Source:
Challenging Glass 7
Conference on Architectural and Structural Applications of Glass
Belis, Bos & Louter (Eds.), Ghent University, September 2020.
Copyright © with the authors. All rights reserved.
ISBN 978-94-6366-296-3, https://doi.org/10.7480/cgc.7.4727
Authors:
Rebecca Hartwell, University of Cambridge
Mauro Overend, TU Delft
The built environment is under scrutiny to address environmental design challenges by considering a whole-life holistic approach that seeks reductions in operational emissions whilst simultaneously pursuing reductions in embodied emissions. Reduced embodied emissions can be found through the responsible sourcing of resources and re-use of materials in their highest obtainable value.
Laminated glass is used widely within the building industry for improving security and for reducing the risk of human injury from glass fracture. At present, few options exist for there-use and high-value re-cycling of laminated glass; it is most commonly disposed of in landfill or down-cycled into aggregate material due to its low perceived value at end-of-life. Whilst some efforts have been made to separate the poly-vinyl butyral (PVB) interlayer from glass in the automotive industry, such processes typically involve destructive crushing of the glass sheets and residual glass that is not at a high enough purity to be considered for re-cycling as cullet for visual glass applications.
A more effective removal of the PVB-interlayer through severing of the PVB-glass interfacial bonds, would allow flat glass from existing laminated glass panels to be re-conditioned to fulfil the latest functional requirements in architectural glass. Whilst the temperature and strain rate dependency of the PVB-interlayer material itself has been well-researched, the fundamental nature of the interfacial bonding between glass and PVB, governed by initial processing, is not well-understood.
This paper presents findings from the latest experimental research that explores methods of separating 2.9 mm x 100 mm x 150 mm flat glass sheets from a 0.38 mm PVB-interlayer for flat glass re-use and/or re-cycling of glass sheets at their highest obtainable value at end-of-life. A bespoke standardised test has been developed by the authors inspired by the compressive shear test, to evaluate methods for achieving separation between the interlayer and glass on a small-scale.
Tests were conducted at room temperature to evaluate the effects of varying displacement rate (0.125mm/min, 0.5mm/min and 1.0mm/min), humidity exposure and the influence of water infiltration along the bond line. It was found that the influence of humidity-ageing and water infiltration along the glass-interlayer interface during separation led to a greater proportion of delaminated area compared to the un-aged samples. The greater proportion of delaminated area was found to be a result of a mixture of the effects of a change in the bulk material properties of the interlayer and the intrinsic value of interfacial adhesion.
1. Background
Laminated glass provides the primary function of enhancing safety or security performance of glazing and at the same time improving the acoustic, UV and durability protection performance in single-and double-glazed units. These functions are achieved by combining the properties of glass with the properties of a polymeric interlayer.
A large variety of polymer interlayers have been developed including poly-vinyl butyral (PVB), ionomers, ethylene-vinyl acetate (EVA) and thermoplastic polyurethane (TPU). PVB interlayers account for around 70% of architectural laminated glass (Martín et al. 2020; Sandén 2015). Flat glass is laminated with PVB via a two-stage autoclave lamination process at high pressure and high temperature.
With an expected lifetime of 25-years and 97% of existing building stock considered operationally inefficient (BPIE 2017), there is an opening for a large amount of laminated glass becoming redundant in the coming decades. Industry has made efforts to recover non-laminated flat glass sheets to glass cullet for internal re-cycling. However, a lack of a fully established collection supply-chain, technical constraints in clean PVB-glass separation and high standards for visual glass production means that re-use and re-cycling options for laminated glass do not currently exist.
The principle of separating laminated glass for flat glass re-use relies on clean interfacial separation, sometimes referred to as delamination, between glass and PVB-interlayer. The understanding and characterisation of the mechanical separation of the rigid glass substrates from the PVB-interlayer is complex due to the combination of effects from the nature of the viscoelastic material behaviour of PVB and the rate-dependent nature of interfacial adhesion (Samieian et al. 2019).
Therefore, the optimal conditions for interfacial separation rely on an optimisation of various parameters including; the control of the material properties of PVB interlayer; prevention of cohesive failure within the PVB interlayer; protection of the rigid glass substrates and; modification to the interfacial adhesion as such to reduce the stress required to initiate delamination and reduce the likelihood of glass fracture.
2. Introduction
2.1. Research Programme
This study forms part of a wider research programme that aims to better address the end-of-life challenges and opportunities in façade design for re-use. Ongoing research developed by the authors intends to establish the behavioural barriers and opportunities, quantify the environmental benefits and effectively address the technical challenges in glass façade re-use. The use of adhesives and laminated glass forms one key technical challenge in the goal of component re-use.
This study will summarise existing efforts to promote re-use and re-cycling of laminated glass; outline the existing methods for measuring interfacial adhesion; discuss the known influences of external factors on interfacial adhesion; explain and describe the development of a new standardised test for evaluating interfacial separation and; through experimental work, identify the parameters that would help to optimise the process of PVB interlayer-glass separation at the end-of-life of laminated glass and therefore allow for flat glass re-use.
2.2. Existing Re-use and Re-cycling Potential of Laminated Glass
At present, adding non-separated laminated glass directly back to float glass processing is not considered favourable. PVB, which constitutes for around 10% of laminated glass sheets, is an organic material and as such bearing a strong reducing potential if introduced in the glass melting process (Kasper 2006). As such, re-use and re-cycling options for laminated glass are limited. Some existing efforts have been made to explore the separation of PVB from glass for re-cycling purposes. Table 1 provides an overview of the existing processes that are either established or in development.
Table 1: Existing methods for re-use and re-cycling of PVB-laminated glass and characterization of re-cycled PVB interlayer.
The main issues arising from the existing processes for recovering glass and PVB from laminated glass are that they often involve pre-crushing laminated glass leading to the recovery of a re-cycled content of glass cullet and/or PVB fragments. The existing established process for obtain flat glass sheets involves heating the laminated glass sheets which will initiate some degradation of the PVB (Anderson 2020). It has been found that recycled PVB can be used for laminated glass, however, it is greatly dependent on the reprocessing steps undertaken (Carrot et al. 2016). Recovered PVB can be transformed to secondary products, or burnt, together with other organic residues for energy recovery.
