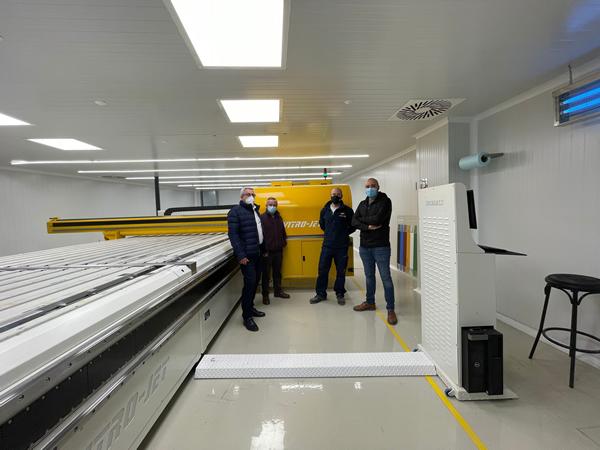
Date: 22 December 2020
The new trade agreement between Cristalería Vinalsa and Tecglass S.L is already a solid reality since our novel digital printer Vitro-Jet “The Thunder” - has been successfully installed in September 2020 at Vinalsa factory in La Rioja (Spain), as part of a complete printing line, a turn-key solution manufactured in-house for mass production in automotive and architectural glass.
The Vitro-Jet “The Thunder” is a revolutionary new concept, pointedly refined for high demanding conditions and intended for companies covering different business sectors in need of having an all-round machine with greater speeds , like Vinalsa does, as a reference in the architectural and automotive market.
It is a multifunctional machine, which without need of any color change, provides dizzying speeds for two colors in pure Single Pass for glass widths below 1.200 mm and the speeds of its predecessor - FS Side Kinetix - in Multi pass for printing all base colors simultaneously. With 36 optimally arranged double print-heads, the Vitro-Jet "The Thunder" becomes the fastest digital printing machine on earth.
The integration of the Vitro Scan at the printer inlet has also made the glass positioning left behind, being nowadays a process fully automated and optimizing production cycle times even further. By means of the Vitro Scan, the glass sheet is quickly and automatically scanned detecting the shape, positioning, thickness and dimensions of the glass making the printing process perfect to the millimeter , being particularly handy for irregularly-shaped glass sheets.
For Tecglass Sales Manager - Mr. Manolo Ramos - being faithful to the familiar and proximity principles that are the hallmark of Tecglass, it is a privilege that a company as Vinalsa becomes now our partner, expecting this new partnership to be extended over a long-term relationship.
Hardly needs any introduction, with a production facility of 8,000 sqm and more than 100 employees, Cristalería Vinalsa is an European benchmark in the manufacture of digitally printed glass with a long term background experience with these technologies.
After 4 months of experience already handling our technology, we had the opportunity to interview Mr. Alejandro Arenzana - Director of Cristalería Vinalsa – to deepen their experience up-to-date with the new Tecglass printing line:
What were the main reasons leading Vinalsa to take the decision of a new supplier for your digital project?
Well, we are not new to this, a few years ago we decided to bet strongly for digital printing technology, since we understood that we had to walk in that direction to optimize our processes and be more competitive, as these new technologies have evolved exponentially in recent years. Our demand has grown considerably and the technology we were using has never met our expectations with the industrial capabilities demanded nowadays in terms of productivity, versatility and speeds.
As you know, time is money in order to be competitive, and the continuous halts in production we were facing in cleaning the machine on daily basis, making continuous color changes depending on the orders incoming, has led us to make the decision to switch, since new solutions with a much higher degree of efficiency are now available on the market allowing us to keep up our commitments with all our customers.
Why has Tecglass finally been your choice for this new adventure?
We knew Tecglass perfectly, they are a leading company in digital printing and not far away from us, but at the moment we decided to bet on this technology on 2017, we decided to go with another supplier convinced that we were making the right decision.
