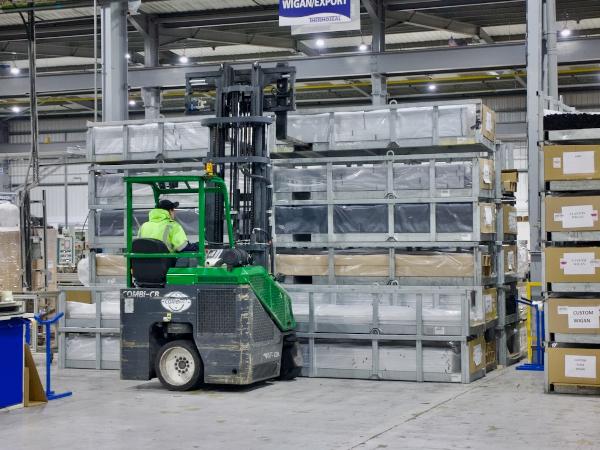
Date: 9 November 2023
“Thermoseal Group delivers all products directly from its four British stock warehouses, using its own fleet of vehicles. Not only that, but it does it sustainably,” says Sales Director Mark Hickox.
“We have complete control over our deliveries,” Thermoseal Group’s Sales Director says. “We don’t need to rely on an external company to arrive on time, and we don’t have to factor in the cost of couriers into our prices. We do it all with our own fleet, and that ensures that our customers get excellent service at an excellent price, each and every time.”
Thermoseal Group produces energy efficient products by energy efficient means, and its transport strategy is no different.
As well as the recent investment in automated production lines that have reduced energy usage in Thermobar’s manufacture by almost 40%, Thermoseal Group are also actively encouraging their Thermobar customers to move to steel stillages as opposed to cardboard packaging.
The metal stillages undergo a cycle of re-use, and through opting into their use, the price of the spacer bar is reduced accordingly.
The customer does not then have the hassle of disposing of the cardboard boxes at their site: they simply set the stillages aside for Thermoseal Group to collect them on their next delivery. With a further £140K recently invested in a further 200 metal stillages, the strategy is a big success with customers, according to Mark.
“The stillages are easier for customers to handle,” he says. “And I think in this day and age, our customers know the importance of sustainability and they can appreciate the fact that we are doing our bit to reduce waste.”
Thermoseal Group’s Thermoflex flexible spacer bar is supplied coiled onto plastic reels, in a plastic bag, inside a cardboard box. To prevent this packaging from being scrapped, the company has developed a system where, similar to Thermobar’s metal stillages, they collect and reuse the bag, the box, and the reel.
This unique packaging method has successfully diverted 80% of packaging away from landfill and has kept the price point of Thermoflex lower for customers, Mark explains.
“We manufacture over 50 million metres of spacer bar a year,” he says. “Imagine how much packaging is required for that amount of product. But with our recycling process, we significantly cut the amount of packaging that we use, and we use everything until its lifespan is completely over, limiting the amount of waste we’re sending to landfill.”
As well as delivery efficiencies, the company recently installed a Solar PV System at its site in Wigan, which produces 420MW of electricity per year. This is used directly by the Thermobar and Thermoflex manufacturing processes, greatly reducing the company’s reliance on the grid and generating approximately 15% of the power used at Thermoseal Group.
Electric vehicle charging points have been installed at all sites so that employees and visitors can charge vehicles during working hours, as well as two electric forklift trucks, which also capitalise on the energy generated by the solar panels.
“At the end of the day, we’re manufacturing energy-saving products and we want to be an energy-saving company,” Mark says. “We recognise the importance in sustainability not only for our duty to the environment, but also to keep prices as low as we can for customers, without compromising on the quality for which we’re so well known.”
For more information, please visit www.thermosealgroup.com, or call 0121 331 3955.
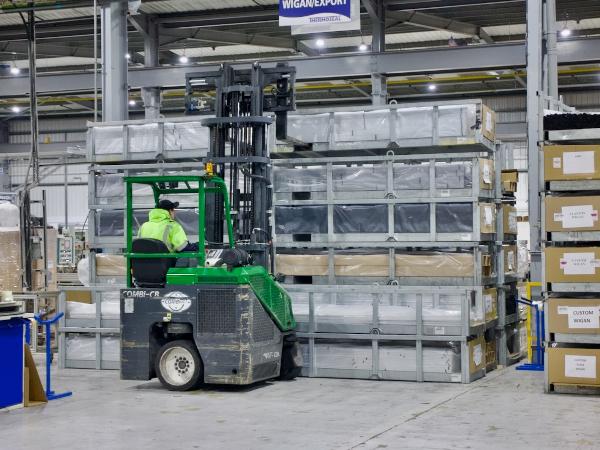

Add new comment