2.3. Interfacial Adhesion between Glass and Polymer Interlayer
Tupy et al. found that the adhesion between glass and PVB interlayers is based on Van der Waals bonds between the -OH groups of polymer chain and the -OH groups in glass (Tupý et al. 2013). The characterisation of the interfacial adhesion between glass and PVB has been investigated via qualitative and quantitative tests with a practical objective to gather knowledge on impact and post-fracture performance. However, the fundamental understanding surrounding adhesion between glass and PVB has been researched to a lesser extent.
Table 2 details some of the better-established tests that are well-detailed in the literature for investigating interfacial adhesion. These include the compressive shear test (Jagota et al. 2000), through-crack tension test, peel test (ASTM 2015) and the pummel test. The peel and pummel tests were adopted as industry standards partly because of their simplicity and convenience.
Table 2: Existing methods for measuring interfacial adhesion.
2.4. Influence of Strain Rate and Temperature on Interfacial Adhesion and Delamination
The material properties and behaviour of PVB are well-known to be substantially influenced by strain rate, level of strain, and temperature of the specimen at the time of testing; it has been characterised as a viscoelastic material that displays time-dependent nonlinear elastic behaviour (Hooper et al. 2012; Iwasaki et al. 2007; Weller et al. 2005; Zhang et al. 2015). Further, the ductility of PVB has been found to reduce as strain rate increases (Zhang et al. 2015).
There is a complex relationship between strain rate, temperature and interfacial adhesion, sometimes referred to as fracture toughness. Some known factors affecting interfacial adhesion include geometry, strain rate, temperature, modified mechanical properties of adhesive, intrinsic stress, defect structure, locus of failure (Ferrante et al. 1988). Existing studies that characterise interfacial adhesion not always decouple the bulk material behavior of PVB from the intrinsic value of interfacial adhesion between PVB and glass. Any method for initiating interfacial separation will require control of bulk material properties of the interlayer, intrinsic interfacial adhesion and glass substrate fracture.
Butchart & Overend quantitatively evaluated interfacial adhesion using the TCT method and found that values of interfacial adhesion varied with rate, however, noted that this was unclear as to the cause of variation was due to polymer behaviour, interfacial adhesion or a mixture of both (Butchart and Overend 2012). Jagota et al. investigated interfacial adhesion using the CST method and found that with progressively increasing imposed strain, a crack nucleates at one polymer/substrate interface at relatively small strains and extends stably with subsequent loading.
It was identified that there exists a critical strain, beyond which, crack growth is unstable,and the interface fails. The initial intrinsic of adhesion was found to havean effect on whether or not the critical value of stress at failure corresponds with interfacial adhesion or glass substrate fracture (Jagota et al. 2000; Sha et al. 1997). Further to PVB displaying a dependency on strain rate, Jagota et al. found that the intrinsic interfacial adhesion, consisting of contributions from bond rupture and a near-tip process zone, to also be rate-dependent (Jagota et al. 2000).
Elziere analytically and experimentally evaluated a limited intermediate range of temperature and applied velocity in which the delamination between interlayer and glass is symmetric and steady state in manner during the TCT. In this regime, the delamination force and strain reach a constant value both in time and space far from the delamination front. At higher temperatures or lower imposed velocities, the delamination fronts are no longer straight and start to undulate.
Propagation often stops after some time leading to the rupture of the interlayer. At higher velocities or lower temperatures, even if the delamination occurs as in the steady state delamination regime, the interlayer toughness is not sufficient which often leads to a brittle fracture of the interlayer. It was suggested that the plateau values reached by both the delamination force and strain are related to a complex combined effect of the interlayer rheology and of the adhesion. Further, Elziere suggested that reduction in the interfacial strength leads to a shift of the steady state delamination regime towards lower temperatures and higher velocities (Elzière 2016).
Samieian et al. found a similar relationship between PVB compliance and adhesion between the glass and PVB layer when investigating the post-cracked response of laminated glass with response to varying in the range of 0°C to 60°C. They found that maximum energy absorbed by the cracked laminate was found to occur at a temperature where there is a balance between the temperature-dependency of adhesion and compliance of the interlayer.
At lower temperatures, greater loads are observed as a result of an increase in the measured value of adhesion and the PVB being stiffer. At higher temperatures and lower adhesion, the PVB is more compliant. Provided the interlayer is stiff enough to transmit the loads required to propagate the delaminated front, a greater delaminated PVB length is formed. This results in the optimum temperature at which maximum energy was dissipated being between the high and low temperature extremes. Depending on the thickness of the PVB, this optimum temperature was also different (Samieian et al. 2018).
Similarly, Iswaki & Satofound that the mechanism of PVB deformation and crack propagation at the interlayer/glass interface in high tensile speed is different from that in low tensile speed but the fracture energy and fracture toughness under the low tensile rates are similar to that under the high tensile rate (Iwasaki and Sato 2006).
The reason for this phenomenon was considered as a result of an offset relation on the fracture toughness, which depends on the stiffness of the PVB and the critical loads for crack propagation, and the potential energies that depend heavily on the energy consumed by the deformation of the PVB sheets. Thus, it was found that the fracture toughness increases only a little with respect to the increase of the tensile speed and the fracture energies are approximately the same in various tensile speeds (Iwasaki et al. 2007).
The existing literature suggests that there is an optimum temperature and strain rate regime in which delamination occurs in a steady-state manner. However, this is subject to a range of factors including the existing intrinsic level of adhesion, behaviour of the PVB interlayer, specimen geometry and testing method. When evaluating these factors, a distinction must be made between what is commonly referred to as interfacial adhesion or interlayer-glass fracture toughness and the intrinsic value of adhesion.
2.5. Influence of Humidity and Water Infiltration at the Bond-line on Interfacial Adhesion and Delamination
There have been several works that have evaluated the effect of the wt% of moisture present in PVB interlayer during the manufacture of laminated glass (Bogatyrev et al. 1981; Froli and Lani 2011; Keller and Mortelmans 1999; Tupý et al. 2013). Water absorption of PVB pre-processing is found to be a problem because it can reduce the intrinsic interfacial adhesion between PVB and glass (Weller et al. 2005). Bogatyrev et al. found that adhesion increases exponentially with a decrease in the moisture content (Bogatyrev et al. 1981). Froli & Lani found that alternating the storage humidity of PVB foil to 45% and 60% resulted in a 15%-38% reduction in adhesion shear stress as measured by CST (Froli and Lani 2011).
