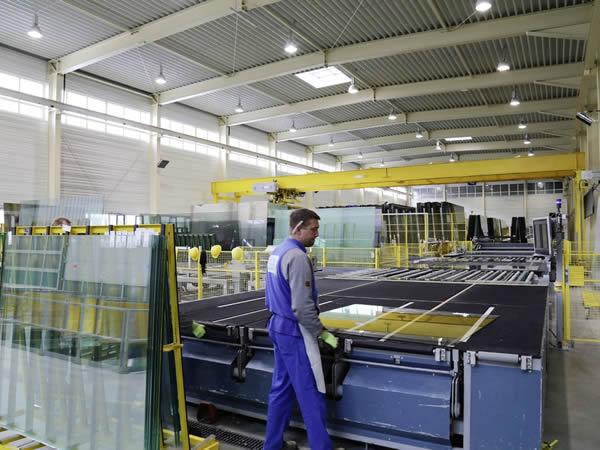
Date: 9 November 2016
Since 1969, 400 specialists have been processing flat glass on a space of more than 50.000 m² in Wagrain, near Salzburg. The high-quality products are furnished with the label Glas Gasperlmair, a promise of quality per se.
85% percent of the manufactured products are installed in Austria, the rest is exported to the neighboring countries. 24 to 30 articulated trucks are leaving the factory per day.
Two years ago, the owning family decided to introduce a software solution by LiSEC – to be specific: capacity planning including production monitoring.
After a period of nine months, the Glas Gasperlmair teams were already working with the new processes and with the capacity planning software. The project took just under two years including fine tuning.
The project is now completed and the success is impressive. A short interview with Mr. Josef Gasperlmair who puts the benefits of LiSEC software solutions in a nutshell.
Can you still imagine your production without LiSEC software?
Glas Gasperlmair: No, not at all. We had reached a size and a variety of products which made the use of software necessary and indispensable.
Without this software we would no longer be able to map the production processes in an economic way.
Which improvements did you achieve by the use of the software?
Glas Gasperlmair: The use of this software had an enormous influence on several parameters. In particular the assignment of the cut glasses to the following processing steps has become much more efficient due to the bar code system: the time-consuming searching of individual glasses is a thing of the past. Let’s take the output rate.
Until recently we produced approximately 7000 sheets per day, now we produce 11000 per day. The process has nevertheless become calmer altogether.
Or let’s take the scrap rate: before we had the software, the rate amounted to just under 2.6%, now the value is 1.4% - this means ready cash! By the way, every company that is not working with a system like that wastes money!
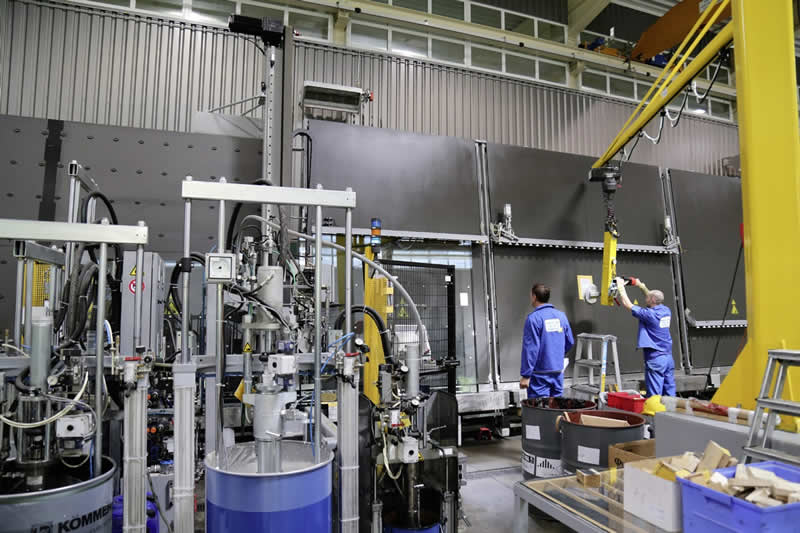
And what about the adherence to delivery dates – has anything changed in this respect?
Glas Gasperlmair: yes – here too, we took a step forward. Before we had the software, we were below 98.4%, now, we achieved 99.6%.
Quite a number of orders were completed by our production, packed on racks and assigned to the individual delivery routes. The glasses are loaded onto the trucks already one day before the delivery.
If processes are optimized and the progress of work is calmer altogether, did the number of occupational accidents also decrease?
Glas Gasperlmair: Definitely. In the past, we had 70 to 80 reportable accidents per year – now we have less than ten. But every accident is one too many for me.
In this context, it must not be forgotten that we have made great efforts in terms of accident prevention over the last three years. For every workplace, we defined and purchased appropriate and safe work wear.
Our employees are instructed in terms of accident prevention two times a year. Meanwhile, we have the instruction available in our factory in more than ten languages. In addition, we have qualified several first responders, who could react competently in case of emergency.
The project including fine tuning took almost two years – how did this go and what is required for this purpose?
Glas Gasperlmair: Two years are a long time. Good nerves and backbone are required in order to implement a project like this. Needless to say that not everything runs smoothly in case of a project of this dimension.
And yes, we also experienced the point when we said: we put a lid on the project and back out. This phase was not an easy one. But: There was no going back.
We have then decided to give us two additional months and to reassess the situation. And this encouraged us to complete the project and chalk up success.
Very helpful in this phase was the collaborative cooperation between our IT department and the experts of the LiSEC software. A high amount of individual modifications, so-called service tags had to be taken care of within a short period of time.
At the same time we had to monitor and adjust the filters on a daily basis. When configuring the screen masks we always seized the suggestions and requests of our administrators.
How do you see the cooperation with LiSEC?
Glas Gasperlmair: I can’t imagine the business without LiSEC. LiSEC is always priority number one with us and has an enormous significance as a partner at Glas Gasperlmair.
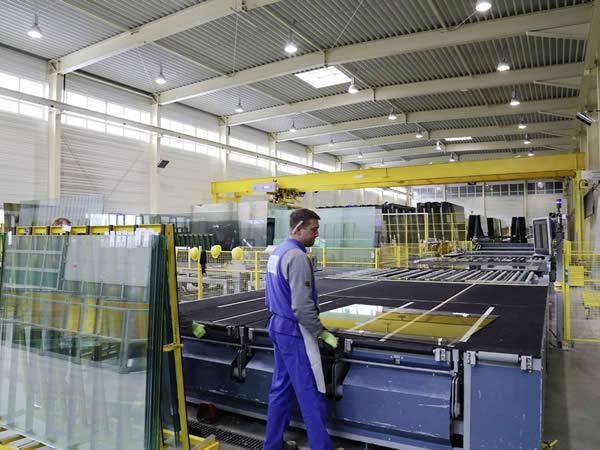

Add new comment