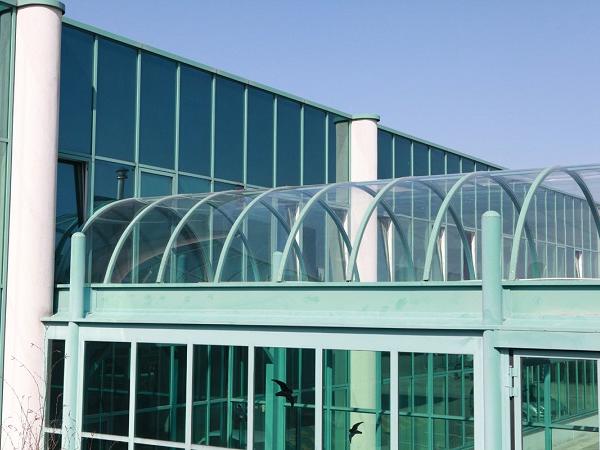
Date: 22 January 2018
Thin glass – as thin as a razor blade or a human hair – is a reliable method to protect smartphone touchscreens, sensitive filters and sensors.
Yet despite its extreme thinness, it is also highly resilient and scratch-proof. Furthermore, thanks to its flexibility and bending properties, it permits totally new applications in architecture, mobility and other industries.
Thin glass is opening up new markets and turning visions into reality. How this works can be seen at glasstec 2018 in Düsseldorf.
Just as smartphones, tablets and e-book readers have changed the way we communicate and convey knowledge, scratch-proof touchscreens have produced totally new qualities in the manufacturing of glass, thus enhancing the performance of this material which has accompanied the history of mankind's development since the first advanced civilizations.
Ultra-thin protective glass seems more like film than glass and is so bendable and flexible, that it can even be rolled up and transported to customers on rolls (Fig. 1, 2). Special manufacturing processes are now available, allowing for the production of ultra-thin glass films which – at 25 μm (0.025 mm) – are even thinner than a human hair or razor blade.
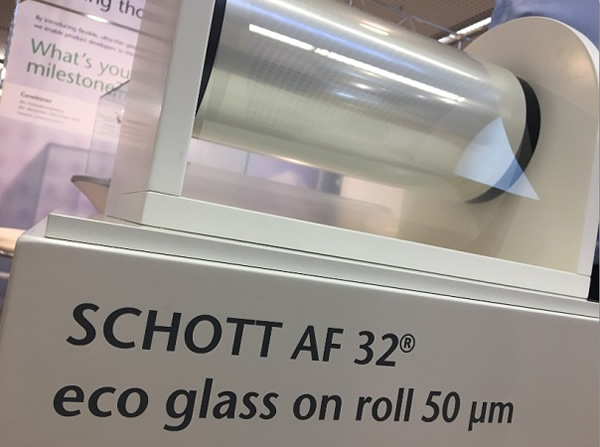
(Photo credit: Schott AG)
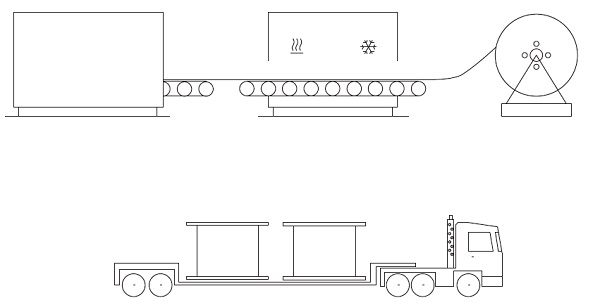
(Photo credit: Timon Peters, Technical University of Darmstadt)
Thin glass – manufacturing methods and definition
The starting material for production is molten glass which then passes through rollers and is drawn upward or downward from a tank in what is known as an up-draw or down-draw process (Fig. 3, 4).
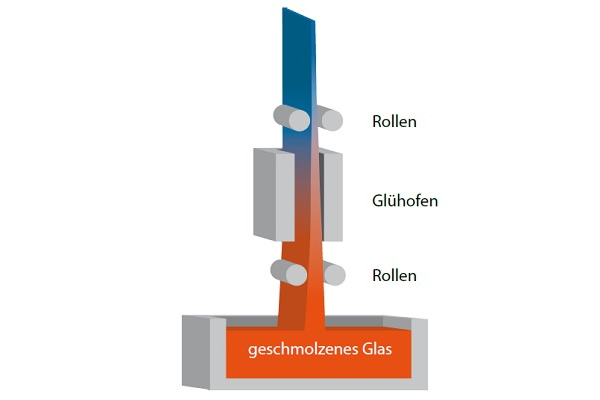
(Photo credit: Schott AG)
It is then left to cool down on the production line as a film with the required thickness, ranging from 25 μm to 10 mm. Alongside these two methods – which, incidentally, are older than float glass manufacturing – thin glass can also be produced with different specifications, using overflow or micro-floating processes.
