This paper was first presented at GPD 2023.
Link to the full GPD 2023 conference book: https://www.gpd.fi/GPD2023_proceedings_book/
Authors:
- Anthony Slack - CEO, eLstar Dynamics, Eindhoven, The Netherlands
- Romaric Massard - CTO, eLstar Dynamics, Eindhoven, The Netherlands
Abstract
Considering as definition for dynamic glass, a surface where a specific transmission can be modified and induced by any kind of force/energy such as heat, electricity, magnetic, light, etc. Dynamic glass can open many new possibilities and applications and a multitude of needs are there. All those applications require different properties and specifications. The main benefits from dynamic glass relate to visual light comfort, light control and spectral modulation, privacy modulation and the most critical nowadays energy savings. Economies around the world are now confronting the issue of climate change, with technology expected to be at the forefront of efforts to reverse the climate change that is threatening our very existence. The building sector alone accounts for 39% of the world’s carbon footprint1. Whilst dynamic/smart glass is estimated to contribute around 20%-30% energy savings within a building. Dynamic glass is a must to come, to combat climate change. How to democratize dynamic glass? How to ensure a limited impact on the planet? It must be simple and effective; low cost, and scalable.
1. Dynamic Glass requirements
Dynamic glass applications can be integrated in many different forms and markets. Non exhaustively, one can think about windows, doors, walls, partitions. All those products embodied in very different environments: building sector including residential and commercial units; automotive sector including cars but also trains, planes and boats; consumer electronic industries with the development of augmented reality devices and transparent displays.
All those products have their own specifics and requirements, but all will benefit dynamic glass integration: dynamic range, optical clarity and haze, visible light and heat modulation, color neutrality, transition speed, power consumption, scalability, cost and sustainability.
Within all those requirements and products, some specifications can vary from one extreme to another. As for example, a front window of a vehicle will require among other aspects an extremely high clarity while the windows of greenhouses a strong diffusion. Similarly, comparing residential windows, color neutrality is critical while specific coloring might be preferred for greenhouses. A front window of a vehicle will require a very high maximum transmittance while its sunroof can be limited to as low as 20% or below.
Some themes however remained constant for each market: high dynamic range, low costs, sustainable. This is even more profound when considering energy savings and the building sector. Climate change is the single largest economic influence of our time. The building sector alone is said to represent 39% of the world’s carbon footprint. Making it easily the biggest contributor to carbon emissions globally. Within those 39%, about 70% is due to the building operations (27% of global carbon emissions). Windows and skylights are the least efficient parts of the facade for thermal insulation. Dynamic glass can therefore play a major role to reduce carbon footprint.
It has the potential to reduce the energy consumption within a building by more than 30%, by controlling the energy allowed in via the windows. It has also the ability to dynamically adjust the light comfort within the building, as well as increasing the usable real-estate by eliminating the so called ‘curtain area’. Within a vehicle, it has the same ability to control inbound light and non-visible radiation (solar IR and UV), but also has the ability to dramatically reduce weight and frontal area. All of which contributes significantly to economy and range especially for electric vehicles. For automotive applications, especially cars, dynamic glass must be flexible to be applied on the numerous non flat glass surfaces present in those vehicles.
Finally addressing the electronic sector, the dynamic glass not only needs to achieve an extreme dynamic range (capable of dimming direct glare of the sun for augmented reality glasses) combined with non-curved surfaces but also require very low power consumption.
2. Dynamic glass technologies
There exist a number of technologies addressing this application area. The most dominant in use for architectural purposes is Electrochromic (EC), though LC (Liquid Crystal) and SPD (Suspended Particle Device) technologies also exist.
The key aspect of dynamic glass for architectural applications is that it should modulate a broad range of light, across both visible and IR spectrums. This is something that electrochromic technology does better than either LC or SPD. However, EC manufacturing requires unique manufacturing processes, and a relatively exotic materials set, and has severe limitations in switching speed and color neutrality. LC based technologies are only effective at modulating visible light, and have a limited dynamic range, meaning that typically multiple layers are required. The consequence of this is that products currently on the market have limited appeal, and are relatively expensive, selling for up to $1,500/m2.
