Authors: Michal Ganobjak, Wim J. Malfait, Janis Just, Marcel Käppeli, Francisco Mancebo, Samuel Brunner & Jannis Wernery
Source: Journal of Building Engineering, Volume 64, 2023, 105600, ISSN 2352-7102 | https://doi.org/10.1016/j.jobe.2022.105600.
(https://www.sciencedirect.com/science/article/pii/S2352710222016060)
Abstract
Silica aerogels are thermal superinsulation materials that have found increasing application in the building sector in the last ten to fifteen years. While the most common material types are opaque insulating blankets and renders, in its monolithic form silica aerogel can be almost transparent, allowing for composite translucent insulating building system.
Here, we developed and characterized a novel modular, translucent and thermally insulating building component based on silica aerogel granules, the aerogel glass brick. Both thermal and mechanical properties were tested and the former were compared to a 3D simulation of the heat transfer through the brick. The glass brick has a measured thermal conductivity of 53 mW/(m·K), corresponding well to the simulation results of 51 mW/(m·K), and a compressive strength of almost 45 MPa. This makes the glass brick the insulating brick with the highest insulation performance reported in literature or available on the market, and at the same time adds the feature of light transmission.
The aerogel glass brick is suitable when the requirements combine daylighting, glare protection and the need to protect privacy, e.g. offices, libraries, museums; an analysis of the materials costs indicates that the insulating glass brick can be competitive in such applications. The glass brick provides architecture with new design opportunities to increase daylight inside buildings.
Graphical abstract
1. Introduction
Building envelopes of existing buildings represent a great opportunity to improve energy efficiency and thermal comfort of our cities and countryside. Aside from improvements on building technology, HVAC energy demands are typically reduced by increasing the thickness of the insulation layer. However, this solution does not work for the transparent façade elements, and in fact, thick insulation layers increase shadowing around the windows. Thus, a new envelope construction system that can reduce lighting and HVAC energy demands simultaneously would be a highly attractive solution. Here, we present an aerogel glass brick that has a high thermal insulation performance for its limited thickness, and simultaneously increases solar gains, reduces the use of the artificial light, and improves visual comfort.
Rising standards on wellbeing, interior microclimate and energy efficiency of buildings bring a new dilemma for existing buildings. Buildings consume approximately 40% of energy globally [1], p. 174] and 20–60% of all energy used by buildings is affected by the design of the building envelope [2], p. 20]. According to predictions “more than 50% of the current global building stock will still be standing in 2050, and in OECD member countries, that figure is closer to 75% or higher” [2, p. 21].
Around 55% of people live in the cities and this number will increase in the future [3]. Cities bring more opportunities and a higher standard of life – e.g. less manual work, abstract specialized work, job opportunities, higher salaries, leisure activities, easier access to goods and services, etc. This high density of population is related with adverse effects of noise, bad air quality, heat island effect, less access to nature and less access to daylight. In high income countries, the percentage of the population living in cities will be 70–88% in 2050 [3]. At the same time it is known that people spend more than 90% of time indoors [4], p. 2]. With the move from rural areas to cities, urbanization, and the change in nature of work, the time spent indoors is increasing. Natural daylight influences our circadian rhythms, the release of hormones, sleep-wake cycle, mood and our cognitive activities [5,6]. The detachment from the nature due to interior lifestyle and artificial daylight and omnipresent screen light may negatively influence human well-being [7,8]. We hypothesize that translucent façades may be a good opportunity to compensate this lack of natural daylight, to bring humans closer towards natural daylight without moving them out from the interior. This would be done by using translucent walls instead of opaque walls, already in the building design stage. Although the main recommendation is to spend more active time outdoors [9] in fresh air and light [10], translucent façades can bring natural daylight into interior, and thus may bring people closer to their natural biorhythm.
Perimeter walls and building envelopes are mostly opaque and often achieve the loadbearing function and effective thermal insulation (low U-value) by combining structural and insulation layers as in external thermal insulation composite systems (ETICS) or renders [11] Good thermal performance is achieved by increasing the insulation thickness and hence the thickness of the perimeter wall. Transparent or translucent windows and fillings of openings for daylight are thinner, but as a consequence, with relatively high U-values, they do not insulate as well as other wall systems. Self-supported façade wall systems with daylighting properties have been in use for many decades [12]. Transparent and translucent glass blocks (luxfers) can offer great possibilities for daylighting and the functional design of the façade.
