Challenging Glass 6
Conference on Architectural and Structural Applications of Glass
Louter, Bos, Belis, Veer, Nijsse (Eds.), Delft University of Technology, May 2018.
Copyright © with the authors. All rights reserved.
ISBN 978-94-6366-044-0, https://doi.org/10.7480/cgc.6.2181
Authors:
Maurizio Froli, Francesco Laccone | Department of Energy, Systems, Territory and Construction Engineering, University of Pisa, Italy
Future smart cities are demanding for new infrastructures and networks. Novel multifunctional objects should be able to acquire, store and transmit information, generate their own energy need, light up the surroundings and more. Thanks to their transparency, glass structures are ideal support for hi-tech components because of the inherent opportunity offered by laminated glass to embed PV cells, sensors, OLEDs and lighting devices. The project HYbrid GLAss-Steel Stele (HYGLASS) aims at the realization of a cantilevering hybrid vertical structure working as a stand-alone or a grid-connected smart tower. The facetted geometry of the construction originates from the tetrahelix solid, and its structural conception is based on segmentation and post-tensioning, which are the same basic principles of the Travi Vitree Tensegrity (TVT).
The spatial complexity and the height of the tower (about 7.00 meters) requires a high ULS safety level that is obtained by designing the structure to withstand the worst-case scenario of all panels cracked. To this purpose and to facilitate the assembly operations, a filigree metal skeleton is placed at the edges of the base polyhedron. Equal triangular glass panels are corner clamped into special nodes at the vertices of the solid. Modularity and dry connections facilitate an easy replacement of the damaged components. FE nonlinear analyses highlight the safe design and efficiency of the system. Such structural concept is the key to extent the hybrid glass-steel construction to the domain of self-supporting high-rise and long-spanned structures or building skins.
1.Introduction
The project HYbrid GLAss-Steel Stele (HYGLASS) is an ongoing research established at the University of Pisa, conceived and lead by M. Froli. Its aim is to materialize into a non-mimetic tower-like object multiple services that the smart cities are currently requiring to acquire and share information. Additionally, such objects can be used as integrative urban signage or lighting system. Self-sufficiency is also a requirement. Glass is optimal material for this use because of its durability and its modern appealing. Moreover, thanks to the possibility offered by lamination and gluing, a glass panel can easily embed miniaturized hi-tech components, such as PV cells, sensors, OLEDs and lighting devices. The structural use of the glass maximizes the transparency in load bearing components, and the limitations are essentially related to its fragility and scattered tension strength. Figs. 1 and 2 shows impressions of how the HYGLASS tower may look like.
In the development of long spanned structures, hybridism is a commonly-used strategy to bridge over glass structural lacks and confer it a fail-safe behavior (Haldimann et al. 2008, Martens et al. 2015a). Static concepts based on the collaboration of glass with steel were developed for beams (Louter et al. 2012, Martens et al. 2016a, 2016b), arches (Sobek 2007, Weller et al. 2009), domes and vaults (Weller et al. 2008, 2010, Ioannis et al. 2012).
In analogy to post-tensioned reinforced concrete, a beneficial pre-stress on glass has been more recently experienced in glass structures to exploit the material high compressive resistance. As a consequence, robustness is increased, and crack appearance is delayed (Louter et al. 2014, Cupać et al. 2017, Bedon and Louter 2016, 2017, Jordão et al. 2014, Feng et al. 2015, Engelmann and Weller 2016).
Research at the University of Pisa showed the advantages related to the supplementary adoption of segmentation in addition to hybridism and post-tensioning. The Travi Vitree Tensegrity (TVT, Froli and Lani 2010, Froli and Mamone 2014) were indeed based on those principles.
During the experimental activities, the TVT beams exhibited ductile collapse: the yielding of the lower bars preceded the buckling failure of glass panels, which, due to prestressing resulted mostly compressed. Segmentation of glass into a regular arrangement of panels avoided the propagation of cracks into the entire system, and only a partial replacement, in case of a local damage, gave back a serviceable structure. Redundancy is obtained by a multilevel duplication of the components (double laminated panes, double beam webs etc.).
