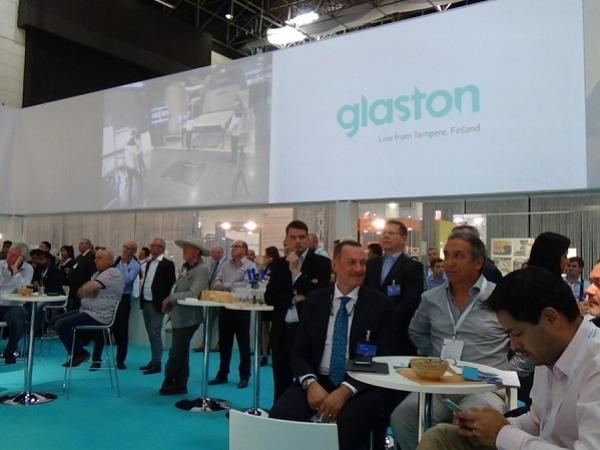
Date: 23 September 2016
At Glasstec, Glaston is making the most of smart connectivity. In live demos, the performance of the all-new flat tempering lines is demonstrated as well as the advantages of Glaston Insight, the online application that gathers global processing data. The flawless glass quality, the ease of use and the real-time reporting can be experienced twice per day.
Taking the online leap
Continuous R&D is one of Glaston’s cornerstones. During the past few years, therefore, the company has thoroughly investigated how to take advantage of new smart technologies, interconnected machines and on-line reporting.
“We see a lot of potential in the new smart technologies and they play a central role in our product development. The journey of digitising the heat treatment business has just begun and we invite our customers to join us,” says CEO & President Arto Metsänen.
FC Series – a Masterpiece of Intelligence
At Glasstec, Glaston is again setting new flat tempering standards with the renewed RC and FC Series.
“With the live demos, Glaston wants to demonstrate the built-in process intelligence, the top quality of the end product and the ease of operation,” comments Metsänen.
Flexible loadings and high loading efficiency are essential when looking for high capacity and lower production costs.
“During the live demos we want to show how it works when the 4, 6 and 8 mm Low-E glasses are flexibly processed. As the loading enables maximal flexibility the glass thickness can be chosen by the audience during the demo. The furnace incorporates the intelligence of Glaston Insight Assistant™ which automatically adjusts furnace settings based on the measured glass size and loading pattern information,” explains SVP Machines Sasu Koivumäki.
For today’s demanding Low-E coatings, highly efficient heating control is needed. Not all heating systems on the market are equal, however.
“Effective and accurate heating is the key to high-quality, high-capacity Low-E glass production. The new FC Series furnace ensures Low-E capability with low waste rates and high glass quality.
The intelligent bottom scanner is a good tool for verifying that the glass is heating uniformly. Compared to a traditional scanner, which isn’t optimal in Low-E glass production, the bottom scanner provides reliable measurement data for Low-E glasses.
A bottom scanner can be integrated with the Glaston Insight Assistant Pro™, which uses the information to automatically make recipe improvement suggestions,” says Koivumäki.
Best anisotropy
Anisotropy is currently a hot topic in the glass processing industry and Glaston has actively studied and developed technology to minimise this phenomenon.
For example with Glaston’s new slot nozzle design in the chiller, stress level differences, and thus anisotropy, can be radically reduced.
“We shouldn’t accept bad anisotropy. With the live demos we want to show that anisotropy can be considerably reduced with the FC series,” says Koivumäki.
Genuine commitment
Glaston Insight brings a lot of interesting possibilities to customer’s production and service operations, for example on-line access to production data and control.
“An online connection obviously brings a range of benefits, as you can analyse production parameters without delay and even without actually being at the factory. Online reporting provides tools to improve machinery productivity, uptime and, most importantly, profitability. Glaston Insight Assistant™ automatically adjusts furnace settings based on the measured glass size and loading pattern information,” explains SVP Services Artturi Mäki.
At Glasstec also GlastOnline, the Parts Arena that ensures continuous production, is introduced. “This is a new era of online spare parts service, available 24/7. This tool is a tailored parts catalogue that meets the customer’s needs, and you can quickly enhance your maintenance performance for all Glaston equipment,” says Mäki.
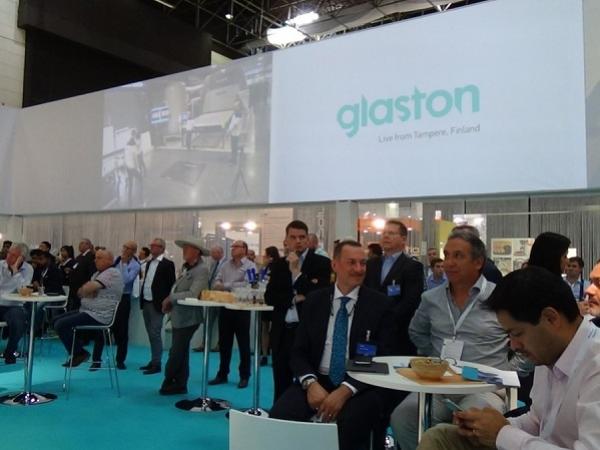

Add new comment