Arch. Lavinia Chiara Tagliabue
Principles and Problems of Integration
Photovoltaic modules are components used for the production of electricity from solar energy and, thanks to their morphological and constructive configuration, are suitable for integration in the external skins of buildings.
Their application and integration, however, involve some problems that must be pointed out if we want to optimize the technological and energetic performance of the modules and obtain the correct interaction between them and the other energy installations, the building and environmental conditions.
Thanks to the safety, reliability and durability of components available on the market, operators of the sector are carrying out experiments and testing different ways of using photovoltaics, even considering the substitution of traditional building elements, with valid results both at architectural level, as well as with regards to energy performance.
Despite numerous positive experiences, we can still see how the availability of ‘solar’ areas suitable for the integration of active conversion components is not proportional to the real use of building practices that include the use of photovoltaic modules among their technological options.
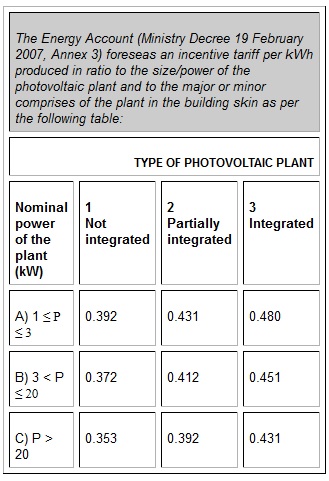
The mechanical, acoustic, hygrometric and thermal characteristics of photovoltaics are compatible with the needs and parameters of other construction materials, after, of course, due considerations and assessments. However, these modules are usually created as additional devices, which are positioned onto a building already constructed using components with functions as per the norms in force, satisfying the performance requirements of the building.
Their combination with the technological requirements of the energetic functions of the building skin, not included previously in the requirements of buildings, considers photovoltaic components as additional elements, to be added at a later date and often placed close together. This is due to a consolidated construction culture that conceives buildings as containers that use energy produced by systems to maintain optimum comfort.
This, in other words, means that buildings are energy users, and must control, protect, make safe and carry out passive adjustment of the flow of energy and material which, coming from the outside, integrate with the building. The installation of these systems is carried out in technical rooms and comprises the distribution of the energy needed for the air conditioning of the construction by means of devices in the walls or in the loft, as well as in floors.
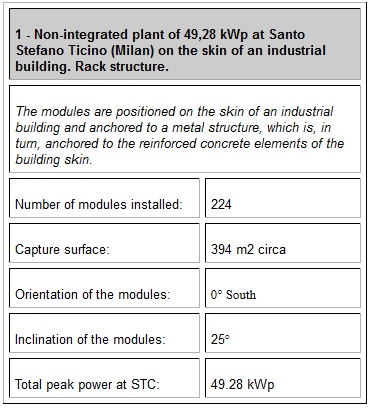
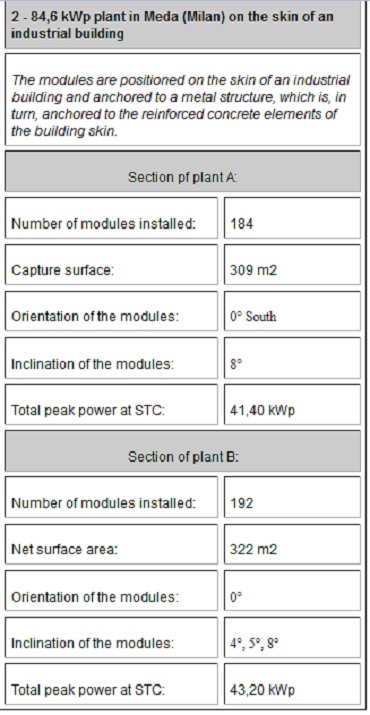
Moving the systems that supply energy to the building and which, in the case of devices for the conversion of solar energy, must be visible, to the outside, is frequently used by architects and by end users who have a static, unchangeable idea of construction but which, in any case, are now gaining new significance and functions, also thanks to the continuously changing norms in force.