Therefore, there is a very poor rate of adoption. However, with the introduction of new legislation, such as the Inflation Reduction Act (IRA) in the US, of which the Dynamic Glass Act[1] is a part, there is renewed demand and incentive for the large-scale adoption of Dynamic Glass. Especially, if it can be made more cost effective, and readily scalable. Further legislation is expected from the EU as part of the Energy Efficiency Directive (EED) and, more specifically, the Energy Performance of Buildings Directive (EPBD) aimed at making all new buildings Zero Emission by 2030 [2], as part of the European Green Deal. Yet there is very limited supply of EC technology, for example, with lead times of more than 1 year and, the cost of building additional capacity is proving a further roadblock to growth.
Considering the automotive market, SPD seems to better adapt to the conformity to nonflat glass required but suffers from high energy consumption and poor color neutrality. Additional to those historical technologies on the market, emerging new ones have appeared in recent years. Derivates of electrochromic ones are showing some evolution toward flexible substrate or with attempt to decrease the production costs using wet processing during the manufacturing. Sustainability of the materials used can remain a challenge. Two other novel approaches are considered: reversible metal electrodeposition and electrophoretic. Within the first approach, the window operates between transparent and reflective states.
Another approach consists in developing dynamic glass based on electrophoresis effects. With such devices, the optical performances are not solely due to the materials used but the device design has a strong impact. It is therefore logical that the dynamic window with the highest optical range reported up to date is produced within an electrophoretic light modulator (ELM). Electrophoretic modulators have strong competitive advantages such as high level of modularity to adapt to a wide range of products/applications, usage of eco-friendly and non-rare materials. Sustainability is a key factor to enable mass adoption of dynamic glass for carbon neutrality.
The other key aspects are the ability to produce high volumes and maintain the product at low cost. ELM technology has this potential by using already existing standard LCD factories. Fab lines, machinery, process knowledge are already proven for decades and can be adapted to produce dynamic glass. Currently this industry is mainly present in Asia. Economic arguments to transfer those competences and volumes to other regions in the world do yet exist, yet demand for domestic production of key technologies is changing this. Combining a standard display and dynamic glass production could be an enabler of local production in all continents and not only Asia.
3. The dilemma of optics and performance
Historical technologies such as electrochromic, LCD and SPD have in common the usage of non-structured surfaces and the needs of transparent electrodes such as ITO. Within the development of those technologies, the optical clarity is considered as a top quality. So, to create an optical effect, 2 approaches were considered: alignment of elongated non-uniform materials (SPD, LCD) or inducing a chemical reaction to alter the ability of the materials to absorbs light (electrochromic). The first two will therefore necessarily be limited in dynamic range as the absorbing materials are always present everywhere on the surface.
The second approach seems more beneficial but will be mainly affected by the speed of conversion which is then window size dependent. Indeed, the amount of electrons flowing to electrochemical materials is decreasing with the resistance of the ITO (visible edge effect with operating large windows). The current cannot be increased too high to not induce irreversible damage. To counteract this effect, a metal electrode grid structure was added in some electrochromic devices but as not optimized created optical distortions and other effects.
Considering now the emerging technologies, the commonality relies on the presence of patterned structure to enable the appropriate optical dynamic range. For both the reverse metal electrodeposition technique and the electrophoretic devices, metal grid structures are implemented to enable the optical effect. For ELM, the principle relies solely on the metal grid and spares the use of transparent electrodes which tends to provide a yellow tint in case of ITO usage.
It is surprising to note that emerging technologies contain patterned metal on their surface. It is a sign that despite the efforts to reinforce the optical properties of the historical technologies, achieving the appropriate performance cannot only be thanks to materials development but should also benefit from the design and engineering of the cell structure.
