The production capacities have grown significantly in recent years, especially in China. The broad acceptance of sputter-coated glass products in even remote areas of the global manufacturing network requires an ever increasing simplification of process requirements. Major advantages in the processing chain of glass coating are post-temperable coatings. Such products simplify the coating process itself by avoiding cut-size handling and the downstream storage and logistics in product distribution.
Since many years the suppliers of glass coating equipments are involved in development and supply of the related glass coating processes. We will describe here our family of Single-, Double- and even Triple LowE coatings which are also available as post-temperable versions. This will be accompanied by Single LowE products with enhanced shading as well as a variety of Solar Control products. Key performance indicators are excellent film thickness uniformity, improved selectivity and low colour shifts during tempering.
Introduction
LowE coating technology has matured over more than 30 years. State-of-the art solutions will be described here to provide insight on current development trends. The solutions apply to all current available glass sizes and are based on commonly used magnetrons. Base, seed and top layers are deposited with dual rotatable AC magnetrons, whereas planar DC magnetrons are used for silver and blockers.
Results
Temperable Coating stacks
A typical coating stack for post-temperable single LowE is shown in Figure 1. Recent work has focused on simplification of such stacks. Indeed it is possible to avoid a dedicated bottom blocker layer if a suitable base layer with Na+ barrier properties is chosen. Such changes look minor at first sight. However this coating stack does not require changes between the standard non-temperable version and the post-temperable version in production. Two volume products can merge into only one, with significant savings in distribution, storage and handling.
Figure 1: Coating stack Temperable Single LowE (TSLE)
Figure 2: Coating stack Temperable Triple LowE (TTLE)
The coating stack in Figure 1 can now be used as a building block for multi-LowE stacks. Introducing a sequence of middle layer / seed layer / Ag / Blocker above the first Ag/Blocker will transform the solution into a LowE with enhanced selectivity (see Figure 2). These optical filters can be further improved in selectivity (reduced intake of solar energy) with each additional building block of Ag and dielectric interlayer (see Figure 3).
Figure 3: VIS/NIR Spectrum of TTLE
Temperable coatings have more stringent requirements in processing than non-temperable coatings. The heat-processing unveils handling action of the glass that is not visible without tempering. Therefore any contact with transportation and lifting devices shall be avoided on the coating side of the glass substrate (typically the air-side) during processing. A state-of-the-art washing machine with polishing bridges in front of the coating system is mandatory for good yield in production of any kind of tempered coatings.
Colour shifts can occur due to heat-induced changes of layer stoichiometry. As mentioned earlier it is very desirable to reduce such shifts to a minimum, because small changes are equivalent with small losses and additionally may simplify the product portfolio.
Another serious problem can be haze (i.e. light scattering) which is a result of rearrangements of the layer crystal structure or sodium diffusion from the glass substrate into the layer stack. Sodium is chemically very reactive and can seriously affect the silver and dielectric layers.
Figure 2 and 3 characterize a Triple LowE coating stack that fulfills the performance criteria described here. High light transmission, very low colour shifts and minimum haze levels are obtained.
To obtain a reduced level of transmission represents an additional challenge for temperable coatings such as LowE-Sun. Reduced transmission is typically obtained from enhanced absorption, which can be achieved with metallic or substoichiometric layers. Many commonly used layers (for example Ni:Cr) tend to be unstable in a tempering step, because they either change in stoichiometry by collecting diffusing oxygen or by re-crystallization if the layers are too thick. Only a very restricted number of materials offer possibilities to stabilize absorption for temperable coatings. Among the possible candidates it is desirable to choose those which also have „blocker“ properties.
Distributing the absorption in one blocker layer above the silver and a second blocker layer below is a possible recipe to avoid thick layers. These two blocker materials must be placed around the bottom silver if neutral to slightly negative colour values for the glass side reflection (Rg) shall be obtained. An example is shown in Figure 4.
Figure 4: Coating stack Temperable Double LowE Sun (TDLE Sun)
Single Layer Performance for Temperable Multi-LowE Coatings
Standard coating uniformity in architectural glass coating is a layer thickness deviation of ± 1.5 % across the width of the glass today. However, the tolerances of each single layer have a more severe impact if more and more layers are piled on top of each other. For Temperable Triple LowE a minimum of 14 to 15 single layers is necessary.
We have analyzed the impact of all the single layer deviations in a layer stack on the resulting colour in glass side reflection (Rg). The colour crosses in figures 5 show the shift in Rg colour if each of the single layers is treated separately with the same standard thickness deviation of ± 1.5 %. It can be easily recognized that the deviation range in the colour box is getting bigger with the number of single layers in the layer stack, although the same set of materials and the same deviation range of ± 1.5 % is applied.
Multi-LowE represents a new challenge in coating uniformity, because tighter single layer uniformities must be ensured to obtain the same absolute colour deviation as a normal Single LowE. Correct and uniform colour is of course a must for any kind of high performance glazing. This challenge would be rather moderate if only one material or layer would contribute to the deviation pattern. But all dielectrics and silver contribute significantly to the uniformity.