In fact, the complete integration of photovoltaics, which can substitute part of the external building skin and not only overlap the traditional layers, is exploited thanks the Energy Account (Legal Decree dated 19 February 2007). This ideal solution is preferred to ground level installations or those with supports and anchorage structures, also from the economic point of view.
The optimization of photovoltaic integration in construction is related to numerous parameters, including environmental and construction factors, such as, for example, orientation, level of solar insulation, construction materials and methods, photovoltaic technology and production methods used for the modules, cost of electricity and promotional and financial strategies. These measure have enabled photovoltaic systems to enter the market, thus responding to increased awareness of the pro blems and environmental quality of buildings as per the European Directive (EPBD).
In any case, the success of a photovoltaic integration project, in the case of retrofit (energetic re-qualification of existing buildings) or of a new construction, is closely connected to an in-depth preliminary study regarding the convenience and constraints of its realization. The numerous solutions that can be used and that provide different opportunities must be considered.
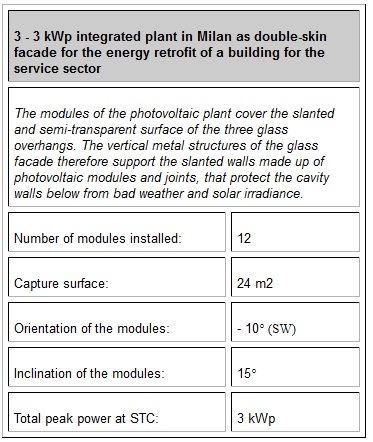
For a comprehensive assessment of the possibilities and constraints regarding the architectural integration of photovoltaic systems, we must consider the variables regarding the characteristics of the modules, which are the basic elements of the systems. These elements have technological and energetic performances with regards to climatic conditions and solar irradiation, the type of integration, the portion of skin involved in the change or substitution.
The basic assumption for the integration of photovoltaics in the construction sector is the availability of construction surfaces directly facing the sun during the day and during the year. These surfaces can be opaque or transparent, vertical, horizontal or inclined, with a series of particular conditions that the alternate or covering component of that part of the skin must face up to and satisfy, compatibly with the requirements.
The topics that must be dealt with in order to have a complete vision of the problem must take into simultaneous consideration the different areas of relevance and their interrelationships. Sometimes, in fact, the problem of integrating an innovative component with a specific function in construction, such as for example, photovoltaic modules, is carried out with simplification that can lead to a lack of consideration of the optimization of energy production and, at the same time, to underestimate the potential of technological elements.
This can lead to constructions in which the modules are applied not applied suing the best orientation, or photovoltaic elements that shade each other, or even the installation of flexible modules on areas with double radius, as well as the application of modules without considering the possibilities associated with the substitution of the bulding skin, with criticizable aesthetic results.
The specificity of photovoltaic components as part of construction therefore comes from the numerous possibilities that they offer and, at the same time, from the risks that their installation involves, in which the parameters of their correct application are only partially exploited.
In fact, the primary and fundamental rules and regulations that must be taken into consideration, can be summarized as follows:
- optimization of the energy produced by the system (positioning of the collecting components, study of installation methods, assessment of possible shading);
- highest possible level of integration, so that the component carries out technological and construction functions other than its main energetic function (thermal insulation, waterproofing, protection and filtering of light);
- attention to the aesthetic results of the installation with regards to the acceptability and visibility of a technology that, today, is still not completely part of the general ideas of buildings (using components suitable for the intervention and assessing the context in which they must operate);
- economic feasibility achievable substituting parts of the skin and evaluating the savings obtained from applications that exploit the solar potential to the utmost.
Further considerations must then be carried out with regards to the type of module used, since the modules present on the market have mechanical, thermal, and physical characteristics able to carry out diverse technological functions according to the comprised stratifications of material and their method of production.