Glass block walls can carry their own load thanks to the frame and the structure that is cast out with reinforced concrete. Glass blocks are typically made by joining two shells of glass. They are available with low internal pressure or with a middle partition to improve U-value. In this solution, the glass joint perpendicular to the wall represents a major thermal bridge. The design of glass blocks has not been improved sufficiently with respect to the thermal properties for decades, even though some theoretical improvements were suggested [13]. Theoretical solutions to limit thermal bridging in this joint have been presented [14,15], including plastic connectors filled with aerogel [16], but practical solutions are still not available. While these glass bricks are relatively thin with 80 mm thickness, their high U-value severely limits their use in times of energy efficiency.
As an alternative to glass bricks, translucent panels can cover big surfaces with thin façade solutions. These panels are not loadbearing, require framing and have intermediate U-values. It is possible to improve the thermal properties of translucent panels and elements with transparent insulations such as low pressure air, vacuum, honeycomb structures or silica aerogels. Silica aerogel granules offer very low thermal conductivities for space savings in dense urban areas [17], vapor diffusion openness, superhydrophobicity and, depending on the supplier and method of production, can achieve very good optical properties [18] and authors already investigated their use in the translucent envelopes [[19], [20], [21]]. This combination brings interesting possibilities for the refurbishment of buildings with glazed areas or even for new constructions. The last two decades have seen the adoption of silica aerogel in buildings (Fig. 1) [22]. In 2001, opaque aerogel blankets were introduced into the market by Aspen Aerogel, with rapid growth in the industrial insulation market, followed by application developments for the construction sector. Granular aerogel solutions were one of the very first for the use in buildings.
In 2003, Cabot Corporation - producer of silica aerogel granules - introduced granules with very high optical clarity. In the very same year, they were used already in Zurich, in the gym hall “Buchwiesen”, in the form of aerogel-translucent polycarbonate (glass fiber) boards [23]. The American company Kalwall brought their thermally isolating polycarbonate panels to the market in Europe also in 2003 [[24], [25], [26]]. Pilkington Glass has been offering insulating U-channeled glass profiles solutions with polycarbonate incorporated aerogel panels since 2004. Birdair sells insulated translucent membranes for tensile architecture with an aerogel sheet with a range of visual transmittance from 2.2 to 4.3% [27]. As of 2021, the Kalwall company has already 600+ applications with translucent panels filled with aerogel [24] and many customized designs have been introduced during the last years. In 2019, the public demonstrator building Nest at Empa showed a new example of a translucent façade with aerogel [28] (Fig. 1).
![Fig. 1. Timeline of the use translucent silica aerogels in buildings (bottom) and opaque aerogel applications (top) [[22], [23], [24], [25],[29], [30], [31], [32], [33], [34], [35], [36], [37], [38], [39], [40], [41]].](/sites/default/files/inline-images/Fig1_288.jpg)
Despite the progress on aerogel-filled panels [[42], [43], [44]] and other high performance solutions, there is no construction element on the market which offers loadbearing functions, thermal efficiency and translucent properties at the same time. In this paper, we fill this gap by presenting the prototype of a translucent glass brick filled with silica aerogel (Fig. 2). The Roman architect Vitruvius suggested that a building and its material should have durability, function and beauty [45]. All three of these attributes increase the resilience of the material, extend its life expectancy and can be considered aspects of sustainability.
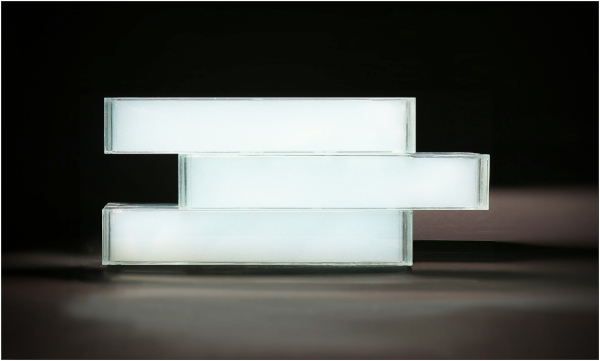
In this study, the goal was to design and characterize a new element for insulating and translucent building envelope wall which adheres to the three Vitruvian qualities and at the same time offers a new combination of improved energy efficiency, increased daylight in the building and space efficiency. To do so, we developed a translucent and insulating glass brick, which we evaluated in terms of its thermal and mechanical properties through measurements and simulation, achieving a very low thermal conductivity of 53 mW/(m·K) – the lowest reported in any insulating brick – and good mechanical properties. The glass brick filled with translucent silica aerogel can offer a new structural façade element for perimeter walls with high thermal performance and an aesthetic and durable surface for daylighting possibilities and large area applications (Fig. 3).
