partitioning walls, doors, greenhouses, winter gardens or verandas. This intervention, however, can require space to store and remanufacture the IGUs. An example from practice, found in vulgarizing publications, is the construction of Number Nine Studios in Gentbrugge. In this project, a double-glazed unit was found on-site and was repurposed as an indoor partitioning wall. The load-bearing structure was adapted during the design phase to the size of the reclaimed window (Opalis 2011).
Furthermore, the feasibility to repurpose reclaimed IGUs into outdoor purposes has been extensively studied by Junger (2019). Junger focused on repurposing the bronze-tinted glazing of the World Trade Centre Towers in Brussels North Quarter into urban greenhouses. Since the glazing of the 1970s does not correspond to current passive standards, an alternative use was sought in which the glazing could be still used to form a thermal barrier or buffer space between the outside and the heated living space. Her research showed that repurpose in greenhouses is feasible in this case if a certain level of remanufacturing was performed (Junger 2019). Yet this study remained theoretical and was not executed in practice.
Open-loop recycling of post-consumer IGUs
Open-loop recycling (i.e., to glass wool insulation, container glass and foam glass) is already—but only marginally (27%)—present in the conventional practices (cf. 3.1.2b) (Fig. 4). During the interview, the architect mentioned a large-scale project in which they had set the ambitions to closed-loop recycle the IGUs. However, one of the interviewed manufacturers (also involved in the project) explained that these IGUs could not be accepted for closed-loop recycling due to the specific colour of the glazing. Since the production process of container glass has less stringent quality-requirements, the IGUs were instead open-loop recycled to container glass. Practically, the IGUs were one by one removed from the building and collected in a separate glass container, which was then brought to a recycling centre.
The advantage of open-loop recycling is that high concentrations of flat glass waste can be recycled into glass wool insulation and container glass, respectively up to 90% and 60% of the raw materials (Dubois et al. 2013; Rodriguez Vieitez et al., 2012). This is particularly interesting for lower quality cullet because less pure cullet is needed compared to the production of flat glass (cf. 1.1). However, it is important to keep in mind that glass wool insulation is an application which is currently not recyclable again (Debacker et al. 2021; Rodriguez Vieitez et al., 2012), while container glass, on the contrary, is fully recyclable. The European container glass recycling rates are the world’s highest, averaging 73% (Heriyanto et al. 2018).
Missing circular practices in Flanders and BCR
Repair of post-consumer IGUs
The repair of glazing was once common practice, but this changed since the breakthrough of the IGU in the 1970s. New failure issues arose with the IGUs, such as condensation issues and a lowered thermal performance. Souviron (2021) explains “cleaning and repair are almost impossible due to the sealed assembly of the two panes, which prevents their separation and thus access to the interior cavity. The replacement of units then becomes necessary, being also favoured by government energy policies and by the glass industry itself, as both promote the use of new and more efficient products (for example, low-emissivity glass, argon insulation, self-cleaning coatings, ultra-clear glass, etc.)”. In this work, Souviron looks at several alternative techniques that circumvent the need to seal the glass sheets in the post-war period, however their use has remained marginal.
A more recent example of such an alternative technique is the theoretical work of Mohamed (2020), called the Re-seal Window. The weakest part of the IGU, the seal, is redesigned to increase the repairability of IGUs. In this design, the seal could be easily replaced every ten years so that the glass panes can have a life span of more than 100 years.
Today, repairing IGUs remains a niche market and is often only explored for heritage or monumental projects, such as the renovation of the Empire State Building in New York and One Triton Square in London. These cases show that glazing can easily be reclaimed for repair purposes. As it is often claimed about these cases, a local pop-up factory was set up to perform repairs of the damaged parts—the disassembling of the unit to clean the glass panes, replace the seals and add new coatings, coated glass, or films. After the repairs, the glazing was re-installed in its original façade (Jackson and Lanzarotto 2021; Koch 2013).
The repair strategy has many advantages as it prevents the replacement of glass units by interventions that extend their service life. Therefore, it allows savings in raw materials and energy (e.g., during production processes) and reduces waste generation.