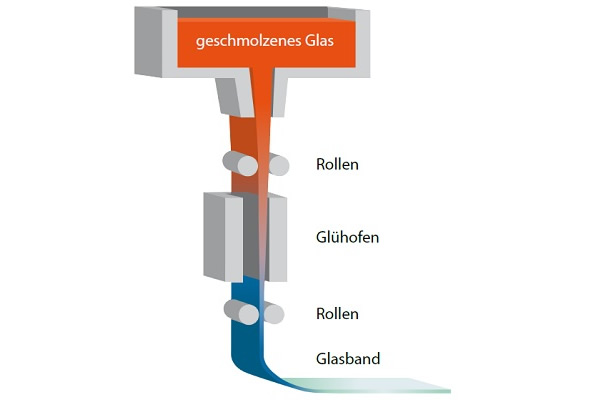
(Photo credit: Schott AG)
Whichever method a company chooses, the decisive element for the properties of thin glass is the formula of the molten glass, which differs from one manufacturer to another and is a well-guarded trade secret.
Thin glass is in demand for a wide range of products in numerous industries (Figs. 5 and 6) and can be classified quite differently, depending on its thickness.
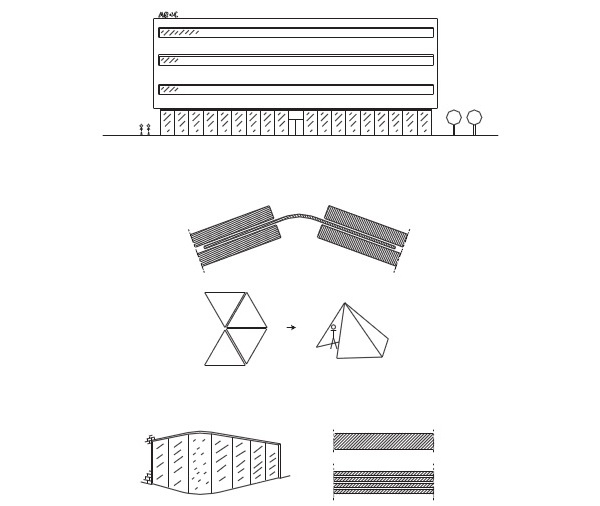
(Photo credit: Timon Peters, Technical University of Darmstadt)
Whereas in construction and architecture, glass is considered to be thin if it is below 3 mm, with virtually no reasonable or practicable use for thicknesses below 1 mm (and no measuring in micrometres). The needs are quite different elsewhere. In media technology, for instance, 2-mm glass would be regarded as rather thick.
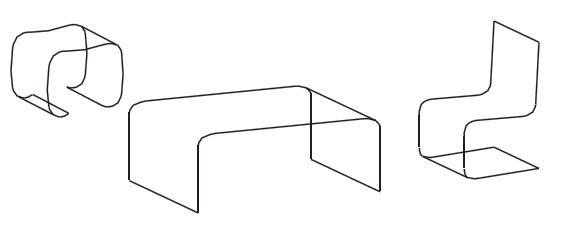
(Photo credit: Timon Peters, Technical University of Darmstadt)
This industry commonly measures thickness in micrometres, and ultra-thin glass down to 20 μm tends to be treated as film (Figs. 7 and 8) and shipped on rolls. In the construction industry thin glass can therefore be produced under a conventional floating process where minimal thicknesses are commonly around one millimetre.