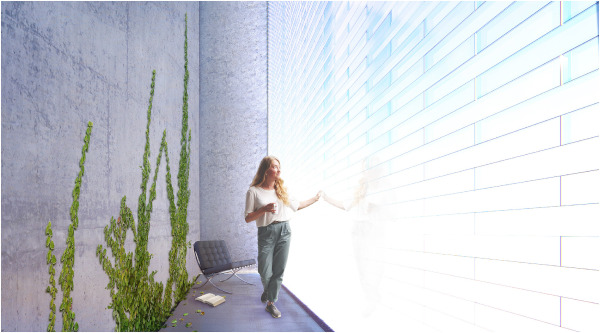
2. Materials and methods//design and measurements
2.1. Materials
The glass brick was made from regular float glass, epoxy and aerogel granulate. The glass panes in the brick were connected with epoxy spacers made from the transparent epoxy resin Esprit Composite Epoxid-Kristallharz EC 141 with low viscosity and high clarity. The cavities of the created brick structure were filled with tapped aerogel granules (Lumira LA1000 from Cabot) with a high optical clarity of >90% Visible Light Transmittance (VLT) per cm [29]. The thermal conductivity values of the used materials were as follows: float glass: 1000 mW/(m·K) as given by the glass supplier; epoxy resin: 226.5 mW/(m·K) as measured on small guarded hot plate device; aerogel granules: 18.6 mW/(m·K) as measured on large guarded hot-place device (range depending on density given by manufacturer: 18–23 mW/(m·K) [29]).
2.2. Brick design and assembly
Several designs of the brick were prepared with various shapes, materials and details. Glass panes were connected with epoxy spacers. Different spacer shapes and glass pane distances were characterized in terms of the heat flow through the whole brick using two-dimensional thermal simulations in the open source software Therm 7.6 (program developed by Berkeley Lab) [47] and the previously measured thermal conductivity values listed above. Using Therm allowed for fast screening of many two-dimensional designs. Several designed internal spacers were tested and evaluated for heat transfer. The boundary condition were selected according to the Swiss standards for U-value calculation [48], with an outside temperature of −8 °C and an interior 20 °C, corresponding to a temperature difference of 28 K. From the evaluated designs, the one with the best combination of manufacturability, low heat flow and good optical properties was selected as internal spacer.
The final design (Fig. 4) consisted of four 12 mm regular float clear glass panes connected with spacers, with the side, bottom and top faces sealed with a 1.5 mm epoxy layer. The spacers were cast directly in between of the glass panes with the help of silicon molds in the shape of spacers. This technique glued the glass panes together while at the same time creating transparent spacers in between. Two shape type of plastic (epoxy) spacers were used to create chambers between the four glass panes. U-shaped spacers (Fig. 4) were employed on the outer layers for aesthetic reasons to give the brick look of robustness and depth. In the middle chamber spacers in zig-zag shape with reduced heat transmission were used. The offset position and shape of spacers is designed to reduce thermal flux. In a similar way as for the spacers, the bottom and side envelope was poured from epoxy with thickness of 1.5 mm. A small opening was left in the seal of each of the six resulting cavities – four in the middle layer of the brick and one in each outer layer. These cavities were filled with tapped aerogel granules without binder and the openings sealed with transparent tape. The final dimensions of the brick are 500 mm × 136 mm x 84 mm.