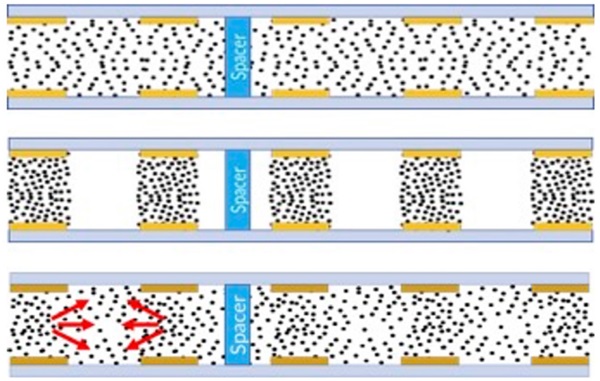
4. On the quest of autonomy
Dynamic glass is part of two worlds: the glass and the display industries, the building and electronic sectors. One of the challenges of dynamic glass is to ensure cooperation between those two industries. As an example, installing windows and plugging them to the grid are two distinct jobs lead by different professions. Installation warranties are therefore problematic to address as both entities are interdependent technically but not legally. Considering the fragmentation of the building industry, this has a significant negative impact on mass adoption of dynamic glass. In that sense, electrochromic by being bistable is limiting the need for power.
Nonetheless, the windows still need to be plugged and the issue remains despite the low power capabilities. Resolving that challenge is only consistent if the dynamic glass is autonomous and does not need to be grid powered. It is an essential first step to enable mass window retrofitting and can be seen as a first required step for dynamic glass mass adoption. It is also quite certain that in time, industries will organize themselves to enable plugging the windows but at start dynamic glass needs to adapt to existing habits and disciplines.
To achieve this, dynamic glass powered by solar cells may be seen highly advantageous. Multiple approaches can be followed. Adding standard solar cells to the frame might be worth considering especially with electrochromic devices. Indeed, adding the solar cells in the frame not only bring constraints to the design but do not scale in size. The larger the window, the lower the relative amount of electricity produced will be. To counteract this, transparent photovoltaic solutions are developed. Usually, those technologies convert the UV and nearIR light into electricity. Some of them are limited in range of dimensions due to the inherent low transmission of the window materials for UV and infrared (here by the transmission within the glass from the center of the window to its edges).
Irrespective of the electricity efficiency that will be lower compared to standard photovoltaic cells, those transparent photovoltaic technologies are usually impacting the transparency and carry some optical structure and coloring. Historic dynamic glass technologies such as EC, LCD and SPD would benefit from the transparent photovoltaic technologies, but the combination will alter their performance. In the case of EC and LCD, the optical clarity will also be affected. If the additional photovoltaic technology is only 70%, this is an additional decrease of transparency on already limited dynamic glass ranges. An alternative approach to enable dynamic glass to be autonomous and therefore being mass market ready is to add the well-known nontransparent standard photovoltaic technologies to the dynamic glass. Indeed, by patterning those solar cells, they can become transparent.
The design of the pattern and the coverage of the surface are then key to its transparency. Of course, integrating such an approach with the historical technologies will severely impact their maximum transparencies. However, for the emerging technologies and especially ELM, the addition of photovoltaic function should be relatively easy. The solar stack can be patterned at the electrode location only and without any negative impact on the current optical performance. Moreover, as ELM is fully produced in standard LDC factories, adapting thin film photovoltaic solar cells is already part of the competences of such TFT lines. Therefore, creating autonomous ELM dynamic glass seems an ideal choice as it complies with the essential criteria to hit mass market: very high dynamic range, lower cost products, market ready production levels and sustainability.
5. ELM the ideal choice for mass market dynamic glass
ELM technology is based upon electrophoretic principles. Its current development relies on the simplest device architecture to minimize cost and, eliminate as many failure modes as possible. An electrophoretic ink is placed between 2 substrates. Metal electrodes are patterned on each of the substrates. By driving electric fields between the electrodes facing each other from bottom to top substates, the charged pigments (responsible for the dark state of the window) are displaced and grouped underneath the electrodes and therefore out of the field of view. The window becomes transparent.
By using this principle, it enables the highest dynamic range up to date going from about 0.1% to about 70%. For example, deeper dark states can be obtained with only design change by increasing the distance between the 2 substrates and compensate with higher voltages to maintain the electrical field level. This shows from a simple example the large adaptability of the technology to different product requirements.
