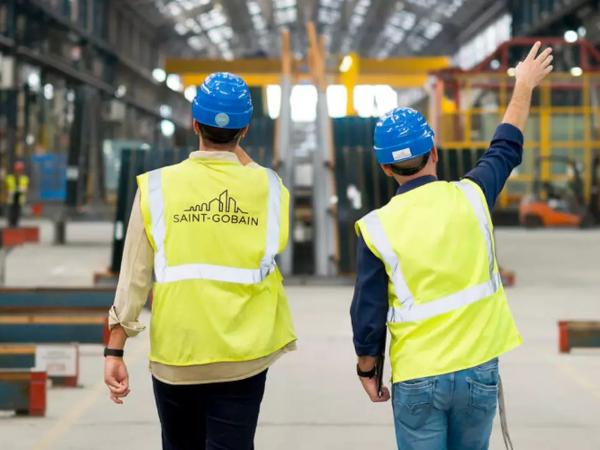
Date: 1 July 2024
Glass is everywhere: from the heat-resistant Pyrex dish in your kitchen, NASA’s space telescopes to the 11,000 glass panels in the Shard, the UK’s tallest building.
This endlessly recyclable material can be reused repeatedly, without losing its quality. Additionally, for every tonne of crushed glass used during the manufacturing process, Saint-Gobain Glass can save on 1.2 tonnes of virgin raw materials and prevent 700kg of CO2 emissions, based on Scope 1, 2, and 3 emissions.
But more can be done, and when it comes to sustainability and innovation, Saint-Gobain Glass is, well, crushing it!
For over 20 years, Saint-Gobain Glass has been an industry leader in the responsible reclamation and remanufacture of broken glass or waste glass, otherwise known as cullet.
Working directly with glass processors to implement e¬fficient glass recovery methods, it’s Saint-Gobain Glass’s mission to ensure a circular economy approach in its operations. Pioneering stuff.
Mike Butterick, Marketing Director, Saint-Gobain Glass, explains: “In the face of the climate emergency, it is imperative to challenge existing business models to secure a more sustainable future for all inhabitants of our planet. At Saint-Gobain Glass our aim is to use 50% cullet by 2030 in the glass we produce at our manufacturing site in Eggborough.
“There’s no doubt that Saint-Gobain Glass is innovative in this field and is truly setting a benchmark for the construction industry.”
Enter Glass Forever. It might sound like a song title, but it is an award-winning sustainable initiative which maximises opportunities with cullet.
Mike adds: “Glass Forever is a circular economy approach to sustainability. Under this programme, cullet glass is sourced from two primary streams: pre-consumer glass waste, generated during our customers’ manufacturing processes, and post-consumer glass waste from homes and commercial buildings across the UK.
“This glass waste is carefully collected and transported to our Eggborough plant, where it is processed and remanufactured into new high-performance glass products.”
How does Glass Forever work?
Collaborating with customers, the cullet collection method can be adapted to suit different sites. For post-consumer waste, several methods have been established to safely remove the glass from frames, break it down, and collect it in one tonne bags ready for transport. For pre-consumer glass waste, cullet bags are positioned in frames throughout the factory to collect clean cullet. Additionally, customers may also use install patented mobile glass crushing machines on site.
This technology separates glass from old window units, the cullet is deposited into Saint-Gobain Glass bags and prepared for collection.
The cullet is transported back to the Saint-Gobain Glass factory using various transportation methods, which are selected to suit the site and project requirements. Next, the cullet is treated in a specialist cullet processing facility to remove any potential contaminations such as nickel. The final cullet is blended with other raw materials and remanufactured into new high performance flat glass.
It’s as simple as that!
Winning partnerships
Minerva house, a prominent yellow brick building on the Southbank of the River Thames, adjacent to Southwark Cathedral and close to Borough Market, is a fine example of what can be achieved through Saint-Gobain’s Glass Forever programme.
Demolition specialist, Morrisroe, has been working in collaboration with GPE, a property development company, on the retrofit project of Minerva house, originally built as an office space.
Saint-Gobain Glass were enlisted as a glass partner by Morrisroe to embed a successful glass recovery model, to remove and recycle the existing glass on site into new, high-performance glazing, thereby supporting the circular economy principles.
The location of Minerva House presented its fair share of logistical challenges, offering learning curves for the teams who experimented and developed solutions. But it’s paying off.
Richard Calcutt, Technical Project Manager at Saint-Gobain Glass, praised Morrisroe's commitment, saying: "Morrisroe has a fully engaged approach to Glass Forever. They are genuinely committed to the programme for the long-term sustainability benefits it provides.
“We've implemented innovative solutions to the recovery of glass on this project, and the logical and methodical approach employed by the team makes them a joy to work with."
Find out more about Saint-Gobain Glass and Glass Forever
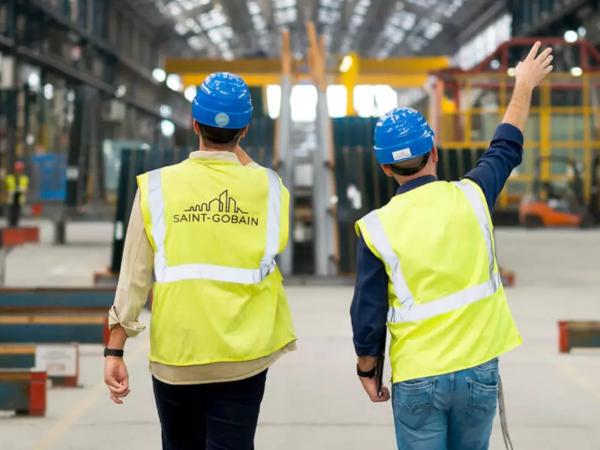

Add new comment