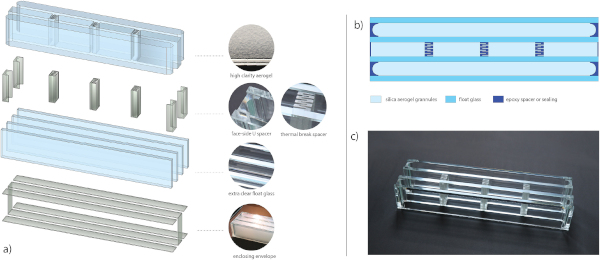
2.3. Thermal simulation with TRISCO
In order to determine the thermal performance of the whole brick including the sealing, a three-dimensional thermal simulation of the brick was performed using Physibel's Trisco software. Boundary temperatures were set at −8 and 20 °C for outside and inside, respectively, according to the Swiss standard on U-value calculation [48]. Additionally, two bricks with a 2 mm gap between them were simulated to compare to the scenario of the physical measurement of equivalent thermal conductivity. In both cases, the brick shape was simplified into a voxelated 3D model with an accurate representation of the brick.
2.4. Thermal conductivity measurements
The thermal conductivity of the epoxy was measured on a custom made guarded-hot plate device constructed for small samples of low thermal conductivity [49]. The measuring zone is 25 mm × 25 mm and accuracy 10%. The difference of temperatures between hot and cold plate was 15 K and the measurement temperature was room temperature. The sample of epoxy was of size 60 mm × 60 mm, with a thickness of 10 mm.
The equivalent thermal conductivity of a mock-up sample wall consisting of glass bricks was assessed by a large-scale guarded hot-place device following the criteria of SN EN 12667 and ISO 8302. The measurement area is 300 mm × 300 mm and plate size 750 mm × 750 mm. This device can measure samples up to 1000 mm × 1000 mm (Fig. 5). The measured mock-up wall - cladding without mortar or any adhesive - had dimensions of 500 mm × 510 mm with 136 mm thickness and was made up of six rows of bricks (three full bricks and six half bricks) in the classic “stretcher bond” laying of the bricks without glue or mortar and a gap between bricks in both direction of roughly 2 mm. Since bricks were manufactured by hand and their thickness varied (136 ± 1.5 mm), two rubber blankets of 5 mm thickness of known thermal conductivity were used to level the bottom and upper surfaces of the sample. The thermal resistance of the rubber blankets was subtracted from the total measured thermal resistance of the sample. The final equivalent thermal conductivity of the brick wall was calculated from the resulting value. A grey expanded polystyrene sample of dimensions (750 × 750 x 100) mm3 was used as a reference sample.
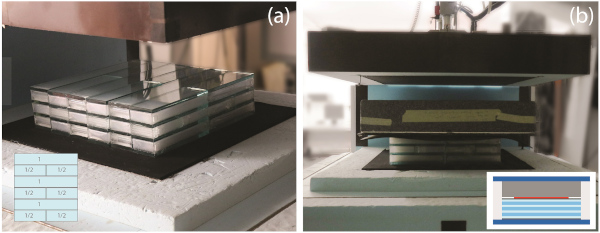
2.5. Compression strength measurement
One whole glass brick of size 500 mm × 136 mm x 84 mm was tested for its compressive strength using a compression testing machine of Alfred J. Amsler & Co. Schaffhausen, Switzerland, with a maximum capacity of 5000 kN. For that, the brick was placed horizontally into the machine, with the glass panes being vertical and the mechanical load also vertical (Fig. 6). This corresponds to the placing of the brick in a wall cladding with vertical loads. To evenly distribute the stress and account for any unevenness of the brick, a piece of high-density fiberboard of the company Pavatex was placed below and above the sample. Also, one of the plates of the testing machine was hinged and hence adjustable to the sample. The loading speed was 0.6 MPa/s and the brick was compressed until failure.
