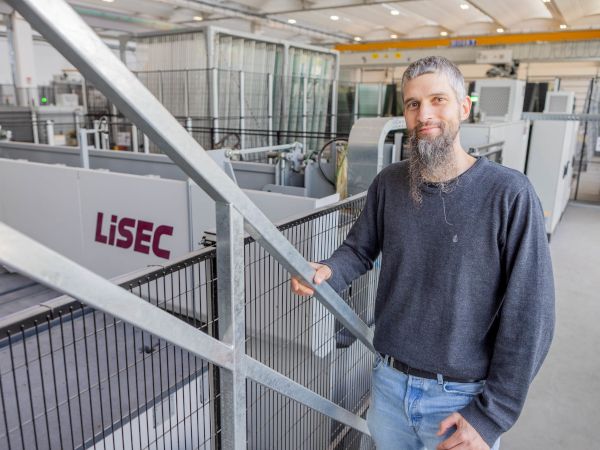
Date: 15 January 2025
Finstral is a family business that was founded in 1969 by the Oberrauch brothers and, with over 50 years of company history to reflect back on, can rightly claim to be a pioneer in window construction from South Tyrol. With around 1,650 employees and 14 sites – including four in Germany and ten in Italy – Finstral covers the entire value chain of window construction and has been run by the family's second generation since 2020, with a focus on sustainable success. Its portfolio ranges from profile development and glass production to final assembly. The company has been using LiSEC products since 1980 and has continuously expanded its LiSEC machinery.
Finstral: Quality, sustainability and innovation are key
Finstral offers a broad spectrum of products. These include the FIN-Window and FIN-Project products in various materials and designs, as well as front doors (FIN-Door), sliding doors (FIN-Slide) and glass walls (FIN-Vista). The products offer Finstral's customers a decisive advantage when it comes to modularity, quality, durability and aesthetics.
But the South Tyrolean company not only focuses on top quality products with high delivery reliability; it also considers sustainability and forward-looking future planning to be key – for example, Finstral plans to be climate-neutral by 2030. This goal has been supported by continuous monitoring since 2012 and ISO 50001 environmental certification. The company has already succeeded in bringing down its carbon emissions by around 80% and is only using green electricity. Furthermore, the organisation is also putting the buzzwords "digitalisation" and "automation" into practice and giving these solutions to the employees as tools. The aim is to increase employee motivation and replace redundant work processes with more challenging tasks using digital tools.
LiSEC & Finstral: Innovation, expertise and reliability
The co-operation between Finstral and LiSEC is a long-standing and fruitful partnership that began in the 1980s. Finstral sees LiSEC as a competent, innovative and reliable partner. "LiSEC designs and builds nothing without looking to the future, something that requires the right expertise – and LiSEC certainly has this in-house. This applies to production at LiSEC itself, production planning at the customer's premises and the handling of new projects," enthuses Florian Oberrauch, one of the managing directors at Finstral. "LiSEC's long-standing employees are an important factor in the company's expertise and therefore also its success. The company is constantly trying out new things and working on innovations. The connection between the machines and the software is just one way in which you can see the company's true innovative strength – just like the all.in.one:solutions. LiSEC's reliability is reflected in the longevity of its machines; they run faultlessly over long periods of time and in doing so contribute to the company's efficiency and productivity."
Finstral at the Oppeano site: Highly automated glass processing for efficiency and quality
One of Finstral's most impressive production facilities is located near Verona in Italy. This plant uses highly automated production processes with machines from LiSEC and is not only a showpiece for LiSEC – Finstral is also delighted with this production facility and is proud to show off its perfectly designed system to its customers.
The plant includes a large glass storage facility with LiSEC crane solution PKL / SBH (fly-over). A special feature of this is the inloader removal system, where an HGV drives directly into the warehouse, sets down a glass storage rack and drives out again. The PKL / SBL suction bridge removes the sheet directly from the HGV rack and either takes it to the loading tables for cutting or stores it elsewhere in the glass storage facility. This process is fully automatic and requires no manual intervention by the operator.
A central remnant plate storage system (RPS) can be operated from all three cutting lines, which means that only one RPS is required. A GFB with VSL-A double bridge solution is available for glass cutting. This fully automatic configuration enables precise and efficient cutting of laminated glass. Another LiSEC GFB with VB for combined cutting is equipped with a breakout table on which the glass is processed manually. The finished sheets are then fed to the sorting system by the operator via a vertical measuring and feeding station. Pure float cutting using ESL-RS offers automatic X and Y breaking, which further increases efficiency. The operator at the breakout table is only responsible for the Z-breaks and residual fractures, after which they push the sheets horizontally on the air cushion table into the sorting system. The situation is similar with the VSL-A: Once cut, the sheet is simply pushed along the air cushion to the tilting table and then fed into the sorting system. Another advantage of this system is that the operator can simultaneously check the quality of the sheets during transport on the air cushion. This not only increases efficiency, but also ensures high product quality.
After cutting, the sheets undergo various processing steps and can either be used directly for IG production or further processed using a LiSEC KSD machine, a LiSEC washing machine and a scanner for quality control. The sheets are then sent to the sorting area, and from there to the insulating glass line. Finstral operates two insulating glass lines, each with its own processing machine. Downstream of the washing machine is another quality scanner on both lines.
A production highlight for Finstral is the LiSEC VSL-A for laminated glass cutting. The logic with which the two cutting tables work and communicate together underwent continuous improvement in the first few months. "When you work with LiSEC, you are part of a team. Both parties seek to identify the best solution during joint meetings. We greatly appreciate the open relationship with LiSEC," says Florian Oberrauch, Managing Director at Finstral. The resulting optimisations led to a considerable increase in production volume; today, Finstral produces up to over 30 jumbo plates per shift. Optimum utilisation of the two cutting systems is a major step forward and means that as much can be cut on two cutting systems as would normally be possible on three systems. This saves on both space and investment volumes.
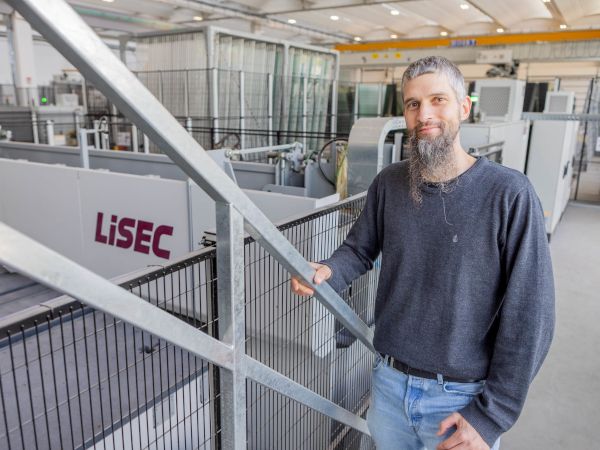

Add new comment