Humidity and moisture have been found to have similar degradation effects on interfacial adhesion post-processing. Butchart & Overend investigated the influence of the presence of moisture on adhesion on specimens of PVB laminated between a layer of glass and a layer of flexible foil backing. The results show that in the direct presence of water, the force required to peel the interlayer from the glass was less than half of that recorded under dry conditions (Butchart and Overend 2013).
Chapuis et al. found that the values of shear stress and shear strain for PVB-laminated glass samples 25 x 25 mm2 drop considerably after exposure to damp heat (DH) conditions (85°C/85% relative humidity) for 70 hours. The peak stress was found to decrease by 50% alongside a 55% reduction in the peak strain. No plastic deformation was observed in the PVB samples and the elastic stored energy was found to decrease by almost 80% (Chapuis et al. 2014).
Belis et al evaluated the effect of humidity (50°C, 100% relative humidity) for 336 hours on laminated glass samples through CST and found that the adhesion level appeared to be only slightly reduced and that the stiffness appeared to increase with reference to the shear modulus at γ = 0.5 (Belis et al. 2007). Andreozzi et al found that humidity exposure (50°C, 100% relative humidity) for 809 hours had the effect of softening the dynamic response of PVB-laminated glass with the dynamic modulus, G0, decreasing with increasing weather time and some delamination phenomena observed. Andreozzi concluded that further investigations were required to separately analyse these features (Andreozzi et al. 2015).
2.6. Influence of Glass Fracture on Interfacial Adhesion and Delamination
Nourry found that the fracture of glass during laminated glass impact testing leads to interlayer delamination and stretching as highlighted in figure 7 (Nourry 2006).
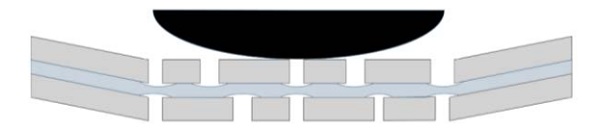
When investigating interfacial adhesion in compressive shear at high values of interfacial adhesion, there is a high chance that some glass substrate fracture will occur during loading. Additionally, glass failure at higher stresses can result in a higher density of glass fragments (Zaccaria and Overend 2012). If glass fracture occurs, it isimportant to consider its consequential effects on neighbouring regions of interlayer deformation and delamination.
2.7. Research Aims
The aim of this study is to develop a standardised method inspired by the compressive shear test to evaluate the parameters that are most effective at initiating full interfacial separation of PVB-interlayer from flat glass sheets for practical application.
The developed test will make use of external parameters including humidity exposure and moisture infiltration, with known influence on the bulk material properties of the interlayer and the intrinsic interfacial adhesion, to directly correlate their relationship with interfacial separation. The level of interfacial separation will be assessed with reference to the peak force and strain at failure, effective shear modulus at γ=0.5 and nature of glass fracture present, under the influence of humidity and moisture infiltration along the bond-line.
3. Methodology
3.1. Sample Preparation
24 samples of annealed float glass laminated with PVB supplied by Kuraray were cut and prepared from a larger laminated glass sheet. The samples were manufactured to EN12600 / EN1063 / EN1354 and were provided from Saint Gobain UK. The samples had dimensions of height x width: 100 ± 0.50 mm x 150 ± 0.50 mm and glass-PVB-glass thickness: 2.90 mm ± 0.05 mm – 0.38mm – 2.90 mm ± 0.05 mm. Details of the pre-test conditions of the samples are given in table 3.
Table 3: Details of pre-test conditions for 24 samples tested.
The humidity-aged samples were exposed to 95% relative humidity at 80°C in an environmental chamber for 504 hours. High temperature increases the water uptake within the PVB interlayer because the diffusion coefficient of water vapor in PVB becomes larger (Hülsmann et al. 2009). Before testing, the samples were removed from the environmental chamber and allowed to cool to room temperature. Samples were tested within no more than one hour of removal from the environmental chamber.
3.2. Experimental Setup
The laminated glass samples were tested using the testing jig designed by the authors and shown in figure 8 on a 150kN Instron in tension mode under displacement control. The applied force on the bottom face of substrate X, shown in figure 8(a,b) leads to an equal reactive force on the top face of the substrate Y, resulting in a shear deformation of the interlayer. The side faces of the laminated glass samples were unconfined.
Horizontal displacement of the outer steel box-sections is constrained by roller bearings to ensure that lateral stresses that arise internally will be transferred to shear stress. Displacement was measured using an external laser to ensure that only the relative displacement between the two glass sheets was recorded. Rotation of the jig during testing was neglected due to its negligible effect.
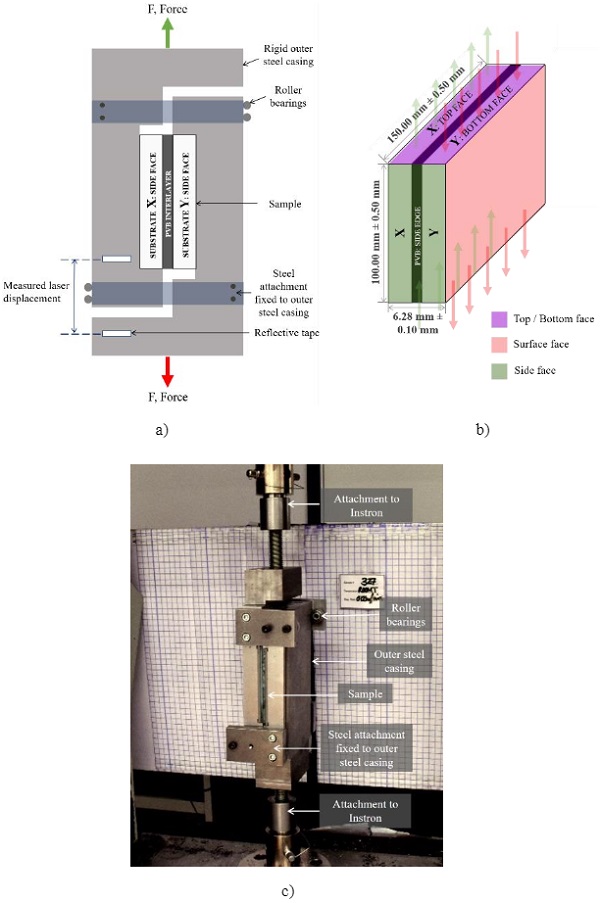
Depending on the intrinsic level of interfacial adhesion, increasing displacement leads to some degree of axial compressive stresses within the glass substrate. The resulting axial strain can be considered equal and negligible in the value for relative displacement. The axial compressive stresses along the height of the glass substrate induce transverse tensile stresses due to Poisson’s ratio effect (νglass= 0.22). Increasing displacement induces a shear stress within the PVB interlayer and shear stress along the interlayer-glass interface. Assuming a linear variation of the lateral displacements the average shear stress and resulting shear strain in the interlayer at small displacements is defined as:
Due to the nature of the experimental set up, the samples can continue to withstand increasing displacement despite glass fracture. Therefore, the effective area changes during loading due to glass fracture. As such, thevalue for shear strength sometimes referred to as the effective interfacial adhesion, will not been calculated within this study.