As I said before, we were not satisfied with the performance of the new machine purchased and we contacted Tecglass again to look for alternatives. We knew that their technological growth had been enormous in recent years and after deep discussion about our issues and future needs they have provided us with an incredible solution with this new printer they have developed, the Vitro-Jet The Thunder , which has simply taken us to another level we did not know before. After visiting their premisses and see the machine in action we had no doubt that it was exactly what Vinalsa was looking for.
To date, how has your production evolved with the Tecglass printing line?
It has been great! Obviously was not a walk in the park, new machine, new technology, new supplier and of course there is always a learning curve you need to go through to fully adapt to the new printing line, but Tecglass team has honestly made the process really smooth to us, they have a great technical team who has made the transition between technologies been perfect for our operators and designers.
After we finalized the complete training provided by Tecglass specialists, we have been in production for three months and our expectations has been more than met. We are able to cover all our product range in an outstanding production time and the possibility it gives us the Single Pass mode we have for two colors for all glass sheets up to 1.200 mm width is just amazing. We do not have to touch at all the color configuration in the Tecglass printer, regardless the order we process, this just plays now for us a significant advantage at all levels saving time, cost and avoiding any halt in production.
You mentioned that you don't make colour changes on the machine now, how important is this factor for Vinalsa?
Well, for us this is a fundamental aspect to keep up and running constantly without having to worry about modifying the machine and new set-up every time we switch from one project to another.
A relevant factor of digital printing in comparison with traditional methods is precisely the flexibility and versatility that this technology provides to cover all type of artworks, you just need a digital file and that’s it. If this technological advantage is limited because you have to make colour changes continuously depending on the job, then obviously the optimisation of production is directly affected.
The colour disposition provided by Tecglass has solved definitely to us this issue we previously had. We have now always 8 colours available in machine at full speed and we never have to worry about flushing or cleaning the printer, our team handling the line just need to keep focused in producing. It simply fits perfectly to us.
What aspects would you highlight as differentiating factors now, that you have experienced two different technologies?
Now we have the experience about being working with the most representative players within the digital glass printing industry, we have seen that there are remarkable differences between both technological concepts.
Nothing further from reality, the final outcome is a digitally printed glass, but the processes, handling operative, degree of automatization, production capacities and after sales support provided really differs from one technological concept to another, and this factor is what made the difference for us when it came the time of the decision making.
There may be many facets to remark, but I would mainly highlight two aspects that for me have made a huge boost to Vinalsa , both in terms of quality and quantity.
Firstly, and this is an undisputed evidence is that we have now been able to multiply our production by 4 within the same working hours in comparison with our previous process.
And secondly, is the fact that Tecglass operates as a single contractor providing us the complete line fully optimized and synchronized. This has really been a key aspect; we have drastically reduced the number of operators involved in managing the digital line and with Tecglass washing machine in line the qualities are optimal, operator only have to worry about feeding the line with glass and the rest comes on its own, we don't have to worry about any preheating of the glass to ensure a good fixation of the ink drop, the cleaning of potential residues or even cleaning the glass again once it is printed and dry to remove any overspray.
This is undoubtedly a factor to be highlighted as it has generated an enormous impact on our production processes, putting us in an incredible position to be competitive in this increasingly changing and demanding market.
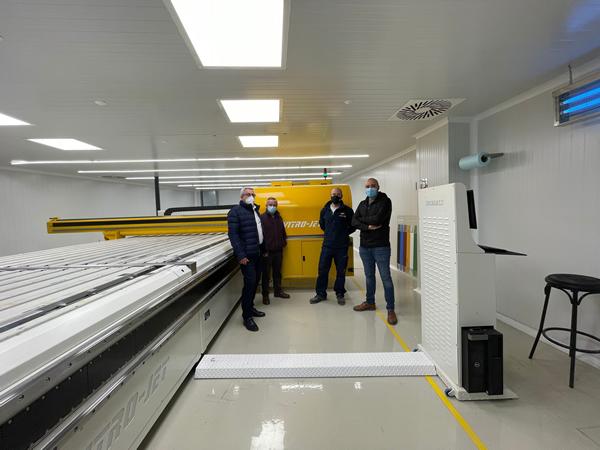

Add new comment