This paper was first presented at GPD 2023.
Link to the full GPD 2023 conference book: https://www.gpd.fi/GPD2023_proceedings_book/
Authors:
Graeme DeBrincat, Graham Dodd, Florence Wu (Arup) Francis Ellington (FACE Architectural)
Introduction
Flat glass manufacturers are rightly focused on reducing their operational carbon and in turn the embodied carbon of the glass materials that they create. That focus prioritises new furnace technology, incorporating fuel switching, waste heat recovery and carbon capture which will have a significant reducing effect on the carbon intensity of glass but will only be realised over an extended period. It is now accepted that increasing the use of recycled content of new glass by utilising high quality, sorted glass cullet plays a crucial role in reducing the energy demand, process emissions and therefore the carbon footprint of new glass products.
Glass for Europe have estimated that by the collection of all glass materials from existing buildings, returning it to the furnaces for remelt could reduce the carbon intensity of glass manufacture by 7%. Sources of glass cullet are either from postindustrial, pre-consumer material, primarily offcuts returned to float glass manufacture by glass processors or post-consumer glass cullet collected from existing buildings. It is imperative that both sources of glass cullet are exploited to find sufficient material to respond to the ambitious targets set by glass industry and increasingly demanded throughout the supply chain.
Demand for high-quality ‘furnace-ready’ cullet far outstrips the currently available supply of cullet. Research by manufacturers has shown that higher percentages of both post-industrial and post-consumer cullet is technically feasible without significant change to existing process or equipment. Despite the acknowledged benefits, there remains both real and perceived limitations to the implementation of increased postconsumer cullet in flat glass manufacture. This paper proposes a new industry approach and business opportunities to overcome these limitations.
The building demolition and glass replacement sectors continue to grow at pace, resulting in significant amounts of glass materials being removed from the external façades and interiors of our existing building stock globally. Deloitte’s 2016 study identified that 1.5 million tonnes of glass was removed from existing buildings in 2013 in the EU. Our research indicates this trend is increasing at more than 5% per annum and can be currently estimated at more than 9 million tonnes globally per annum. This represents a significant unfulfilled potential to recover end-of-life glazing for second use in new glass production by applying disassembly techniques to collect materials ready for high level recycling or for reuse.
Modern glazing elements are complex composite materials that require separation to find the full second-use value of the materials contained within them. Since the 1970’s flat glass has increasingly been processed into insulating glass units (IGU’s), formed of multiple layers of glass with polymer-based sealants, metal or polymer spacer bars and desiccant. Likewise, the use of laminated glass has steadily increased over similar time spans. These glazing products require new approaches to separation to realise the holistic value of the materials they contain.
Significant opportunities in technology development and new business implementation exist within the glass industry to take advantage of this position. This report will form the basis for a workshop during the 2023 GPD event and we look forward to welcoming the industry to this discussion. We have purposefully left out of this paper discussion on economics and business models. These important topics will form part of our workshop discussion with an aim to developing “ways to grow” new products and services to respond to the opportunities described in this paper.
Business as usual
At a global scale, glass materials removed from existing buildings continues to go to landfill. Despite growing glass recycling activities associated with building glass much of these rely on traditional demolition techniques that break the glass and combine it with other construction and demolition waste that do not result in sufficient quality for recycling back to flat glass. This is the business-as-usual approach described below. Cullet return schemes are already in place in a number of global geographies, yet many locations are still to tap this important source of high-quality pre-consumer cullet.
This is not only important to collect this glass but allows further development of new streams of post-consumer glass flows through the same system as described below. Flat glass manufactures and glass processors must implement these schemes as a matter of urgency where they are not already in place. Europe is global leader of this cullet return approach with cullet utilisation increasing from 20% to 26% over the last decade. This is now approaching maximum quantities of preconsumer recycling and therefore developing the infrastructure to collect, separate, process and transport post-consumer glass is now urgent to meet manufacturer’s declared targets.
Cullet return schemes that utilise empty float liner haulage has significantly reduced transportation costs and associated carbon emissions to alternative logistical arrangement and therefore must be part of the solution developed to collect more pre and postconsumer glass cullet for use in new glass manufacture.
Supply Loop Role Opportunities
As indicated in Figure 2 below, a gap analysis has been conducted through our research that has identified two new and specific roles between the demolition contractor and flat glass manufacturers that we recommend are adopted to ensure high quality furnace ready cullet can be created from materials removed from existing buildings. These two new players present a significant opportunity for existing businesses to move into these spaces. These new roles will establish a systematic approach to creating a greater yield of flat glass cullet in addition to attaining the highest value of recovery. The two roles are identified as the Specialist Façade Dismantler and the Glass Recoverer.