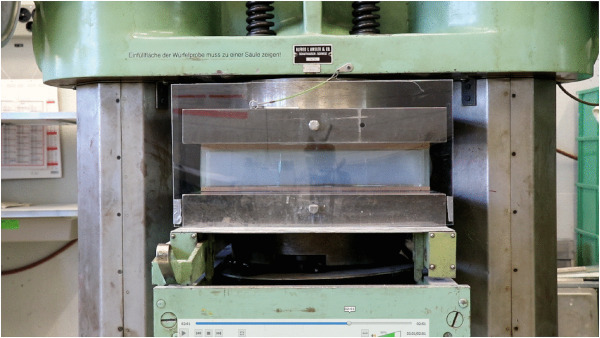
3. Results and discussion
3.1. Brick and spacer design
Different shapes of spacers were simulated on how they would hinder heat flows inside the brick (Fig. 7). Open shape spacers (A, B, C, D, E, F, M, N, O) are filled with silica aerogel granules, whereas enclosed cavities (G, H, I, J, K, L) were filled with the air for purpose of the simulation. For the internal cavity the zig-zag shaped spacer N (Fig. 7) was selected because it had the lowest simulated U-value and because it was possible to cast this shape in between panes of the brick. At side of the brick, U shaped spacers marked O were selected as a compromise between heat flow and mechanical stability. The final prototype bricks used 4 sheets of 12 mm glass panes (Fig. 4), initially with designed 30 mm gaps (29.3 mm in practice) for a total brick thickness of 136 mm.
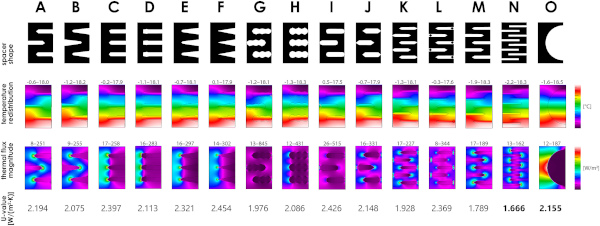
3.2. Thermal and mechanical performance
The thermal simulation of the entire brick included the top and bottom cover of the brick in the 3D simulations. The 3D thermal simulation in Trisco (Fig. 8) resulted in a U-value of 0.350 W/(m2·K) for the 136 mm thick brick, corresponding to an equivalent thermal conductivity of 50.5 mW/(m·K). This is very close to the measured value on the guarded hot plate device of 0.365 W/(m2·K), corresponding to an equivalent thermal conductivity of 53.0 mW/(m·K). For simulation within these boundary conditions, there is a smooth redistribution of the surface temperature on the faces of the brick (Fig. 8), which suggests no observable thermal bridging within the structure of the brick. The simulation and experimental convergence is very high, and the minor difference may be due to simplification of the model, uncertainties in the material properties used in the simulation, or experimental uncertainties in the measurement of the prototype. The compressive strength of the element was 44.9 MPa, corresponding to a maximum applied force of 3042 kN, before total collapse of the brick structure.
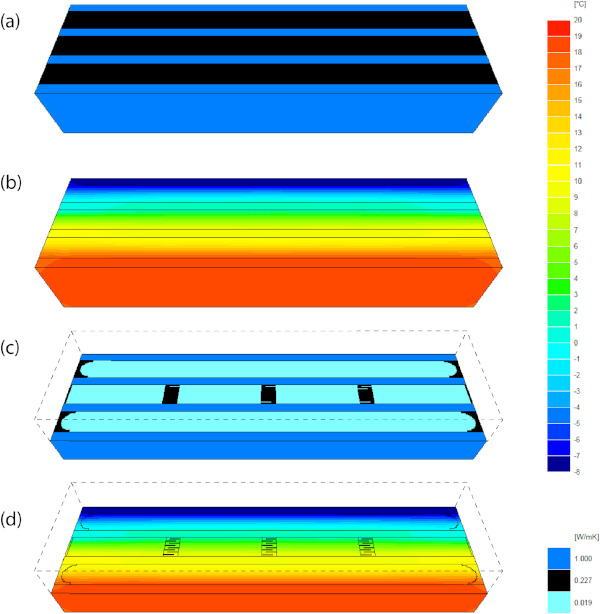
The prototype of the brick showcases a novel approach in daylighting elements with its combination of loadbearing, translucent and thermal insulating properties and substantial improvements of these characteristics. It can be used in design as a substitution for opaque perimeter walls with additional daylighting advantage (Fig. 9). Comparing to standard, opaque insulation brick blocks, the aerogel glass brick is multiple times stronger in terms of its loadbearing property. With its low thickness, the glass brick can bring extraordinary thermal properties and allows a lot of natural daylight to come into the interior.