Given the importance of the environmental contributions that Dynamic Glass is expected to contribute, it is important that any serious player in this sector be able to broadly modulate light of any wavelength. Especially, those sectors of the solar spectrum which contribute most the energy efficiency of the end application. ELM has significant advantages with this respect. Being pigment based, it is possible to imagine an electrophoretic system which can be tuned to modulate light across almost any wavelength profile. With such a broad variety of applications to consider, ELM is currently demonstrated with a broadband ink which can uniformly modulate light across a broad solar spectrum.
ELM is manufactured using existing display manufacturing techniques. This eliminates the financial risk of having to build new facilities, and makes use of well established, high yield manufacturing processes, that are already familiar when handling large areas of glass. The manufacturing process aims at a small set of existing manufacturing processes from the standard LCD manufacturing ones. The ELM concept is based upon simple array definition, with passivation layers, followed by assembly using conventional ODF facilities and processes. Cell uniformity has been achieved using a variety of standard techniques, such as ball spacers or photolitho spacers, as well as nano-imprinting. So, it is versatile and robust. Therefore, the entire process consists of <50% of the processes required for TFT-LCD, for example.
All based on design rules which any commercial facility can replicate with ease. Having such effective manufacturing basis is important for the wide-scale roll-out of the technology. In order to address the intended market fully, expectations are that dynamic glass modulators meet the necessary specifications, with a manufacturing cost of around $100/m2. The BOM (Bill Of Materials) for an ELM is also very different from that of a TFT-LCD. No polarisers or Colour Filters are required. So, with the ink contributing less that 10% to the BOM, the materials costs, as well as the processing costs, are estimated to be less than half that of a large TFT-LCD. Standard LCD factory are handling thin glass (<1.5mm), therefore it is essential to laminate ELM to thick glass to ensure mechanical robustness. Standard lamination likewise security glass can be applied. It was demonstrated using 4mm tempered glass with an interlayer of PVB. Optical performances are reported in Figure 3.

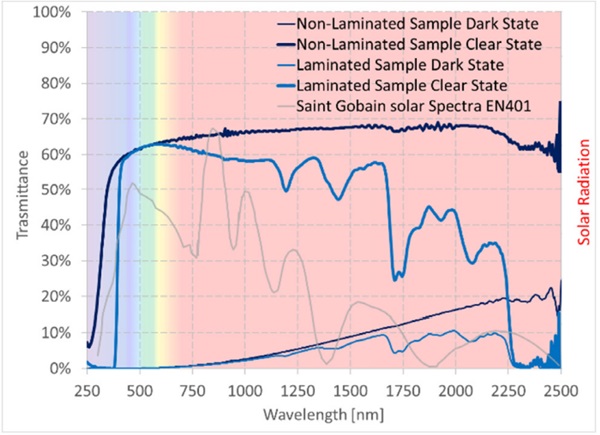
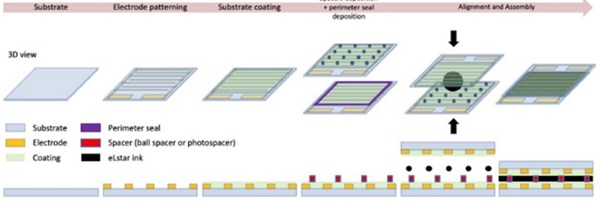
6. ELM an efficient technology to modulate energy
By integrating ELM into a double-glazing unit, its ideal position on the exterior side of the window. The energy absorbed by ELM in its dark state is then irradiated for some parts in the cavity of the double-glazing unit and reflected back by using an e-coating on the interior pane.
With such design, ELM can provide to the DGU a modulation of the g values from 4% to more than 49%.
7. Outlook of the integration of photovoltaic function with ELM
A thin Film photovoltaic stack can be added to an ELM and patterned at electrode locations. Those technologies are well known and range from amorphous silicon to CIGS or CdTe. An overall efficiency of 20% for those technologies will be considered for the evaluation described below.
