First presented at GPD 2017
Abstract
The use of structural glass in Architecture has always been a challenge since the beginning of time, and despite Peter Rice’s first great achievements in this field in the middle of the XX century, it is something that we should always try to improve and seek greater achievements. If we add the desire to achieve the largest possible glass dimensions that can be made with the greatest transparency (see figure 1) then the challenges are big.
The concept of architectural design in the Auditorium of the New Headquarters of the Banco Popular in Madrid (Spain) was made by Arquitectos Ayala and ENAR as part of the Architects team. It is a question of combining all the previously mentioned ingredients to achieve the Architect and Facade Consultant intention of creating a double skin glass with the fewest visible pieces as possible in order to eliminate the visibility of any supporting structure. By this way, we are able to have a fully “transparent box” for the enjoyment of the people who use this facility.
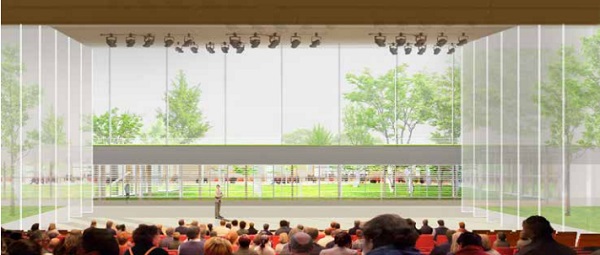
Introduction
This document refers to a small explanation of the Auditorium execution process from the design and development of the technical solution, testing, manufacturing, to its final execution. As usual in this type of singular projects, the design and calculations were essential to ensure the correct functioning of the facade system. Obviously, to build a glass box, the first objective was to define the structural concept of the double skin and run the calculation of all elements that forms part of the entire system.
Once the calculations were done and the compositions of the glasses were defined, the next step was to test a real scale mock-up in a certified laboratory to check its feasibility. If the results were as expected at structural and performance level then the manufacturing and assembly phase can begin.
Although the manufacture required a great control to avoid problems of lamination and finishing due to its large format, the biggest challenge was the installation due to the fact that the Auditorium is located between two large buildings with limited access to the glazing logistics and resources.
Typical details
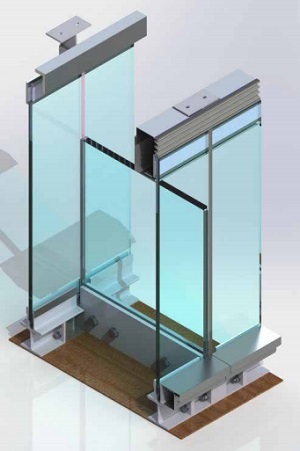
After reviewed the original drawings and specs, the initial idea was clearly defined. The exterior and interior glass should have a dimension of 2,600x9,500 mm (width x large) and both surfaces should be separated 700 mm with a 7,980 mm glass fin inside between them.
A top gap (1800 mm) was required to allow the passage of two bespoke rail systems for future maintenance (see figure 2). All the glasses are composed with low iron glass to focus the transparency and laminated with standard PVB.
The inner and outer glass panes are fixed in its lower part in the 3 axes and supported on a hidden metallic substructure.
However, in the upper end the glass are fixed in axes (x, z), leaving free movement in the vertical (figure 3). In relation to the glass fin, it is embedded 280 mm in its lower part by the use of screws, using polyamide, nylon and resins in the holes for proper operation.
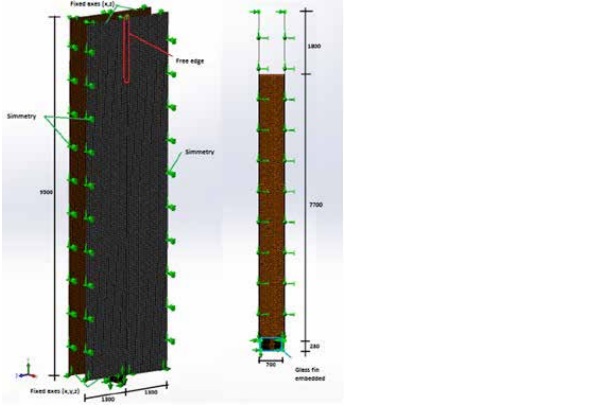
Structure and analysis
The design calculation of the agreed solution was made by Autodesk Robot Structural Analysis, SolidWorks Simulation (figure 3) and SJ Mepla.
Initial conditions:
Wind pressure: Wp=Ws= ±0,6 KPa (typical bay)
and Ws= -0,9 KPa at corners (first 2,6 m)
Horizontal live loads: 1,6 KN/m (h=1,2 m)
Maximum displacement for outer/inner panes:
L/65 or 50 mm
Upper slab maximum deflection: 32 mm
After all the calculations (SLS and ULS), the final glazing compositions are:
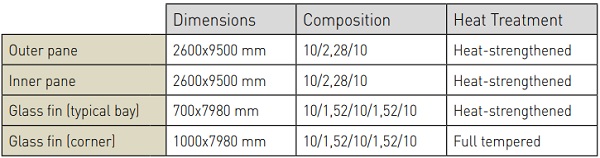
On the other hand all the joints required to bond the glass panels were designed, and tested is chemical and adhesion between all the elements. For example, the joint with the vertical aluminum profile (figure 4), the top horizontal edge and a special vertical join at corners.
