This paper was first presented at GPD 2023 by Louis Moreau MOGLEX Corporation, Québec (QC), Canada.
Link to the full GPD 2023 conference book: https://www.gpd.fi/GPD2023_proceedings_book/
Author
- Louis Moreau - MOGLEX Corporation, Québec (QC), Canada
Abstract
During more than 10 years of working with complex laminated assembly, we were often asked to replace failed components, or find an explanation for a collapse. We always tried to understand the root causes of those events and come up with experiments to validate our hypothesis.
Since the original Apple staircase, metallic components embedded in glass laminates have been used more and more. We will show why some metals can be dangerous.
Multilayer laminates are used to increase strength, redundancy and residual capacity, but some configurations can lead to catastrophic failures.
In previous GPDs we introduced our work on optical phenomena that happen with rigid interlayers. We will do a quick review of our work on anisotropy that paved the way to two new standards to quantify it in architectural glass.
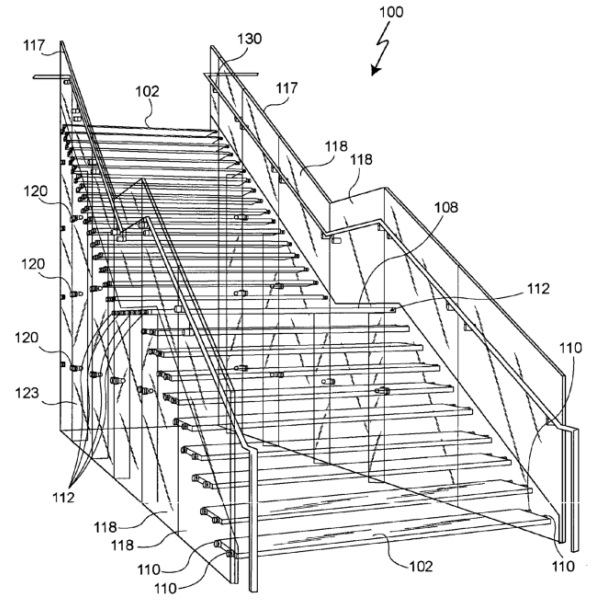
When Steve Jobs et al. filed their glass staircase patent in 2003, they set up the base of modern structural glass:
- Use Ionomer interlayer.
- When possible, use annealed glass.
- Use titanium embeds.
Stiff interlayers
Shear is an action or stress resulting from applied forces that causes two contiguous parts of a body to slide relatively to each other in a direction parallel to their plane of contact. The shear modulus (G) is a measure of the rigidity, expressed in MPa.
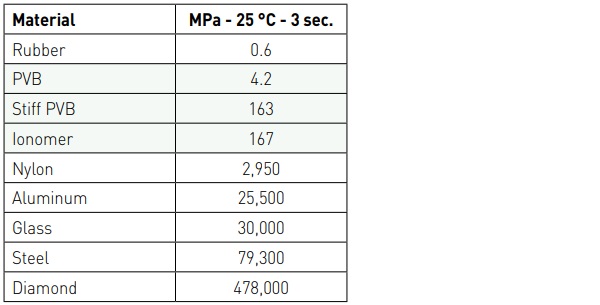
Interlayers being plastic, their properties are greatly influenced by their environment. Temperature and time are critical.
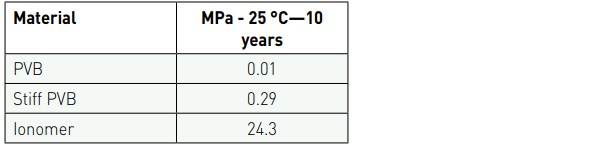
Those numbers show that stiff PVBs cannot be used where long duration loads or higher temperature exist. However, they are excellent material for short duration stress like wind loads encountered in a façade.
The adhesive bond strength to glass is very strong and even greater to metal.
Other properties, like resistance to water and extreme temperatures, are also driving factors when choosing a stiff interlayer
Embeds
Embeds are generally metallic and allow interfacing mechanical fasteners to glass. In laminates, they are located inside holes or notches and are secured by the interlayer. The ionomer is the interlayer of choice to embed materials because of its fluidity at the autoclave cycle temperature (135 °C).
Embeds are preferably made of titanium, but stainless steel and aluminum ones are found. Those three metals are very different when it comes to their thermal expansion coefficient α.
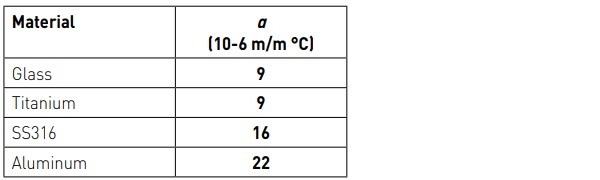
My most challenging project used a T-shape titanium rail in a triple laminate. It was supporting a 990 mm wide, 175 kg door.
