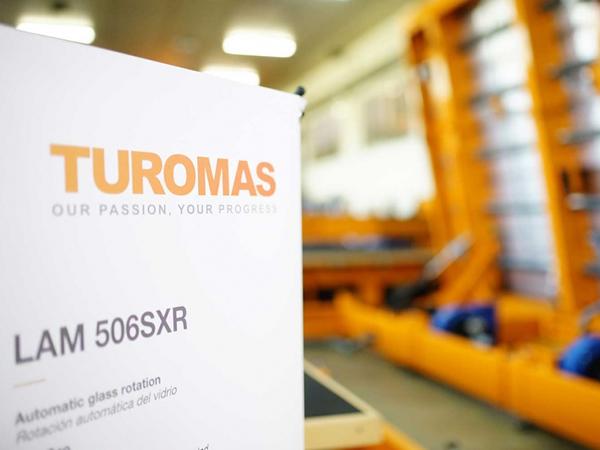
Date: 30 April 2020
When a piece of glass is cut perfectly, whether float or laminated, it reduces additional processes; and Turomas makes the difference in its 12+12 mm laminated safety glass cut.
The 30 years of experience TUROMAS has at the highest international level, developing and improving its range of glass machinery, in collaboration with the main laminated glass manufacturers, have provided TUROMAS with specific knowledge that has enabled this Spanish company to be at the forefront for these types of solutions.
In 1989, TUROMAS manufactured the first laminated glass cutting table, incorporating a cutting system with two tools, which is implemented by all manufacturers on the market today.
The systems that form part of the Turomas LAM SERIES range of machinery, has guaranteed the highest quality and precision in each movement required in the scoring, breaking and separation processes for laminated glass.
There were also improvements made during these years, and Turomas still works daily with its R+D team and customers to improve and implement innovations that help facilitate and optimise the plant work for all of them.
Laminated glass machinery range
TUROMAS offers its customers a wide range of laminated glass cutting machinery, from independent machines to fully automated lines.
The LAM 300 SERIES is aimed at companies looking for a versatile machine, with high performance and a quality cut. Compactly designed, the table can work together with a RUBI SERIES float glass cutting table for an efficient mixed cutting line for both float and laminated glass.
The LAM 500 SERIES is aimed at companies that need maximum productivity and automation. Designed to work as part of a laminated glass cutting line or mixed line, it can position, rotate, strip, cut and separate glass up to 12+12 mm fully automatically, even in glass with high strength butyral.
Main features
The structural design of the range is assembled as a whole to provide robustness and avoid the stresses that compromise its operation. The table surface, made of aluminium boards, guarantees the air flow and minimises possible losses from the air cushion.
The glass is positioned using “honeycomb” straps with a non-slip texture, incorporating a traction system centred on the table structure. This system makes it possible to move 10+10 mm glass, and even 12+12 mm, fully guaranteeing no slippage to ensure perfect positioning with respect to the cutting bridge.
TUROMAS laminated glass cutting machinery can score straight and curved shapes fully automatically, and automate the process of scoring, heating and subsequent separation. This is used in the cutting of diagonals, for example, so much in demand nowadays for the manufacture of railing panels.
All the machines are designed, manufactured and assembled at the Rubielos de Mora, Spain plant. Thus, each of the production stages and processes is controlled to guarantee the high level of quality that characterises the TUROMAS brand
In addition to incorporating the best European reference components at a worldwide level to guarantee the highest reliability and performance under any circumstances.
All of them can be linked to communicate with the main commercial optimisers on the market; in addition to incorporating software as standard in the control desk to create and manage optimisations.
TUROMAS Cutting head
The cutting head that makes up the range consists of 2 tools in the LAM 300 series and 4 tools in the LAM 500 series. TUROMAS is the only manufacturer in the world that has this technology. Each one acts independently and is dimensioned to exert the appropriate pressure for a specific range of glass thickness. The tools have a height adjustment sensor and are offset from the vertical axis to ensure perfect alignment with the cut.
They are designed to mechanically absorb irregularities in the glass. To ensure the best cutting quality, the system actively controls the pressure exerted by each tool by continuously stabilising and regulating it according to the glass plate thickness and cutting speed. The head has a constant lubrication system that favours the movement and penetration of the roller on the glass to obtain the ideal cut and ensure correct operation over time.
Breaking and separation system
Breaking is a key part of achieving the highest quality in cutting laminated glass. TUROMAS uses sensors to control and ensure the ideal path and pressure of the breaking tools for each glass thickness. The upper nylon wheel descends and travels along the glass to carefully perform the first operation as this is the most critical. Then, a ruler cuts the glass from its underside.
The PVB is heated by a specific infrared lamp that prevents the heating of the glass to preserve its quality while, at the same time, the two sides of the glass are separated by the pull exerted by two sets of independent suction cups at the bottom so a blade can enter and cut the PVB. The lamp light is adjusted to the size of the glass to be separated, with only the sections necessary being heated to save energy and speed up the process.
100% compatible with low emissivity glass
The entire range of machinery is fully compatible with glass with low-emissivity layers, since at no point in the cutting process or through any device does it touch the part of the glass where the low-E layer is located. TUROMAS is the only brand in the world that does it this way, as recommended by low emissivity glass manufacturers.
They incorporate a high performance stripping grinding system, managed by a control device that constantly stabilises and monitors the applied pressure for the ideal removal of the low-E layer. The grinding wheel is self-sharpening and incorporates an advanced system for vacuuming stripped waste. In addition, since 2001 the LAM 500 series has included a patented automatic rotation system.
This system works by combining the movements of 2 independent suction cups that grip the underside of the glass on the X and Y axes, offering rotation under safer conditions while preventing contact on the glass low-emissivity layer at all times to preserve all its qualities.
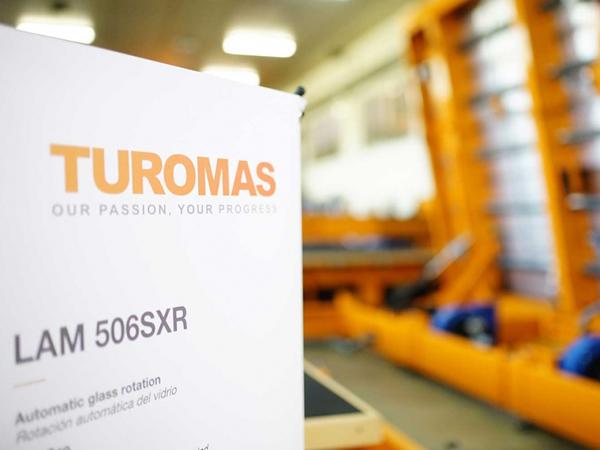

Add new comment