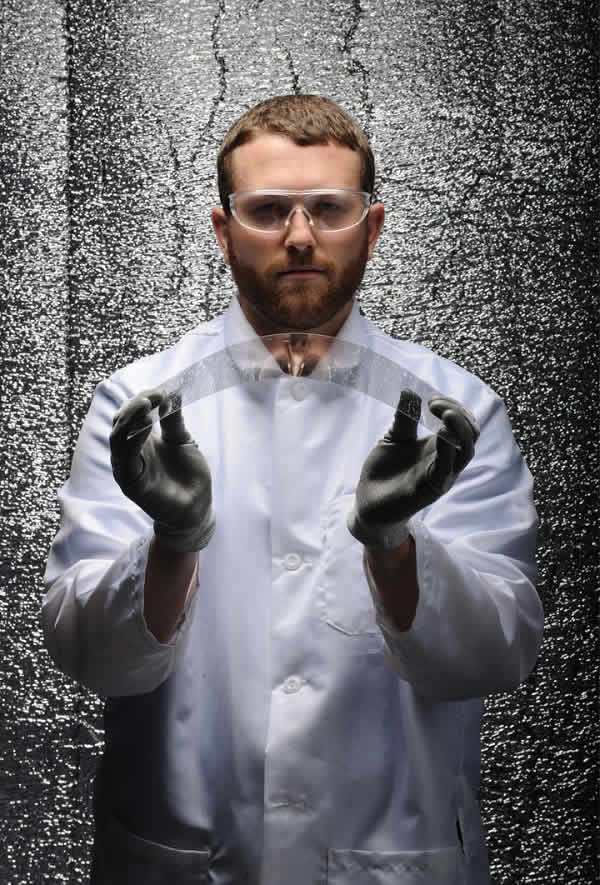
(Photo credit: Corning Inc.)
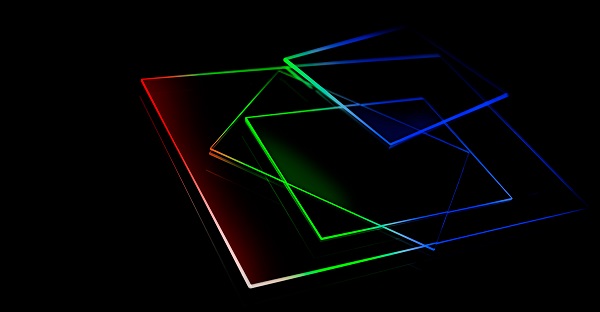
(Photo credit: Corning Inc.)
The benefits of thin glass are its material and constructional qualities, on the one hand, and its low weight, on the other, e.g. in combination with other glasses, such as multiple insulating glasses (Figs. 9 and 10).
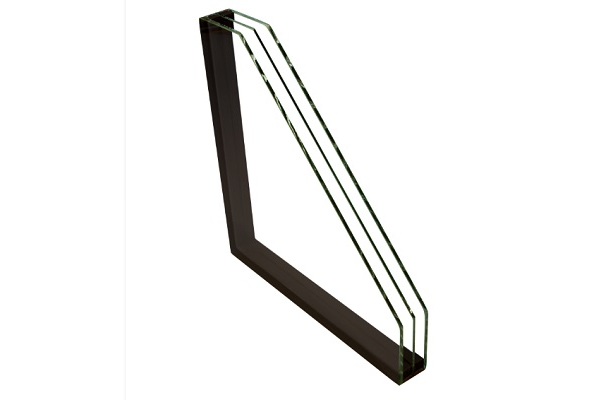
(Photo credit: Lisec Austria GmbH)
The stability and resistance of thin glass can be further enhanced through chemical tempering – something which is particularly in demand for displays and protective covers on smartphones. Other applications are protective covers for microscopic instruments and near-infrared filters for smartphone cameras.
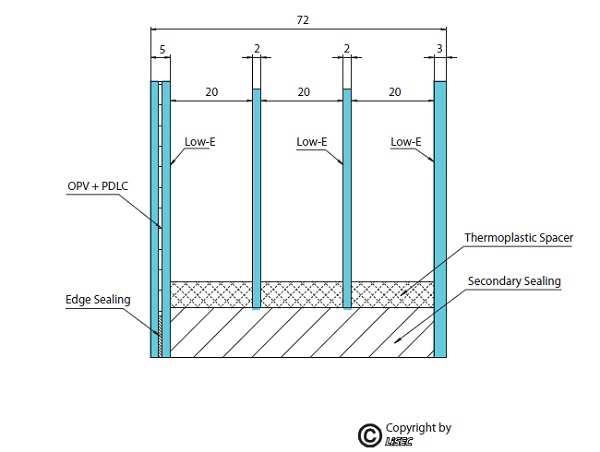
(Photo credit: Lisec Austria GmbH)
Thin glass in construction and architecture
The construction industry, too, uses thin glasses to cover a wide range of applications where polymer solutions have their limits (e.g. the coating on solar panels). Compared with a plastic film, glass is far more heat-resistant, keeps its shape, is gas-tight and has outstanding visual qualities.
