This paper was first presented at GPD 2023.
Link to the full GPD 2023 conference book: https://www.gpd.fi/GPD2023_proceedings_book/
Authors:
- Dr. Wilma Dewald (Volkswagen AG)
- Fabian Unterste-Wilms (tesa SE)
- Dr. Regine Niepmann (FLABEG Automotive Germany GmbH)
- Hartwig Schneider (TU Braunschweig)
The German publicly funded project KODOS evaluated the implementation of ultrathin glass in various applications. In this paper we focus on automotive applications and describe the tests we performed to find the limits of ultrathin glass in handling and within tests simulating stress expected in the field. The advantage of ultrathin glass is obvious: scratch resistance, good diffusion barrier properties, chemical robustness and flexibility are combined. At the same time first products using ultrathin glass are appearing on the consumer market like foldable smartphones and rollable television screens. Compared to consumer market the requirements in automotive applications are higher. First, the temperature range to be covered is -40 °C to 80°C, the lifespan of the device has to be longer and mechanical impact from stones in the exterior or safety issues in the interior have to be considered. In Figure 1 different application areas in a car are shown and critical tests are given in Table 1.


First, the possible geometry which can be covered by ultrathin glass has to be evaluated. For 3D curved surfaces a hot forming of the glass sheet is necessary. Tests showed that with existing equipment for gravity bending an accurate hot forming cannot be performed. This limits the glass geometry to 2D cold bending of the glass. Here the glass thickness must be chosen according to the desired curvature. The higher the curvature the thinner the glass must be chosen to avoid fractures and recoiling forces as much as possible. This correlation can be seen in Figure 2 following the equation σ=(E∙T/2)/R, where σ is the tensile stress, E is the Young’s modulus, T the glass thickness and R the bending radius of the glass sheet. 50 MPa is assumed to be the tensile stress at which the glass tends to break. This depends also on the edge strength and treatment of the glass during handling. It can be seen, that for small bending radii, like 50 mm for a typical ring lens, thin glass of 50 µm thickness is beneficial. For applications like a slightly curved B-pillar with bending radius of about 2 m thicker glass can be used. Considering that potentially a laminate of several functionalized ultrathin glasses is used, a glass thickness of 100 µm is well chosen.
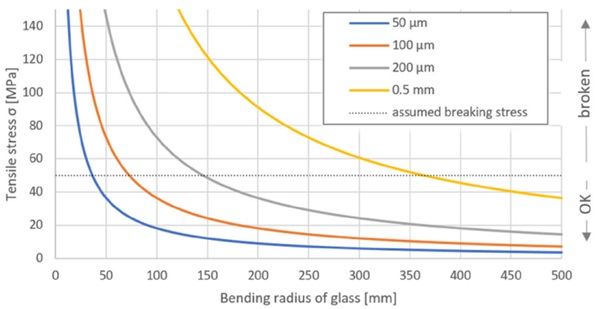
For the car exterior stone impact tests are crucial especially for areas around the front bumper, where impacts with high kinetic energy are expected. Therefore, stone impact test analog to standard ISO 20567-1 method B were performed on 100 µm glass and polycarbonate plates Here 500 g of stones are shot on the sample with a pressure of 2 bar within 10 s. This is done twice. The angle of incidence is 45°. Test panels for this test are 100x100 mm². Also 50 µm ultrathin glass laminated on a polycarbonate ring lens was tested. Unfortunately, in both cases the glass is damaged by the stone impact as can be seen in Figure 3 and Figure 4. Ultrathin glass is not suitable for applications in stone impact areas especially in the front of a vehicle. In the interior all surface in the head crash zone must survive an impact of a 6.8 kg pendulum with 165 mm diameter and 24.1 km/h velocity according to ECE-R21. This is harsher than the stone impact test.