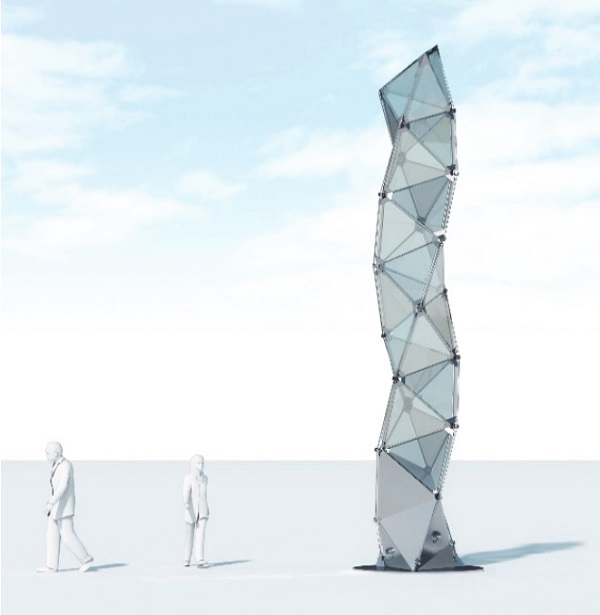
The HYGLASS tower has been designed according to a specific structural concept (Froli and Laccone 2018), which origins from the TVT concept and preserves its main characteristics. But, being a lattice structure, an enhanced redundancy is required. This has been obtained by combining a filigree steel truss with the transparent panels and post-tensioning the latter by external cables. In this way two distinct steel components play the role of reinforcement and post-tensioning devices.
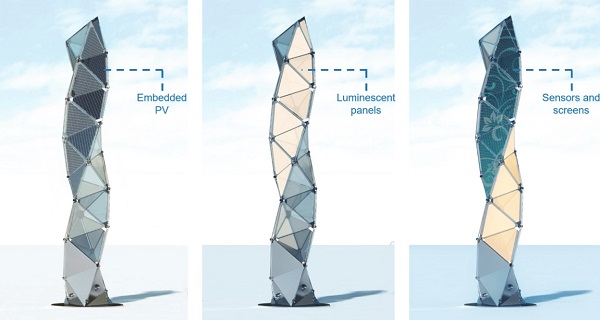
2.Structural and geometrical principles
The shape of the HYGLASS tower has been selected among the triangulated helical polyhedrons as the solid named tetrahelix (Buckminster Fuller 1982). Its outer surface is made of a helical arrangement of three stripes of triangular panels. The main components of the system are: triangular laminated glass panels allocated to overlap the faces of the tetrahelix, tubular slender steel beams at the edges of the solid, and six-way steel connections, which constitute the most complex part of the structure, supporting the corners of the glass panels and fastening the extremities of the beams.
The panels are made of an inner laminated glass structural panel with rounded edges, and an outer sacrificial layer with no structural function, but only with the geometrical purpose to link the edges of glass guaranteeing a continuous reflectivity of the surface and hiding the direct view of the opaque truss. As happened in TVT beams the rounded corners of the glass panels are clamped between nodal plates and a removable cap with interposed aluminum and PVC spacer material. A kind of shoe-shaped device is created. The difference with the older system consists in a larger adjustability degree that is necessary due to spatial complexity of the tower. The larger adjustability is obtained by means of through-hole bolts, which fit the residual space at the merging line of two contiguous nodal plates.
The base structural concept discussed in Froli and Laccone (2018) is in the following briefly recalled.
- Any ideal continuous curved shape surface can be segmented, generating multiple triangular or in general polygonal flat glass panels. Such expedient constitutes a fail-safe and a low-maintenance, cost saving strategy since only broken panels need to be replaced once failed.
- Mutual pre-stress of the components is applied by means of external cables. This is done to globally stiffen the system and to additionally apply a beneficial compression pre-stress. A design opportunity is to orient the cables path to benefit from the loading condition.
- The dry assembly of the connection allows an easy mounting and replacement of the components. Since only contact ensures the transfer of forces, the panel can slide within the connection in case of tensile stresses higher than the pre-compression values.
- In such a way, the panel is mostly compressed except for tension stresses that may arise for significant second order effects or out-of-plane loadings. Such connective device is akin to the TVT node.
- The steel beams that constitute a metal skeleton frame are allocated in adjacency of the panels edges and symbiotically collaborate with glass in supporting loads. The frame additionally constitutes a suitable redundancy barrier before ULS collapse. Hence, it is designed to withstand at least the own weight in the absolute worst-case scenario where all glass panels are accidentally cracked, and then mechanically useless. Lastly the metal skeleton aims at facilitating the assembly and replacing operations, avoiding the use of provisional scaffolding.
3.Numerical modeling
The analysis of the 7.00 meters tall HYGLASS has been developed in the Straus7 release 2.3.3 (G+D Computing 2005) computational environment. A global modelling of the structure aimed at assessing its fail-safe reserves, particularly at evaluating the redundancy degree. Main materials used in the model are common Heat-Strengthened Glass (HSG) and S275 steel. Aluminum spacers like those employed in the TVTγ beam prototype have been designed, but, because of the simplification adopted in the model, the latter have not been introduced and only special links simulated the nonlinear contact between steel and glass.