Thin glass is being used more and more for the middle pane in triple glazing, where it allows a clear reduction of thickness and weight.
A pane structure comprises an outer float glass pane (4 mm in thickness), a semi-tempered middle pane (2 mm) and another float glass pane on the inside (3 mm). Compared with conventional glazing (4/12/4/12/4), this combination reduces the weight from 30 to 22.5 kg/m2. The benefits of light, thin glazing are particularly noticeable in refurbishment projects.
In architecture thin glasses not only reduce weight, but also excel with their combination of breakage resistance and high flexibility, allowing specific customisations. Moreover, they permit new and variable options in shape and design, as it is possible to add specially treated coats to thin glass, e.g. through grinding or screen printing.
However, such applications are still more a matter of vision than everyday use (Figs. 11 and 12). Other forward-looking applications include integrated functional coats such as OPV (organic photovoltaics), where energy is harvested via windows and switchable PDLC coatings (polymer dispersed liquid crystal). This technology permits the creation of cloudy, opaque viewing guards which only become transparent under an electric current.
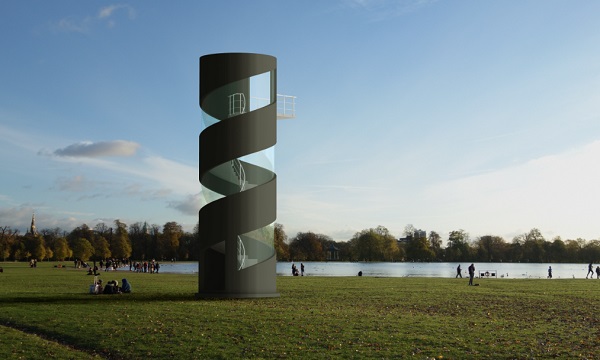
(Photo credit: Timon Peters, Technical University of Darmstadt)
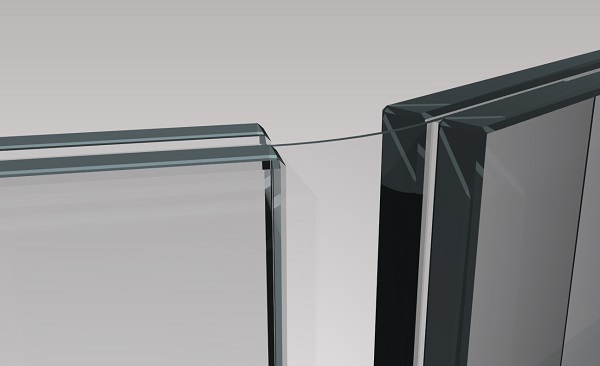
(Photo credit: Timon Peters, Technical University of Darmstadt)
One specialist in this type of technology is the Austrian company LiSEC whose vacuum coating process with diffusion-proof edge seals also protects functional coats from humidity and environmental impact. At glasstec 2018 LiSEC will present, among other things, suitable machines for the treatment of thin glass (Fig. 13).
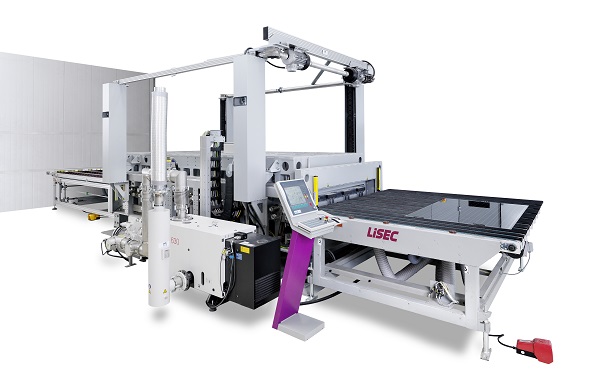
(Photo credit: Lisec Austria GmbH)
Thanks to thin glass technology, curved glasses, too, may well become increasingly established in architecture. Tempered thin glass can be bent into the desired shape on site either through cold bending or installation bending (Fig. 14) and can then be used as single glass or as a coat. It is an inexpensive alternative to hot bending at the factory. Furthermore, cold-bent glass has excellent visual qualities, due to fewer distortions.
