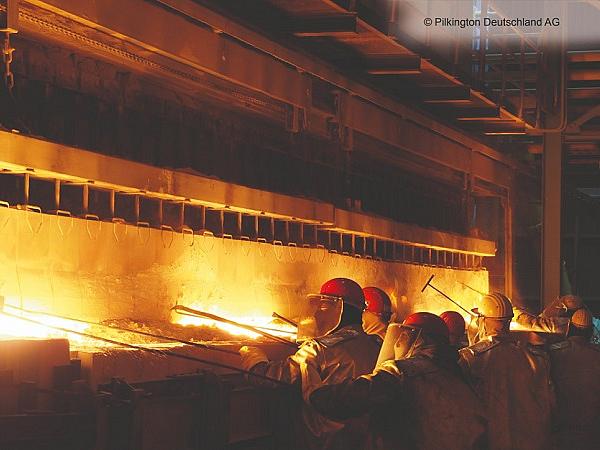
Date: 14 January 2019
Pilkington is part of the NSG Group and produces float glass on two lines – primarily for use as architectural glass. After ten years of continuous operation, the "Float Two" line needed to be modernized with a retrofit in order to ensure production remains economical.
Pilkington decided to use its long-term partner, Siemens, in order to be able to achieve this mammoth project within the 100 day time frame. State-of-the-art automation solutions from Siemens were used to upgrade the line.
This has allowed Pilkington to reduce energy consumption and exhaust emissions through intelligent controls. The open system architecture also provides a high degree of flexibility.
Pilkington is part of the NSG Group and manufactures float glass on two production lines – primarily for architectural purposes.
Over a period of ten years, "Float Two" has produced a remarkable volume of material: With up to 810 tonnes of glass daily, 365 days a year without a break, the line has produced the equivalent of a 3.5-meter wide glass sheet approximately 75,000 kilometers long – enough to go around the Earth twice. In light of this achievement and also because spare parts supply is becoming increasingly difficult, the line has definitely earned a retrofit.
The line had to be completely shut down for this cold repair. As part of the upgrade, the process control system has also been replaced with a state-of-the-art solution from Siemens which had already been tested and approved in a factory acceptance test in Karlsruhe.
"By upgrading to a PCS 7 process control system, we now have a future-oriented investment in place on Float Line 2 which we can operate with complete confidence," says Pilkington Plant Director, Reinhold Gietl.
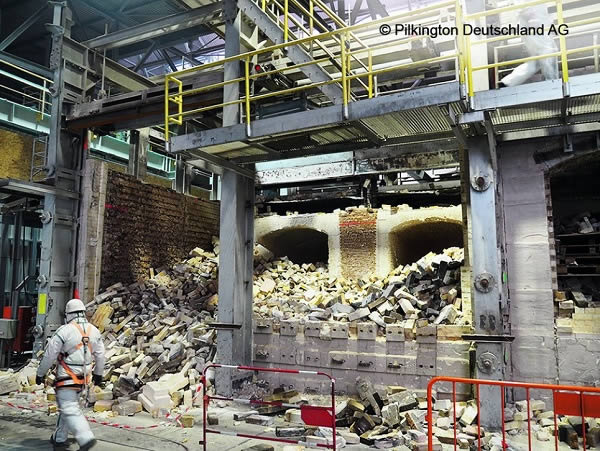
Intelligent, flexible and future-oriented
The new decentralized control system guarantees a high-quality production process as the PCS 7 process control system monitors precise maintenance of all variables during glass production. Intelligent controls also contribute to energy savings and to minimizing exhaust emissions.
The process control system thus provides an optimum technical platform to be able to meet the growing demands on economy, conservation of resources, and environmental sustainability. At the same time, the open system architecture also provides a high degree of flexibility which is a precondition for further technical upgrades.
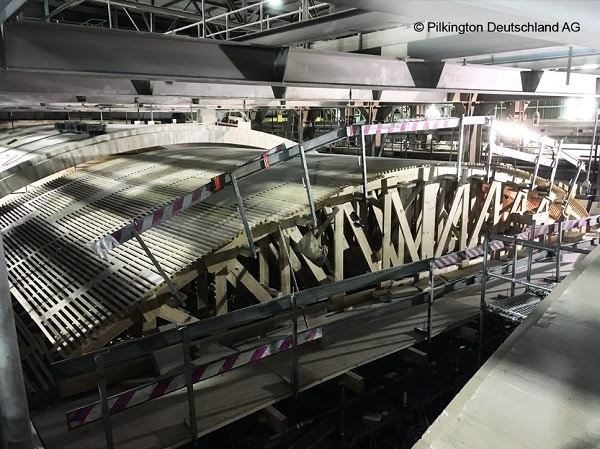
Success through team work
"Our central engineering department at Pilkington worked closely with the Siemens specialists and colleagues from the plant at Weiherhammer during the control system upgrade. The combination of automation and project management specialists worked perfectly," adds Gietl. "It is only through years of intense and proven collaboration with Siemens that we have been able to complete a project of this complexity without any problems in such a short period of time."
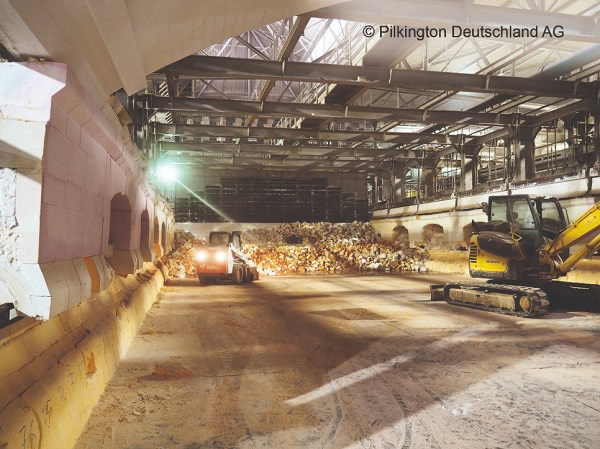
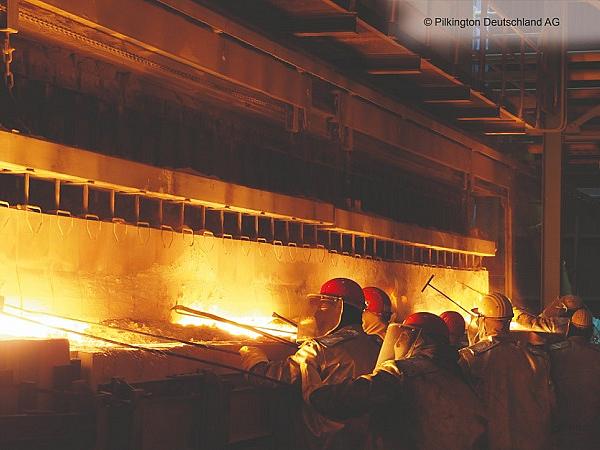

Add new comment