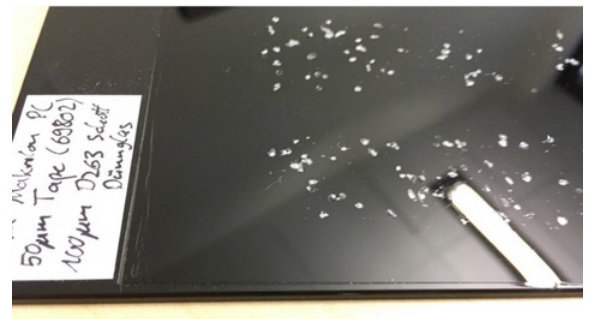
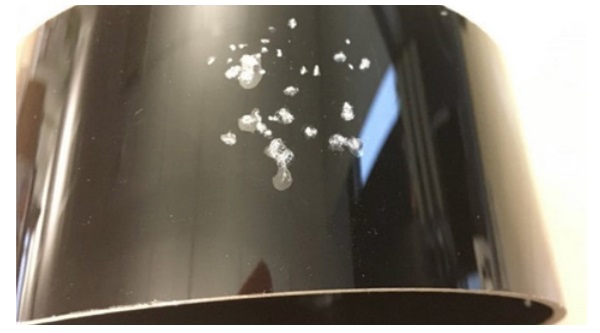
Applications of ultrathin glass in the head crash zone in the interior should be avoided. Ball drop tests for checking medium mechanical robustness were done with a 32.6 g ball with 20 cm diameter, height was set to 153 cm. This equals the kinetic energy a ball would have if 100g are falling from 50 cm. The specification should be met for parts being touched and pressed by passengers e.g. for B-pillar covers in the exterior. The ball drop test results are given in Table 2. While the polycarbonate plate is not damaged, a bulk glass of 2 mm thickness is destroyed already at a height of 56 cm. Polycarbonate/Optical Clear Adhesive/Ultrathin glass laminates are more robust than glass only, but slight damage can be seen at maximum height of 153 cm. tesa® 69802 Optically Clear Adhesive with two different thicknesses of 50 µm and 150 µm was tested. The thickness did not change the result at maximum height.
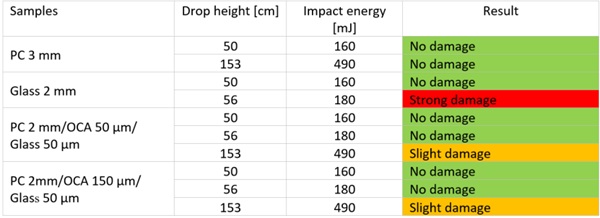
Finally for laminates of different materials the thermal expansion coefficient might lead to stress formation and eventually delamination if temperature is cycled. Climate change tests between -40°C and +80°C in twelve cycles were done on 50x50 mm² samples with 50 µm glass and 200x400 mm² polycarbonate/OCA/ glass samples with glass thickness of 100 µm. The small samples passed even 20 cycles, but the 200x400 mm² samples showed a bending along both axes (see Figure 5) especially at - 40°C. This led to fractures and delamination as can be seen in Figure 6. The adhesive cannot compensate these high shear forces.
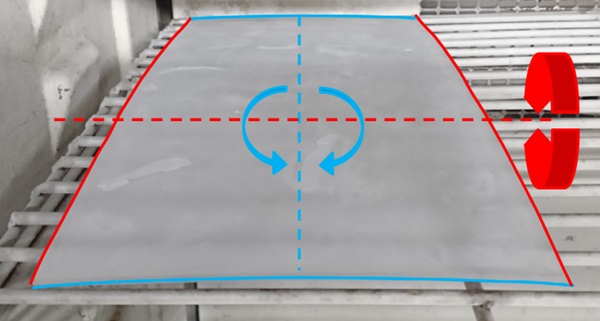
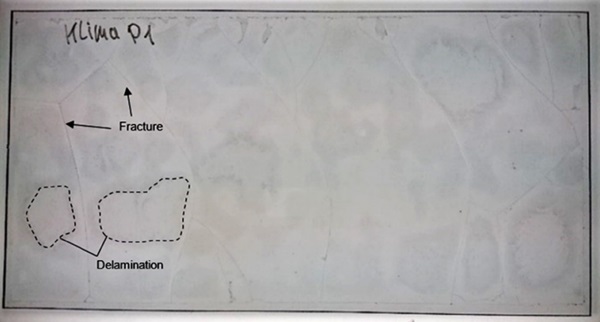
In this feasibility study the following limitations for ultrathin glass applications were found:
- Cylindrical or flat geometries possible with cold forming. Glass thickness has to be chosen according to desired curvature.
- No application in stone impact or head impact zones.
- Laminates of polycarbonate and ultrathin glass should be smaller than 100x100 mm².
- Laminates of ultrathin glass on glass are OK.
Acknowledgement
Project KODOS was funded by the Federal Ministry of Education and Research of Germany under support code 13N14605. The authors are responsible for the content of this publication.