This paper was first presented at GPD 2017 by Mr. Reinhold Senf from Grafotec Spray Systems GmbH.
The comparison of existing application systems e.g. roller applicators, nozzle applicators as well as dry or liquid spray nozzle systems which are used worldwide to apply the interleaving material required to bend a wind shield will be introduced and advantages as well as disadvantages are discussed. Attending this session will enable you to take a decision for the “right” application system fitting your production line.
Introduction of interleaving material used for windshield bending
Before understanding the application equipment, it seems to be of advantage to know something about the interleaving material.
The most common interleaving material is “Kieselguhr” or “Diatomaceous Earth - DE” or “Diahydro” or “Celite”. These materials are all naturally occurring, soft, chalk-like sedimentary rock that is easily crumbled into a fine, white powder. It has an abrasive feel, is very light due to its high porosity. It is very well heat resistant. The typical chemical composition is about 85% silica, about 5% sodium, about 3% magnesium and about 2% iron.
It is clearly stated, that the interleaving material used for windshield bending is a material nobody wants to work with. Because of the small particle size (< 20µ) it has very poor flow characteristics – therefore it is difficult to handle with the common application equipment. If used in a dry application system, the flow characteristic is a problem, if used in a wet or liquid application system sedimentation is a problem.
Introduction of existing application systems
The interleaving application machine market knows two ways to apply the interleaving material:
Dry:
with a dry applicator working with a “roller”
with a dry applicator working with “air-nozzles”
Wet:
with a liquid applicator working with “air and liquid through spray-nozzles”
with a liquid applicator working with “liquid through spray-nozzles”
with a liquid applicator working with a “liquid through spray-roller”
Dry application machines
Dry application – through “roller” application
The dry application method has the most experience and has established a large community working with such devices. When geometries become more difficult, the technical ability to distribute the interleaving material as the geometry needs is reaching the limit quickly. Then the wet application systems came into the game and established themselves as the more precise and modern way to apply the interleaving. Both methods do have advantages and disadvantages, which I want to introduce to the auditorium.
The standard technology is the “DRY ROLLER APPLICATOR” - where an engraved roller is turning in the interleaving material itself. The material was hold back from either 2 doctor blades on the side of the roller (Figure 1) or 1 doctor blade from the top of the roller and a brush from the bottom side (Figure 2). Both technologies depend on gravity, both systems are equipped with some kind of electrostatic devices trying to increase the particle adhesion to the windshield. Both systems essentially need an enclosure to ensure that air draft cannot blow away the interleaving material.
Dry application – through “air-nozzle” application
Transferred from the printing machinery manufacturing, air-nozzle systems (Figure 3) are much more flexible than “roller” systems.
The air is used as transporter and transfers the interleaving material from the reservoir through plastic air hoses and different kind of nozzles (Figure 4) onto the glass. Due to their fast reaction time, the interleaving spill – beside the glass – is minimized.
An enclosure might not be necessary without having the environment too much polluted. Because of local conditions many of the users install an enclosure to protect the spray from the wind draft, so that the distribution quality of the interleaving material appears quite good.
Liquid application machines
Liquid application – two component nozzles - air and liquid through “spray-nozzle” application
Like the air-nozzle systems the wet application with two component nozzles (Figure 5) uses air as a transporter. The liquid – or better suspension – is getting mixed with the air either inside the nozzle or right before the nozzle. Under pressure and due to the geometry of the nozzle a spray curtain containing fine aerosols appears. Normally 2 of these nozzles are used for standard windshields. Surrounded from an enclosure, the spray falls onto the glass.
Due to the number of aerosols, the control of the spray curtain is very difficult so that all these systems need an enclosure.
Liquid application – liquid through “spraynozzle” application
Same principle as the two-component nozzle system, just working with only one media under pressure (Figure 6).
The suspension is pressurized and the nozzle produces the fine mist, which falls down onto the windshield.
The standard design for such machinery is containing 2 spray nozzles covered from an enclosure.
The production of aerosols is almost identical to the two-component nozzle.
Liquid application – liquid through “roller” application
This system (Figure 7) is not using nozzles nor working with a separate media as a transporter. The spray curtain is produced due to a roller turning at high speed and its very specific surface (Figure 7-A).
The geometry of the surface takes the suspension and throws it out of the housing. A shutter opens a gap through which the suspension is released.
After introducing the individual systems we can discuss about advantages, disadvantages and problems of the systems.