Reuse of post-consumer IGUs
Although the reuse strategy for façade systems and components is very well documented (Beurskens and Durmisevic 2017; Gorgolewski 2008; Hartwell et al. 2021), the reuse of post-consumer IGUs is lacking in practice. The interviewed deconstruction contractors mention that there is currently no market demand for reclaimed IGUs for reuse. Souviron et al. (2019) point out: “reuse of windows are more or less anecdotal, partly because the technical obsolescence of the product recovered, but also because of damage caused by disassembly and transportation.”
Closed-loop recycling of post-consumer IGUs
Despite the lower environmental benefit of closed-loop recycling compared to other open-loop processes (see Fig. 7), two interviewed researchers and deconstruction contractors advice to give priority to closed-loop recycling for two reasons. First, in the open-loop recycling processes the flat glass downgrades irreversibly to another product (cf. 1.1). Second, the percentage of flat glass cullet that is used as secondary raw material in the float process—now reaching 30%—can be increased if also post-consumer flat glass waste would be accepted (DeBrincat and Babic 2018). However the demand of flat glass manufacturers for high-quality flat glass cullet, the supply seems not to be met.
A unique example however shows that closed-loop recycling of flat glass is feasible. The Lloyd’s project in London was the first to input such an enormous amount of post-consumer glass—approximately 123 tonnes—into the float process (Bowers and King 2013). Bowers and King (2013) explain: “This represented a high degree of environmental responsibility, as discarding such a quantity of glass would have been very wasteful.”
Barriers and opportunities
The above-discussed circular practices remain niches. In identifying the barriers and opportunities to scale up these practices, five central themes emerged from the cross-practitioners’ interviews and literature study: organisation, (material-) technical aspects, financial aspects, legislation, and mentality and knowledge. Figures 8 and 9 map, respectively, the encountered barriers and opportunities that were mentioned during the interviews per theme.
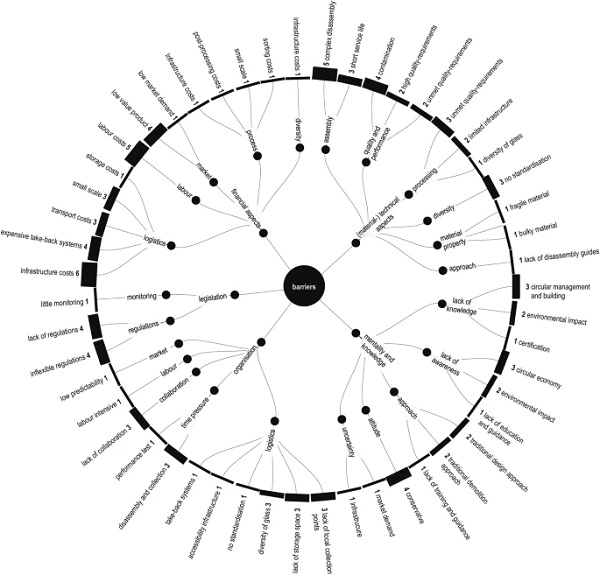
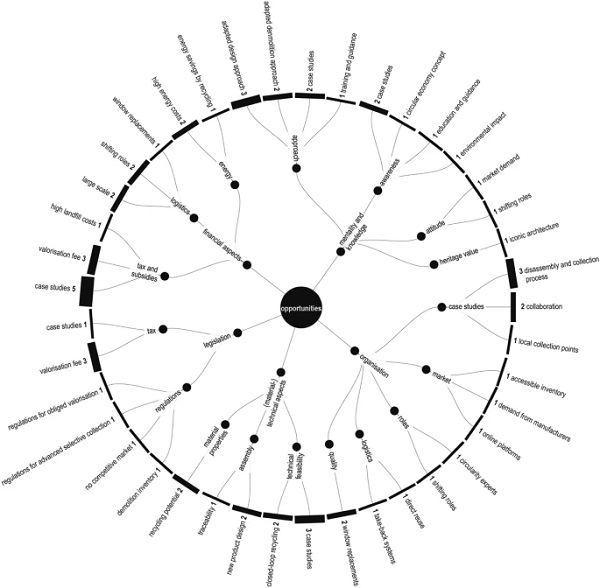
Organisation
Barriers
From the interviews and literature study, within the dispersed supply chain of IGUs, there is only limited collaboration between the different network actors. However, collaboration is key to valorise end-of-life IGUs. For instance, reclaim and reapplication of the materials can only be achieved when the construction team and deconstruction team collaborate; matching the potential reuse materials with the actual reclaimed materials and searching for a sales market.
