First presented at GPD 2019
Actual limitations of bent glass products are shapes with sharp curves, meaning bending radii smaller than 50 mm are not available. Within this work, we present an innovative and advanced bending process for manufacturing sharp curved glass. Using this technology designers and architects are able to create expressive shaped glass shells for products and buildings. We use a special glass bending facility to apply local heat to the glass.
Numerical simulations with an advanced material model and a detailed description of the thermal conductance and temperature distribution are performed during the development phase. Real samples were formed to demonstrate the potential for the use in modern façades and automotive applications.
1 Introduction
Glass is a fascinating material which plays an important role in architecture. Due to its characteristics, being transparent or translucent it controls the incidence of light into the building. Besides it is also reflective, may be colored, has gloss, so it lends buildings to an extraordinary aesthetics from the outside.
There is still potential to increase the combination of design and functionality through individual and special glass designs. Architects and builder-owners go in for high optical quality demanding glass with low waviness and without defects like imprints. Ideally the glass products are manufactured ready for installation, have precise geometrical fittings, are free from interruptions and provide high and constant level of thermal insulation to make sure that the heat transition along the window front has little variations.
Glazing around the building’s corner up to now uses glued or post and beam constructions. These solutions have nontransparent areas caused by non-glass elements such as spacers or beams at the corners, see figure 1. Apart from the visual impression with interrupted transparency, controlling of the heat flux in the corner areas is technically challenging. High gradients of thermal conductivity hold the risk of condensation, which can cause mould formation, especially problematical at glued lines. A full glass corner could be an elegant way to avoid these problems.
At the bottom: View through the above glazing, modeled in CAD. Configuration a. and b. represent common glued corner insulation glazing taken from [1]; configuration c. represents the insulation glazing demonstrator from Fraunhofer IWM.
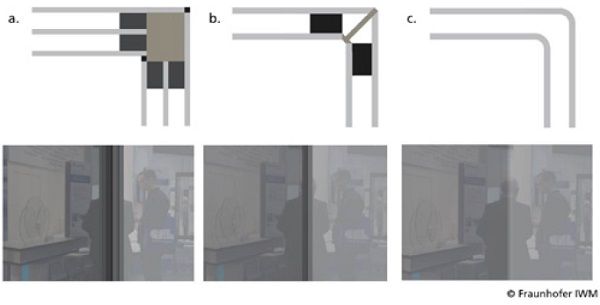
2 Bending process
At Fraunhofer IWM, glass bending processes have been developed for forming sheet glass especially with application of local heating. These processes have several advantages compared to conventional bending processes. Non-isothermal processing of the glass with “hot” and “cold” areas within the glass sheet enables handling, fixation and supporting of the glass body at the “cold spots” far away from the “hot spots” of the softened glass material which is to be bent and remodeled.
As a result the quality of the bent and the flat areas are at a very high level. Shapes with flat areas retain the very high surface quality of the origin float glass concerning flatness and waviness as the flat areas will not be deformed at all during the glass bending process. Besides, applying precise, concentrated and well-defined local heating enables pronounced shapes with very small bending radii, whereby shapes can be realized that have never been formed in glass before – some examples are shown in Fig. 3 and Fig. 5.
Glass sheets up to 1m x 1m can be processed inside the research glass bending machine at the Fraunhofer IWM in Freiburg. Local heat is applied by a high power laser in combination with a laser scanner enabling any path to be scribed on the glass. During the process local heating is controlled by laser energy and laser path kinetics imposed by the laser scanner program. This yields to an enormous flexibility concerning process guiding.
For example, bending a glass sheet to a 90 degree corner, the width of the heated zone and the intensity along the heat zone can be adjusted to customized requirements, figure 2. By these parameters, laser power and laser duration, the bending radius and the bending angle can be controlled precisely.
![Fig. 2: Left: Scheme of a bending set-up to perform a 90° shape with different bending radii according to the width of the heat zones b1 and b2, from [2]; right: simulation of bending process, colored is the temperature field.](/sites/default/files/inline-images/Fig2_15.jpg)
The laboratory bending machine is additionally equipped with an infrared-camera, allowing the researchers to have a look onto the glass sheet inside the furnace and to measure and register transient local temperature distribution. These data are used to improve the bending process.
However, to optimize such bending processes is a multi-parameter challenge. Stateof-the art procedure to cope with these challenges is to rely on the experience of glass specialists. At Fraunhofer IWM we also make use of numerical simulations based on finite elements method to simulate glass material behavior throughout the heating cycle and the bending process [2], figure 2. In current projects we are working on advanced automated and intelligent workflows to support the optimization by using simulation methods and machine learning tools and algorithms.
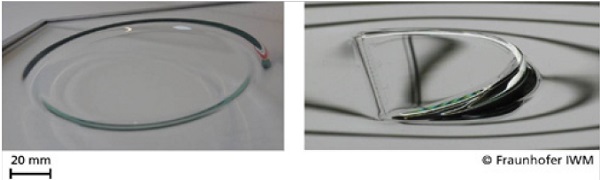
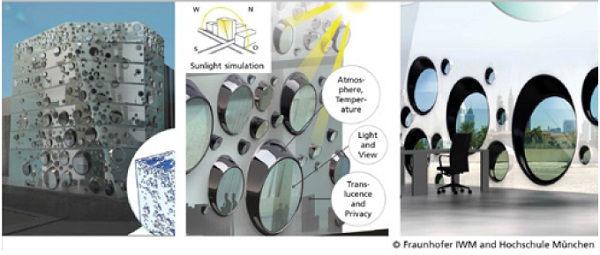
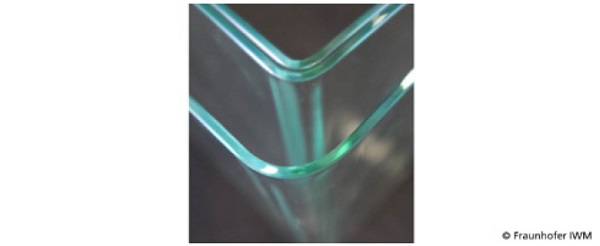
3 Expressive shaped glass products, examples and demonstrators
Several different shapes have been formed by using this method. The examples shown below, demonstrate the feasibility to form geometric outstanding shapes, figure 3, and also show possibilities to apply the formed glass to products or complete systems made of bent glass.
Shapes like the round plate and the semicircle in figure 3 have inspired design students to create a building façade with functional “bubbles”, figure 4. The virtual building created by the design students of the Hochschule München has a vertical flat and translucent façade which lets sun light pass dazzle-free but prevents people standing outside of the building to look inside it.
People from inside of the building can look through the translucent glass. The “bubbles” have two functional areas: the flat transparent areas allow people from the inside of the building to have a clear look to the outside, and allows indirect light from the environment to come in. The curved areas are nontransparent and prevent direct sun light to shine into the building. This ensures a pleasant atmosphere and helps to regulate the temperature inside.
The second example uses sharp bent glasses as basic elements. Using the above described technology glasses can be sharply bent to defined radii. Figure 5 shows three glasses of thickness 3 mm, each bent to 90° angle but with different radii, i.e. 5, 10 and 20 mm radius respectively.