Shear modulus values will be evaluated and compared at small strains (γ=0.5). The samples were loaded under displacement control at varied displacement rates until the force dropped by 80% the test was manually suspended due to the authors observing of a relatively large load drop followed by a sustained plateau in the load which was attributed to stepwise crushing of the glass substrate at a rather than shear deformation of the interlayer.
3.3. Water Infiltration
In order to supply water to the bond line of the samples, an external water pump was set up to provide a continuous constant supply of water of 500ml/minute to the interface of one edge of the laminated glass samples as shown in figure 9.
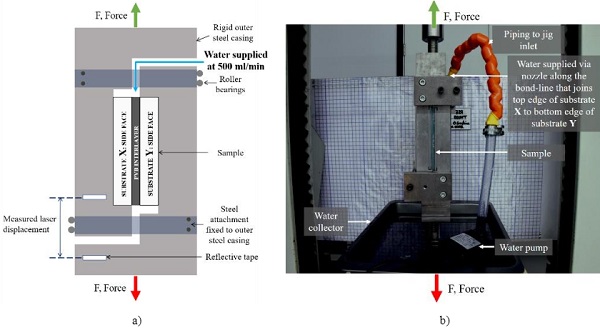
3.4. Testing Procedure and Observations
During testing, aural observations were made to listen for glass fracture. The side faces of the samples were visually monitored to note any observations of outward displacement of the glass substrates.
3.5. Post-Test Evaluation
A red dye penetrant was applied to the samples after testing to highlight regions of delamination between the glass and interlayer. Photographs were taken before and after a dye penetrant had been applied to allow visual observations of the extent of glass fracture and regions of interfacial separation.
4. Results and Discussion
4.1. Failure
In all samples, what will be referred to as failure, occurred at some peak force as a result of; fracture of glass to an extent that leads to the loss in engagement of the samples and a reduction in their load-bearing capacity and, in some cases, interfacial separation between the glass and PVB-interlayer, initiated by glass fracture. There was no evidence for cohesive failure within the interlayer in any of the samples tested.
4.2. Force-Displacement Response
The force-displacement curves for all samples at 0.125mm/min, 0.5mm/min and 1.0mm/min for non-aged, humidity-aged and humidity-aged with bond-line water soaking are shown in figure 10. All samples reached a peak force, after which there was a sudden drop in load, or a small drop in load followed by a plateau region at which displacement progressed at the same load, followed by a sudden drop in load.
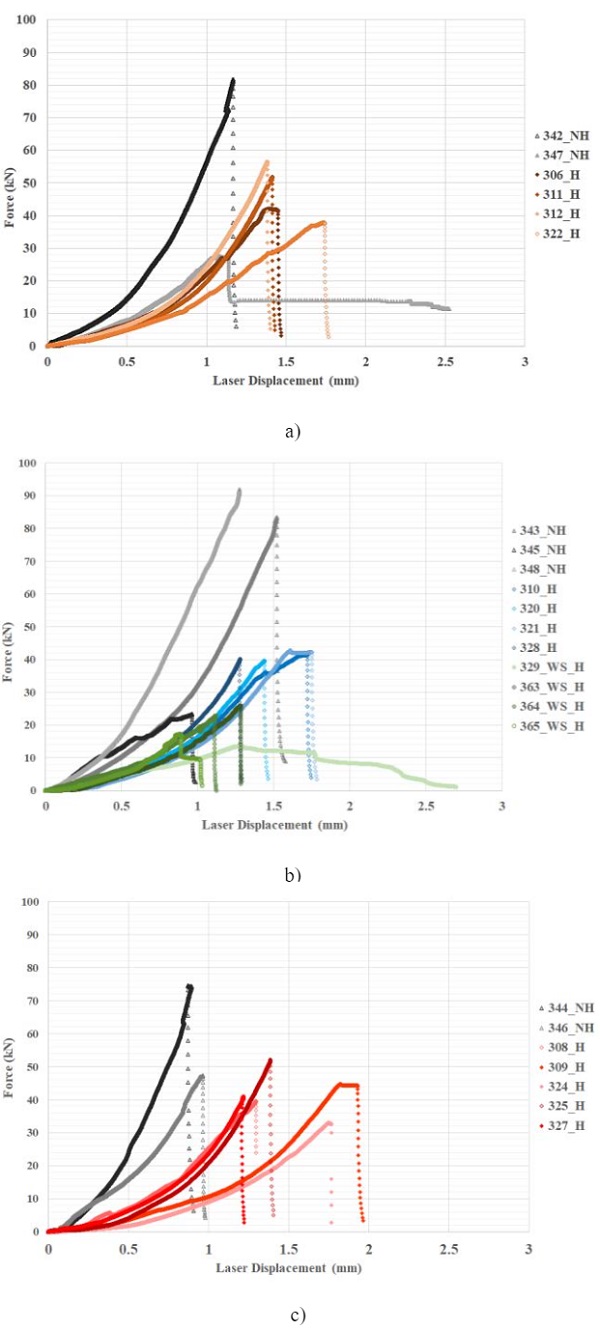
The sudden drop in load-bearing capacity of the samples was found to be a result of combination of glass fracture and interfacial separation between the PVB interlayer and glass leading to a loss of sample engagement.
