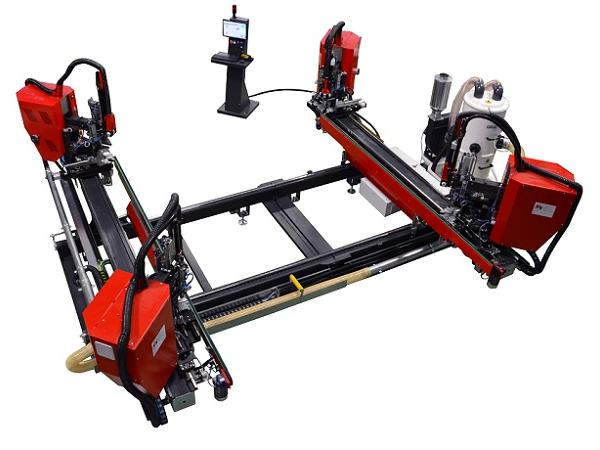
Date: 6 September 2016
First exhibited by Promac at the FIT Show in 2014, having pre-cleaned to exacting tolerances the SL4FF, zip welds the frame corner joints, whilst controlling the flow of sprue, delivering a seamless but incredibly strong window frame.
The on board control system and CAD Scan software maps the profile chamber configuration directly from a standard photocopier scanner, which allows the operator to work with actual dimensions rather than profile related drawings.
This brings a new level of accuracy and finish perfection, eliminating grooving to create a smooth weld, ideally suited to the welding of foiled product
Kurt Greatrex, Sales Director, Dekko, explains: “If you look at the market there just aren’t that many fabricators with the capability that the Graf machine gives us. We can manufacture a window that’s different and our customers can sell a window that’s different,” he says. “We see it as a real commercial advantage.”
Set up by Greatrex and Managing Director, Gary Torr in 2007, Dekko fabricates more than 1,400 frames per week from its 55,000 sq ft manufacturing capability.
Having started out manufacturing Deceuninck and Kommerling, Dekko later added an aluminium system from Reynaers – and the Residence 9 from Eclectic, to its portfolio in 2013.
The decision to carry R9, was instrumental in setting the fabricator on a course to build a premium offering alongside its standard ranges. The Räum Infinity is its latest product to be launched by Dekko within this camp.
Available in Deceuninck’s 2500 or 2800 profiles, it features a seamless corner weld - manufactured using the Graf Synergy SL4FF Seamless Corner Welder.
“We’re not looking to rubbish traditional manufacturing. We’ll continue to make windows using traditional reverse weld joints”, says Greatrex. “But what’s inescapable is the quality of seamless weld, the smooth finish and the mechanical jointing of the transom and mullion. It’s a much ‘crisper’ window with equal sightlines and stronger aesthetic”, he continues.
FACTBOX: SL4FF/SL4FF EVO
- Pre-cleans to exacting tolerances then zip welds the corner joint whilst controlling the flow of sprue, delivering a seamless but incredibly strong corner joint
- On board control system and CAD Scan software maps the profile chamber configuration directly from a standard photocopier scanner – allows the operator to work with actual dimensions rather than profile related drawings
- Production control data can be input directly at the machines side or via USB, bar code or networked via Ethernet.
- Profile height compensation – identifies profile tolerances and automatically adjusts to median welding height/operator alert system
- Cutting error compensation of up to 2mm length or vertical/horizontal angle of 1 degree
- Parallel welding
- Increased welded angle breaking point
While market forecasts predict window industry growth as a whole at a steady five per cent per year to 2020, they share Greatrex’s analysis that there will be more aggressive pockets of activity. PVC-U foils and flush finish profiles, identified as areas of accelerated growth.
“The Räum Infinity is pitched at the more ‘affordable end’ of the premium market. We can manufacture it efficiently and it should be much more affordable but still deliver something that’s aesthetically far stronger than standard 70mm systems”, concludes Greatrex.


Add new comment