Figure 5.1: Colour Cross TSLE
Figure 5.2: Colour Cross TDLE
Figure 5.3: Colour Cross TTLE
In order to match the more restricted uniformity requirements of modern Multi-LowE coatings VON ARDENNE has further developed and improved its magnetron hardware. A special effort has been made to improve the magnet systems. Figure 6 shows results for reactive ZnSn sputtering to obtain stoichiometric ZnSnO3 layers. The results have been obtained on a GC330H jumbo coating system. The uniformity range on 3.3 m wide glass with an edge exclusion of 5 cm is ± 1.0 ... 1.1 %. Similar or better results are obtained for TiO2 from ceramic TiOx targets and Si3N4 from Si:Al8 targets.
The plot in Figure 6 shows three curves. ID4513 and ID1415 are the single layer cross uniformities deposited from one (1) double rotatable magnetron (RDM3750) each. ID 1370 shows the result if the ZnSnO3 layer is deposited from both RDM3750 together. The two RDM3750 were placed in neighbouring process compartments.
These results show that the necessary hardware for cutting-edge coating stacks is available. We expect further improvements in this direction and continue to research for even better performance.
Figure 6: Uniformity of single layer ZnSnO3 from one double rotatable magnetron and a dual arrangement of two double rotatable magnetrons (RDM3750).
Thickness deviation of RDM a (ID 1370): ±1.2%
Thickness deviation of RDM b (ID 4513): ±0.9%
Thickness deviation of RDM a+b (ID 1415): ±1.1%
Conclusions and Summary
We have analyzed the current requirements for modern LowE coatings, especially taking into the requirements for safety glass processing of coated glass. Solutions for temperable Multi-LowE coatings are presented. As a conclusion we have shown that a key parameter for the increasing complexity of LowE coating stacks is coating uniformity. Despite 30 years of hardware and process development magnetron sputter coating, it is still possible to obtain significant improvements. Single layer thickness uniformities of all relevant process can be pushed to well below ± 1.5 %.
Acknowledgements
The authors would like to thank Mr. Hank Lin, Mr. Chou Ching Chun and Mr. Yang Weiqiang of Taiwan Glass for continuous cooperation in coating stack development.
AUTHOR: Christoph Köckert, Harald Hagenström - VON ARDENNE
Biography
Since his graduation in Low Temperature Physics at the Technical University of Dresden in 2001, Dr. Christoph Köckert has worked at VON ARDENNE as lead technologist for Thin-Film Applications, Processes and Components.
His work on optical simulations and layer stack development covers the whole range of PVD-applications from optical multi-layer systems, CSP relevant coatings like absorbers and mirrors up to large-area coatings like Low-E and Solar Control systems for architectural glazing.
He is author of publications about magnetron sputtering and PVD technology and co-owner of several related patents.
VON ARDENNE ANLAGENTECHNIK GMBH
Plattleite 19/29
D-01324 Dresden
Germany
tel: +49 (0)351 - 26 37 4 35
fax: +49 (0)351 - 26 37 3 08
Koeckert.Christoph@vonardenne.biz
www.vonardenne.biz
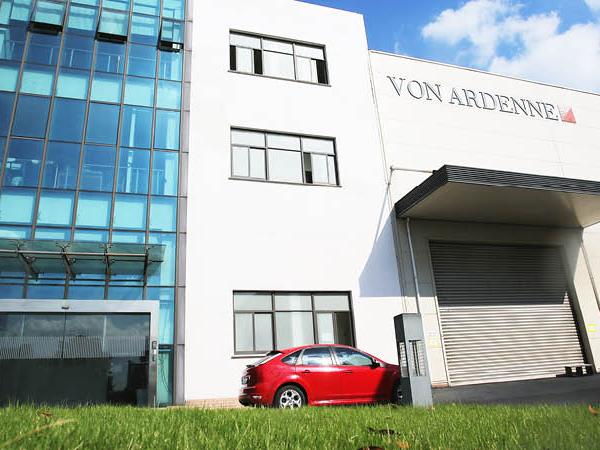
Date: 19 April 2012
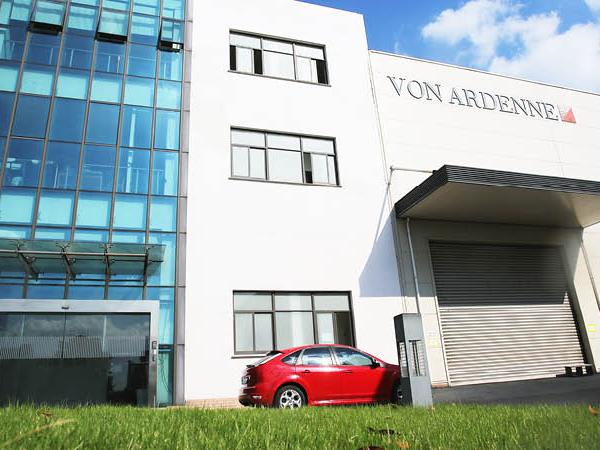