Specialist Façade Dismantler (SFD)
The role of the SFD is to deconstruct the façade into glazing assemblies suitable for glass recovery. This will require existing façade assembly knowledge to understand how to remove glazing components within the restraints of the building and the site. Existing methodologies and specialist equipment can be utilised to remove glass assemblies in a controlled process to allow the glazing units to remain intact.
The benefit of keeping the glass assembly intact is two-fold. It mitigates the chance of contaminates from demolition/construction sites prior to culletisation, the biggest risk in current practices which primarily require breakage of the glazing units during the demolition stage and it provides future routes for inspection, processing and reuse of both the glass panes themselves, and non-glass materials not currently salvaged such as sealants, spacer bars and interlayer materials. Transport of the glazing units to a safe and clean environment for culletisation is on stillages. Stillages reduce potential breakages and user error to reduce contamination. The SFD will then transport the glass assemblies on stillages to the Glass Recoverer. This journey replaces the transport needed to take the components to existing waste management or landfill and is predicated on a network of Glass Recoverer facilities located near sources of materials, such as large cities.
We see in the most recent glass recovery projects that existing specialist façade contractors are well placed to undertake the SFD role, utilising their skills and knowledge of the existing façade systems, supply chain connections both upstream (with main contractors for example) and downstream (with glass processors for example) positioning them well to undertake these dismantling works. There is a space also for existing demolition contractors to move into this role also utilising their skills and knowledge of disassembly and materials salvage depending on the nature of the façade being dismantled.
Glass Recoverer (GR)
The GR role provides a specialist service to generate high-yield, high-quality cullet to be returned back to flat glass manufacturers. Once the glazing units are transported to the GR, they will further dismantle the glazing units into individual materials using new and novel techniques and equipment. This approach maintains the very low contamination requirements and potential high value recovery routes, it also allows for careful sorting of different glass types prior to culletisation, producing cullet of quality equal or better than current pre-consumer cullet streams. This sorting ensures that the right materials are returned to the most appropriate second use. Further discussion on the development of these techniques and tools are described in later sections of this paper as is the need for defined cullet quality hierarchy codified in industry standards.
The role of GR is well suited to existing glass processors, particularly those with additional facility space to grow a new business around these material separation and collection activities. Glass processors have the technical knowledge of glass as a material, fabrication methodologies, flat glass handling equipment and existing cullet return systems which can result in very high levels of cullet separation into suitable graded and sorted materials, ready for collection.
Cullet materials not “furnace ready” can also be separated and sorted by the GR for transfer to other second use industry supply loops including that of container glass, glass-based insulation products and the like. Additional non-glass materials can also be separated and prepared for their second uses and recycling streams before return to manufacturers. Existing waste management or glass recycling companies may also be well suited to the role of GR, but current experience indicates that once materials enter the waste stream, they are rarely kept at sufficient levels of contaminated to be furnace ready. This approach therefore also proposes opportunities for these operators to grow new business models.
Reuse opportunities
Establishing the described recycling infrastructure and these proposed roles is essential for wide scale adoption of glass recovery from existing buildings for recycling back to flat glass manufacture. Additionally, it develops a system that could be transformed to process flat glass materials suitable for reuse, preparing glass panes for remanufacture or reprocessing into new products without remelt in the float tank, as indicated in the supply loop diagram in Figure 3.
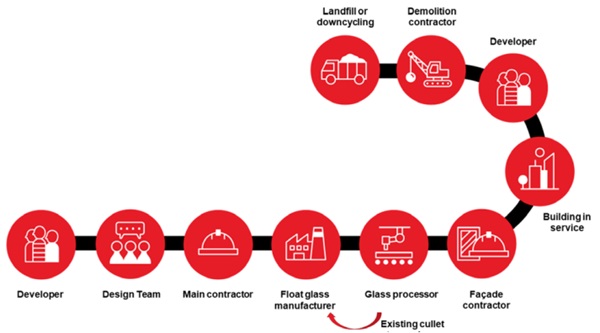
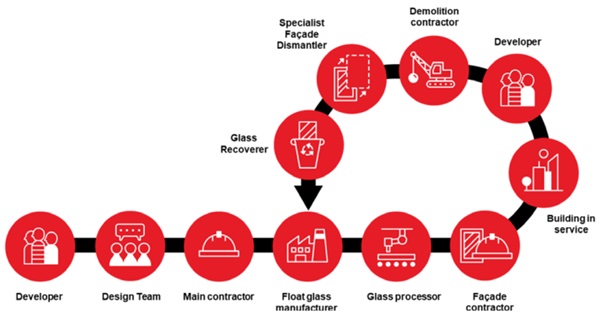
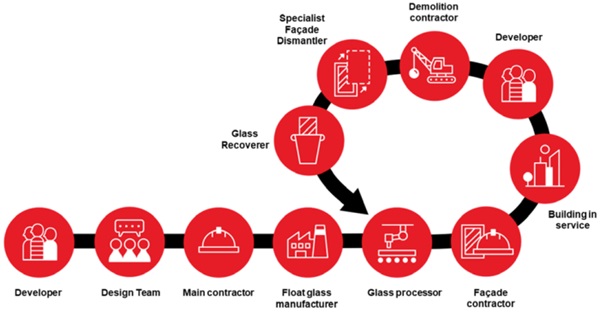
The role of consultants and client teams
To ensure the recovery of materials in practice, it is essential that this approach is considered early in the design and feasibility study stages of an existing building refurbishment or demolition project, well before façade dismantling is to take place. Through the specification of a series of important steps to ensure sufficient time and budget is allowed for the identification of materials, development of suitable dismantling methodologies, identification of SFD and GR project partners and recording of the process and outcomes is essential to successful material recovery.