Photovoltaic modules differ essentially as per the production technology used for cells, the layers of materials used for the physical configuration of components, the layout and density of the cells inside the module(s). Diverse applications depend on these characteristics in which the use of a specific module (with frame, without frame, opaque, semi-transparent, etc.) is advisable, and which provide specific technological performance and energy contribution, leading to the substitution of functional elements of the building skin.
Materials used to produce photovoltaics cells
The most frequently used material for the photovoltaic cells is silicon, even if other materials such as gallium arsenide (GaAs), cadmium telluride (CdTe), copper indium diselenide (CulnSe2), are also used, above all for the realization of thin films, which differ mainly because of their production and doping process. Moreover, plastic cells are now in the experimental phase, with rather limited yield at the moment, but if improved could become competitive from the cost point of view.
The modules on the market and used in construction at present are mainly those made of mono - crystalline and poly - crystalline silicon and amorphous cells.
From the construction point of view, the biggest difference can be seen between crystalline silicon and amorphous cells. As far as the first sector is concerned, cells made of monocrystalline silicon are made using a single crystal, while those in poly-crystalline silicon come from an ingot created by the solidification of the molten mass of silicon in a parallelepiped-shaped crucible.
The difference between the two types of cells, other than their aesthetic appearance, is also their different yield in terms of conversion of solar radiation and, therefore, of production of electricity. The former have an efficiency that can reach 20 per cent (about 15 per cent average), while the latter reach an efficiency of about one or two per cent less.
Cells in amorphous silicon, on the other hand, are produced by the deposition of silicon vapours onto a suitable substrate, in vacuum or controlled atmosphere. This technology enables to use much less material compared to crystalline silicon and to therefore produce cells that are called “thin film”. In fact, a layer of only a few micron is sufficient to obtain photovoltaic conversion. However, the stabilized average yield is, at about six to nine per cent, considerably less.
It must be noted that amorphous silicon undergoes deterioration in performance during the first months of exposure to sunlight (Staebler-Wronsky effect) followed by stabilization, but, nevertheless, causing an initial reduction in efficiency conversion that can reach 30-40 per cent. In operative phases, the panels reach high temperatures (even 40-45°C higher than environmental temperature), causing a negligible decrease in photoelectric conversion performance. In the long term, however, amorphous silicon modules can undergo a regeneration of efficiency, proven by experimental data.
A further observation regards the production of thin film cells. This process requires less energy compared to that of the production of crystalline silicon wafers , with consequent reductions in energy and economic costs of amorphous cells compared to crystalline cells, with a positive comparison at equal power, and is a consequence of the smaller amount of material needed.
In fact, the ratio between the amount of material needed for amorphous silicon cells compared to that needed for crystalline silicon cells is from 1 to 150-200 in favour of the first, also because the production processes of crystalline silicon wafers are affected by the problem of waste product, with consequent increased costs of finished products. Moreover, the production temperature of amorphous silicon is about 300°C, a lot less than the 900- 1,000°C needed for the production of crystalline silicon.
There are other materials and technologies at experimental level for the production of cells, which are still not used in the construction market as they are still not completely reliable or because their production is extremely expensive. Until now, silicon, used in thin crystal layers as in the case of mono-crystalline or poly-crystalline silicon, or deposited by means of particular procedures as in the case of amorphous silicon, has demonstrated stability, efficiency, reliability over time and production costs that have made it preferable compared to other material for photoelectric conversion.
In any case, components made from other materials with photoelectric characteristics are presently undergoing studies and experimentation that include production processes to produce thin films: vacuum deposition per layer and thermal treatments for CIS – copper indium selenite or with gallium (CIGS – resulting in laboratory yields of up to 18 per cent), screen printing and electro-deposition for cadmium telluride (CdTe), or also hetero-junction cells for copper sulphide (Cu2S) and cadmium (CdS).