Mono-dimensional FE beam elements have been adopted for the steel truss. Ground nodes have been simply pinned. Double laminated 8+1.52+8 HSG glass panels with PVB interlayer and 1000 mm side have been modelled as FE triangular plate elements with sharp vertices. Indeed, the evaluation of glass stress peaks, which may occur because of the force transfer mechanism at the corner area, is not considered in this work. Due to the absence of real scale experimental data, the modelling phase was based on past experimental and numerical activities of TVTs (Froli et al. 2014 and 2017). As cross area of the steel beams, hollow steel 4 mm thick steel tubes with 33,6 mm diameter have been selected. The post-tensioning value practiced on the strands is 10 kN, and no loss of prestressing is considered.
Loads acting on the tower are: own-weight, automatically introduced from the material characteristics; non-structural load, derived from the 6 mm sacrificial outer panel and hi-tech equipment; static-equivalent wind load, applied as a face pressure on the plate elements. Analyses involve geometrical, material and contact nonlinearities. To be on the safe side, the bracing steel plates of the basement have not been included in the FE model.
4.Results and discussion
4.1.ULS behavior
Based on the analyses result, the stress paths on the panels highlight a prevailing compression regime. Despite the non-accurate modeling of the panel corner, the maximum principal stress reaches at maximum a value minor than 9 MPa at the edge side for the ULS load combination with prevailing 3 sec peak-wind loading. This means that in this case the panel could not be subject to crisis. However, this data needs further investigation. The main loading flux is located nearby the most inclined helices of the tetrahelix, where the tower is also endowed with the external post-tensioning path (fig. 3).
Concerning the truss, at ULS the lower beams are the most stressed component. Hence, the safety factor is evaluated to be 3.2, which is an acceptable value for such hybrid and tall glass structure.
4.2.Static and dynamic stiffness
Natural frequency analyses (NFA) eigenfrequencies and SLS characteristic deflection constitute a measure of the dynamic and the static stiffness of the system respectively.
The pre-stress loading on the strands has been selected to reach the SLS of de-compression on the panels for wind loading prevailing combinations and contemporarily to obtain a good dynamic stiffness. The value of 10 kN represents an optimal value considering both requirements. The parametric design strategy based on the NFA gives the results summarized in tab. 1 and represented fig. 4. Only the first (representative) eigenfrequency is showed.
The SLS deflection obtained at the tip of the structure yields the value of 11.35 mm, which constitute a drift of 1.49·10-3, well within the limits of 1/300 usually given in the codes for stand-alone structures.

Table 1: Parametric dynamic stiffness of the structure, bold values are current design values.
4.3.Redundancy
To design the redundancy, another global FE model has been created, neglecting the in-plane stiffness of glass panels; or rather the glass Young’s modulus has been set to 0 MPa, and the out-of-plane loading is distributed by means of load patches at the corners. Such setting wants to simulate the worst-case scenario where all glass panes are cracked due to a improbable accidental event. The safety factor for the steel components is 2.27.
A representative measure of the redundancy degree can be assumed as the ratio between the two global safety factors, namely at ULS (hybrid solution, with all ‘mechanically-active’ panels) and at the worst-case scenario for the same load combination. That value is 1.41, which means the hybrid solution has the 41% of mechanical reserves.
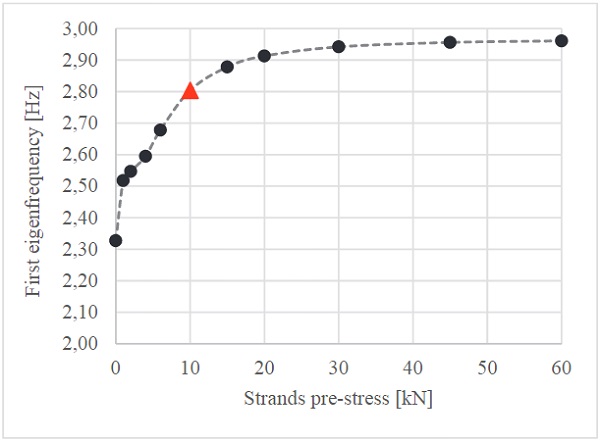
5.Conclusions
A cantilevering tower structure has been conceived in the framework of a research project HYGLASS, which brings in the smart city context a new infrastructure capable to manage data, to interact with residents and visitors and to play public functions.
A novel structural concept, derived from the TVT concept, has been applied to design a geometrically-complex and challenging object. The concept is based on segmentation, hybridism and post-tensioning, and its main aims are to achieve redundancy and to guarantee easy erection in the construction phase and cost-saving during the nominal life. The structural safety level with respect to the global failure scenario is a design choice and can be set on desired value. Hierarchy is also obtainable by a careful graduation of glass and steel cross-area and the design of the connections. Based on this first application here discussed, the static concept demonstrates potentiality to a further extension to long spanned and free-form compressed structures.
Acknowledgements
The authors would like to express gratitude to the researches that joined and are contributing in the multifunctional development of the HYGLASS project: Profs. Massimo Ceraolo, Franceso Leccese, Roberto Saletti from the University of Pisa. Ing. Luca Guidi is acknowledged for the collaboration in the numerical modelling.
