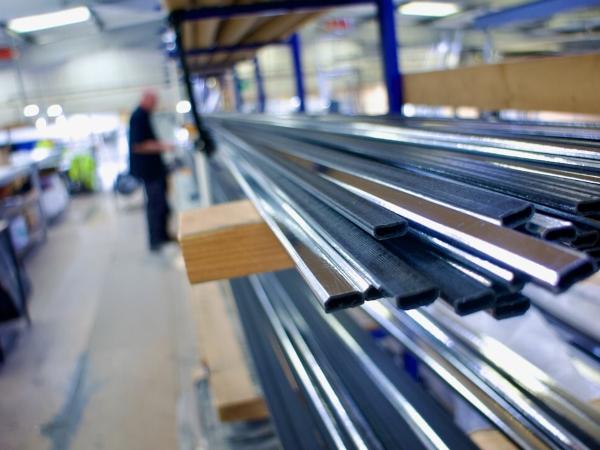
Date: 7 May 2024
The supply of IGUs into the glass and glazing industry is highly technical, with multiple points where a mistake can cause premature failure.
With an IGU, different environmental conditions compete to inflict damage on a product which, once installed, cannot actively protect itself. Sunlight, moisture, wind, heat, cold, and even atmospheric pressure seek to degrade the unit from the moment it is installed.
Once that unit leaves the factory it must be fault-free, and the company installing must be confident that once installed, they won’t be called back to repair or replace it.
Cost of success
Given what I’ve described above, it shouldn’t come as a surprise that units occasionally fail, and problems continue to occur if we don’t learn from our mistakes. In my experience, a significant threat to the integrity of a unit is where manufacturers cut costs and cut corners.
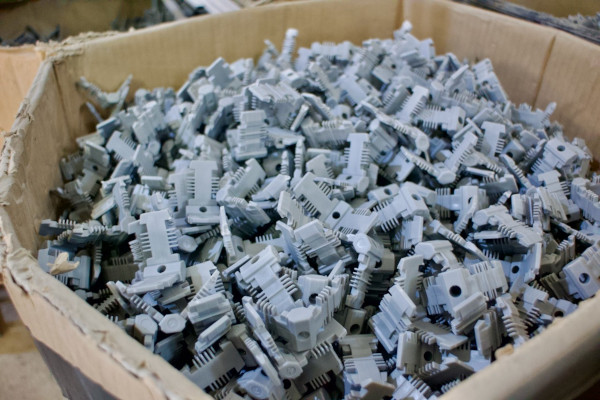
This isn’t necessarily because that component is cheaper. In fact, quite often cheaper components will function better than more expensive alternatives.
Typically, a unit will be designed that will work faultlessly for many years beyond the warranty of the IGU. But that comes at a price. So, if you are making hundreds or thousands of units a week, a small component replacement can have a positive impact on your overheads.
But IGU manufacturers sometimes don’t explore the possible effects of swapping out components, even when their customers expect an exceptional warranty period relative to the cost of the IGU to cover the replacement of the whole unit.
A decision to save money by replacing components – ignoring technical arguments made by suppliers – could result in a liability that could bankrupt an IGU producer some years down the line. This would leave the installer to pick up the tab on worthless warranty promises, leaving them in an unprofitable situation as well.
That component could be any number of things. It could be reduced desiccant, reduced depth of seal, poorly applied sealant, or less robust spacer bar. In some cases, they will be of a poorer quality, using raw materials that aren’t up to the task they are designed for. We often see this with desiccant.
In other cases, individual components are swapped out but they may not be fully compatible with the components that have already been specified. For example, a chemical that naturally leaches out over time in one component can degrade the integrity of a component it is in contact with. We often see this happen with the cloth tape that IGU manufacturers protect the edges of the units with.
Test, test and test again
One way to overcome these potential shortfalls is to test the components and test their compatibility within a unit. We have extensive testing facilities at our site in Wigan where we have invested in high-end equipment to measure the performance of our products.
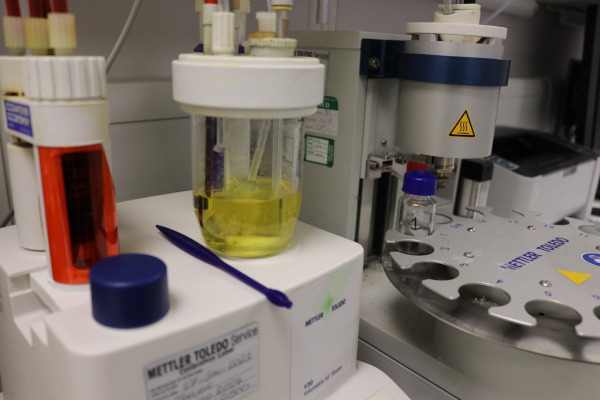
First, we make sure each component performs and lasts as we say it does, and we test all components together in unts to make sure there is not issue with cross contamination.
Let’s take the desiccant for example. We test our desiccant by putting it in our cycling cabinets. We have one set up to do EN1279 Part 2, and a second one dedicated to high humidity cycling. This saturates units day after day, so we know exactly what is required of our products.
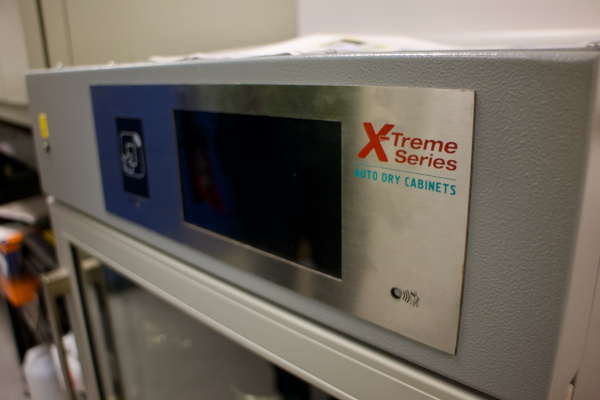
All our desiccant is continually batch-tested and benchmarked against other market-leading molecular sieve desiccants, and we randomly select product from our warehouses for performance testing. Every shipment is tested and delivered with a Certificate of Analysis.
We will also go one step further: we can test our customers’ units to see if they will perform as promised.
Yes, there is a price attached to the perfect IGU, but there is also a price for failure. Together we can produce the perfect unit.
For more information, please visit www.thermosealgroup.com, or call 0121 331 3955.
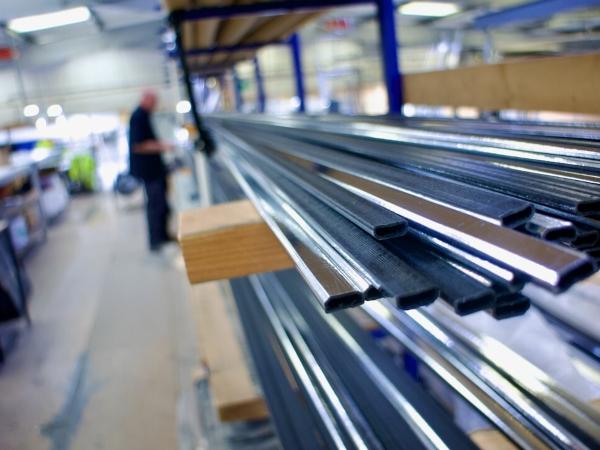

Add new comment