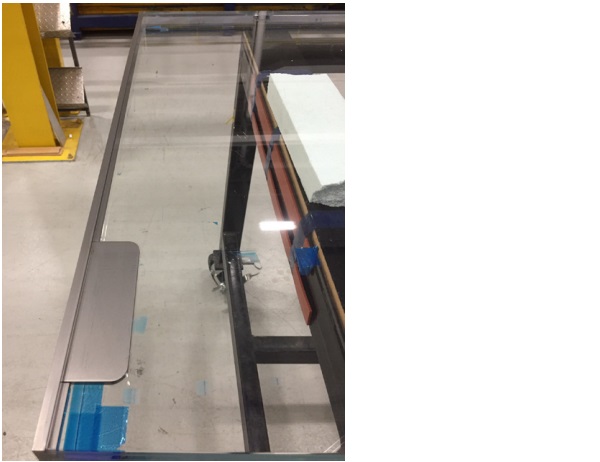
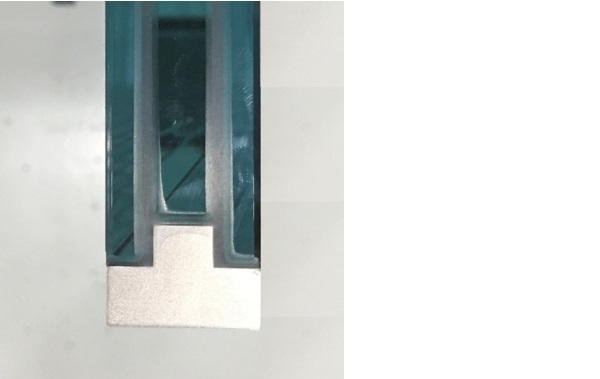
Even at this length, it has been very stable. We used a small round stainless-steel insert for the handrail. The puck is chamfered, so it is mechanically stable in a countersink hole. A Delrin sleeve wraps its body. It was successfully used in a quadruple laminate on the Onassis staircase stringers.
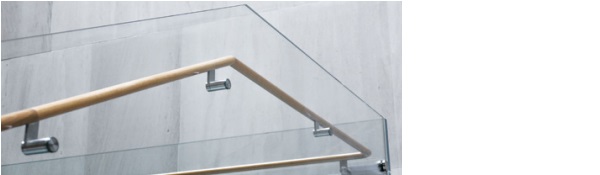
AGNORA has also used these threaded inserts to attach signs to glass.
More recently, a customer asked to embed his own cylindrical stainless-steel pucks. After installation, a delamination inside the laminate was noticed around some pucks.
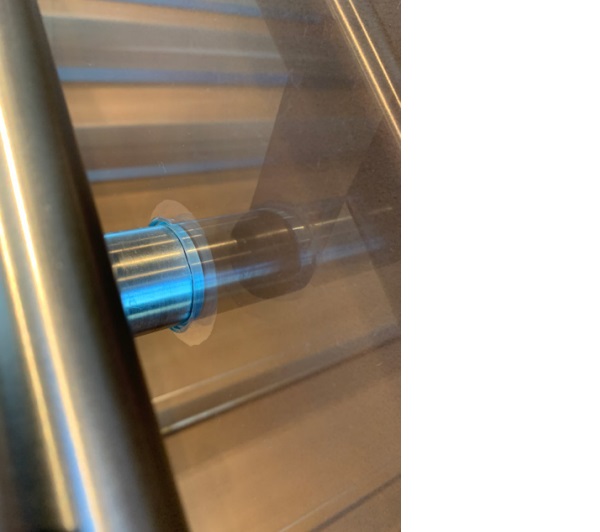
I started investigating different configurations.
- Cylindrical SS
- Chamfered SS
- Chamfered Aluminum
- Chamfered SS with Delrin sleeve
We made 10 mm on 10 mm annealed laminate using 1.52 mm SentryGlas. After processing, the laminates were frozen overnight at -19 °C. The results were stunning and coherent. All metallic inserts pulled and cracked the glass around them!
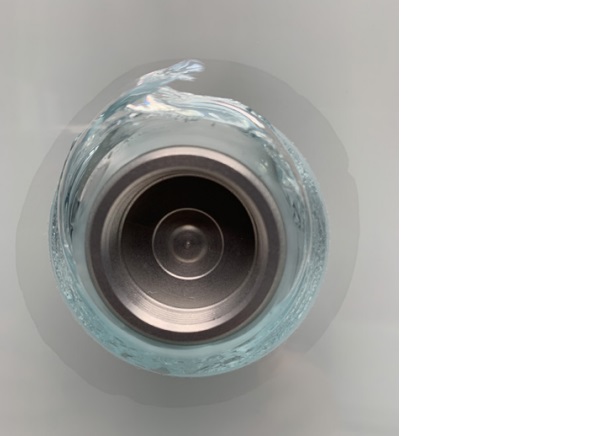
Only the SS chamfered with Delrin came out unscathed. The Delrin acted as a bond breaker around the insert.
