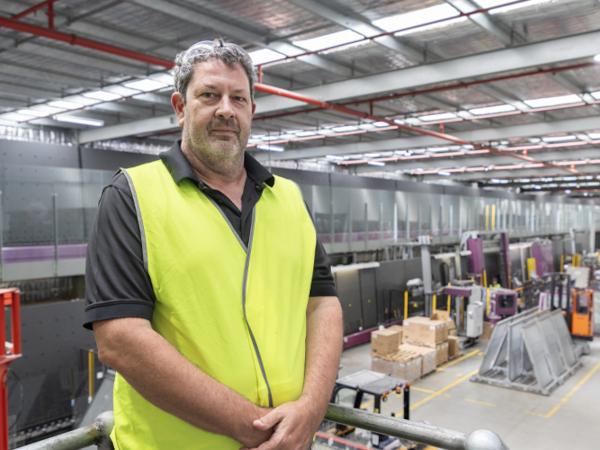
Date: 14 August 2024
How do you optimise production output within limited space, while also connecting different machines that are physically separated?
VENTORA and LiSEC have found a suitable solution to overcome this challenge that is tailored to the local conditions at VENTORA and forms the basis for achieving the company's strategic automation targets.
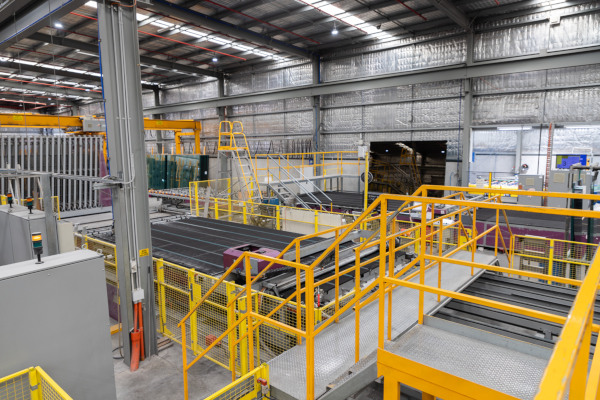
VENTORA, which was known as JELD-WEN Australasia or STEGBAR before July 2023, is leading the way in the development and production of doors and windows. With an established reputation for innovative design, unrivalled craftsmanship and outstanding customer service, the company has been providing reliable doors and windows for homes, apartments and commercial buildings for over 50 years.
VENTORA designs and manufactures a wide range of windows, doors, partitions, showers and similar products.
Dave Pakeman has been working as Operations Manager at VENTORA in Rowville, Australia, since 2014 and can draw on decades of experience in the glass industry.
When he started out in the 1980s, he was still being confronted with manual production processes in glass finishing. Following a sideways career move into window production, he returned to find that the world of glass finishing had developed significantly – and had become mechanised and interlinked. Today, the aim is to manufacture products in highly automated processes and deliver them to the end customer as quickly as possible.
A highly integrated plant that supports the machine cells in the production flow by means of slot rack cart logistics and a LiSEC automation solution is indispensable; this is how the VENTORA plant (back then still JELD-WEN Australasia) became the first highly automated plant for the production of shower doors and more at that time.
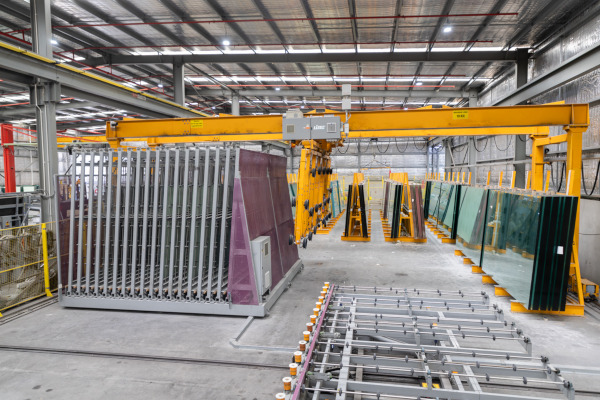
How do you maximise production capacity in limited production space?
There's no such thing as impossible! Making the most of limited space requires extensive experience, product knowledge, as well as creativity, outside-the-box thinking and unorthodox ideas when implementing solutions.
"LiSEC's Technical Sales Service is highly innovative with its approaches and solutions and has a suitable layout for every challenge," says Dave Pakeman, who is responsible for the complex system network at VENTORA. In addition to the specialists from LiSEC, as a LiSEC automation expert Matthias Schöbl, Head of Software Sales, was also involved in the planning and implementation:
"It is always a pleasure to see this automated plant with so few manual interventions after so many years. The machines, which were initially connected to slot rack carts, and the several extensions with buffer solutions demonstrate the flexibility of the underlying automation solution from LiSEC. The expansion of the glass processing plant to include the production of insulating glass was a logistical challenge. Instead of consistently developing the existing slot rack cart concept, we combined this concept with the available buffer solution. The space restrictions were resolved by opening automatic buffer areas in the mezzanine level and automatically connecting the insulating glass line. Furthermore, the single glass shipping buffer has made production more flexible, reduced manual sorting work to a minimum, and increased production output. This plant, which I have had the honour of providing support to for over 15 years, demonstrates the successful implementation of expansions and adaptation to the requirements of a dynamic glass market that our customers have to face on a daily basis."
The highlight of VENTORA's production: a buffer store installed on the mezzanine level, which can supply the machines on the ground floor via a LiSEC SHL lifter, thereby offering more options in a limited space. This finally opened up the third dimension in glass finishing.