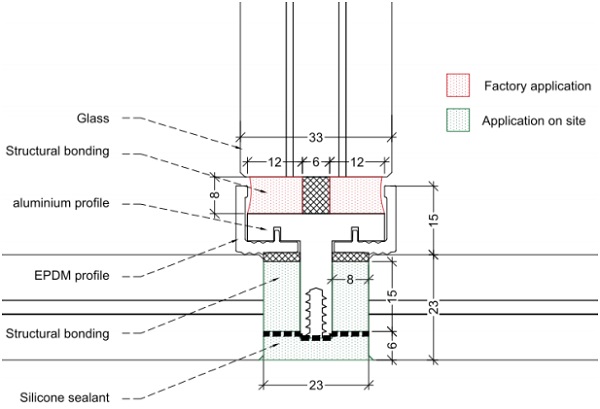
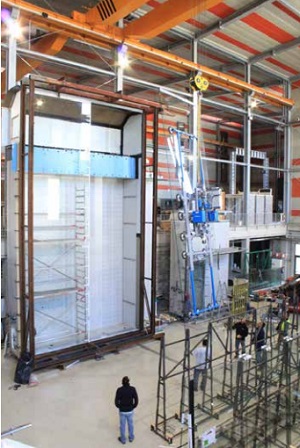
In figure 4 we can see that the bond process of the aluminium profile to the glass fin were made in the factory, while the strings that join the side of the glass with the metal profile itself is made with the same material, but on site.
The design allows Appling the silicone only with two surfaces contact. Finally the finishing silicone is applied also on site. As required by the Architect all aluminium profiles are hidden creating the desired effect of a completely “glass transparent box”.
Testing of prototype Due to the large dimensions of this façade it was required to create a special chamber (first of its kind in the Iberian Peninsula) to perform the laboratory tests (see figure 5).
Test for air permeability, watertightness, resistance to wind load and impact resistance were done according to the current regulations standards. As expected, the results were satisfactory (see table 2)
Summary table of test results:
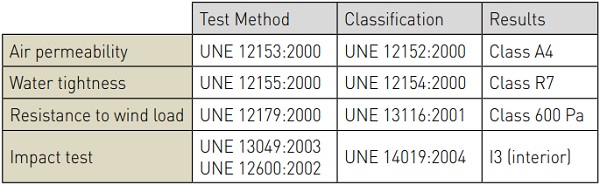
Installation
As mentioned before, the installation process was a big challenge (see figures 6 and 7). A detailed 3D assembly sequence study was done to ensure a proper execution of the work. Due to the fact that bottom level of the different “cube faces” were different we had to double check the levelling of all supporting structure in order to ensure a perfect fit of the glass. Once the overloads of the areas near the final site were verified, the zone was modelled to analyse the installation tolerances for the future movements. It was very important because in addition to the glasses dimensions, each unit weighs more than 1,200 kg.
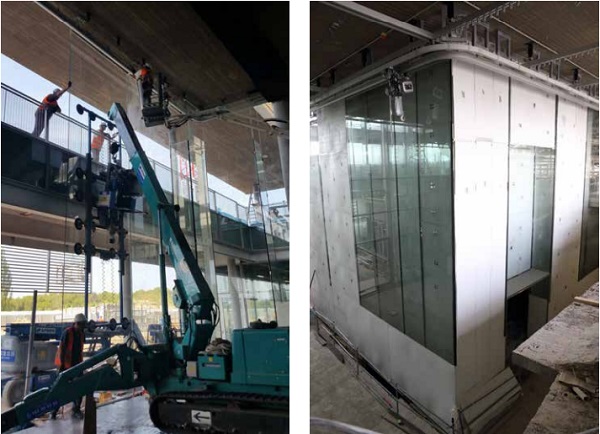
Future opportunities for concepts development
Looking to the future, it would be interesting to collaborate in a new project with bigger panes. Why not use 16x3,21 m pieces to build a new glass box? Another aspect is the use of titanium inserts to make the joints between glasses, although sometimes the use of these pieces, even punctual, may not follow the architectural concept of self-supporting transparent structure without visible metallic profiles.
Acknowledgements
Many thanks to our Client, Banco Popular, for the trust shown to Martifer during the development of project, and to believe on this type of singular constructions. To Ayala Arquitectos and ENAR for designing this type of structures that are so different and special that creates great technical challenges and make us overcome every day. Also grateful to BOVIS for the coordination during all this execution of this special project.