Furthermore, several issues arise concerning the collection and reclamation of IGUs. First, the interviewed deconstruction contractors complain that often insufficient time is planned to realize this. Second, the interviewed architect claims that often there is a lack of storage space to store the reclaimed IGUs or to place a flat glass container for selective collection. Third, the logistical feasibility depends on the scale of the project. For instance, in smaller projects, the quantities of flat glass collected are often not enough to fill a full flat glass container (Debacker et al. 2021; Dubois et al. 2013). And last, interviews with one researcher and recycler indicate that, in Flanders and BCR, the distance to the stone processing plant is often shorter than that to a glass processing plant, which makes it logistically and financially more interesting for demolishers to mix the flat glass waste with the stony fraction (Debacker et al. 2021). This implies that a network with local collection points for flat glass is lacking in Flanders.
Opportunities
The two mentioned case studies illustrate that logistical barriers can be countered in some cases, e.g., by creating a pop-up factory to remanufacture and store the reclaimed insulated glazing nearby the site (cf. 3.2.2a) (Jackson and Lazzarotto 2021). Sharing the knowledge of these case studies will highlight how they deal with logistics and timing in their project. Often, for instance, space can be reserved on-site (in large-scale renovation or (de)construction projects) or nearby the site (e.g., available public storage) with minimal effort.
The interviewed flat glass manufacturers, recyclers and collector mentioned how the foundation of Vlakglas Recycling Nederland in The Netherlands counter logistical barriers with a recycling fee for imported and produced insulated glazing (Wittekoek 2020). The initiative allows contractors to deposit flat glass waste free of charge at local collection points, therefore, making it easier for the contractor to choose advanced selective collection. It was the collaboration of network actors that led to a successful up-scaling of the logistical system for recycling flat glass. The interviewed flat glass manufacturers explicitly indicated that they were open for such collaboration and participation in a similar system.
Furthermore, the interviewed deconstruction contractors explained how they underwent a shift of their initial role (from demolishing IGUs—initial role—to reclaiming and reselling them—new role) to contribute to a circular economy. This allows the actors to act within different stages of the life-cycle, e.g., product, construction and end-of-life phase of the IGU. For instance, by introducing take-back systems, a logistical system that the interviewed manufacturers want to experiment with further. In fact, to take back material for i.e., recycling, has many benefits for the glass producer, like lower energy consumption and cost, and savings in virgin materials (cf. 1.1).
(Material-) technical aspects
Barriers
In the interviews with the recyclers and researchers, the complex disassembly due to the irreversibly glued connections was raised as a difficulty for valorisation –disassembly is required for recycling and repair, and optionally reuse and repurpose. Besides, the disassembly of an IGU is a dangerous task because of the material properties of glass; it is fragile and breaks easily.
The limited technical service life of the IGU is mentioned by the architect and contractors. The gradual drop in thermal performance leads to questions about how the quality and performance of such a second-hand product can be guaranteed. The quality needs to be reassessed, yet an approach to validate the performance of reclaimed IGUs is not yet developed among network actors, nor in policy implemented.
Opportunities
The technical end-of-life possibilities of IGUs are promising: once disassembled the glass panes are fully recyclable and can be re-assembled for reuse or repurpose. Case studies like the renovation of the Empire State Building, Lloyd’s building, One Triton Square, etc., illustrate that with tailor-made infrastructure, the disassembly, remanufacturing, and re-assembly of end-of-life insulated glazing is technically feasible, despite the complex assembly. More research and experiments are needed into the remanufacturing possibilities of end-of-life IGUs and the corresponding quality and performance of the repaired, reused, or repurposed product. Moreover, redesigning the IGU’s irreversible connections (cf. 3.2.2a) would facilitate the disassembly process significantly.