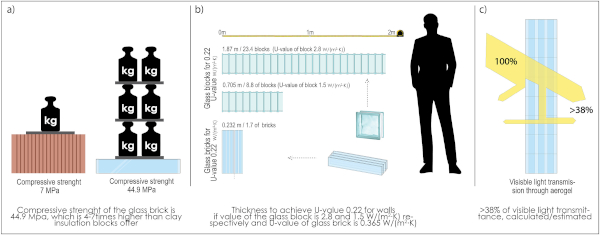
The characterization of the brick presented above shows that a very high-strength material system can be realized with a low thermal conductivity and a good light transmission. This bridges the gap between daylighting elements - windows and thermally insulating walls - and a variety of opaque of construction material from a thermal insulation point of view (Fig. 10). In the following, we will first discuss the individual properties of the brick and then its combined properties and application potential.
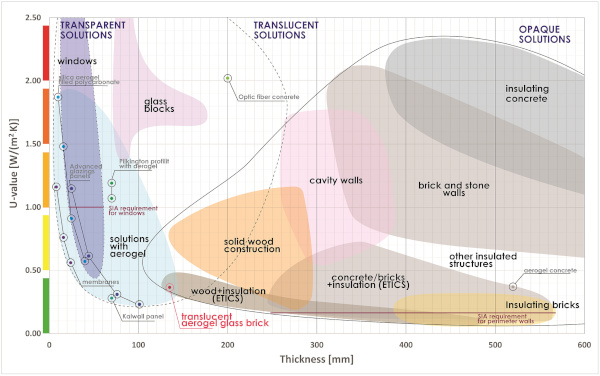
The thermal conductivity of the brick is very low with 53.0 mW/(m·K) – in fact all commercial systems as well as scientific prototypes in development, to our knowledge, have higher reported thermal conductivities, with the best insulating, opaque (!) brick having a thermal conductivity of 59 mW/(m·K) [50]. With the realized thickness of 136 mm, the brick achieves a U-value of 0.365 W/(m2·K) according to the measurement, which is higher (less efficient) than legal requirements in central Europe for opaque walls (e.g. 0.17 W/(m2·K) in Switzerland [48,51]), but considerably lower (more efficient) than requirements for windows (1.0 W/(m2·K) in Switzerland [51]). However, the brick can also be designed with a higher thickness in order to provide an even better insulation effect. Since the glass brick allows to achieve a great insulating property with a single layer for a ready perimeter wall, and does not need any other finish layers, construction time can be significantly reduced, leading to concomitant reductions in construction and operational costs.
With a compressive strength of 44.9 MPa, the compressive strength of such a brick is several times higher than clay insulating bricks and brick blocks available on the market (Fig. 9). These typically have compressive strengths between 6 and 13 MPa [52]. However, insulating bricks are usually much thicker, starting at around 365 mm and more. Conventional load-bearing clay bricks are used in thicknesses comparable to the glass brick and have compressive strengths around 28 MPa [53]. If these bricks serve as primary construction they require additional thermal insulation to achieve standard thermal comfort with the structure, which at the end brings new technological steps (e.g. application of the penetration paint, mortar-glue, core plaster, ETICS system anchoring, glass fiber mesh, finish plastering, paint) and extended time for scaffolding and at the end does not make walls thinner. The main findings are summarized in Table 2 which shows simulated and measured values.
The light transmissivity of the glass bricks was not studied experimentally but can be estimated from existing data on aerogel granules. The total thickness of the translucent silica aerogel in the brick was about 90 mm. Assuming a visible light transmission value of >90% per cm [29], the lower bound of the transmissivity is estimated at 0.99 = 0.38, e.g. >38% (only aerogel granules without glass). The exact light transmission in whole spectrum UV–vis-IR of such composite translucent element is difficult to evaluate experimentally at the prototype level due to internal reflection, scattering and absorption of the light. For a commercially available elements made of transparent polycarbonate and aerogel granules with a total thickness of 70 mm, the range of transmissivity in the visible range was given as 15–21% [24]. Panel made of polycarbonate is a light-weight solution.