Within the model presented here, a few assumptions were made. It is considering an office building with a large window façade area of 30m2 for a 80m2 room area. The model is considered to maintain a minimum of 300 Lux/m2 of office area. ELM maximum transparency is 70% resulting from a 30% metal coverage considered as the surface used for the photovoltaic function. The model uses the solar irradiation data from the photovoltaic geographical information system (PGIS) from the European Union [3] (based on 2020 year). Additionally, 4h of full transparency ELM per day is also considered here (covering evenings). Here are considered façade windows (vertical windows) with a south orientation (except for Sydney with a north orientation).
Over the year, ELM integrating PV stack can potentially be highly effective to maintain the ELM functioning and provide extra power to the grid when connected. In a city like Tampere in Finland, the sun exposure is not strong enough to cover the total need for the ELM, using this current model. In those regions, the window needs to be transparent for longer times (so consuming more power) where there is lack of sun to generate enough electricity. For all other cities evaluated, the number of cumulative days without enough power is no more than 2 days. Adding batteries to the window frame will ensure continuity of the window service, for example. Additionally, ELM technology is constantly being improved and its power consumption will continue to be optimized. Within the last year, the power consumption was already reduced by a factor 2. The current power short-fall is likely to be addressed in the future.
8. Future of Dynamic glass
As described here, requirements of dynamic glass are nowadays very wide and can be applied for many industries crossing buildings, automotives and electronics. Considering the carbon neutrality and energy savings challenge, dynamic glass consists of an ideal solution to optimize energy usage of buildings and vehicles. However current technologies on market have difficulties to scale to the demand and to integrate easily especially for buildings. Some of the merging technologies such as ELM can easily integrate extra functions without impacting their performance and cost ranges. Photovoltaic function is a particularly interesting one as it can make the technology easier to integrate and retrofit. With using state of the art photovoltaic technologies, self-autonomy of ELM can be achieved in most regions of the world, enabling strong energy savings.
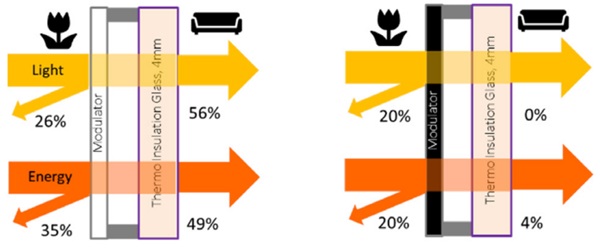
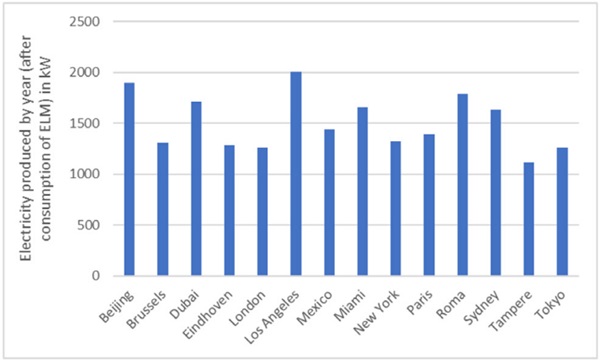
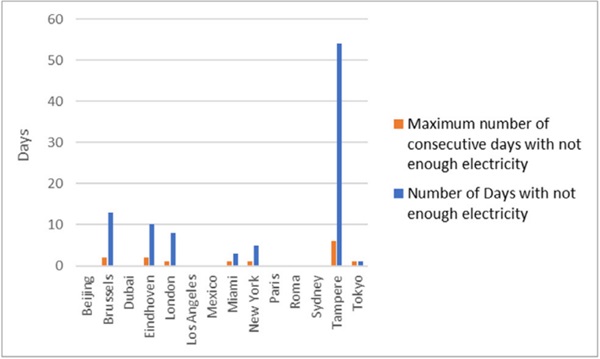
References
[1] S.1609 – Dynamic Glass Act (S.1609 - 117th Congress (2021-2022): Dynamic Glass Act | Congress.gov | Library of Congress).
[2] https://www.esgtoday.com/eu-proposesrules-requiring-all-new-buildings-to-be-zeroemission-by-2030/
[3] https://re.jrc.ec.europa.eu/pvg_tools/en/#HR