The interviewed deconstruction contractors stated that the reclamation of IGUs from buildings is facilitated by window beads (present at most window frames, such as PVC and metal window frames). This reversible connection allows fast demounting.
Financial aspects
Barriers
A major bottleneck that the interviewed network actors encounter today is the financial feasibility of the circular strategies. The interviewed deconstruction contractors mention that labour costs for the advanced selective deconstruction method (e.g., reclamation, disassembly, and other interventions), and logistic costs for the selective collection (e.g., separate container, infrastructure, transport, and storage) are high in Flanders and BCR. Labour taxes are the highest in Belgium, the tax wedge for the average single worker reaches up to 52.6% (OECD 2022). In addition, Debacker et al. (2021) explain that “the price difference between primary and secondary raw materials remains too small […] to stimulate (advanced) selective demolition and separate collection.”
If not done manual, to repair, reuse, repurpose or recycle IGUs sometimes expensive techniques or infrastructure are needed (e.g., expensive tailor-made machinery for disassembly, expensive sorting techniques to sort out contaminants, etc.) An investment that the interviewed recyclers and deconstruction contractors are not willing to make because of the low financial value of flat glass. A financial incentive is thus missing.
Opportunities
The scale of a project can have a significant influence on logistical costs. Debacker et al. (2021) explain for Flanders and BCR: “the proportion of transport costs in relation to the total cost decreases by 19% for the advanced selective deconstruction of 23 houses instead of one house.” Advanced selective deconstruction, and so the selective collection or reclamation of flat glass waste, can be financially beneficial for projects containing large amounts of IGUs. To illustrate the feasibility to the industry, more project examples and initiatives from the actors are needed in Flanders and BCR. Charging a recycling fee, as successfully introduced in The Netherlands (Wittekoek 2020), can make circular strategies financially feasible on a large scale.
Legislation
Barriers
The interviewed researchers mention a lack of regulations for advanced selective collection of glass and for the implementation of circular strategies. For instance, for Flemish and Brussels’ deconstruction contractors there is no legal incentive to selectively collect or reclaim IGUs, besides the technical prescriptions for glass in recycled aggregates (PTV406) (COPRO vzw 2020). In addition, the interviewed architect complained about inflexible regulations for energy performance in buildings that make the implementation of reused materials, such as reclaimed IGUs (with no quality guarantee), almost impossible.
Opportunities
In Flanders and BCR, a demolition inventory must be carried out if a building is demolished. The main task of this demolition inventory today is to identify hazardous waste materials so that they can be removed from other building materials (Debacker et al. 2021). However, it does not mention how non-hazardous waste materials should be collected or if it is obliged to collect a non-hazardous fraction separately. One of the interviewed deconstruction contractors and researchers suggested that the demolition inventory could instead support the implementation of circular strategies. For instance, to identify the reuse potential and repair, repurpose, or recycling possibilities of end-of-life insulated glazing.
Mentality and knowledge
Barriers
According to the interviewed network actors, in general there is insufficient knowledge and awareness among network actors about the circular strategies and their implementation, especially concerning technical aspects. The traditional demolition approach—which refers to the minimal selective collection method—and more specifically the conservative attitude of most demolition companies, is pointed out as a barrier by the interviewed recyclers and manufacturers.
Furthermore, including reclaimed IGUs for reuse in a design requires a totally different approach than the traditional design approach (Beurskens and Durmisevic 2017). “Reclaimed materials do not show up at the right time, in the right amount or the right dimensions” confirms Gorgolewski (2008).
Opportunities
Some of the interviewed recyclers and all deconstruction contractors requested specific training for labourers and organisations. For instance, to educate them on how to collect and reclaim IGUs properly and safely. As sector federations, e.g., of the construction sector, glass sector, etc., already play a role in the conventional practices to give advice and sometimes workshops to network actors. This could be an opportunity to reach out to the network and share technical, logistical, and other knowledge to valorise end-of-life IGUs.