As far as thin films are concern ed, polycrystalline layers of gallium arsenide (GaAs) and gallium arsenide and aluminium (GaAlAs), are, at present, not competitive for the construction sector due to their high costs. They are, however, highly reliable and have a good level of conversion (theoretical efficiency of single-junction cells of 30 per cent, such as mono- crystalline silicon, which can be improved using multi-junction cells).
Composition of Photovoltaic Sandwiches, Constraints and Opportunities
The stratification of the crystalline silicon photovoltaic modules available on the market include several layers of material creating a sandwich. The side in direct sunlight is made up of a pane of high-transparency tempered glass, which guarantees the highest passage of solar irradiance along with excellent mechanical resistance. This is followed by a sealing film (EVA), the photovoltaic cells with electrical contacts, another sealing film (EVA) and a back support that can also be in glass or in light polymeric material with good insulation qualities (such as, for example Tedlar®).
Both external layers are often made of polymeric material and the panel can (ifrequired) be inserted in a frame with extruded aluminium borders , which are the stiffening support sof the panel.
Amorphous silicon cells, on the other hand, are made up of material deposited on different substrates: rigid (glass, for example) or flexible (also thin transparent laminas) which do not need sealant.
The resulting cells can now be inserted in a sandwich to create crystalline silicon modules or laminated with rigid or flexible polymeric materials such as sheaths (for example Tefzel®, Sarnafi l®).
Regardless of the kind of cells, the type of assembly of the modules is particularly important since the materials used determine the building skin, resistance to atmospheric agents, thermal, acoustic and mechanical behaviour.
Possible stratifications can therefore be as follows:
- glass-glass modules (semitransparent);
- glass-Tedlar® modules (opaque);
- flexible sheathed modules (opaque or semitransparent).
Opaque or semitransparent panels can be obtained as per the substrate and positioning of the cells.
The transparency of photovoltaic modules can be obtained using transparent closure surfaces and by distancing the cells. Thanks to developments in production systems, some module manufacturers are able to offer architects the possibility of personally deciding the positioning of the cells, thus creating tailor made, versatile components, able to adapt to diverse planning and architectural needs.
Terms of Photovoltaic Integration
It is important to stress that the term “ integration” is often used incorrectly to indicate any kind of installation of photovoltaic components in building skin, while, generally, it would be more appropriate to speak about the ratio of photovoltaics with the building skin.
There are, in fact, diverse methods of interaction between the two systems of application of the component, with integration being just one of the possibilities.
The same difference can be found in the English acronyms PVIB (photovoltaics in buildings) and BIPV (building - integrated photovoltaics) used in technical literature, to indicate the different ratio existing between the photovoltaic generator and the building:
PVIB - photovoltaics in buildings: this refers to all the possible anchorages of photovoltaics to buildings, both in retrofit interventions on existing buildings or on the surfaces of new constructions. These interventions do not generally presuppose la compliance of the photovoltaic modules to the technological requirements of the traditional materials of building skins. The modules are fixed to the construction using diverse methods and mainly carry out energetic or ancillary item functions.
BIPV - building - integrated photovoltaics: this regards the real integration of photovoltaics into the building, more often new constructions, in which the photovoltaic elements have a secondary function as part of the same building, that is as components of the skin that must be able to carry out the same technological functions with results similar to those of normal construction materials.
Thermal Performance of the Skin
The use of photovoltaic modules as external building skins requires the evaluation of the actual performance of thermal insulation obtained by the installed component since, because of the construction sector’s energy savings goals, heat loss transmission containment must be respected.
The inclusion of energy generation devices in buildings must therefore guarantee physical and thermal characteristics to reduce energy needs, and be able to correctly combine technological plants for the use of renewable sources, (for example, heat pumps for winter- and summer air conditioning, photovoltaic systems for the production of electricity needed for the functioning of these devices).
Determining the thermal characteristics of photovoltaic modules depends on the stratification of the panel and on the conductivity of the materials used. The installation of photovoltaic modules as elements of an external wall does not cause particular problems, as the limited thermal resistance is, in any case, added to technological features that delegate insulation functions to other materials in the stratification of walls.