Table 4: Mean values for shear modulus, peak force and displacement at peak force for samples tested at 0.125mm/min, 0.5mm/min and 1.0mm/min.
The shear modulus at γ=0.5 for non-aged samples, highlighted in table 4, are shown to increase with increasing strain rate and are in the same order of magnitude as existing literature providing some validation for the testing jig developed within this work (Hána et al. 2017). Humidity influences the shear modulus at γ=0.5 by a reduction of 44%, 82% and 84% for 0.125mm/min, 0.5mm/min and 1.0mm/min displacement rate respectively.
Based on the force-displacement curves alone, it is unclear as to whether the reduction in stiffness for humidity-aged samples is a consequence of humidity effecting the shear modulus of the interlayer or; because of a reduction in the intrinsic interfacial adhesive stiffness. The bond-line water-soaked samples show slightly higher values of shear modulus than the non-water-soaked samples which had undergone the same humidity-ageing process.
Sample 348 did not fail; the test was stopped early to assess the fracture pattern before the peak load was reached, and therefore was not included in calculations for the peak force at failure shown in table 4. The peak force reached across the samples for the humidity-aged samples showed a reduction of on average 23%, 38% and 31% reduction and 49%, 54% and 30% reduction as taken from the maximum peak force value reached amongst all samples within the 0.125mm/min, 0.5mm/min and 1.0mm/min displacement rates respectively.
Samples 329_WS_H and 365_WS_H exhibit a non-zero plateau in the force for increasing displacement after the peak force is reached providing some evidence for progressive stable crack growth and interfacial separation, before the sample failing through glass fracture occurring to an extent that results in a loss of the sample load-bearing capacity.
The higher loads expressed for the non-aged samples suggest that the intrinsic value for interfacial adhesion is much higher in the non-aged samples. If the glass were able to separate from the interlayer, as would be the case for lower values of intrinsic interfacial adhesion, the samples would lose their ability to transmit loads to the interlayer, and therefore fail. However, we see the non-aged samples can maintain their structural integrity at higher loads, despite glass fracture during loading.
The associated displacement at failure was 32%, 26% and 69% higher for the humidity-agedsamples than for non-aged samples at 0.125mm/min, 0.5mm/min and 1.0mm/min respectively. As such, based on the force-displacement curves alone, it is not clear as to whether the humidity-aged samples are failing due to due to the intrinsic value of adhesive strength being reduced and therefore allowing that the samples to lose their ability to transmit load to the interlayer at lower loads through interfacial separation initiated by glass fracture, or, due to the bulk material properties of the interlayer behaving in a less stiff manner, and therefore allowing for the critical strain for crack growth along the interface to be met more easily.
4.3. Effects of Humidity and Water Infiltration on Interfacial Separation
Figure 11 provides a surface view for substrates X and Y for all 24 post-fractured laminated glass samples before and after a dye had been allowed to penetrate the regions of interfacial separation.
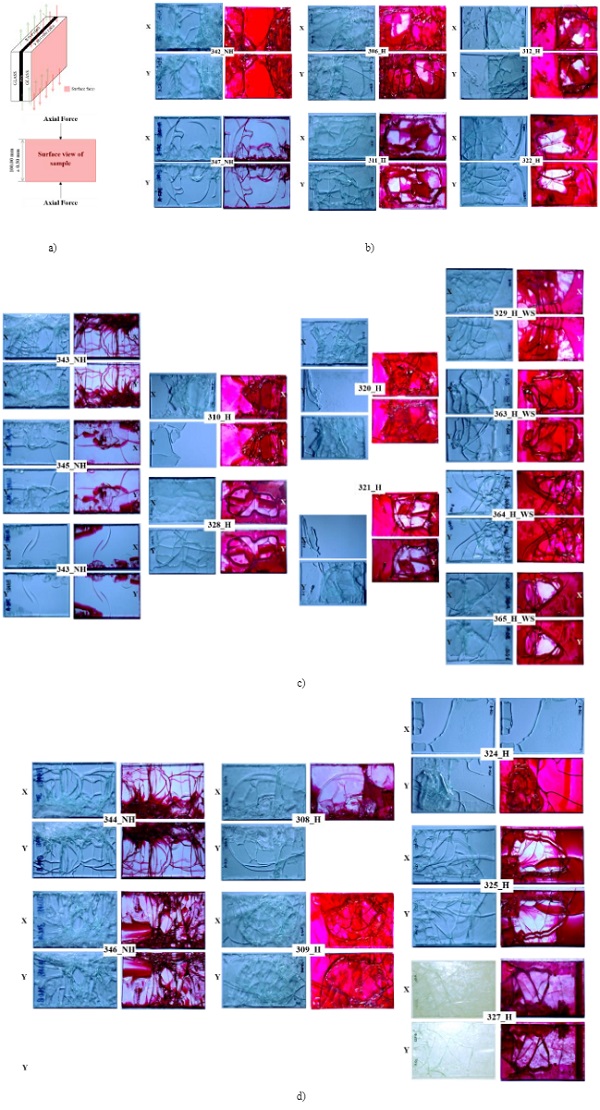
There was no clear correlation between the level of interfacial separation observed and the different displacement rates within each test pre-condition. However, humidity was shown to have a significant effect on the interfacial separation observed at all displacement rates tested. This is a result of: a change in the bulk material properties of the interlayer in terms of reduced stiffness and therefore the interface experiencing a lower relative load with increasing displacement allowing some critical strain for interfacial separation to be met or, reduced intrinsic interfacial adhesive strength leading to glass fracture initiated interfacial separation or, a mixture of both effects.
Sample 348_NH did not exhibit a load drop; the test was stopped to assess the fracture pattern before the peak force is reached. It is evident that despite some glass fracture occurring during loading before the peak force is reached, the sample is still able to provide load-resistance. Humidity can be seen to have a more dominant effect on reducing the intrinsic value of adhesion on observation of samples 343_NH and 348_NH in figure 11(c).
Both samples reach similar levels of strain at peak force as samples 320_H and 328_H, yet samples 343_NH and 348_NH,show a low proportion of interfacial separation. This would suggest that in the instance of no humidity, the intrinsic interfacial adhesion is much higher and therefore, when the glass fractures during loading, it remains attached to the interlayer.