Glass on the other side is often a more durable solution of higher quality with loadbearing possibilities. Kalwall is using fiberglass reinforced polymers in the setting and colorized panels which result in less visible light transmission. Another producer offers 4 inch (101.6 mm) glazed panels with visual light transmission range between 5% and 20%, varying with influence of glass, internal honeycomb structure and light diffusive veil [54]. The amount of light transmitted through the glass brick can be affected by reflectivity of outer surface glossiness, type of glass, clarity of aerogel granules, latitude, weather and daily position of the sun. In the design, float glass 12 mm was used with 0.84 visible light transmissivity. There is possibility to use extra clear – low iron glass with 0.90 visible light transmissivity [46].
With the presented estimate, a wall made of translucent bricks would provide roughly the same light transmission as a wall of the same area, where roughly 20–40% of this wall would be made of windows and the rest of an opaque material. Assuming that rooms usually already have a window, extra daylight gains can be created with a translucent envelope wall. The aerogel allows IR radiation to pass through enabling solar gains in winter, but with a risk for overheating in summer [21,55] For this reason visible light transmission percentages over 30% are not recommended for most Kalwall applications [24]. Although UVA and UVB radiation is mostly filtered by the aerogel granules (and the glass), visible light necessary for photosynthesis is still transmitted and diffused light penetrates deeper into canopy of vegetation [56], which makes glass bricks suitable for greenhouse application like in other aerogels applications [24,55].
In summary, it can be said that the aerogel glass brick most likely transmits slightly less light than other, thinner translucent aerogel solutions, such as polycarbonate panels. However, it is much stronger mechanically with the measured compressive strength. Even typical completely opaque brick walls often used in combination with ETICS have significantly lower compressive strength. This makes the glass brick a unique solution combining good light transmission with excellent mechanical strength.
3.3. Potential for energy savings
Building represent about 40% of energy consumption with ratio residential buildings 27% and 12% commercial building [1, p. 174]. Around 60% of energy loss is due to the building envelope. Energy consumption by interior lighting represent about 10% in residential buildings and about 20% in commercial buildings [57]. The glass bricks shown here can save energy by utilization of daylight, by use of solar gains and by creating a thermal barrier against loss in space heating and space cooling. This is of particular interest in commercial and public buildings (services), which are particularly used during daytime. Of course, the potential for energy savings due to solar gains and savings in terms of lighting depend strongly on the location and orientation of the building which in term determine the amount of incident solar radiation. Hence, this aspect should be explored in more detail in the future by the examination of specific building examples in several different locations.
3.4. Where the aerogel glass brick can be used
The brick is suitable for aesthetic architectural design (Fig. 3, Fig. 11) for representative buildings with generous foyer, patios and glazed walls, and/or in positions, which do not require visual contact with the exterior while would like to utilize natural daylight. Bricks are appropriate for buildings, where it is required to avoid visual connection from exterior (privacy, security, avoidance of disturbances, etc.) and to bring daylight inside e.g. offices in busy areas. Diffusive light is appropriate for libraries, art workshops, galleries, museums, foyers, staircase core and everywhere, where it is necessary to eliminate dark areas and strong shadows, secure proper illumination, while avoiding direct sunlight glare. The usage of the brick can be suitable for large-scale spaces, where it is necessary to bring proper illumination deeply into the interior (gym hall, libraries, multipurpose halls, etc.).
Translucent bricks are appropriate for solutions - harvesting heat from sunlight by infrared radiation, e.g. enclosed tropical gardens, greenhouses, patios or Trombe walls for heat energy utilization [58,59]. The glass brick can be suitable for clients building their family houses, patios or representative public buildings and spaces. Furthermore, it can be used for retrofitting as high thermally insulating replacement of glass blocks (luxfers) in buildings built from the 1960s–1980s, when use of inefficient squared glass block was very popular for daylighting of the staircase areas. The new insulating aerogel glass brick has the potential to bring appropriate illuminating conditions, high aesthetic value while offering high thermal insulation performance. For some locations in residential buildings, nocturnal light pollution may represent a challenge, but this can be avoided by interior curtains, blinds and light impermeable bed canopies.