Specifically, this is what the process at VENTORA looks like:
Downstream of a LiSEC PKL glass storage system with remnant plate storage, there is a GFB for cutting float glass and a LiSEC ESL cutting table with an automatic X, Y, Z breakout system, which in turn is connected to a LiSEC KSR and KSV, i.e. a glass edge seaming machine for rectangles and shapes.
Instead of a normal sorting system, a LiSEC slot rack cart automation system (FWA) was installed, which is docked to various stations: a LiSEC WSL, i.e. a water jet cutting system from LiSEC, as well as various grinding machines and a tempering oven. The tempering oven is automatically loaded by the slot rack carts, the tempering bed is automatically created, moved into the tempering oven and automatically removed again with LiSEC roller / belt tables (RWF).
The sheets are then sorted, which is where LiSEC's innovative solution for VENTORA begins.
The sheets are either placed in packing sequence on the LiSEC GAL (a packing line that places the sheets on the rack using cord layers), or the sheets are transported up to the mezzanine level, where an additional storage unit is installed, via a LiSEC SHL lifter. Both the LiSEC VSA insulating glass line and a line at the other end of the hall can be loaded in the correct sequence via this mezzanine level. The transport routes therefore offer the option of connecting machine areas on the ground floor via the mezzanine floor without taking up or blocking production space. The buffers have been optimally planned.
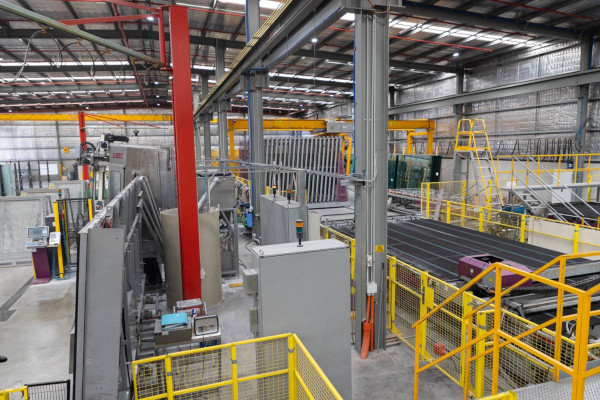
How do you connect systems and machines?
Optimised solutions thanks to the right software
"The LiSEC software is outstanding. It allows the entire plant to run in a highly automated manner, and the integration of third-party machines is possible without difficulty," says Dave Pakeman, describing the LiSEC software used. The LiSEC software installed largely covers all process steps, and comprises: order – for order management or quotation and order processing, cadcam – a LiSEC CAD solution or design program for flat glass processing, prod – a LiSEC software for the organisation and planning of production batches, and ident – which informs the user about relevant details such as breakage and completion reports, as well as LiSEC software tools for shop floor management such as autofab, lineserver, perfectscan and mon.
"When I describe LiSEC's USPs to someone in the industry, certain persuasive points always come up: Automation and software from a single source," says Dave Pakeman. "Everything is connected and we only have one point of contact. From the moment the order is entered, you no longer need to worry about anything – the production batches are scheduled seamlessly! And on top of that, the LiSEC machines are more than just reliable."
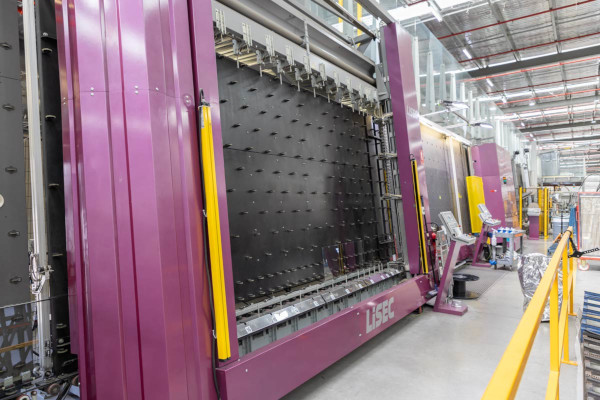
A great advantage of a good partnership: support in every respect
VENTORA also found a competent partner in LiSEC when it came to selling their infrequently-used laminated glass system. The search for a buyer was supported and completed with success.
[1] In July 2023, JELD-WEN Australasia became VENTORA and part of Platinum Equity's portfolio of companies.
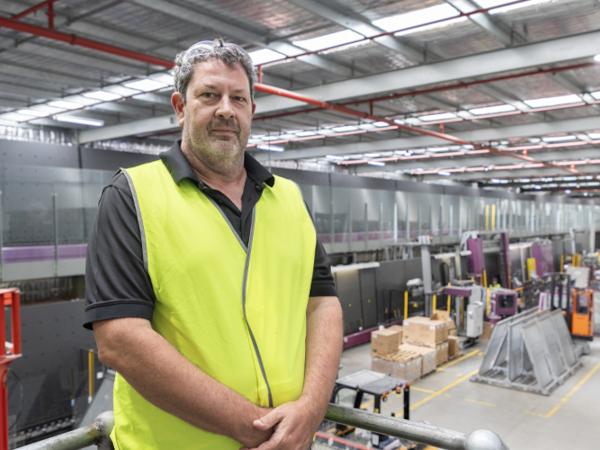

Optimizing production output within a limited space while connecting machines that are physically separated is a challenge that many manufacturing facilities face. VENTORA, formerly known as JELD-WEN Australasia or STEGBAR, has successfully addressed this challenge by implementing a highly integrated and automated solution in partnership with LiSEC. interior design orlando