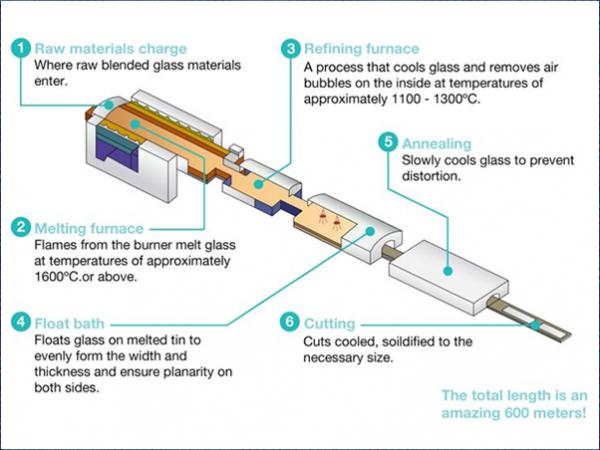
Date: 9 April 2020
This paper intends to inform policymakers on the rationale and implications when flat glass manufacturers decide to switch a flat glass melting plant into ‘hot-hold’. While having recourse to this industrial option is exceptional, it is essential that moving operations to ‘hot holds’ is facilitated when facing unforeseen short-term crisis.
What are ‘hot hold’ operations in flat glass manufacturing?
‘Hot hold’ operations are the only option for a float glass manufacturer to cease production, while preserving the integrity of its industrial equipment.
Flat glass making is a high-temperature continuous production process (see description of the float process in the next page). A float glass plant cannot switch-off production from one day to the other in an uncontrolled manner. The temperature inside the industrial furnace, normally between 1500 and 1600°C, needs to be lowered gradually, while progressively feeding less raw materials.
A flat glass furnace is on ‘hot hold’ when the furnace temperature has been lowered to approximately 1200°C and glass production is stopped. Almost no virgin raw material is fed into the furnace anymore but only scrapped glass eventually. This is meant to maintain the melt within the furnace to the very minimum (mixture of scrapped glass and raw materials which start melting) to preserve the furnace’s inner and outer structures that are made of refractory bricks.
The adequate temperature of a flat glass furnace on ‘hot hold’ is around 1200°C. Lower temperatures would generate a thermal stress on refractory bricks, which would irreversibly damage the furnace.
Why are ‘hot hold’ operations necessary in flat glass manufacturing?
In the event of a sudden and massive drop in demand for flat glass product or of a regulatory instruction to cease production for a few weeks, as is the case in certain countries fighting against the COVID-19 pandemic by limiting industrial activity, moving furnaces to hot holds may be necessary.
In order to cease production, the only other alternative for a flat glass manufacturer would be to take the furnace to a complete cold. Such an operation irreversibly damages the industrial furnace. A furnace turned to cold would require several tens of millions of euros investments for a furnace rebuilt, which would take several months to complete before a restart can be envisaged. The closing down of a furnace is a last-resort option, usually only envisaged when a furnace reaches the end of its 16 to 20 year-lifetime and there is no prospect of increased demand in the medium-term.
By contrast, the integrity of the industrial equipment is maintained during a ‘hot hold’ and production can resume within a matter of days. These hot holds may require that special derogations to industrial permits are granted (see next section). Glass for Europe calls on authorities to rapidly and positively consider these derogation requests in case of exceptional circumstances.
What does ‘hot hold’ entail for float glass manufacturers?
Moving a furnace from production to hot hold status requires three to four days to complete with adequate engineering and a skilled workforce on-site. They must switch-off the downstream part of the production line, supervise the gradual lowering of the temperature and the equipment’s reaction while controlling the melt level within the furnace.
Once on ‘hot hold’, presence of workforce on-site is still necessary to control and ensure the stability of the operation. During the ‘hot hold’, the site:
- No longer produces any saleable flat glass.
- Uses almost no raw materials: either the melt is kept within the furnace or a small ribbon of poor-quality glass drawn out of the furnace is scrapped to be reinjected into the furnace.
- Consumes energy to maintain the furnace temperature, although less than when in production.
- Emits less CO2 than when in production.
- Quantities of pollutants (e.g. particles, SOx) released are considerably lowered, except for NOx emissions. NOx emissions increase exponentially since high-tech dust filters equipping float glass plants cannot operate once the furnace temperature is lowered to 1200°C. As many emission limit values within permits are expressed in mass emission per melted tonne of glass, these emission limit values cannot be met as there is no production of glass.
- Have to request from authorities authorisation to stop the Air Pollution Control system, including the filter, as generally such stop is only authorised for a couple of days per year for maintenance purpose. Derogations may also be needed to allow, for example, for increased NOx emissions during the period.
Moving and maintaining a float glass furnace under ‘hot hold’ is a complex and very costly operation, which generates heavy losses. Hot holds can hardly be sustained over long-periods of time. Recourse to this industrial option is exceptional, yet it must be facilitated when the industry is faced with unpredictable events or sudden and massive drop in demand.
Float glass manufacturing
Float glass manufacturing is one of the highest temperature industrial processes. Both sand and recycled glass need to be heated up to 1600°C to form a ribbon of molten glass. The molten glass then floats on a bath of melted tin to guarantee planarity and control thickness. It is then gradually cooled down before cutting and storage.Hot holds Operations GfE paper April2020
An average float glass installation in Europe produces 650 tonnes of glass a day in furnaces of over 60-meter-long, 25-meter
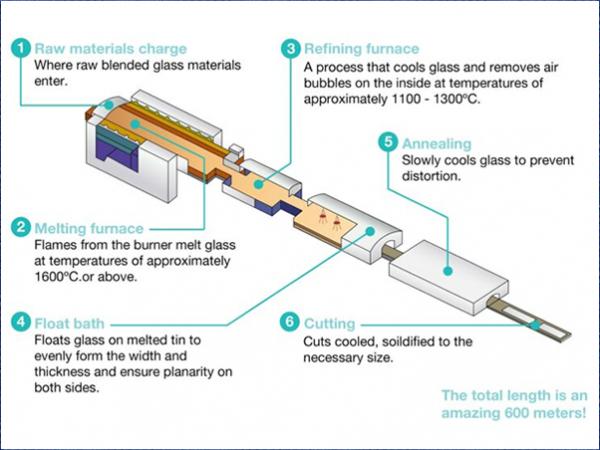

Add new comment