The force-displacement curves for the humidity-aged water-soaked samples in figure 10 exhibited similar stiffnesses but a reduction in the peak force and corresponding strain to failure compared to non-water-soaked samples. The proportion of delaminated area in the water-soaked samples was similar to that of the non-water-soaked samplesbut reach a much lower peak force. This indicates that the water soak has a mixed effect on the intrinsic level of adhesion, the interfacial stress distribution and/or the bulk material properties of the interlayer.
In samples 363_H_W, 364_H_W,and 365_H_W, there is some evidence for internal wrinkling of the interlayer. At the point of failure, despite a high % of delamination present across the samples, there is not clean separation of one glass sheet from another and the external edge glass fractures that delaminated cleanly in the humidity-aged samples, were still part bonded to the interlayer. This suggests that that the water soak may create a further non-uniformity in the stress distribution at the PVB-glass interface.
4.4. Interfacial Separation Overview
Two methods of interfacial separation were considered in the observation of the dyed laminated glass samples post-test: i.) interfacial separation initiated by glass fracture governed by the intrinsic adhesive strength and ii.) interfacial separation that occurred as a consequence of peeling of the interlayer from one glass substrate at the edge of the glass-interlayer contact under deformation leading to inducing a crack initiation and further growth at the interface leading to a permanent slip along the effected edge.
4.5. Interfacial Separation Initiated by Glass Fracture
In all cases, the glass substrates display a complex and highly fragmented fracture pattern. In the non-aged samples, no correlation can be drawn between the influence of glass fracture on initiating delamination as there are very few visible regions of interfacial separation. This is consistent with the force-displacement curves that show that the samples can withstand much higher loads; despite glass fracture with increasing displacement, the glass substrates are still able to transmit loads to the interlayer and retain their structural integrity under the test conditions.
This further suggests that the non-aged samples exhibit a relatively higher value of intrinsic interfacial adhesion. There is some evidence to show that a higher force at failure corresponds with a greater density of glass fragments in the non-aged samples when correlating the peak force at failure with the observed fracture pattern between 342_NH and 347_NH (0.125mm/min) and 343_NH and 345_NH (0.5mm/min) as shown in figure 12(b). Samples 342_NH and 343_NH failed at much higher loads than samples 347_NH and 345_NH.
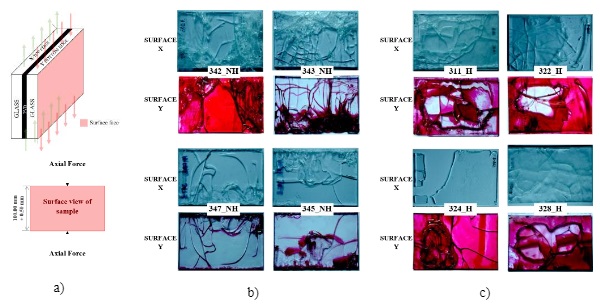
Cracks that develop within the humidity-aged samples during loading are shown to influence the regions that eventually delaminate. Clean interfacial separation tends to follow the glass fracture pattern. Interfacial separation in the regions of glass fracture in which the delamination is concentrated along the outside side edges of the pane is likely due to the combined effects of longitudinal tensile cracks that follow the full height of the samples due to the effect of Poisson’s ratio and glass-fracture induced interfacial separation along these regions as shown in samples 322_H and 324_H in figure 12(c).
Following with the correlation between glass fracture and interfacial separation, it can be seen from the samples shown in figure 12(c), it can be seen in the regions of no interfacial separation, there is a crack around the perimeter of the region. The side faces of the glass substrates are free to expand due to the configuration of the testing jig and as such longitudinal cracks that form can freely initiate interfacial separation. Samples 311_H, 322_H and 328_H exhibit less delamination in the presence of transverse cracks. Meanwhile, sample 324_H exhibits a large area of interfacial separation and exhibits few transverse cracks in the region of interfacial separation.
The regions that show no dye penetrant suggest that glass fracture occurred in the perimeters of these regions during loading in a similar manner to that suggested in figure 13.
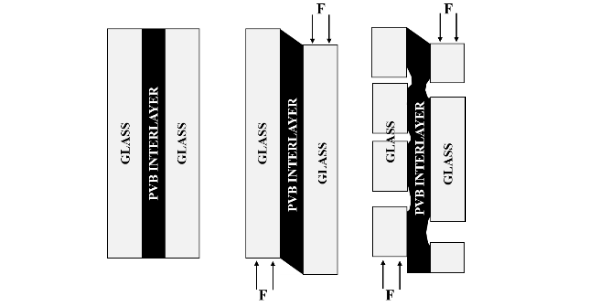
Similar to the influence of glass fracture on interlayer stretching during impact loading proposed by Nourry, the formation of transverse cracks could introduce regions of interlayer relaxation with increasing displacement (Nourry 2006). Internal transverse glass fracture would mean that the affected regions of glass are no longer able to transmit loads to the interlayer during deformation and internal interlayer stretching will occur.
4.6. Interfacial Separation Initiated by Interfacial Cracks
Some regions of permanent slip of one glass substrate relative to the other were observed within the humidity-aged samples as highlighted in figure 14. This provides evidence of delamination initiated by a longitudinal interfacial crack growth along the glass-polymer interface at the top edge on the opposite edge of the loaded glass edge. Edge-dominated failure could be a result of a peak in the stress distribution along the top and bottom edges of the glass substrates as a result of shear lag (Volkersen 1938).
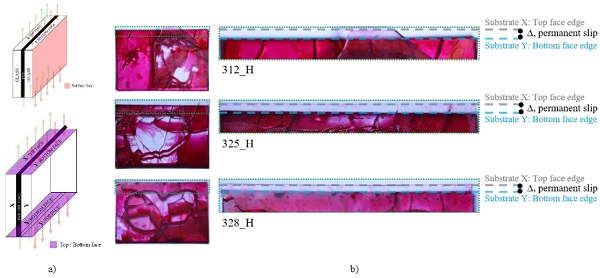
Delamination between the top of one substrate and the interlayer leads to a permanent slip, ∆, of the substrates relative to one another. With increasing displacement, the interlayer that is still engaged with the glass can stretch leading to internal wrinkling of the polymer interlayer within the central region of the structure, where the interlayer is still engaged with the glass.