References
Bedon, C., Louter, C.: Finite-element analysis of post-tensioned SG-laminated glass beams with mechanically anchored tendons. Glass Struct. Eng. 1, 39–59 (2016).
Bedon C., Louter C.: Finite Element analysis of post-tensioned SG-laminated glass beams with adhesively bonded steel tendons, Composite Structures. 167, 238-250 (2017).
Buckminster Fuller R.: Synergetics: explorations in the geometry of thinking. Estate of R. Buckminster Fuller, New York (1982)
Cupać J., Martens K., Nussbaumer A., Belis J., Louter C.: Experimental investigation of multi-span post-tensioned glass beams, Glass Structures and Engineering. 2(1) (2017)
Engelmann M, Weller B, Post-Tensioned Glass Beams for a 9 m Spannglass Bridge, Structural Engineering International. 26.2, 103-113 (2016).
Feng R.Q., Jihong Y., Yao Y.A.: New Type of Structure: Glass Cable Truss, Journal of Bridge Engineering. 20(12) 04015024 (2015).
Froli, M. and Lani, L.: Glass Tensegrity Trusses. Structural Engineering International, N°4, 436-441 (2010)
Froli, M. and Mamone, V.: A 12 meter long segmented, post-tensioned steel-glass beam (TVT Gamma). Challenging Glass 4 & COST Action TU0905 Final Conference. London: Louter, Bos & Belis (Eds.) Taylor & Francis Group, 243-251 (2014).
Froli, M., Masiello, G., Melis, A., Mamone, V., and Giammattei, M.: The Energy Gallery: a pilot project in Pisa. Engineered Transparency. International Conference at Glasstec, Düsseldorf, 621–628 (2014).
Froli, M., Laccone, F., and Maesano, D.: The TVT glass pavilion: theoretical study on a highly transparent building made with long-spanned TVT portals braced with hybrid glass-steel panels. Buildings, MDPI, 7(2), 50 (2017)
Froli M., Laccone F.: Static concept for long span and high-rise glass structures. Journal of Architectural Engineering, ASCE, 24(1): 04017030 (2018)
G+D Computing: Straus7 User’s Manual. G+D Computing, Sydney (2005)
Haldimann, M., Luible, A., and Overend, M.: Structural use of glass (Vol. 10). Iabse, Zurich (2008)
Ioannis S.M., Simon D., Nhamoinesu S., Overend M.: Investigation of double-layer tensegrity glazing systems, IASS Annual Symposium - IASS-APCS 2012 Seoul, South Korea. (2012).
Jordão S., Pinho M., Martin J.P., Santiago A., Neves L.C.: Behaviour of laminated glass beams reinforced with pre-stressed cables, Steel Construction. 7, 204-207 (2014).
Louter C., Belis J., Veer F., Lebet J.P.: Structural response of SG-laminated reinforced glass beams; experimental investigations on the effects of glass type, reinforcement percentage and beam size, Engineering Structures. 36, 292-301 (2012).
Louter C., Cupać J., Lebet J.P.: Exploratory experimental investigations on post-tensioned structural glass beams, Journal of Facade Design andEngineering. 2(1-2), 3-18 (2014).
Martens, K., Caspeele, R., and Belis, J.: Development of composite glass beams – a review. Engineering Structures, 101, 1-15 (2015)
Martens, K., Caspeele, R., and Belis, J.: Development of reinforced and posttensioned glass beams: review of experimental research. Journal of Structural Engineering, 142(5), 04015173 (2015)
Martens K., Caspeele R., Belis J.: Load-carrying behaviour of interrupted statically indeterminate reinforced laminated glass beams, Glass Structures and Engineering. 1(1), 81-94 (2016).
Martens K., Caspeele R., Belis J.: Numerical investigation of two-sided reinforced laminated glass beams in statically indeterminate systems, Glass Structures and Engineering. 1(2), 417-431 (2016).
Sobek W.: Strutture in vetro, Archi: rivista svizzera di architettura, ingegneria e urbanistica, Swiss review of architecture, engineering and urban planning. 24-31 (2007).
Weller B., Reich S., Ebert J., Krampe P.: Testing for individual approval of a vault roof with in-plane loaded glass panes, Proceedings of the International Association for Shell and Spatial Structures (IASS) Symposium 2009, Valencia. 2990-3001 (2009).
Weller B., Reich S., Ebert J.: Testing on Space Grid Structures with Glass as Compression Layer, In Proceedings of the Challenging Glass Conference, Delft. 155-162 (2008).
Weller B., Reich S., Ebert J.: Transparentes Raumstabwerk über dem Innenhof des Berliner Reichstagspräsidentenpalais, Stahlbau. 79(S1) 3-9 (2010).