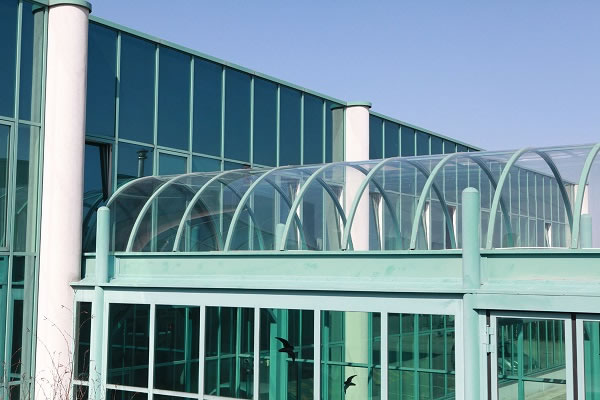
(Photo credit: Lisec Austria GmbH)
Thin glass in media technology and automotive engineering
Thin glass in the micrometre range makes glass particularly flexible, and indeed without compromising on stability and hardness. One company that specialises in the development and production of ultra-thin glass is SCHOTT, which uses its own down-draw technology.
Its project AS 87 eco has led to what is currently the world’s thinnest glass, at only 25 μm (Fig. 15), and is now mass-produced for sensitive applications (e.g. fingerprints) and optical components (camera filters) in smartphones, where it offers reliable protection. The market for this type of glass is enormous.
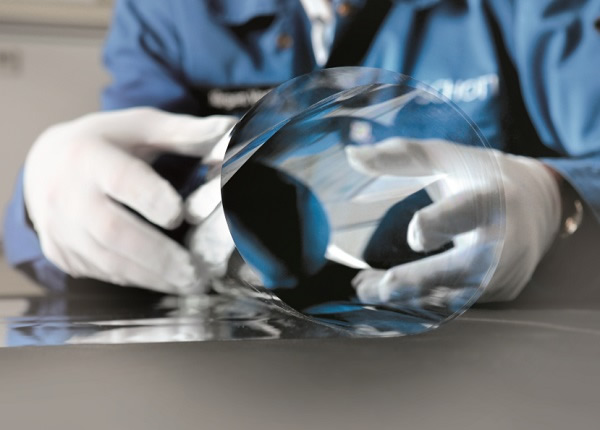
(Photo credit: Schott AG)
There has been a steady rise in the demand for fingerprint sensors alone and also for special solutions to protect such sensitive components. Whereas in 2014 the number of units shipped to customers was 316m, this figure rose to nearly 500m in 2015, and the forecast for 2020 is currently as high as 1.6 billion units.
Fire-polished protective glass is amazingly hard and is therefore also used for smartphone displays. Moreover, it is as thin as a razor blade, which makes the precision of the manufacturing process particularly remarkable. With a thickness tolerance of only ten micrometres or less, it promises a high level of reliable safety and quality.
Thin glass is also becoming more and more desirable in the automotive industry – for the interior, for freely shaped windscreens and for the cockpit.
Here, too, digitisation has long been a well-established feature. It is a domain where highly resistant, scratch-proof ultra-thin glass below 250 μm can be used to its full advantage, particularly in convex and concave geometries.
Glass does not age and is therefore superbly suited for the panelling of vehicle interiors. Whereas, in the past, such applications involved a risk of injury in an accident and were therefore unthinkable, thin glass has now achieved such a high level of stability, almost unlimited mouldability and superior optical qualities (e.g. for touchscreens), that it has opened up totally new paths in automotive engineering and has become the alternative to plastic.
Its optical qualities and homogeneity are far better, and its chemical and thermal resistance are so high that it can easily withstand humidity, UV radiation and high temperatures.
Tomorrow’s visions can be admired at glasstec 2018
Furthermore, flexible thin glass is also opening up new innovative options in virtual, mixed and augmented reality (i.e. the computer-aided enhancement of our perception of reality). One vision for tomorrow’s electronics is to achieve a good level of bendability (Figs. 16 and 17) without compromising on the outstanding visual qualities, clarity and valuable tactile properties of glass.