5. Conclusions
The aim of this research was to make steps to identify the key parameters that effect delamination of the PVB-glass interface. The intention is to use this knowledge to ease separation at end-of-life and enable re-use or high-value re-cycling of flat glass.
As such the research described in this paper, describes a new method for separating laminated glass in shear and investigates the effect of humidity and water infiltration on delamination of PVB interlayer from glass with the aim of achieving delamination with minimal glass fracture and clean separation along the full area of the glass sheet.
Due to glass substrate fracture, it is not possible to accurately quantify the interfacial adhesion based on the current set of experimental findings. However, useful conclusions can be drawn on the following effects on delamination of PVB-interlayer from glass in compressive shear:
• The values of shear modulus at γ=0.5 for non-aged samples are shown to increase with increasing strain rate and are in the same order of magnitude as existing literature providing validation for the testing jig. [42]
• Force-displacement curves shown in figure 10 and post-fracture evaluation highlighted in figure 11 for samples that reach similar levels of strain in the same displacement range show an increase in the level of interfacial separation for humidity-aged samples providing evidence for a reduction in the intrinsic value of interfacial adhesion.
• Water infiltration at the interface causes a further reduction in the peak force and corresponding displacement at failure, albeit with similar levels of interfacial separation present as with humidity-aged samples.
• Glass fracture can initiate interfacial separation. The nature of glass fracture in terms of fragment size and directions of cracks relative to the loading direction will influence the effective area and subsequently regions of delamination at failure. The presence of transverse glass cracks can reduce the level of interfacial separation at failure.
• Observations of permanent relative slip between the glass panes and internal wrinkling provides some evidence of delamination initiated by a peak in the interfacial stress distribution along the horizontal top edges of the samples leading to the formation of interfacial cracks along the glass-polymer interface.
• Internal wrinkling suggests that some internal regions of interlayer were freely able to stretch and absorb the energy in the system after neighbouring delamination has occurred.
6. Future Work
Existing literature looks to quantify the behaviour of laminated glass as one system that accounts for the effects of bulk material behaviour of the PVB interlayer and behaviour at the glass-PVB interface. As previously suggested, it must be considered that there is a complex interplay between interlayer bulk material behaviour and the intrinsic value for interfacial adhesion. Some complex analysis is required to evaluate the work done to separate the viscoelastic PVB interlayer from the glass pane.
In the context of existing post-processed laminated glass panels, modification to the level of adhesion requires a balance of the control of external parameters that when modified are likely to affect the bulk properties of the interlayer material behaviour as well as the intrinsic value for interfacial adhesion.
Future work will look to better understand the delamination phenomena between PVB-interlayer and glass and its response to strain rate and temperature; build on the existing method of using humidity and water infiltration to reduce the intrinsic level of adhesion to allow peak force to coincide with interfacial crack propagation and delamination; evaluate the critical strain at which a crack nucleates from one polymer/substrate interface and; experimentally and analytically evaluate methods of achieving steady-state delamination and clean interfacial separation.
The contributing effects of glass fracture means that it is not possible to associate interfacial failure with the maximum shear strength. To better characterise the effects of the external influences used in this study, it will be necessary to procure higher strength glass, ideally toughened glass, and/or protect the glass edges in some way to decouple the effects of glass fracture from bulk material behaviour and interfacial delamination.
Later work will exploit any optimised parameters to return to testing annealed glass and evaluate the effects of size when considering scaling up the sample size with the overall aim of achieving delamination with minimal glass fracture and clean separation along the full area of the glass sheet.
7. Acknowledgements
This research is undertaken within the Future Infrastructure for the Built Environment doctoral programme funded by Engineering and Physical Sciences Research Council (EPSRC), UK. The authors are also grateful to the Society of Façade Engineers for supporting the development of the new testing apparatus, Lee Glover, Chris Lloyd and Lauren Whittaker at Saint Gobain UK for providing the glass samples within this test programme and Marco Zaccaria at AGC Europe for providing laminated glass samples in the development of the testing jig.
8. References
Acevedo, C.F., Martinez de Morentín Osaba, L., Arteta, E.O., Herrera, G.M., Fernández, M.A.F.: Method for the Recycling of Polyvinyl Butyral, https://patentimages.storage.googleapis.com/bc/7c/dd/b5ef7765daa73b/US8530531.pdf, (2013)
Anderson, A.: Delam Australia, http://www.delam.com.au/, (2020)
Andreozzi, L., Briccoli, S., Fagone, M., Ranocchiai, G., Zulli, F.: Weathering action on thermo-viscoelastic properties of polymer interlayers for laminated glass. Constr. Build. Mater. 98, 757–766 (2015). https://doi.org/10.1016/j.conbuildmat.2015.08.010
ASTM: Standard Test Method for Peel Resistance of Adhesives (T-Peel Test)(2015)
Belis, J., Zarmati, G., Parmentier, B.: Structural behaviour of laminated glass elements –a step towards standardization. (2007). https://doi.org/10.13140/2.1.3592.6084
Bogatyrev, L.C., Plaksina, A.M., Kaprov, A.I., Shishkin, I. V., Gusel’nikova, V.N.: Adhesion of a PVB film to flat glass measured by exfoliation and shear. Glas. Ceram. (1981). https://doi.org/10.1007/BF00701748