In cases where the thermal evaluation of photovoltaics must be assessed in detail, the ones to be used are those with semitransparent modules as external closure of the skin, created using metallic anchorage systems, which can be similar to window and door frames (even thermal bridge) in the case of fixing structures to curtain wall, used for façades, glass atria, etc.
In the case of solutions that comprise the ventilation of the modules and, therefore, the presence of a cavity wall for the realization of a cold, transparent façade, the thermal resistance of photovoltaic components is not significant, while, on the other hand, the transmission of the internal layer to satisfy the needs of thermal insulation must be considered.
In the case of double skins with external photovoltaic layer (generally semitransparent), advantages can be obtained during the winter, with a reduction in heat losses by creating a space between the inside and the outside.
With regards to the thermal resistance of photovoltaics as skin cladding, warm façades or similar, or those with a cavity wall of still air are only the ones considered important. As is already known, the glass parts of building skins are subject to the highest part of thermal losses and for this reason are not recommended for large transparent areas in countries with cold winters.
For the evaluation of the values of transmittance and compatibility of installation of modules substituting transparent enclosures, a table summarizing the values is defined by Legal Decree 192, dated 19 August 2005 “Fulfilment of Implementation of the 2002/91/CE Directive regarding the energetic yield in construction” and following updates (Legal Decree 311/06, DPR 59/09). This includes the definition of transmission value limits for building skins in relation to the climatic area of the site, deriving from daily degrees of heating.
The established values range from 5.5-5.0 W/ m2K to 2.4-2.2 W/ m2K; these report, as examples, the information regarding three areas rep resenting the different climatic conditions of Italy.
Thermal insulation performance deriving from the use of photovoltaics is comparable to that of a single glass pane of 6 millimetres (U = 5.7 W/m2K). The values of conductivity of the materials of the sandwich are:
- glass λ: = 1,16 W/mK
- Tedlar λ: = 0,18 W/mK
The stratification comprises thicknesses of 3-4 millimetres for each layer with results of 5.7-6 W/ m2K of thermal transmittance for glass-glass (4 millimetres + 4 millimetres) or glass- Tedlar. This result is also lower than the minimum limit comprised by the norm at ive per zone with daily degrees lower than 600 (U = 5.5 – 5 W/ m2K).
It is therefore evident that double-glazing stratifications with an external barrier of photovoltaics are necessary. In this way, transmission values the same as those of traditional double glazing – about 2.5-2.7 W/m2K can be ensured.
In order to obtain values established by the norms for northern Italy, it is necessary to insert low-E coating in the cavity wall (vacuum or pyrolitic deposition).
These types of treatment, applied to internal glass panes, can reduce the exchange between the surface of the laminated photovoltaics and that of the glass, reaching overall transmittance values of 1.5-1.7 W/m2K for cavity wall with air and 1.4-1.1 W/m2K with the addition of noble gases such as argon or kripton.
The technological transparent group of elements with photovoltaics have the advantage, in winter, of stemming the “cold wall” effect thanks to thermal resistance and to heat loss during the photoelectric conversion phase. In the summer, in any case, the fact that the photovoltaic part cannot be opened and is subject to strong sunlight can cause considerable discomfort , due to the increase in solar radiance temperature, other than penalizing the production of electricity.
Alternatively to the introduction of photovoltaic double-glazing, semitransparent stratifications with ventilated cavity walls to remove the heat from the back of the module and to mitigate the overheating effect in the summer, releasing the hot air, are also a possibility.
The flow of air in the cavity wall can also be used during the winter to preheat the air for air conditioning, with a consequent decrease in the energy needs of the building (hybrid photovoltaics). In fact , it is not economically convenient to use technologies from renewable sources if, at the same time, they create a burden by means of energy needs for internal environment air conditioning.
Arch. Lavinia Chiara Tagliabue, Department of Science and Technology of the Construction Environment (BEST), POLITECNICO DI MILANO