Complex composite components
Modern glazing elements are complex composite materials that require separation to find the full second-use value of the materials contained within them. These glazing products require new approaches to separation to realise the holistic value of the materials they contain.
Glass materials
Most significant by weight and embodied carbon in these assemblies is of course the glass elements. These glass materials are typically in the form of IGU’s. Glass assemblies that currently can be broken using similar approaches to pre-consumer glass culletisation or utilise existing technology are classed as low-barrier glass assemblies. Glass assemblies that currently cannot be broken into cullet using a similar approach is classed as high barrier glass assemblies. These glass assemblies if separated and broken up properly may yet be suitable for flat glass recycling. Glass assemblies that contain elements that are currently not able to be recycled such as electronic glass have not been investigated in this study.
IGU’s with only monolithic glass are considered low-barrier glass assemblies. Mechanical methods such as hammers or crushing machines are a low technology methodology which provide a good yield of cullet with little investment or skilled labour. This process can be used as an entry level approach for Glass Recoverers to start to recover the central zone of monolithic IGUs but these methodologies leave glass stuck to the spacer bars and edge seals, reducing yield and raising potential for contamination to find its way into the cullet stream.
Improving the separation technology to provide high yield non-contaminated materials from IGU’s is an urgent industry requirement. Technology that allows first the removal of the edge seals and spacer bars, which themselves are recyclable when suitable separate from other materials, removing the multiple panes of glass whilst still intact, must be developed. This approach will then allow the appropriate treatment and sorting of the multiple glass types associated with typical IGU build-ups. This becomes even more important as we move from the earliest mostly monolithic IGUs, currently being removed from buildings to the growing complexity of more modern IGU make ups that will need to be reprocessed in the near future.
Particularly, this approach allows for a body tinted glass pane or a laminated glass pane to be removed from other laminated or monolithic glass panes, such that separate and appropriate reprocessing of individual glass panes can take place. This in turn allows different materials to be stored separately, ready for their most appropriate second use. Laminated glass, itself a composite material, requires an additional step of further reprocessing to be able to recycle the constituent materials and non-glass materials (interlayers) and these are considered in a later section of this paper.
Whilst some glass manufacturers accept laminated glass to be included in the cullet mix input at the furnace, the resulting combustion of the interlayer materials is not the preferred outcome for these valuable polymer materials.
Our research of mechanical processes for laminated glass separation indicates that at best, glass cullet is produced at a size of between 5-20mm with a fine glass cullet sub 5mm and PVB flakes. Due to the crushing approach, contamination may also be present. Due to these contaminants and the small cullet sizes, the output from the machines is not suitable for recycling back to flat glass. The cullet produced are therefore downcycled into components such as glass-based insulation products or aggregate for concrete. New methodologies of laminate glass separation, to produce clean glass and recycle ready interlayers materials are also urgently required.
Methodologies to remove post-applied films that are efficient are also urgently required to realise the full potential of materials available from existing buildings. Much of the historic glazing systems in buildings have been fitted with post applied films for solar control, security or privacy and the presence of these materials are an obstacle to recyclability. Glasses with ceramic frits and embedded electronics remain a significant challenge to recycle at high level, these too require methodologies and end-of-service strategies to be addressed.
With these challenges understood, it is evident that not all glass recovered from buildings will be efficiently separated and processed to a furnace ready level of quality. There is an urgent need for standardisation of a cullet quality hierarchy. This should be codified on a global level to allow for glass materials recovery, development of suitable separation technology advancements on the basis of the required gradings and standards. This ensures that the right material finds its right second-use. As such the existing demands from container glass, glass-based insulation products, road paints and aggregate can be fulfilled with materials that are suitable for that use criteria without downgrading materials that would be more suitable to supply the demand for higher order second uses such as flat glass production.