Multilayer laminate
A friend sent me this picture taken in Manhattan in September 2014.

It was a large triple 12 mm laminate with six aluminum inserts in the middle layer. The outer ply was intact but completely delaminated, the middle fully tempered (FT) layer was shattered. With only this picture, I could not identify the problem, and told the installer it was probably uncured laminating resin. AGNORA supplied replacements using an ionomer. During transportation, the same large laminate shattered for unknown reasons.
Speaking to a European engineer, I shared the picture of the complete delamination. He told me that he witnessed the same phenomenon. We concluded that the expansion of the middle layer, caused by cracking, shears the surface of the glass. It is not an adhesion failure; it is a cohesive failure of the glass. The ionomer has enough adhesive strength and is so stiff that it acts like the ancient horse glue used to produce glue chipped decorative glass.
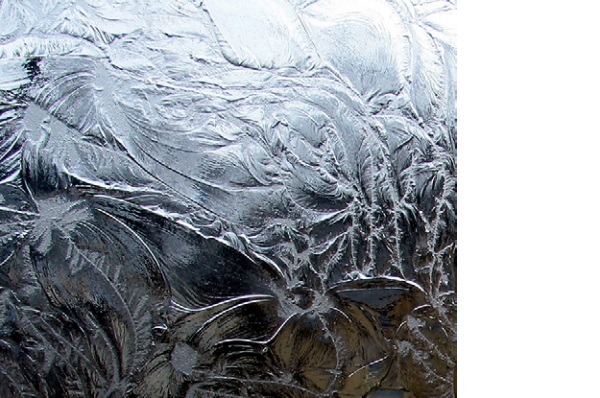
Finally, at the last GPD, I attended a workshop¹ where the presenter confirmed my observations. He recommended to never use a FT layer inside a multilayer laminate.
After my last fall experiments, I connected the dots for the Manhattan replacement: the aluminum insert in the middle ply of a triple laminate shrank more than the glass surrounding it. Because of the ionomer properties, it broke the FT glass. In the original glass, the middle layer expansion caused a complete delamination. In the replacement glass, the laminate did not separate.
Optical
Haze
Another aspect to consider when using stiff interlayers is the haze. SentryGlas is a hazy material (up to 2% for 1.52 mm), stiff PVB haze is an order of magnitude less.
The cooling rate in the autoclave influences the haze level. Kuraray recommends a cooling rate of 1 °C/min. This is obtainable on thinner laminate like 6 mm on 6 mm. It becomes much more problematic on very thick (> 4 × 10 mm) laminate because of the thermal mass involved. The haze is proportional to the thickness of SentryGlas used.
This cloudiness is seen in this Montréal project where a 14 layer cantilever meets an 8 layer beam.
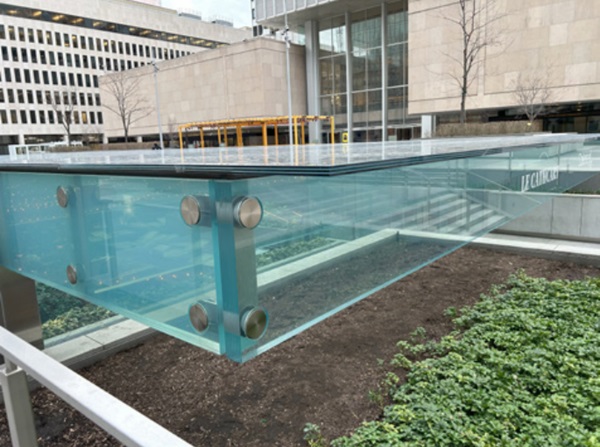
Colour
Stiff PVB Yellowness index can be high compared to SentryGlas. Some manufacturers compensate the yellowness to harmonize the edge colour, but this results in a bluer light transmission.
Anisotropy
At GPD 2019, I presented on anisotropy. To keep you updated on the subject. The “Standard Test Method for Measuring Optical Retardation in Flat Architectural Glass” ASTM C1901 went live in January 2021. One of our team members, Steffen Dix, continued to work on the subject for his PhD and led the German specification DIN 18198. It was published in English last October.
Conclusion and Takeaway
The choice of structural interlayer is conditioned by several factors. The load duration and service temperature remain crucial. The ionomer offers the widest range of configurations, but stiff PVBs are efficient in wind and snow load applications.
The material of choice to incorporate in glass structures is titanium, but other materials can be used if a bond breaker is used.
When designing multilayer laminates with ionomers, it is important not to incorporate FT components inside the assembly.
Watch for the optical effect in thick laminates.
¹ “all-glass constructions: requirements for design and engineering”—June 26, 2019 | Christoph Bauchinger (Seele), Martien Teich (Seele), Stefan Marinitsch (Arup).