BPIE: 97% of Buildings in the EU need to be Upgraded (2017)
Butchart, C., Overend, M.: Delamination in Fractured Laminated Glass. Proc. 3rd Int. Conf. Eng. Transpar(2012)
Butchart, C., Overend, M.: Influence of Moisture on the Post-fracture Performance of Laminated Glass. In: Glass Performance Days 2013. pp. 59–61 (2013)
Carrot, C., Bendaoud, A., Pillon, C.: Handbook of Thermoplastics: Polyvinyl Butyral. In: Handbook of Thermoplastics. pp. 89–137 (2016)
Chapuis, V., Pélisset, S., Raeis-Barnéoud, M., Li, H.Y., Ballif, C., Perret-Aebi, L.E.: Compressive-shear adhesion characterization of polyvinyl-butyral and ethylene-vinyl acetate at different curing times before and after exposure to damp-heat conditions. Prog. Photovoltaics Res. Appl. 22, 405–414 (2014). https://doi.org/10.1002/pip.2270
Eitner, U., Rendler, L.C.: The mechanical theory behind the peel test. Energy Procedia. 55, 331–335 (2014). https://doi.org/10.1016/j.egypro.2014.08.096
Elzière, P.: Laminated glass: dynamic rupture of adhesion, https://hal.archives-ouvertes.fr/tel-01381142, (2016)
EU: Design and development of a demonstrative pilot plant for the recycling of polyvinyl butyral ( PVB )(2013)
Ferrante, J., Bozzolo, G.H., Finley, C.W., Banerjea, A.: Interfacial adhesion: theory and experiment. NASA Tech. Memo. (1988)
Froli, M., Lani, L.: Adhesion, Creep and Relaxation Properties of PVB in Laminated Safety Glass. In: Proceedings of Glass Perfomance Days (2011)
Hána, T., Eliášová, M., Machalická, K., Voká Č, M.: Determination of PVB interlayer’s shear modulus and its effect on normal stress distribution in laminated glass panels. In: IOP Conference Series: Materials Science and Engineering (2017)
Hoffman, J., Demski, H..: Method of separating glass from film in the recycling of laminated glass.U.S. Patent No. 5,855,325. (1999)
Hooper, P.A., Blackman, B.R.K., Dear, J.P.: The mechanical behaviour of poly (vinyl butyral) at different strain magnitudes and strain rates. J. Mater. Sci. 47, 3564–3576 (2012). https://doi.org/10.1007/s10853-011-6202-4
Hülsmann, P., Philipp, D., Köhl, M.: Measuring temperature-dependent water vapor and gas permeation through high barrier films. Rev. Sci. Instrum. 80(2009). https://doi.org/10.1063/1.3250866
Iwasaki, R., Sato, C.: The influence of strain rate on the interfacial fracture toughness between PVB and laminated glass. J. Phys. IV JP. 134, 1153–1158 (2006). https://doi.org/10.1051/jp4:2006134176
Iwasaki, R., Sato, C., Latailladeand, J.L., Viot, P.: Experimental study on the interface fracture toughness of PVB (polyvinyl butyral)/glass at high strain rates. Int. J. Crashworthiness. 12, 293–298 (2007). https://doi.org/10.1080/13588260701442249
Jagota, A., Bennison, S.J., Smith, C.A.: Analysis of a compressive shear test for adhesion between elastomeric polymers and rigid substrates. Int. J. Fract. (2000). https://doi.org/10.1023/A:1007617102311
Kasper, A.: Recycling of Cullet into Flat Glass Melting Furnaces. In: Kriven, W.M. (ed.) Ceramic Engineering and Science Proceedings. The American Ceramic Society (2006)
Keller, U., Mortelmans, H.: Adhesion in Laminated Safety Glass –What makes it work? Glas. Process. Days(1999)
Kinloch, A.J., Williams, J.G.: The mechanics of peel tests. In: Adhesion Science and Engineering. pp. 273–301 (2002)
Martín, M., Centelles, X., Solé, A., Barreneche, C., Fernández, A.I., Cabeza, L.F.: Polymeric interlayer materials for laminated glass: A review. Constr. Build. Mater. 230, 116897(2020)
Nourry, E.: Laminated glass behaviour under perforating impact.Doctoral dissertation(2006)
Samieian, M.A., Cormie, D., Smith, D., Wholey, W., Blackman, B.R.K., Dear, J.P., Hooper, P.A.: Temperature effects on laminated glass at high rate. Int. J. Impact Eng. 111, 177–186 (2018). https://doi.org/10.1016/j.ijimpeng.2017.09.001
Samieian, M.A., Cormie, D., Smith, D., Wholey, W., Blackman, B.R.K., Dear, J.P., Hooper, P.A.: On the bonding between glass and PVB in laminated glass.Eng.Fract.Mech.214, 504-519(2019)
Sandén, B.: Which interlayer for which glazing application? In: Glass Performance Days 2015. pp. 152–156. , Tampere, Finland (2015)
Sha, Y., Hui, C.Y., Kramer, E.J., Garrett, P.D., Knapczyk, J.W.: Analysis of adhesion and interface debonding in laminated safety glass. J. Adhes. Sci. Technol. (1997). https://doi.org/10.1163/156856197X01010
Shawn, A., Baranova, I., Poley, J., Reis, H.: Energy Saving Glass Lamination via Selective Radio Frequency Heating. New York (2012)
Swain, B., Ryang Park, J., Yoon Shin, D., Park, K.S., Hwan Hong, M., Gi Lee, C.: Recycling of waste automotive laminated glass and valorization of polyvinyl butyral through mechanochemical separation. Environ. Res. (2015). https://doi.org/10.1016/j.envres.2015.08.017
Tupý, M., Měřínská, D., Svoboda, P., Kalendová, A., Klásek, A., Zvoníček, J.: Effect of water and acid-base reactants on adhesive properties of various plasticized poly(vinyl butyral) sheets. J. Appl. Polym. Sci. 127, 3474–3484 (2013). https://doi.org/10.1002/app.37597
Tupy, M., Mokrejs, P., Merinska, D., Svoboda, P., Zvonicek, J.: Windshield recycling focused on effective separation of PVB sheet. J. Appl. Polym. Sci. (2014). https://doi.org/10.1002/app.39879
Volkersen, O.: Die Niektraftverteiling in Zugbeanspruchten mit Konstanten Laschenquerschritten. Luftfahrtforsch. 15. 41–47 (1938)
Wang, H., Xie, C., Yu, W.T., Fu, J.G.: Efficient combined methodof selective dissolution and evaporation for recycling waste polyvinylbutyral films. Plast. Rubber Compos. 41, 8–12 (2012). https://doi.org/10.1179/1743289811Y.0000000016
Weller, B., Wünsch, J., Härth, K.: Experimental study on different interlayer materials for laminated glass. Glas. Process. Days. (2005)
Zaccaria, M., Overend, M.: Validation of a simple relationship between the fracture pattern and the fracture stress of glass.Proc. Eng. Transpar. Int. Conf. Glas. 25–26 (2012)
Zhang, X., Hao, H., Shi, Y., Cui, J.: The mechanical properties of Polyvinyl Butyral (PVB) at high strain rates. Constr. Build. Mater. 93, 404–415 (2015). https://doi.org/10.1016/j.conbuildmat.2015.04.057