Mental and behavioural changes are needed among the network actors to valorise end-of-life IGUs. For instance, pioneering projecs show innovative design approaches for repurpose of reclaimed IGUs (cf.3.2.1b). Additionally, interviews with the network actors show that there is already some interest and demand to valorise end-of-life flat glass.
Furthermore, Debacker et al. (2021) advise to increase the research and knowledge on material streams on the part of government and policymakers, so that material streams can be better controlled, and strategic decisions can be substantiated.
Conclusion
With a specific focus on the end-of-life stage of IGUs, this exploratory study gives, for the first time, an overview of Flemish and Brussels conventional and circular construction practices with corresponding barriers and opportunities.
First, following other studies, the priority must be set on how to valorise post-consumer IGUs, hence, circular strategies are marginal in the Flemish and Brussels conventional construction practices. Yet, at a small scale, the circular strategies repurpose and open-loop recycling of end-of-life IGUs are being successfully explored. In contrast to post-consumer IGUs, pre-consumer flat glass waste from IGUs is already completely recycled or reused at high-value.
Second, repair, reuse and closed-loop recycling are circular strategies absent in Flemish and Brussels construction practices. However, pioneering projects from other regions illustrate the viability of repair and closed-loop recycling of post-consumer IGUs. Reuse remains unexplored.
Third, the barriers and opportunities to the up-scaling of the circular strategies are identified per theme by interviewing 13 network actors and researchers. In general, the main organisational barriers are limited collaboration between actors (e.g., between construction and deconstruction teams, and between recyclers and manufacturers), challenging logistics (e.g., lack of storage space to store reclaimed or collected glass, and lack of local collection points), and time and cost pressure that hinder the disassembly of IGUs. However, sharing knowledge from case studies can help facilitate the implementation of circular strategies in construction practices.
Also, network actors are experimenting with take back systems and role shifts to act within multiple life-cycle stages of the IGU. The material-technical constraints, specific to IGUs, are its complex assembly and uncertain quality and performance at the end-of-life. Redesigning the unit would facilitate this process, however, successful cases prove that these technical challenges can be surmounted. At a systemic, economic level, high labour, and logistic costs (e.g., disassembly is labour intensive, higher costs for storage and transport of reclaimed or collected glass, etc.) and expensive techniques or infrastructure to reclaim or process glass contribute to the lack of financial incentives for network actors in Flanders and BCR.
Large scale projects and legal financial incentives can reduce these financial challenges. In general, legislation for selective collection is missing and should be introduced, for instance in an updated, obliged demolition inventory. Further, sharing knowledge and providing training for labourers can change the conservative attitude of labourers and improve insufficient knowledge and awareness of applying circular practices among network actors.
Finally, the insights of this study—innovative niche practices, barriers and opportunities for the network actors, and cross-practitioner insights in ongoing practices—are the basis for further research in how to close the material loop for IGUs. For instance, which conditions are required to upscale or replicate current local niche practices; but also, how to bring other—currently absent—niche practices to the Flemish and Brussels region.
Data availability
The datasets generated during and/or analysed during the current study are not publicly available due to confidentiality reasons but are available from the corresponding author on reasonable request.
References
Acknowledgements
We would like to thank all the participating interviewees for their valuable input and feedback. This research was funded by Fonds Wetenschappelijk Onderzoek (FWO), Grant Number 1S20722N
Author information
Authors and Affiliations
Department of Architectural Engineering, Vrije Universiteit Brussel, Pleinlaan 2, 1050, Brussels, Belgium - Esther Geboes, Waldo Galle & Niels De Temmerman
VITO Transition Platform, Flemish Institute for Technological Research (VITO), Boeretang 200, 2400, Mol, Belgium - Waldo Galle
Contributions
The conceptualization, the outlining of the methodology, the original draft preparation and the making of the figures was performed by E.G; For writing—review and editing, E.G. and W.G. were involved. The study was supervised by N.D.T. and W.G. All authors have read and agreed to the published version of the manuscript. On behalf of all authors, the corresponding author states that there is no conflict of interest.
Corresponding author
Correspondence to Esther Geboes.