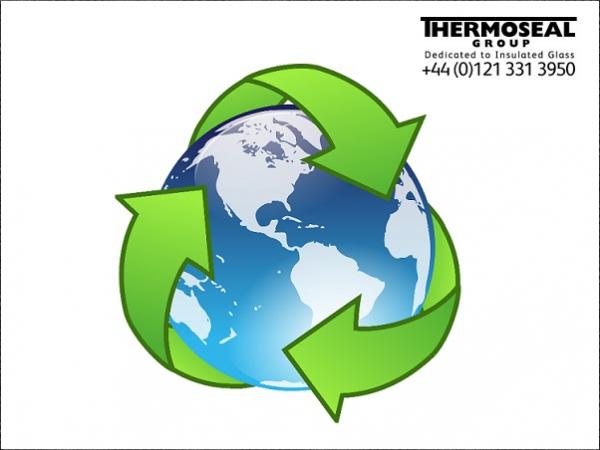
Date: 19 July 2019
Over recent years we have seen exponential growth in our manufacturing division to meet the requirements of the growing market for our industry-leading warm edge products.
With new machines recently installed to increase the production of Thermobar and fittings range, we can now manufacture millions of metres of spacer bar and injection moulded fittings on a weekly basis.
Like any responsible manufacturer, we see it as our responsibility to analyse, monitor and take continual steps to reduce our carbon footprint. As a result, the latest addition to our production facility is our new Plastic Recycling Plant which has already seen a six-figure investment.
Since we produce our products using lean manufacturing initiatives from Six Sigma and Kaizen manufacturing strategies, we have already taken strides to continually decrease the plastic waste from our production facility. Therefore, the new recycling plant was the only way to improve on our current efforts.
Click here for more About Us >>
Our NEW Plastic Recycling Plant
This new plant will enable us to recycle all of our plastic waste including the unusable sprues that injection moulded fittings are attached to when they come off the machines. There is also inevitable waste on start-up of the extrusion lines which can also be recycled.
Our new equipment includes a grinding machine which converts the plastic waste material to fine shavings. These shavings are fed into our recycling plant and mixed with the exact percentage of virgin material. This blend is repackaged and used for normal production of Thermobar or fittings with no detrimental effect on the finished product.
Click here for Warm Edge Manufacturing >>
Our Drive to Reduce Packaging Materials
As you can imagine, we require a significant amount of packaging to ensure our products are stored and delivered in the top quality they come off our production lines. This is particularly important for our export customers who will receive our products after thousands of miles of transport. Whilst we take steps to reduce our use of packaging, we always have to keep the functionality in mind.
However, we use returnable Stillages for our customers where possible and are continually analysing our packaging material to maintain the correct balance between reducing our cardboard consumption and maintaining the integrity of the products.
ps. If you have any of our Stillages, please return them now so that we can continue to recycle them to help reduce our carbon footprint and also to keep your product costs to a minimum.
Click here to see 2,500+ IG Components >>
Paperless Order Processing & Delivery
Perhaps one of our most significant achievements in reducing our environmental impact is the installation of our new order tracking and delivery system which was the final stage in achieving a paperless sales order processing service to customers.
As well as doing its bit for the environment, this system provides a multitude of benefits to customers including real-time tracking and satellite location of deliveries, as well as same-day e-mailed delivery notes and invoices.
This new tracking system complements our earlier-installed barcoding system to ensure that delivery errors are minimised and our teams work together to provide prompt and reliable deliveries.
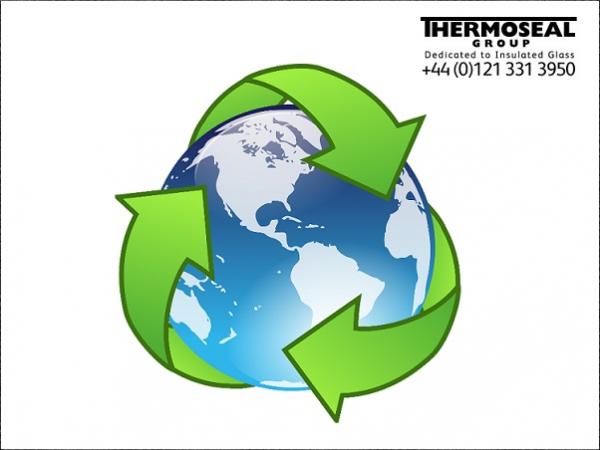

Add new comment