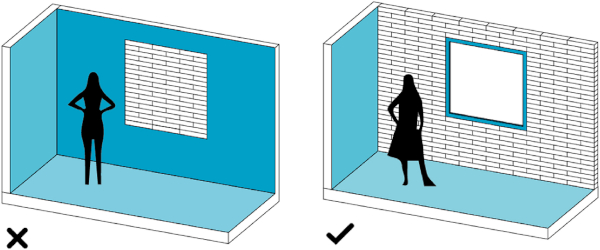
4. Conclusion and outlook
Here, we have developed and characterized a new insulating and translucent brick for building envelopes. It is unique in its thermal performance, with a thermal conductivity of 53 mW/(m·K) which is below even that of any reported opaque insulating brick. The brick has a high compressive strength, which is important for its use in facades as self-supporting walls. The presented brick provides a new, aesthetic solution for building envelopes that not only insulates well but also brings natural daylight into the interior of the building. With that, it can offer architects a completely new way to co-design building pleasant facades and interiors, making better use of the natural resource of daylight in buildings.
4.1. Open technical questions
Using transparent aerogel brick opens the potential to create a building envelope with a mechanically self-supporting translucent façade. The measured compressive strength is clearly higher than what is needed for this application and can be optimized (Fig. 9). The main challenge is to optimize the brick design and cladding details for practical use in masonry and to determine the optimal adhesive between bricks (mortar or glue). Future studies will investigate the strength of the wall cladding in comparison to single brick strength. For enhancement of safety, the brick has to be improved against collapse under impact of high pressure, e.g. by lamination of the glass or using safety glass. Resistance to fire needs to be investigated.
The lateral shear forces of such a thin building envelope will need to be taken into account and future research should study the possibilities of reinforcing a wall built with one layer of these bricks. Also, the thermal behavior of a wall in whole cladding should be studied in the future. The measurement of transmissivity is another open challenge, since aerogels as quasi-homogenous materials have substantial internal reflection and scattering. Improving manufacturability is required to reduce costs and can make the brick affordable at the market. The materials cost, while substantial (Table 1), is not a major barrier given the performance. Finally, the energy consumption of new and retrofitted buildings with this type of external wall should be determined in future work.
Table 1. Selected parameters of the materials.
Table 2. Summary of results.
4.2. Outlook
The presented new brick design allows edge-to-edge frameless construction of highly insulated translucent walls with mechanically self-supporting function. The use of glass offers glazed internal and external surfaces, which are weather resistant, user-friendly and durable finishing materials, in contrast to polycarbonate panels. Highly insulating, thin, translucent perimeter walls allow to harvest natural daylight and secure thermal energy gains in the building's overall energy balance. Architects and civil engineers will have more possibilities to saturate natural daylight demand in the designed space, as almost the full spectrum of daylight is transmitted. This brings visual privacy, eliminates glare and diffuses direct natural sunlight - softening sharp shadows of direct light, lighting deeper areas of the interior with diffused daylighting. Light, thin and energy efficient perimeter walls are possible with this solution. We believe that aerogel the filled glass brick can bring more light into interiors of buildings through the building envelope, while improving health, and helping to save energy necessary for lighting and heating.
In summary, we have presented here a translucent, insulating brick for building envelopes with improved energy efficiency – achieved by very good thermal insulation in combination solar heat gains – with increased light comfort – via the transmittance of daylight into the building – and with optimized spatial efficiency – due to the low thickness achieved by the use of thermal superinsulation.
Author statement
Michal Ganobjak: Conceptualization, Writing - Original Draft, simulations, measurements, Writing - Review & Editing, Visualization, Revising.
Wim J. Malfait Writing - Original Draft, Writing - Review.
Janis Just Measurements, Review.
Marcel Käppeli Measurements, Review.
Francisco Mancebo Simulaitons, Review, Revising.
Samuel Brunner Writing, Measurements, Review & Editing.
Jannis Wernery Conceptualization, Writing - Original Draft, Writing - Review & Editing, Revising.
Declaration of competing interest
The authors declare the following financial interests/personal relationships which may be considered as potential competing interests:Michal Ganobjak, Jannis Wernery, Matthias Koebel has patent #E 2017-310 pending to Empa.
Acknowledgements
This research was supported by Velux Stiftung, project No. 1440 on development of thermal super-insulating translucent glass brick for diffusive daylight. The idea was developed with support of the European Union's Horizon 2020 Research and Innovation program under the Marie Skłodowska-Curie Actions, grant agreement No. 746992.
We would like to thank the two anonymous reviewers for their helpful comments on the first version of the manuscript.
Data availability
Data will be made available on request.