Any such specification of removal process and the standardisation of cullet quality needs to include material handling descriptions to ensure that the recovered glass is appropriately handled as to not increase the risk of NiS inclusion in the furnace ready cullet. Keeping glass intact for as long as possible in the recovery process allows cullet provenance to be more carefully recorded and tracked. With these process safeguards in place, glass cullet will have no additional risk of NiS inclusion than the raw material currently utilised.
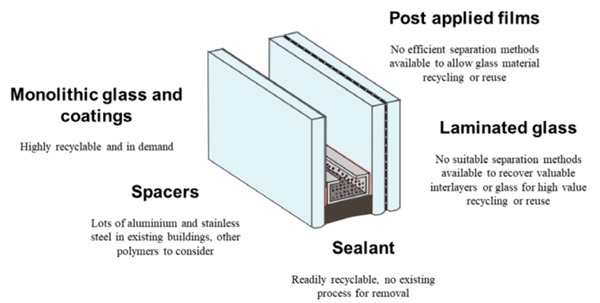
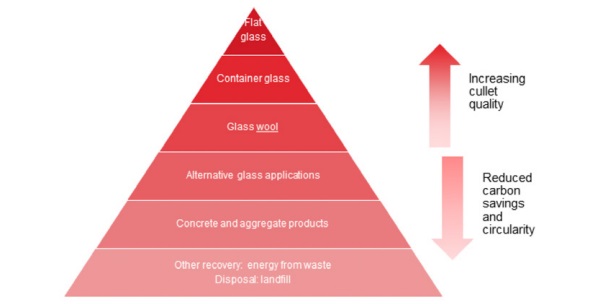
Non-glass material recovery
The framing elements supporting glazing units are typically made from metals such as steel and aluminium or timber. The ability to dismantle glazing units from frames is widely understood as they are a designed to be replaced in modern façade and glazing systems so that glazing units can be changed out in service. Metals are widely recycled in a mature market and therefore these materials are not discussed further in this paper.
In IGU’s the primary and secondary sealants are typically made from various polymers including polyisobutylene and silicone for example. Our research indicates that particularly silicone polymer manufacturers are ready to take back these materials if suitably removed from glazing units with minimal contamination. Routes for recycling exist for these materials to be utilised as feedstock for new polymer materials produced with an increased recycled content. Spacer bars are typically made from aluminium, stainless steel or various polymers. These materials can be readily recycled if suitably separated and collected. Careful removal of any stainless-steel spacers requires consideration as to ensure that no stainless steel enters the glass cullet stream.
Desiccants are the drying agent within the IGU spacer bars. It has been shown that these are readily dehumidified, reactivated and reused in industry. Opportunities to develop suitable collection and return systems for such materials would require further research and coordination with industry partners. In laminated glass, typical materials for the interlayers are polyvinylbutyl (PVB) and ethylene-vinyl acetate (EVA). Existing separation methodologies for recovering the interlayer materials are based on crushing and pulverising techniques which do not produce interlayer materials suitable for high level recycling. In this mechanical separation process, the interlayer flakes produced are typically contaminated with small yet significant quantities of fine glass particles.
To recycle the interlayers, further cleaning processes are needed which is often cost prohibitive and does not result in sufficient quality for recycling into new interlayer material. The cleaned interlayer flakes may be used for applications such as binders in adhesives, incinerated at energy from waste plants or sent to landfill. There are therefore opportunities to create new techniques that recover interlayer materials without contamination and that do not alter the interlayer’s physical characteristics as the manufactures are demanding return of materials for recycling into new products. For glass with post-applied films the removal of the film prior to culletisation is preferred and opportunities to develop efficient technology to remove film from glass exist and suitability of these materials for recycled following their removal needs further research.
Conclusion
It is accepted that increasing the use of recycled content of new glass products by utilising high quality, sorted glass cullet plays a crucial role in reducing the energy demand, process emissions and therefore the carbon footprint of new glass products. It is imperative that all sources of flat glass cullet are exploited to find sufficient material to respond to the ambitious targets set by the glass industry and increasingly demanded throughout the supply chain.
There remains significant unfulfilled potential to recover end-of-life glazing from existing buildings for a second use in new glass production and new processes and equipment are urgently required to collect materials in a suitable way such that they are furnace ready for high value recycling or for reuse. Significant opportunities in technology development and new business implementation exist within the glass industries to take advantage of this position.
We look forward to finding new ways to grow this topic during our workshop session at GPD 2023 and look forward to welcoming the industry to this discussion, finding ways to collaborate and drive forward the industry change required to meet this challenge.