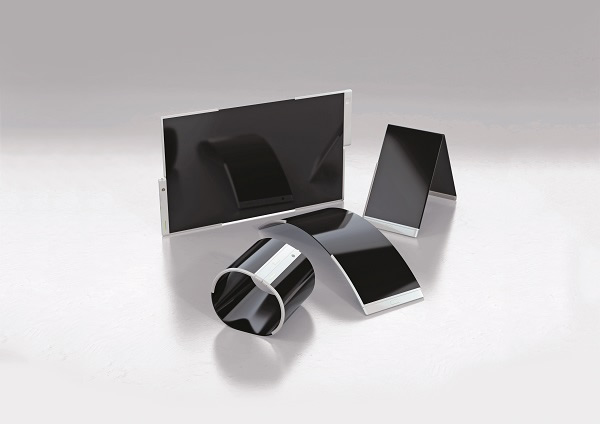
(Photo credit: Schott AG)
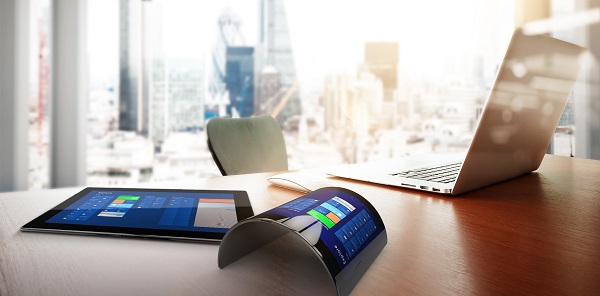
(Photo credit: Schott AG)
glasstec, Düsseldorf, 23-26 October 2018
International Trade Fair for Glass – Production, Processing and Products
From 23 to 26 October Messe Düsseldorf will be the venue of glasstec 2018, the well-established leading global trade fair on glass as a material. In sheet glass the main focus at glasstec 2018 will be on interactive glass, while in container glass it will be on energy-efficient and emission-reducing technology for glass production.
The most important target group for exhibitors is the glass industry, followed by mechanical engineering, architecture, the construction industry, the German trade sector and increasingly also the trade sectors of other countries.
The last glasstec in 2016 attracted 40,105 visitors from 121 countries and had 1,237 exhibitors from 52 countries, presenting their latest products, machines, developments and visions.
One element that makes the trade fair especially attractive to exhibitors is the large number of decision-makers among trade visitors, of whom three quarters come from middle to senior management and who either come to glasstec with specific investment plans or who want to find new suppliers.
What matters to trade visitors is meeting qualified contacts, concentrated demonstrations of innovative strength and a visionary outlook on future developments and business opportunities.
All this is presented at the special show glass technology live in Hall 11. The show is managed by Prof. Ulrich Knaack (Technical University of Darmstadt), who is extensively networked with numerous other universities, including Dortmund and Dresden in Germany and Delft in the Netherlands.
Four glass cubes will be presented here, featuring innovative solutions from the areas of interactive façades / display glasses, energy and performance, construction glasses (solid and thin glasses) as well as forward-looking technologies. Hall 10 as the glass conference venue will feature ideal thematic combinations of theory and practice in the form of conferences.
Claudia Siegele
Born in Stettfeld (Baden) in 1963. Studied architecture at the University of Applied Sciences in Karlsruhe from 1988 to 1994. 1994 to 2004: editor for the German construction industry magazine db deutsche bauzeitung; has run her own architectural studio in Ubstadt-Weiher since 2. 2004: founded the editorial office frei04 publizistik in Stuttgart together with Dr. Ursula Baus and Christian Holl. Technical author and author of books on architecture, civil engineering and energy-efficient construction. Technical journalist and editor for a range of printed and online publications, including Gebäude-Energieberater, greenbuilding and Marlowes. Currently living in Karlsruhe.
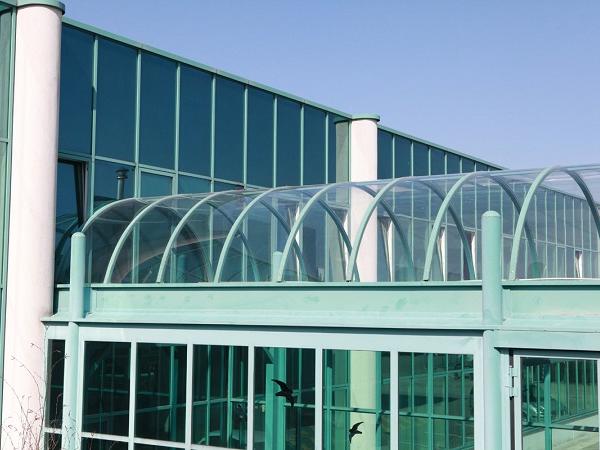

Add new comment