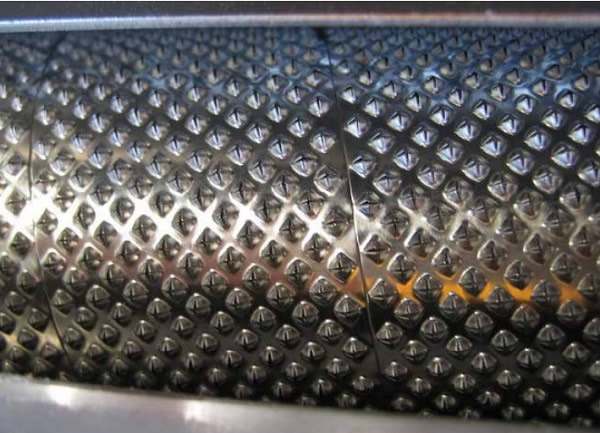
Advantages
Dry application machines
ROLLER application system
Price-wise very attractive
Robust systems with rare breakdown
Air nozzle system (dry interleaving air operated application)
Price-wise attractive
Robust systems
Liquid application machines
Two component nozzle system
Price-wise very attractive
Very fine distribution of interleaving
Spray nozzle (pure liquid) system
Price-wise very attractive
Fine distribution of interleaving
Roller spray system
Fine distribution of interleaving
Enclosure not essentially needed
No deposit of interleaving material in the area (even in an enclosure) – relatively clean conveyor
Absolutely no spitting effect – even after long operation time
Highly resistant against wear-off effects
Nozzle-free system
No change in application quality
Little need of maintenance
Disadvantages
Dry application machines
ROLLER application system
Accumulation of interleaving material on the underside of the applicator → “fall-off” and lumps
Interleaving distribution quality decreasing over operation time
Vagrant interleaving material all over
→ needs an enclosure and/or dust extraction
Need for maintenance (cleaning) is very high
Air nozzle system (dry interleaving air operated application)
Accumulation of interleaving material on the underside of the applicator → “fall-off” and lumps
“Spitting” effect occasionally seen
Vagrant interleaving material all over → needs an enclosure and/or dust extraction
Need for maintenance (cleaning) is high
Liquid application machines
Two component nozzle system
Enclosure is essential – otherwise contamination of environment and conveyor
Accumulation of interleaving material on the inside of the enclosure → “falloff” and lumps
“Spitting” effect after some time
Wear-off of the nozzle mouth results in bad distribution and uneven deposit of interleaving
Need of maintenance becomes more critical the longer in operation
Spray nozzle (pure liquid) system
Enclosure is essential – otherwise contamination of environment and conveyor
Accumulation of interleaving material on the inside of the enclosure → “falloff” and lumps
“Spitting” effect after some time
Wear-off of the nozzle mouth results in bad distribution and uneven deposit of interleaving
Need of maintenance becomes more critical the longer in operation
Roller spray system
Price-wise unattractive
Little maintenance
Problems
Dry application machines
ROLLER application system
Operators report that they need two applicator systems to operate continuously. Whilst one unit is in production, the second one is under maintenance.
Due to the roller design and the high voltage distribution, lumps are uncontrolled falling off the underside very frequently. This increases the rejection rate.
The high voltage feature needs more replacing as the operators like.
The control of the powder amount is not so good as it is mostly done through a potentiometer. A digital setting method would help to control the powder amount much better.
Interleaving adhesion to the glass is not so good, meaning that some of the interleaving is lost during handling – depending on the process.
Pairing right after the interleaving application seems to be the best process step, but the risk of plate movement during transportation is quite high.
Over-spray contaminates the application area – especially below the glass.
Air nozzle system (dry interleaving air operated application)
Operators report that the accumulation of interleaving on the underside and around the nozzles is causing problems, because the interleaving falls off uncontrolled and leaves lumps on the glass.
Occasionally operators report that “stripes” can be seen in the distribution of the interleaving, without quality effects in bending.
“Stripes” are commonly indicating worn-off nozzles. After replacing the “stripes” are gone.
The risk of plate movement is also present.
Over spray contaminates the application area – especially below the glass.
Liquid application machines
Two component nozzle system
The major problem with all nozzle systems is “spitting” and the “area contamination”. Depending on the quality of the spray nozzle the “spitting” effect occurs earlier or later, but no nozzle design can overcome this problem.
Most of the operators of nozzle systems have an enclosure for the spray system. The biggest problem with it is maintenance. What happens is that the spray curtain also reaches the walls of the enclosure on the inside. The interleaving accumulates and falls-off after some time. Only frequent maintenance (cleaning) helps out of this problem.
Another reported problem is sedimentation. All the liquid application machines face the problem to keep the suspension agitated.
Over-spray contaminates the application area – especially below the glass.
Spray nozzle (pure liquid) system
Again, “spitting” and “area contamination” is the most common problem reported.
Most of the operators of nozzle systems have an enclosure for the spray system. The biggest problem with it is maintenance. What happens is that the spray curtain also reaches the walls of the enclosure on the inside. The interleaving accumulates and falls-off after some time. Only frequent maintenance (cleaning) helps out of this problem.
Over spray contaminates the application area – especially below the glass.
Roller spray system
Some operators claim that the application area is dirty because of the “overspill” - same as with the dry application systems.
Other operators claim, that the applicator unit becomes dirty after some time – cleaning is necessary.
Report from a windshield manufacturer
Our customer requested a complicated (small bending radii, deep sag bending) windshield from us. With our standard dry roller application system, we found a rejection rate of 47% due to bending faults. We immediately established a liquid spray nozzle system where we could drop the rejection rate to below 30%. Modifications to the systems allowed us to retrieve a rejection rate of 27% as our best result. Then we tried the liquid roller spray system and found a rejection rate of 8% due to bending faults. This was now satisfactory to us. Turkish car glass manufacturer.
Conclusion
There are 3 points we have to focus if we want to establish a rank list:
• Application quality
• Cost for housekeeping
• All over investment cost
Concerning application quality, I only can advise the liquid roller spray system as it supplies constant quality conditions in matters of even interleaving distribution and amount control, followed by the liquid nozzle spray systems which are weak in constant quality performance and finally the dry nozzle spray system followed by the dry roller spray system.
Housekeeping cost is completely neglected from purchasers as this is a different account, but together with the machine investment it is the true system cost to be paid for.
The lowest housekeeping expenses is to find with the liquid roller spray system, followed from the liquid spray nozzle systems, the dry spray nozzle system and the dry roller application system.
The liquid roller spray application system offers the best performance in regards of application quality, housekeeping and lifecycle-cost, followed by the liquid spray nozzle systems, the dry spray nozzle system and the dry roller application system.